The bus build didn’t start with us planning on buying a bus, nor a vehicle of any sort. It actually started with us trying to build a bowl for the warehouse. We already started 3D renderings of what it would look like but after long weekends camping, plans changed. Collin realized we shouldn’t spend money on a bowl where we would only have a few people riding it from time to time and instead we should build something that brought the scooter community tighter. A vehicle that could hold some dudes and put in some long miles.
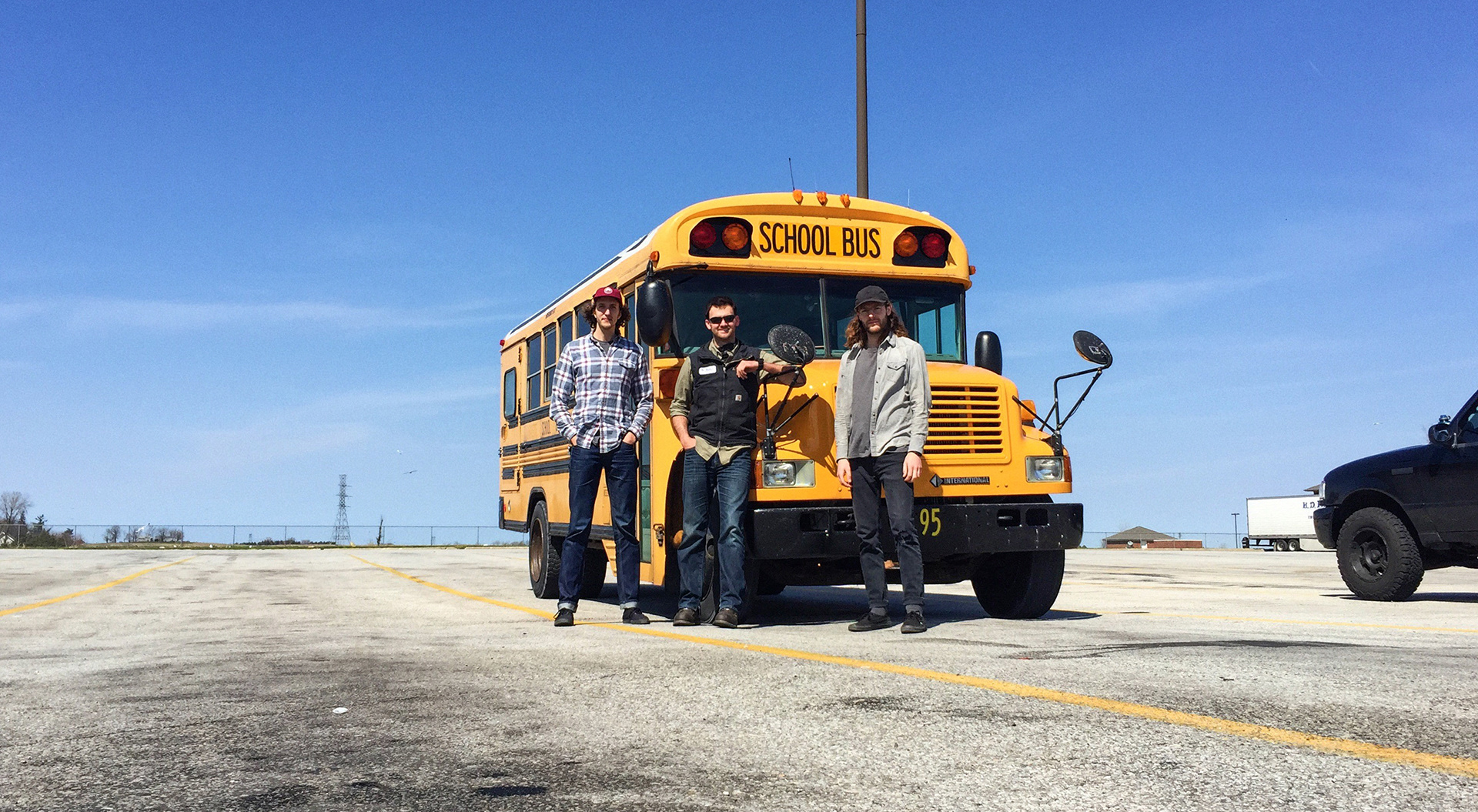
Our first couple of options were smaller vehicles and frames. After plenty of back and forth we settled on class C busses. Plenty of research went into just choosing which vehicle to buy, and plenty more needed to be learned on the fly. This could be our biggest mistake or success that we have ever been a part of. We did not know exactly what we were getting ourselves into, but we had to work fast.
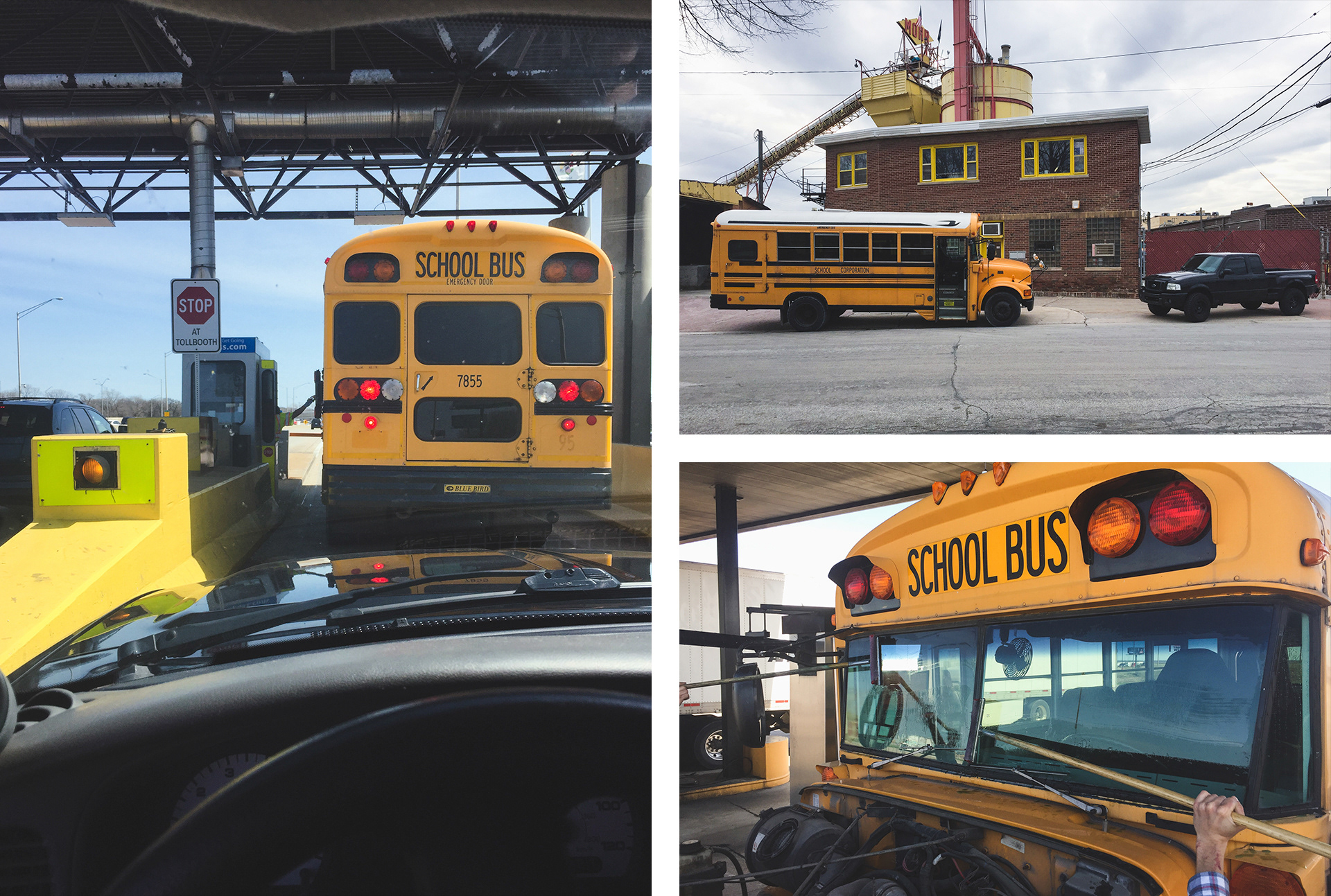
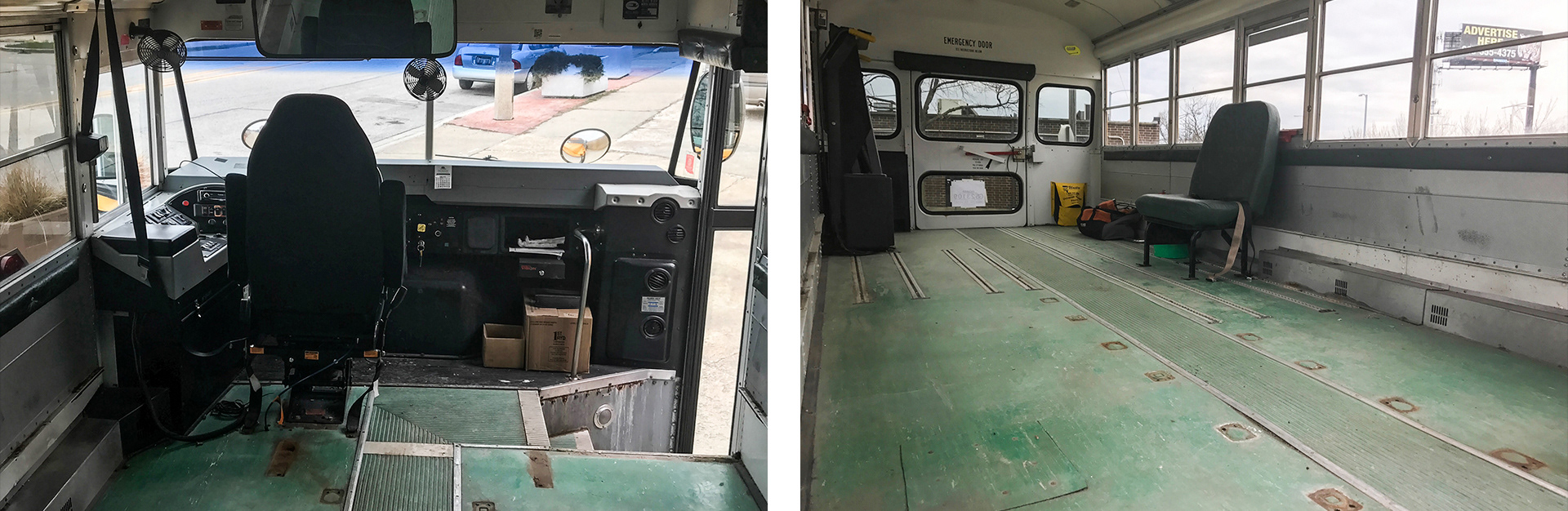
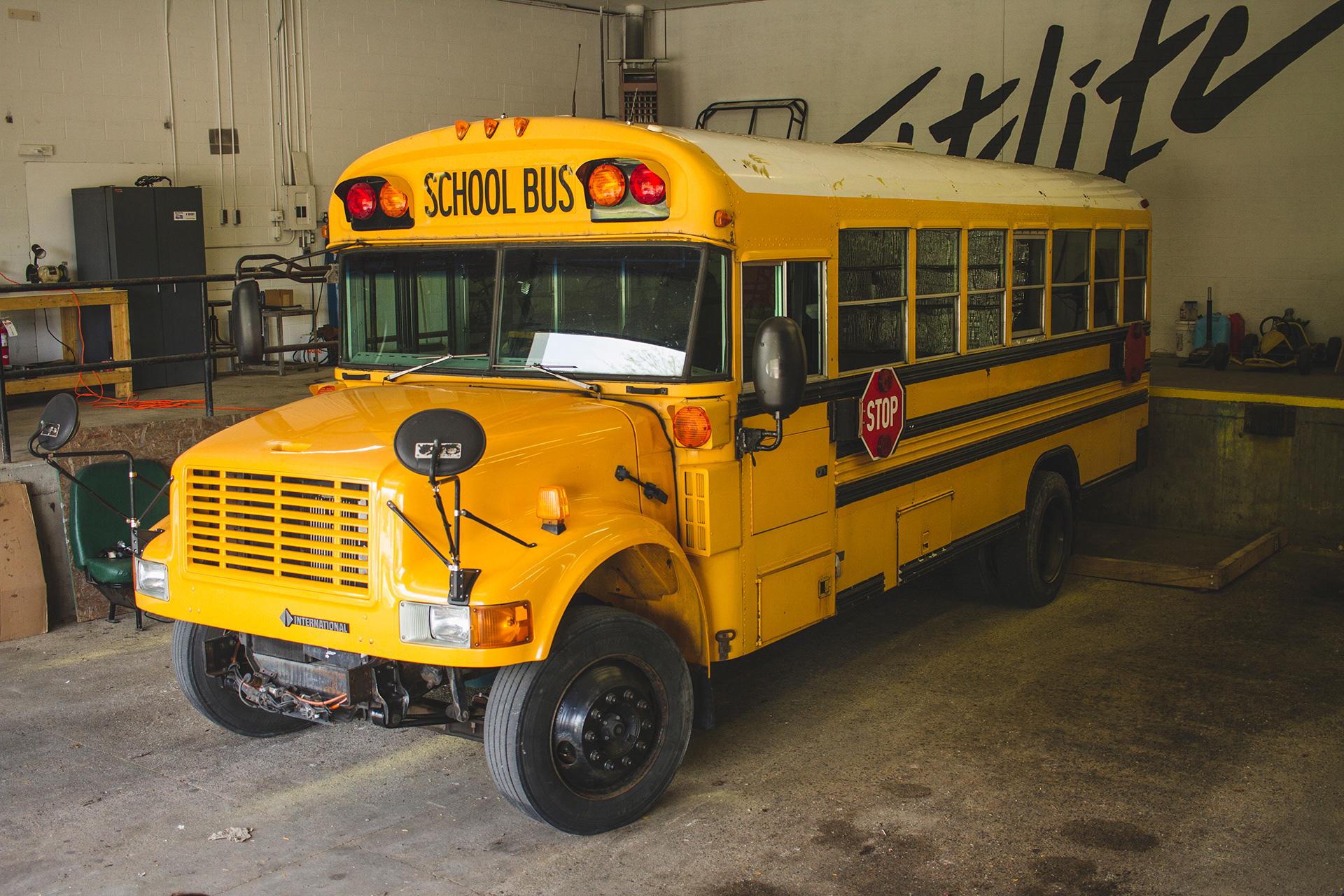
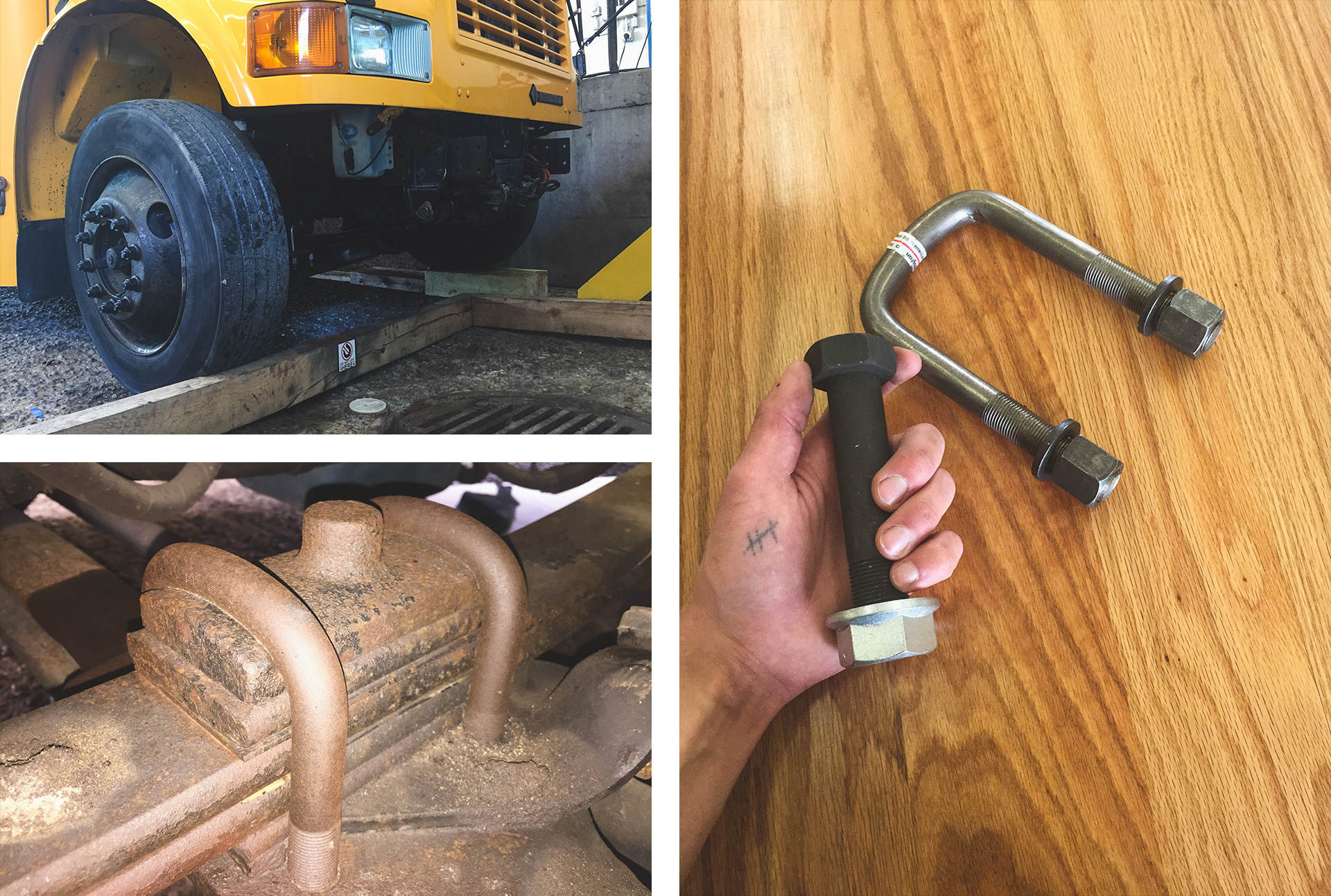
After the first couple weeks of owning the bus, getting it looked over by mechanics, and replacing some suspension issues we realized how heavy duty this thing was. You can’t just take a bus to a jiffy lube, you have to service it at the same place semi trucks get serviced at. Most of our tools weren’t spec’d to work on a bus so we had to buy the right tools which aren’t cheap. We learned this by breaking a few wrenches and drills bits. Once Collin realized how doomed we were, he called for backup, Chris and Mike were scheduled to come up in a couple of weeks but the help was needed now. Chris showed up that weekend with the bus pretty much fully intact.
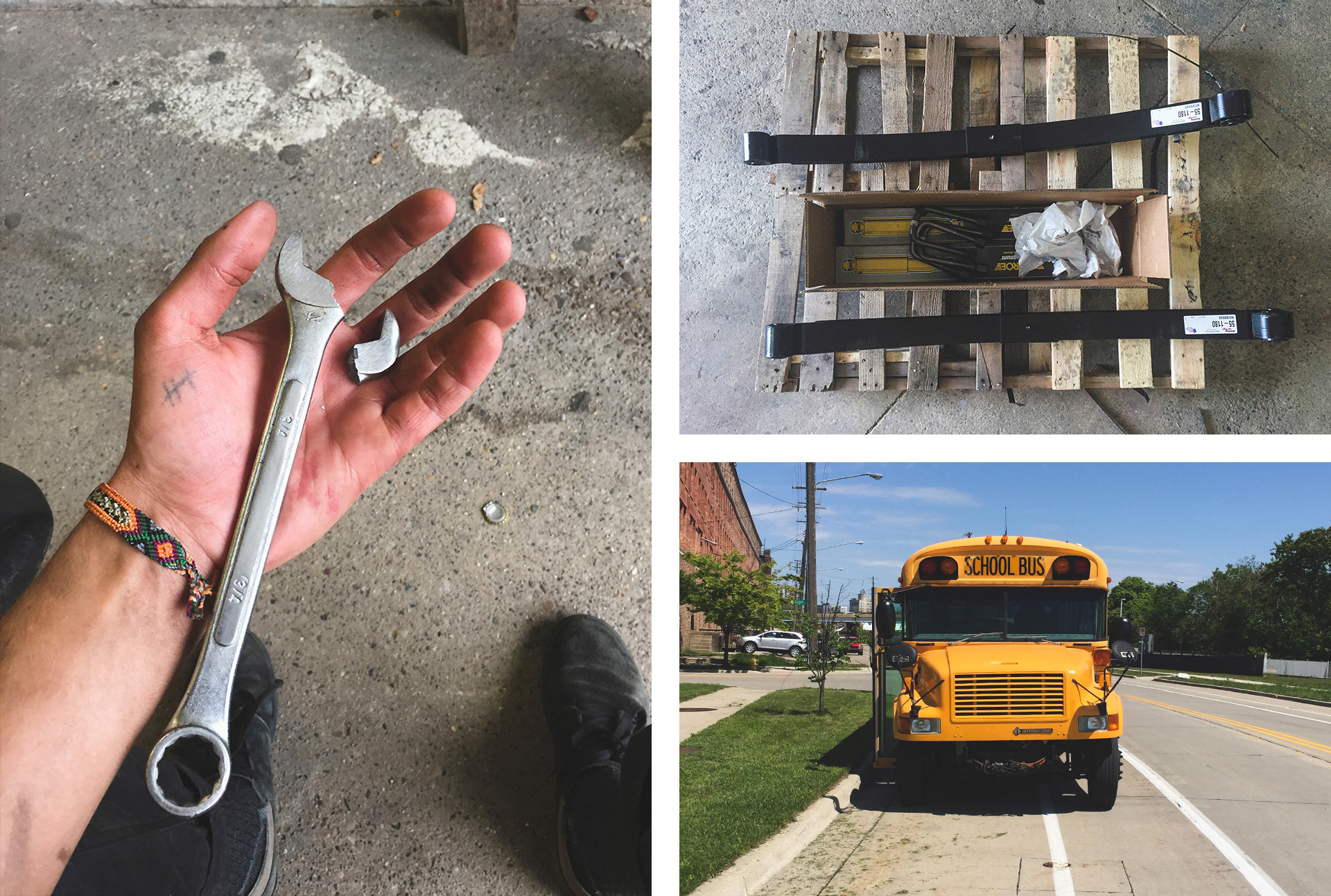
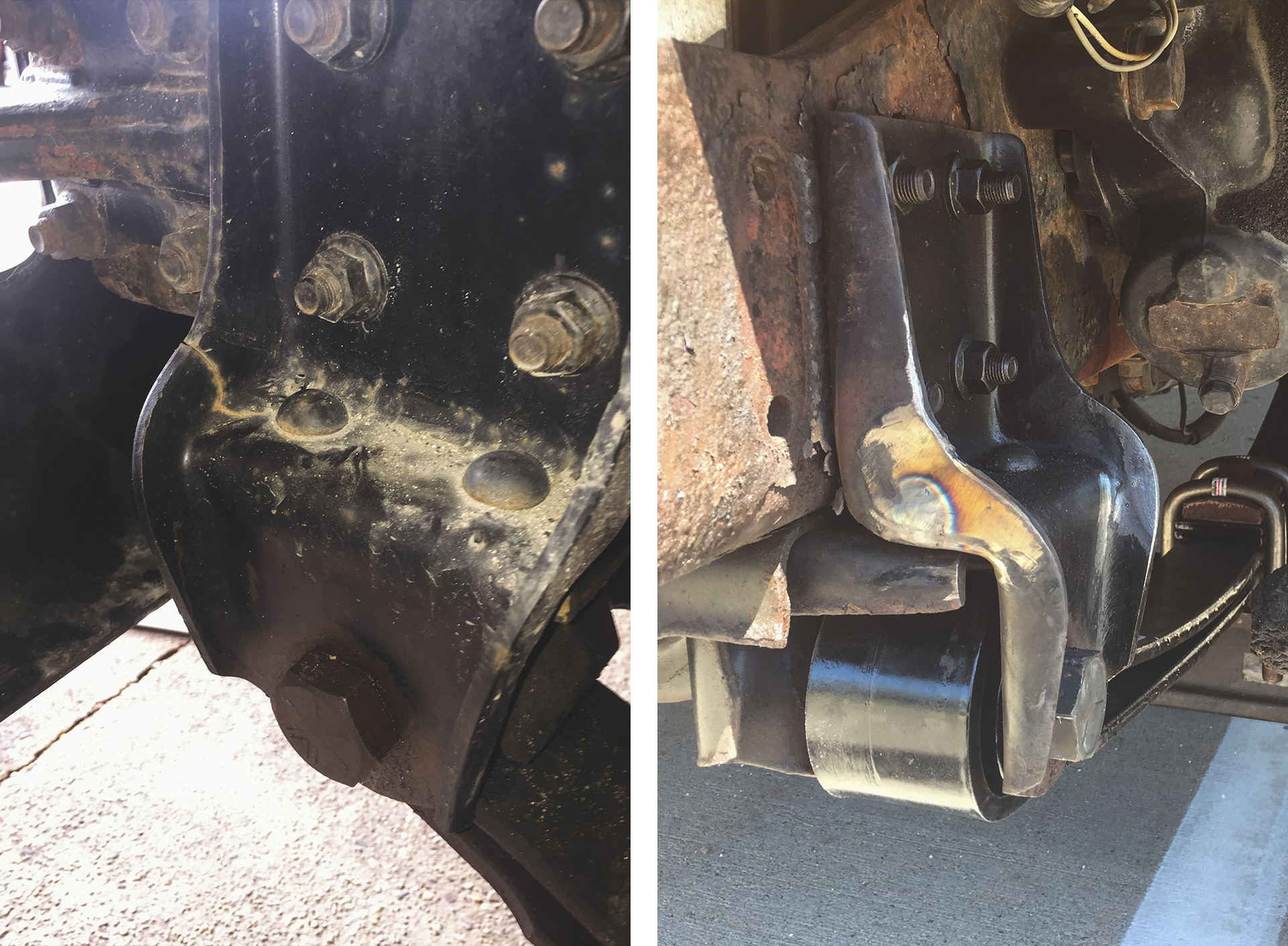
First steps were to demo the bus. Christian already had a jump start on the exterior but the inside was the main focus for now. Pulling windows out, trying to pop rivets, exposing the interior, removing doors, pitching insulation and cutting/labeling wires. We knew one extra body wasn’t going to do it all so we nailed down an extra hand by the name of Stevie, a local skater. We also brought on William from Anvil Goods, a talented carpenter. Things started to pick up with every day feeling like two days. Lines blurring between running a scooter company and Snoek’s Custom Chop Shop. Each day ended with “Wow, we have a lot more to do but damn, we did a lot today.”
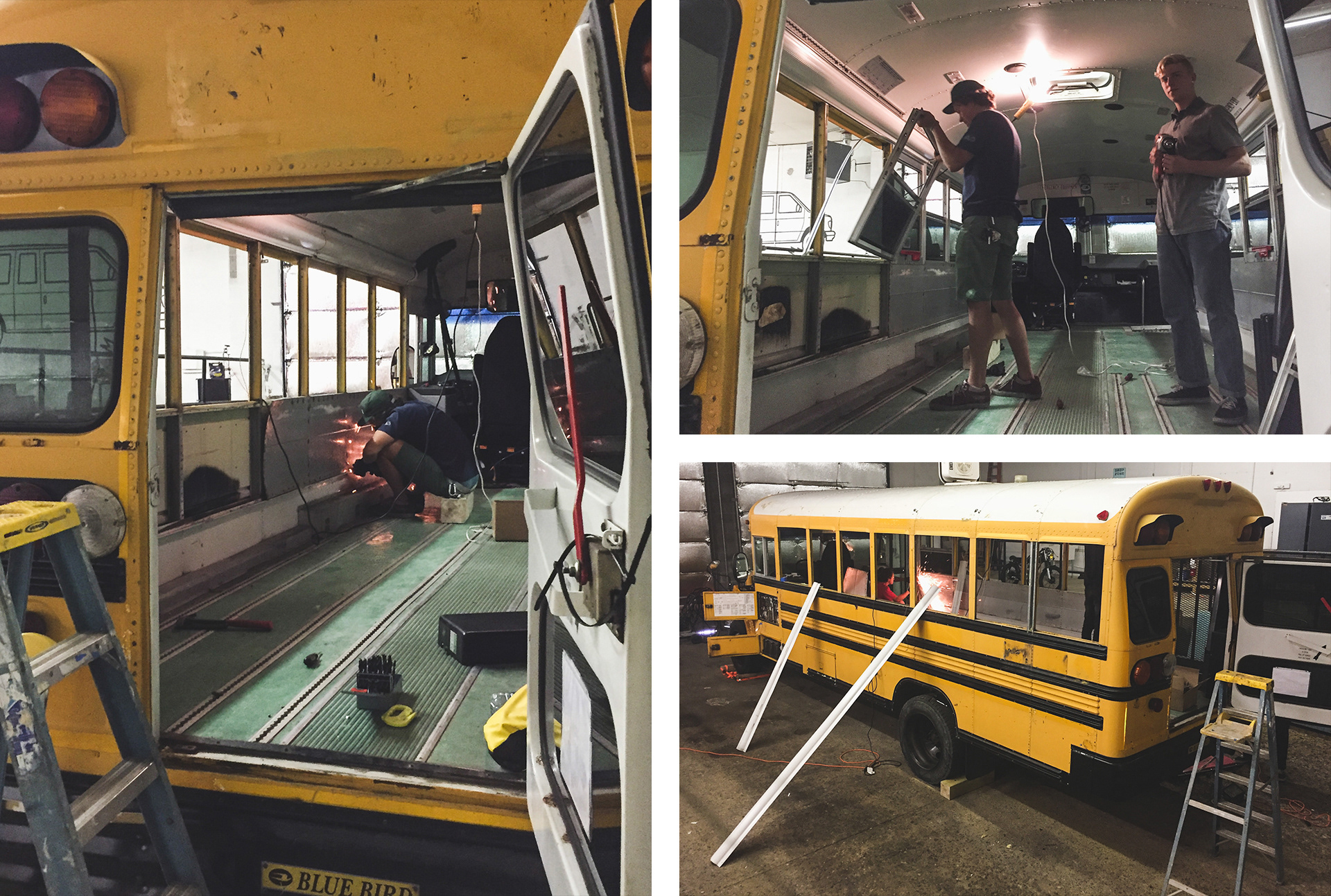
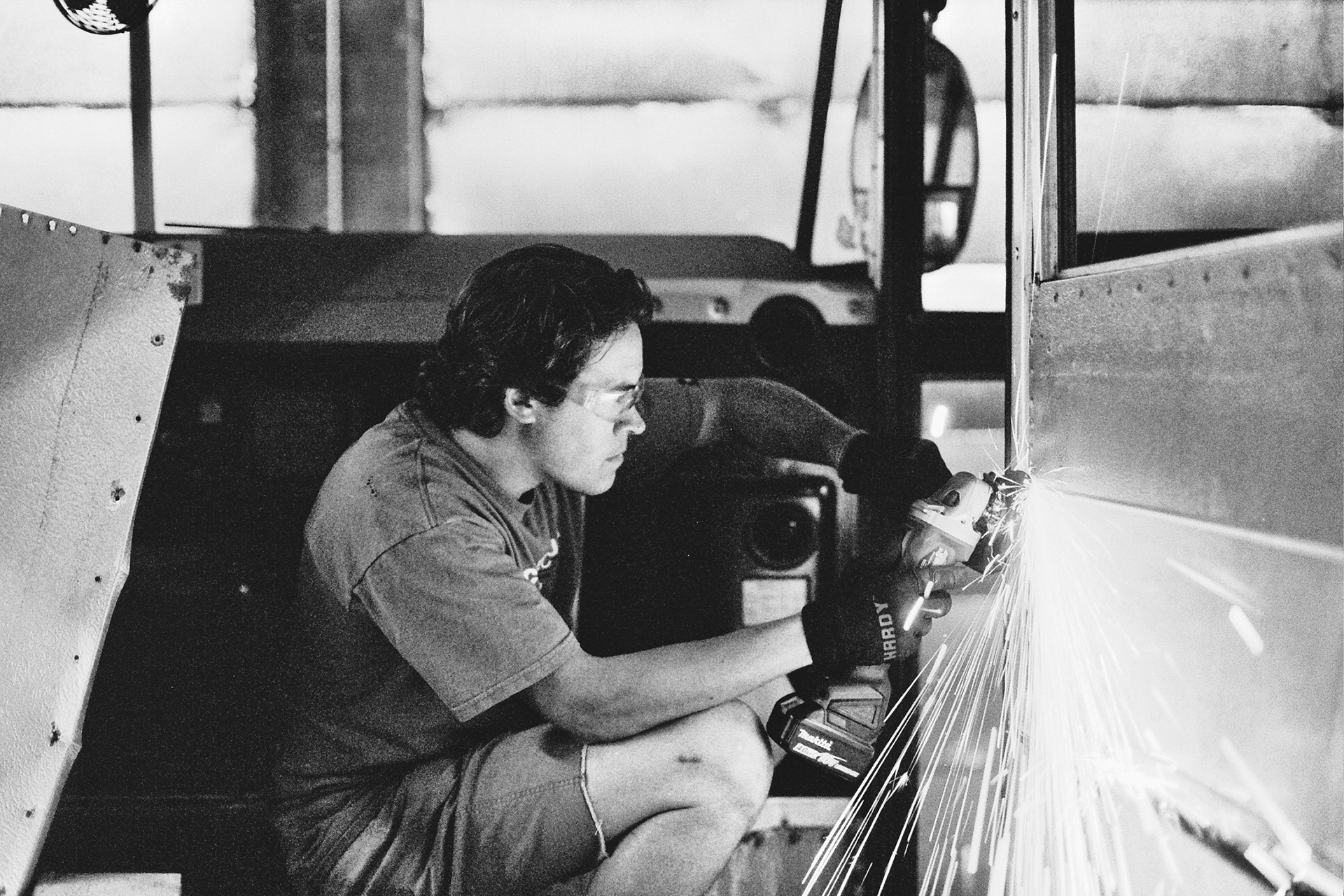
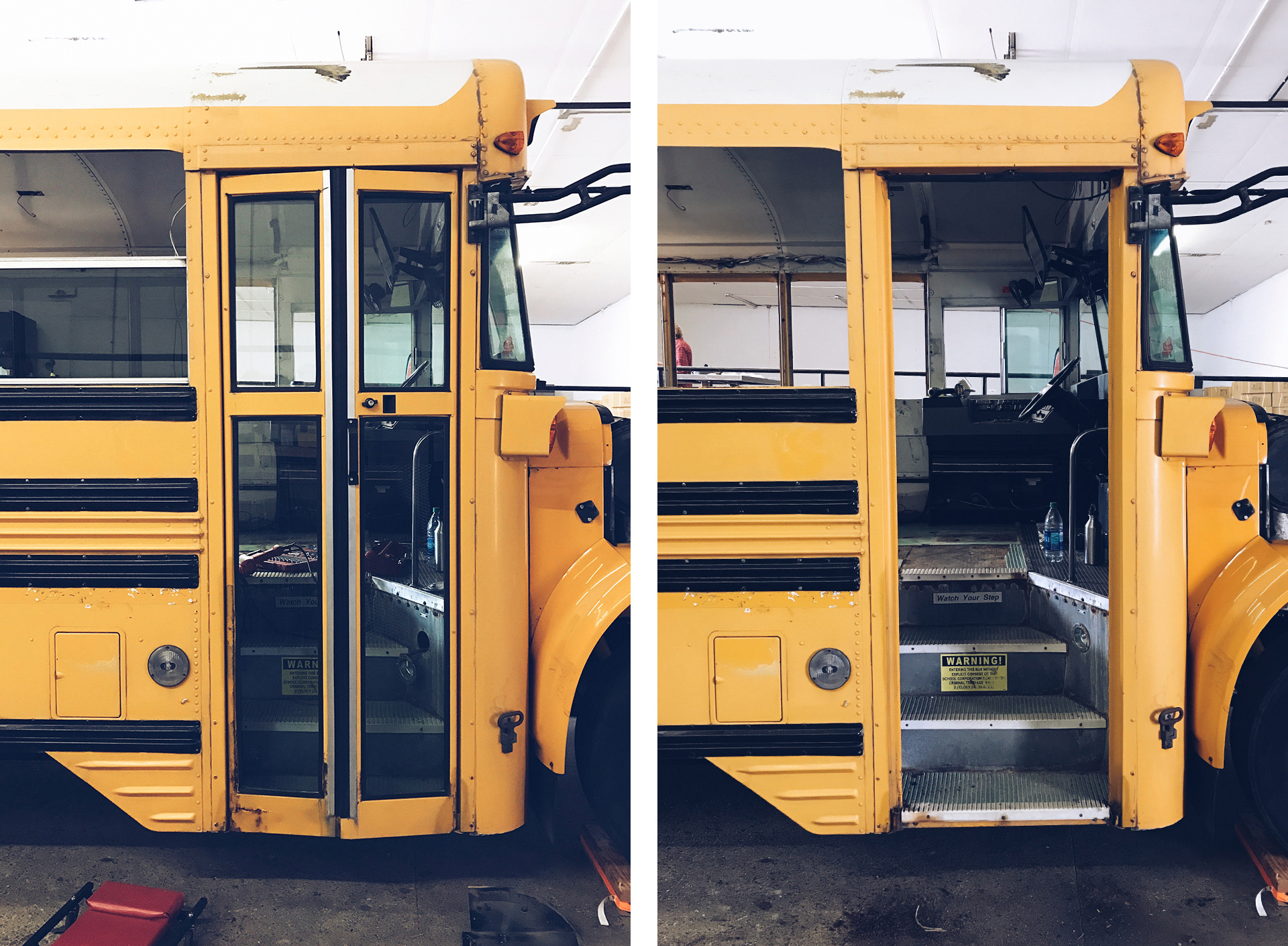
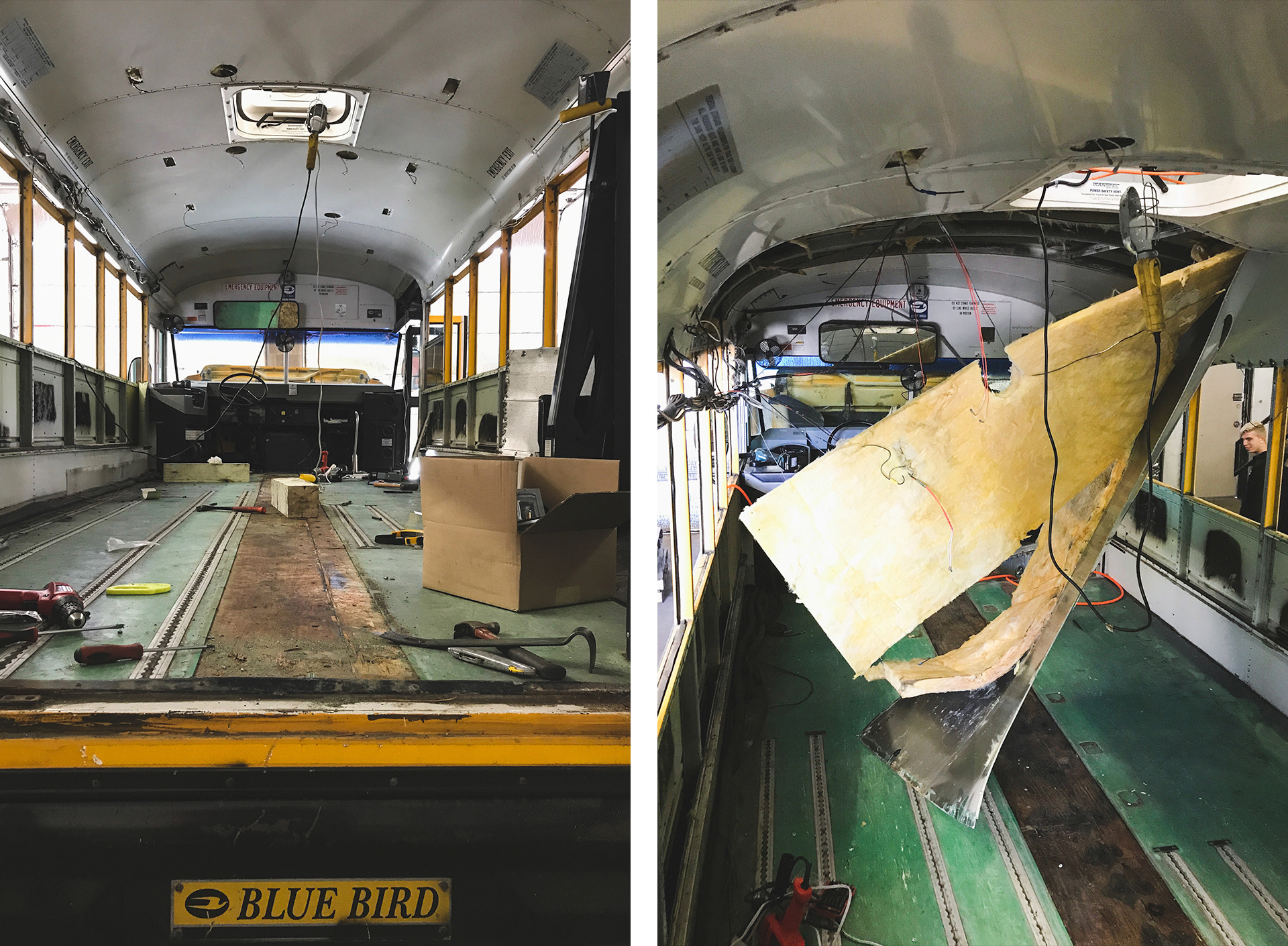
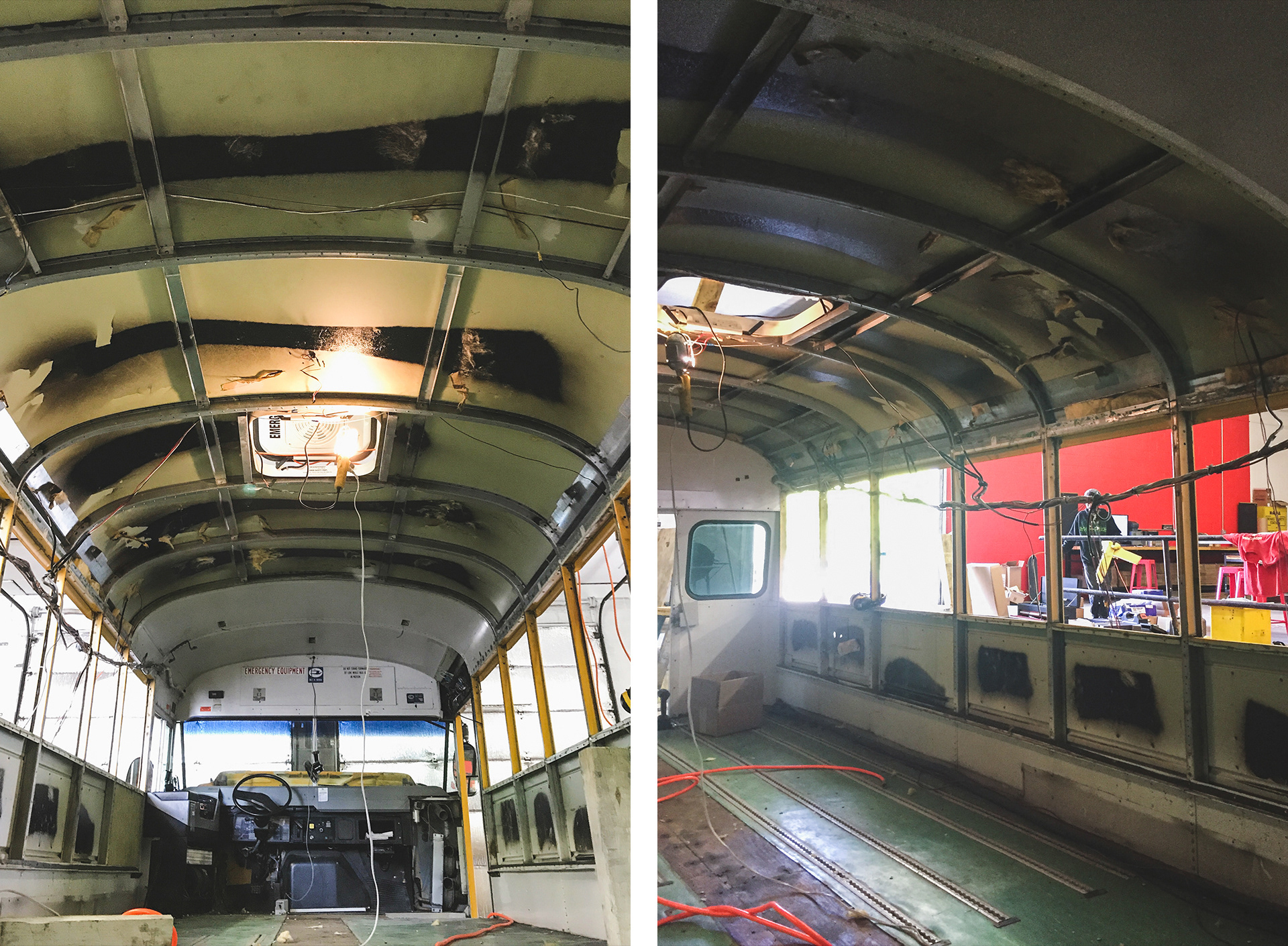
When arriving to the shop on a bright and early morning, you would have absolutely no idea what time you'd be leaving that day. This caused everyday to feel like one big blur. "Wait, that was today? I thought that was yesterday..." was a common saying during the long days of building. Removing the ceiling was easier said than done, just like everything else on the bus. Since it was a Blue Bird bus, that meant quality and a bunch of rivets instead of bolts. The entire ceiling was held together by hundreds of rivets that needed to be punched and grinded off. After a couple of days of going to town, the ceiling and insulation was ready to come out of the bus.
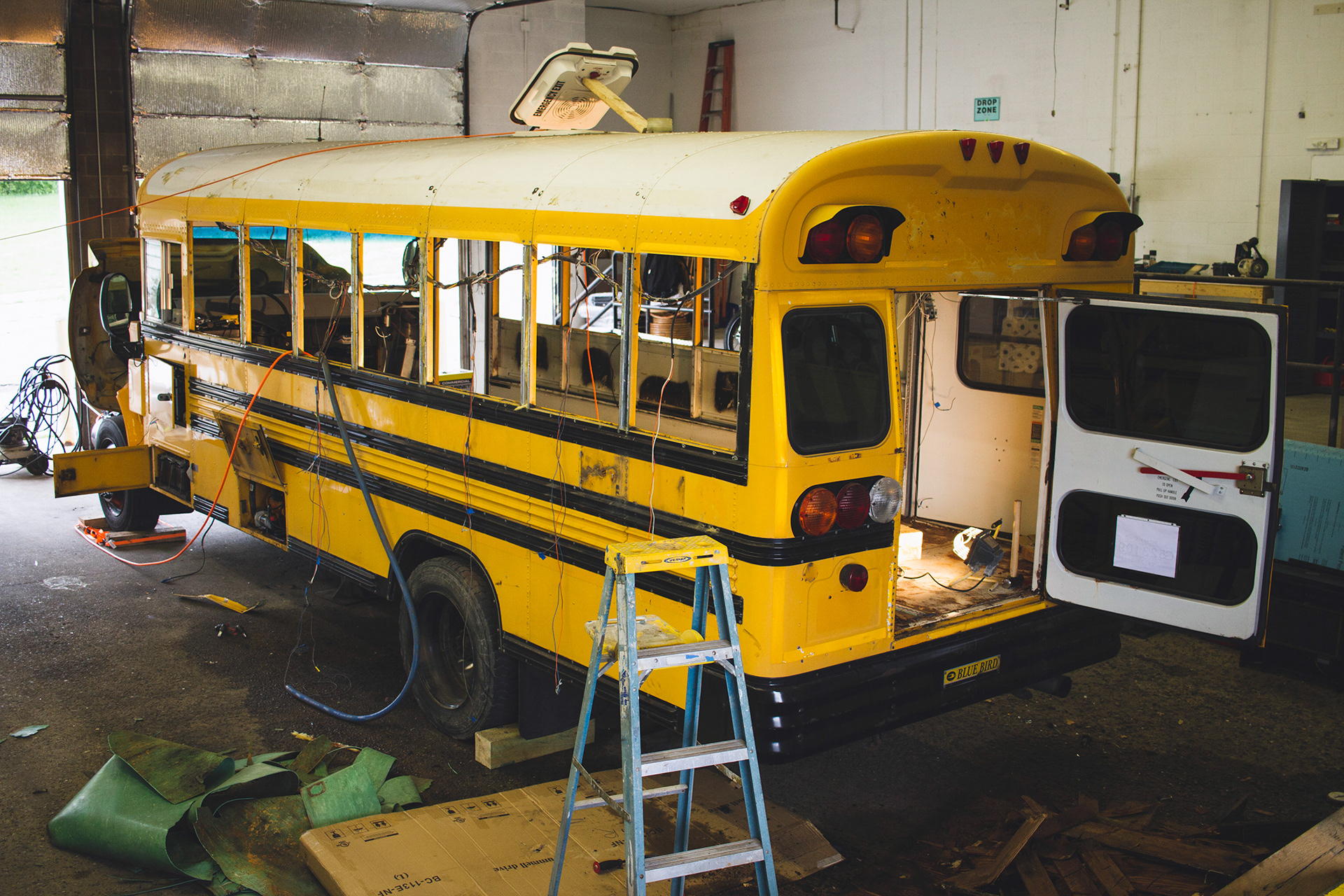
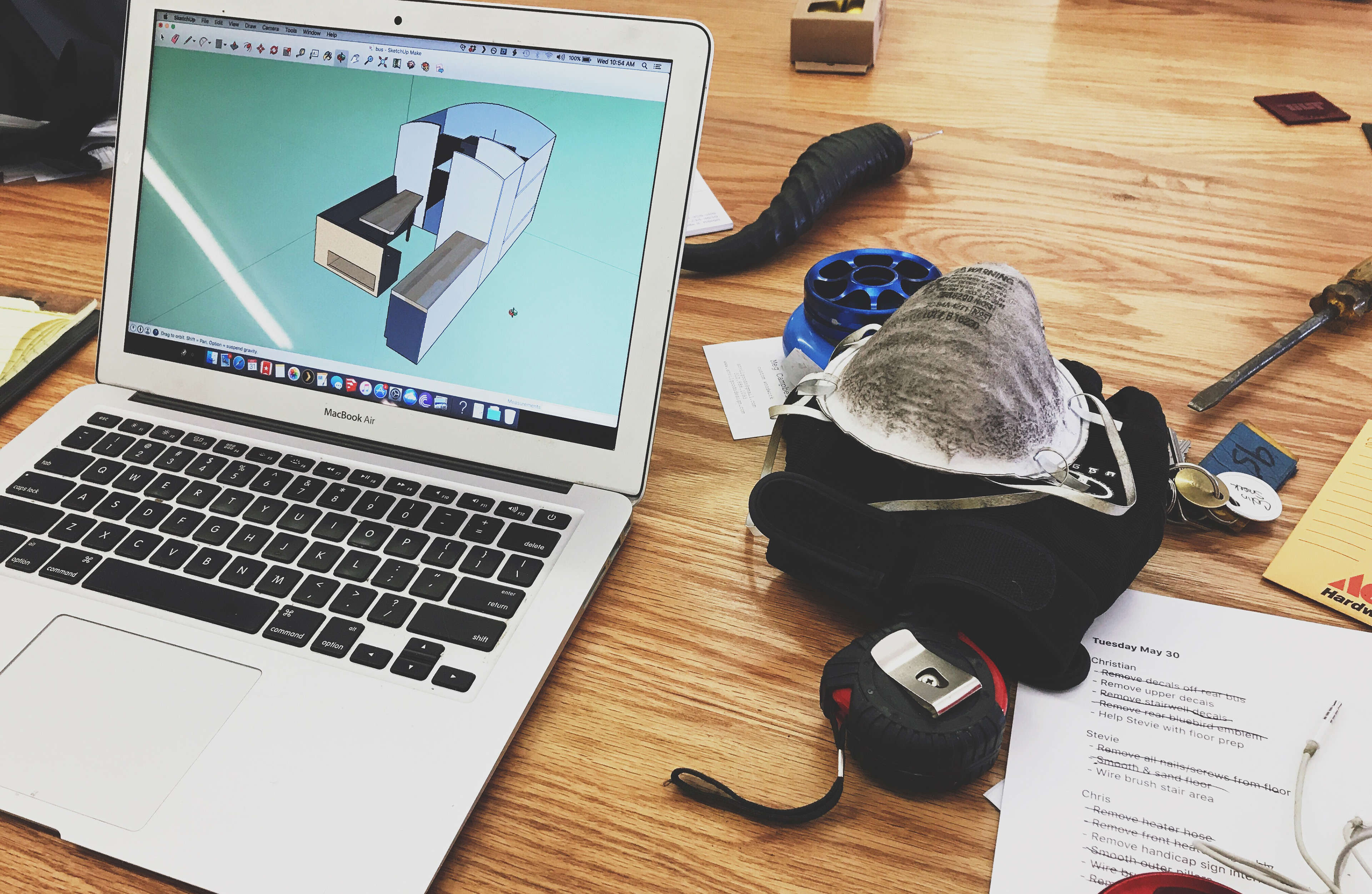
In order to hit our deadline we were forced to see into the future. Mocking up the interior and buying new products for the bus were just some of the steps we were taking to try to stay on track. We purchased the new RV door from an RV parts dealer in south Michigan. The cabinet and batteries came from Sam’s Club.
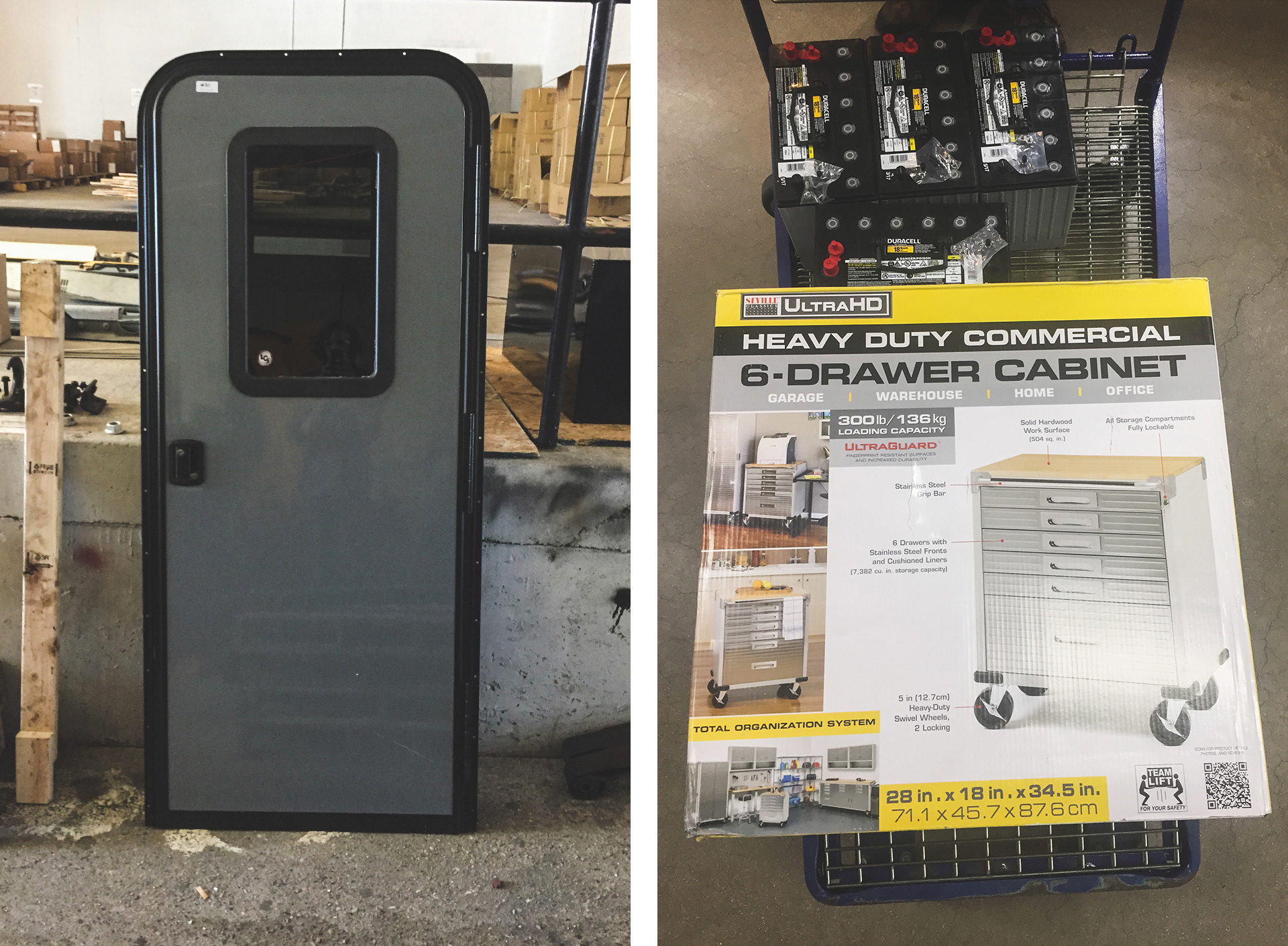
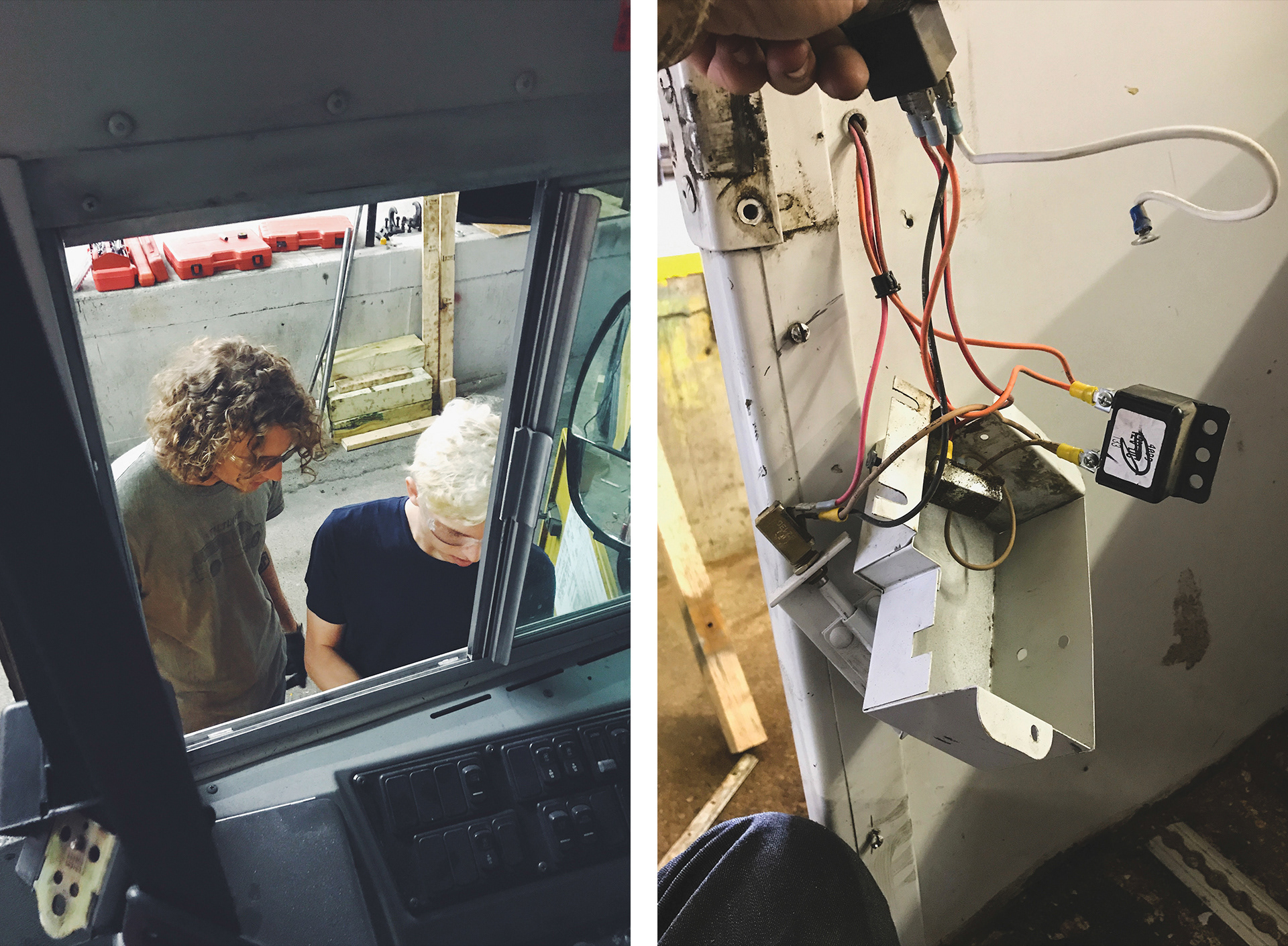
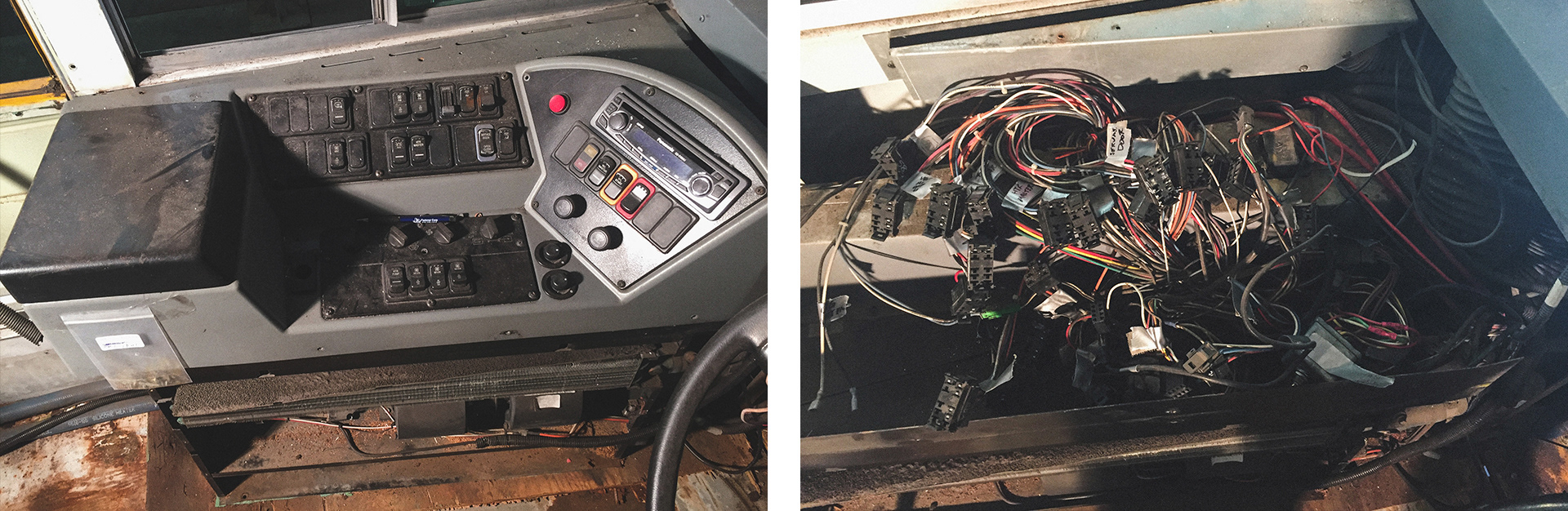
Collin was the only one that had a grasp on the wiring but he was so busy being project manager along with everything else that he called his buddy Jordan to lend a hand. Jordan helped strip the bus from any unnecessary wiring and cleaned up the harnesses. We would of been screwed without him.
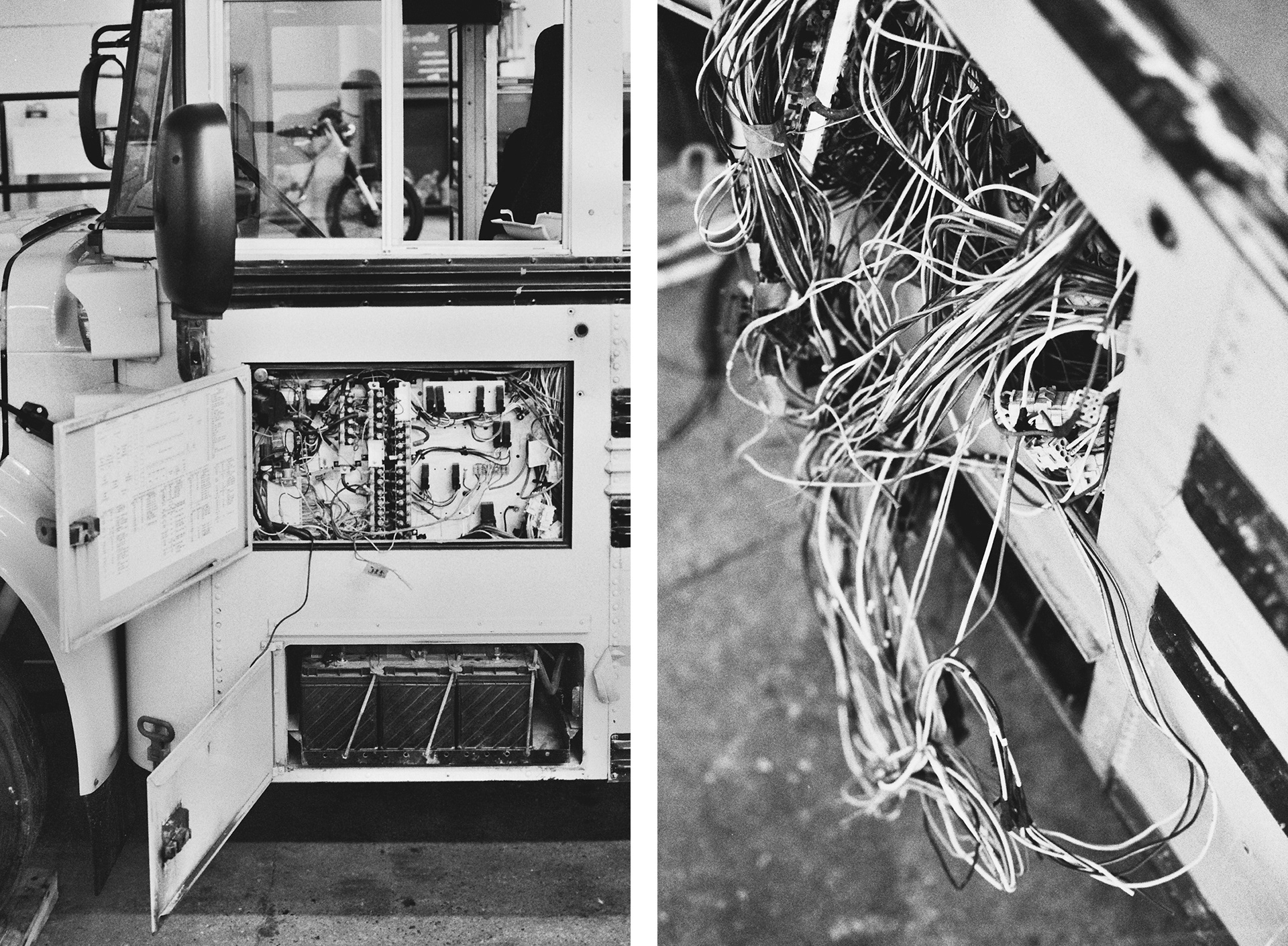
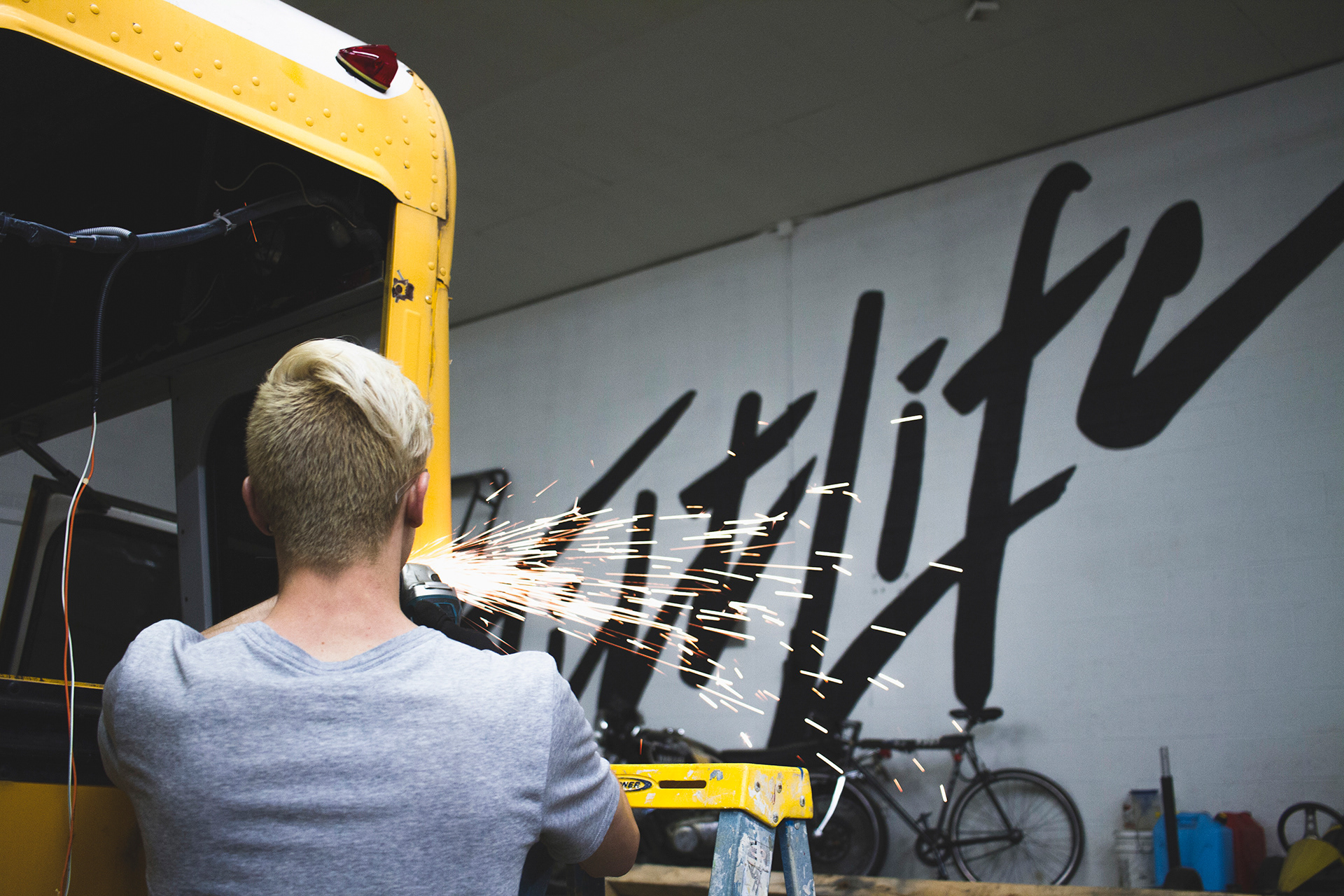
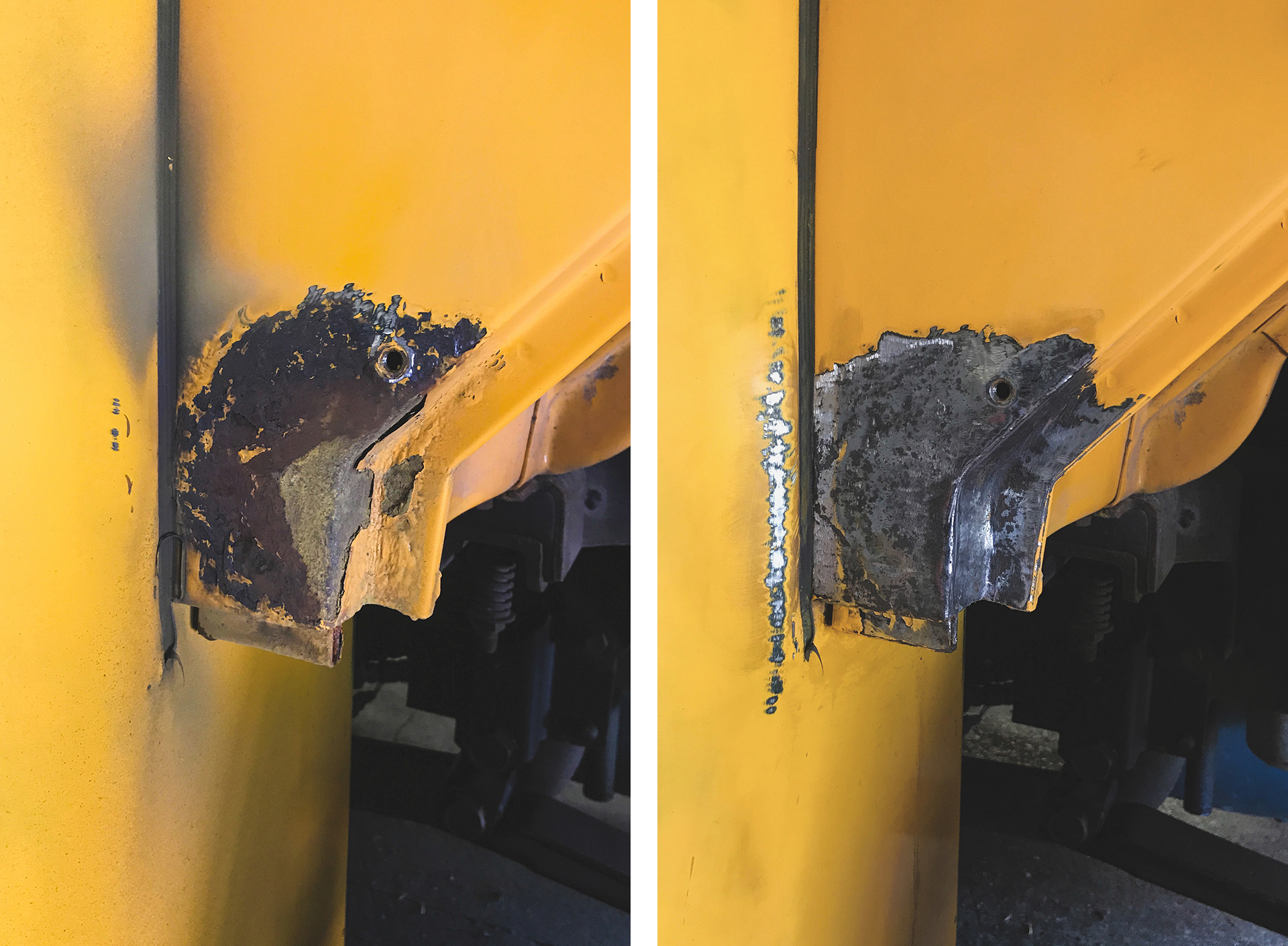
Some of the bus had seen better days and had rust build up on the exterior. We went around with a cut-off wheel attached to a die grinder to shred away any of the rust. We then hit the metal with abrasive stone point attachments along with 120 grit sanding bands. After that, we would wet sand the paint to blend into the bare metal. It was a process but the outcome was flawless and unnoticeable after the final coat of paint was on the bus.
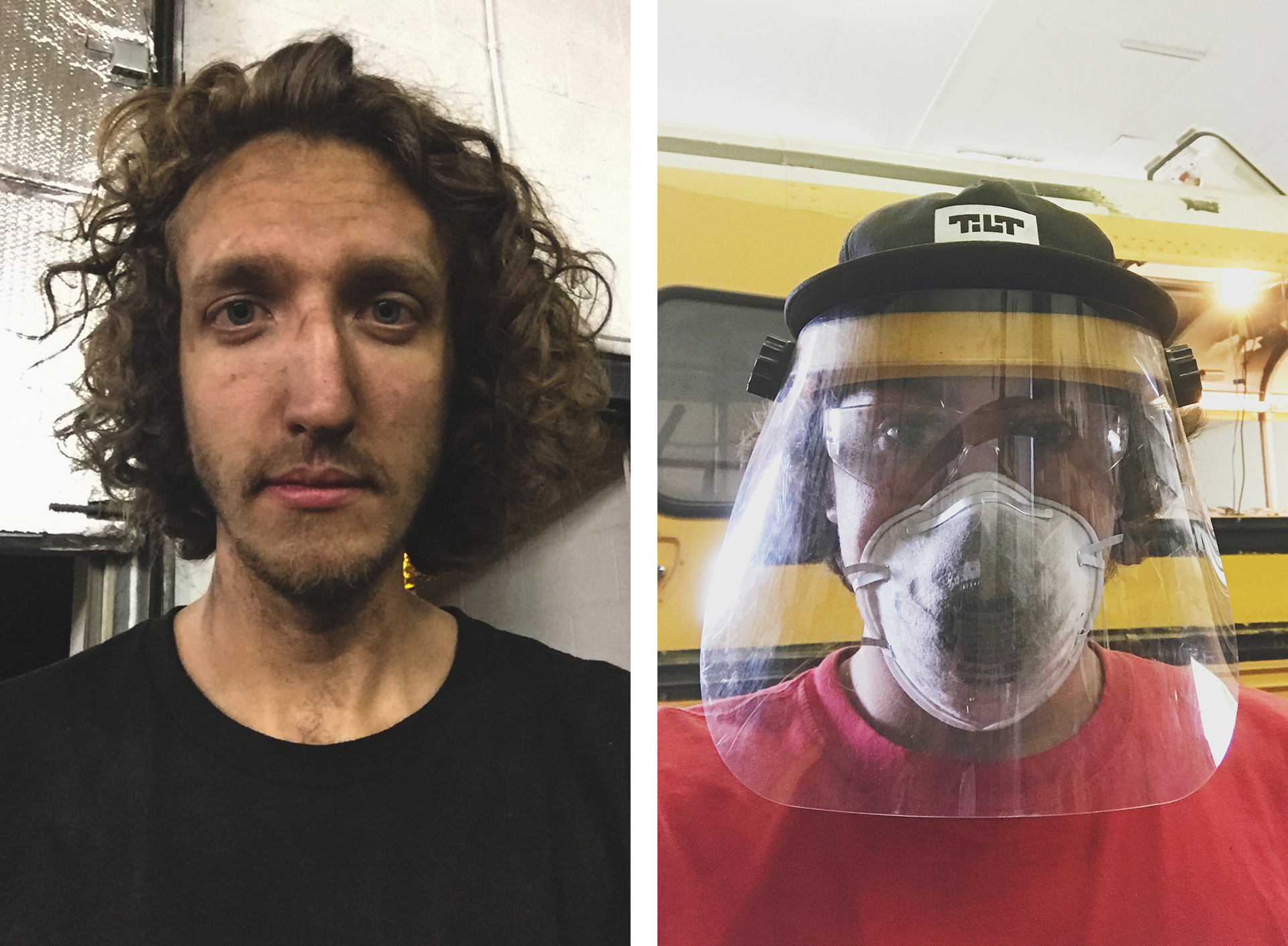
Mike stepped in twice during the build since he was pretty much the only one running TILT while the rest of us tried to focus on the bus. The first time he left Chicago to come to GR was to help wet sand the exterior to get it ready for prime. Since Mike has a very keen eye to detail, most of the bus was done by hand. A very long, grueling process that no one should take on themselves. While some of the focus was on the exterior, there was still work being done on the interior. The ceiling was coming out, more wires being cut and stripped, and the floor…oh man the floor! One of the hardest tasks we weren’t expecting that everyone helped out on but was mainly tackled by Stevie and Christian. The floor was coated with vinyl, plywood and then steel. There were rows of aluminum rails that held the old bench seats. These rails were held in with hardened steel bolts. The head of each bolt had over a decade of gunk around all of them. If you were lucky enough to get to where you put the drill bit in the head to unbolt these, you would strip the head. Cutting the bolt from underneath wasn’t an option because there was too much in the way. Since the heads were hardened steel, breaking the heads off with a drill wasn’t an option either. Our only real option was to cut each bolt from underneath the rail but above the steel floor. That meant using a circular saw that would cut perfectly down past the depth of the wood but not cut the metal floor. Then you take a pry bar and rip up all the plywood around the rails. Then you take a pry bar to hammer out all the wood in-between the rails and metal floor. Then you take a pry bar and wedge it in-between the rail and floor so you can fit a sawzall in there to cut the hardened steel bolts. This wasn’t like you turn on a saw and it does all the work, You had to saw back and forth while changing the angles to get the job done. It felt like you were trying to hold on to a vibrating handle that was trying to jerk your shoulder out of its socket. We were lucky if we got one rail done in 3 hours. There were 8 of them, spanning two-thirds of the bus. This was our hell!
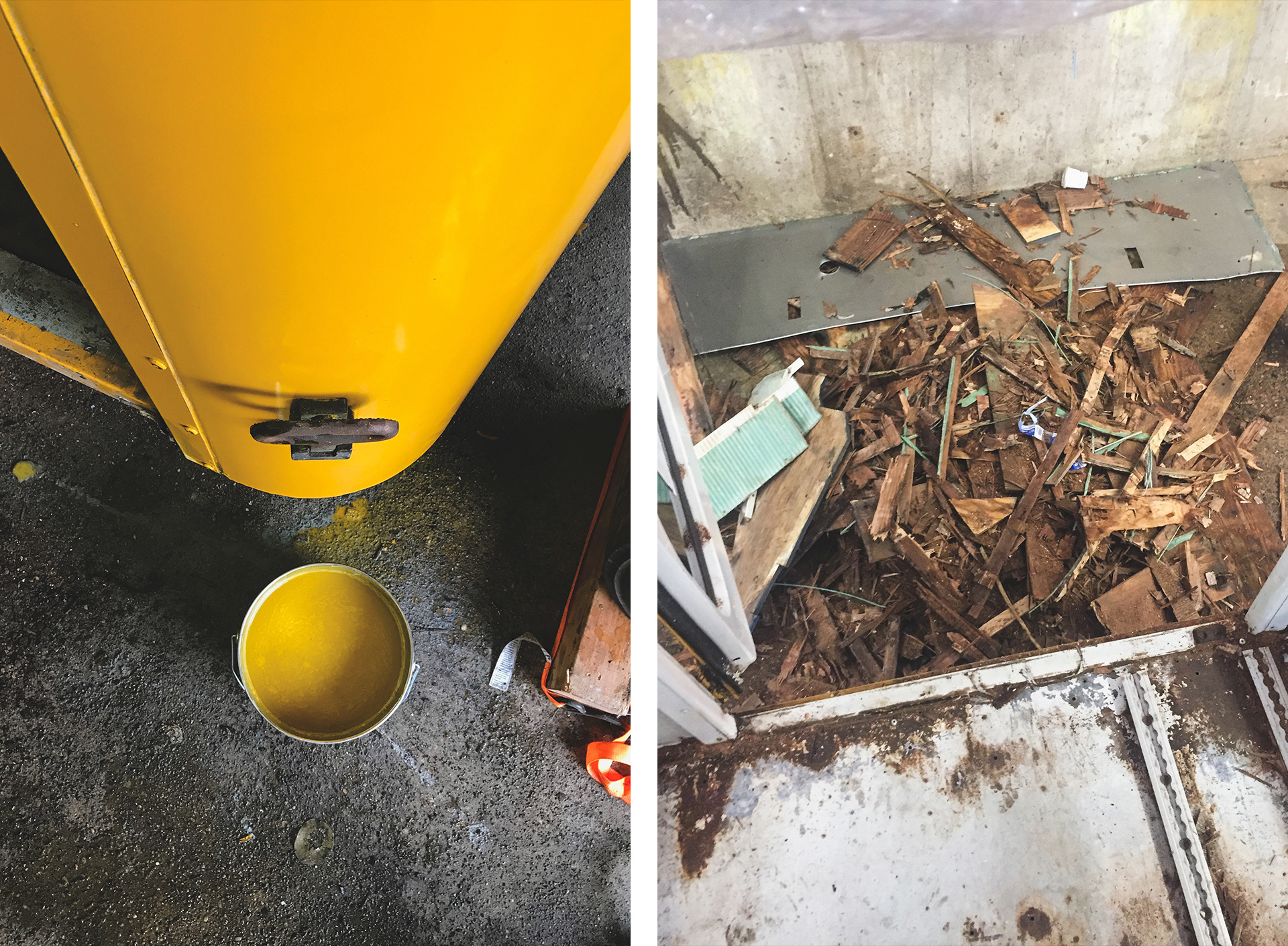
Looking back on it, it was funny that even though I wasn’t working on the bus, I felt stressed all the way over here in Chicago. It was probably due to the tasks needed to get done, lack of communication due to the bus work, and that I had just moved into my apartment. – Mike Spizzirri
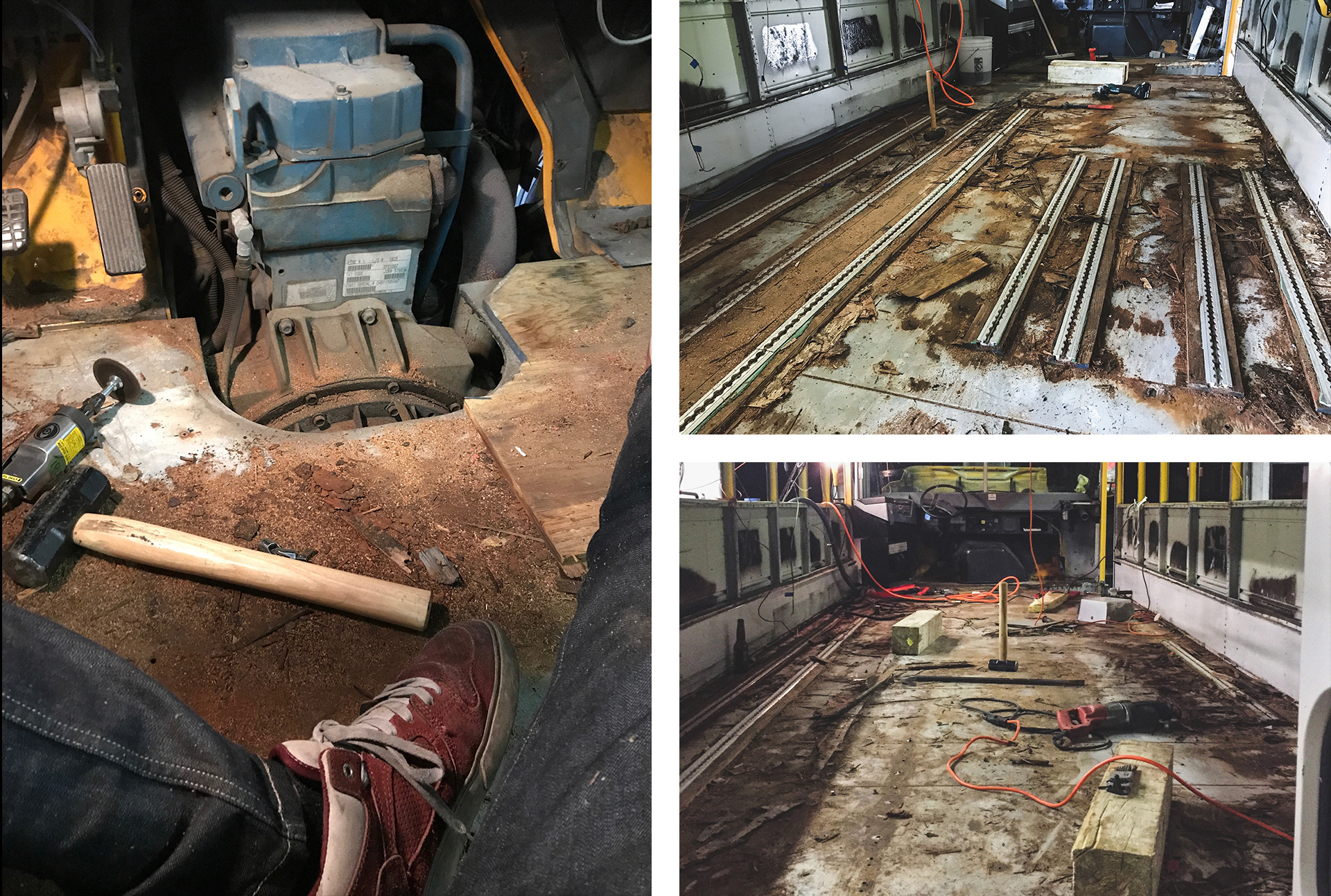
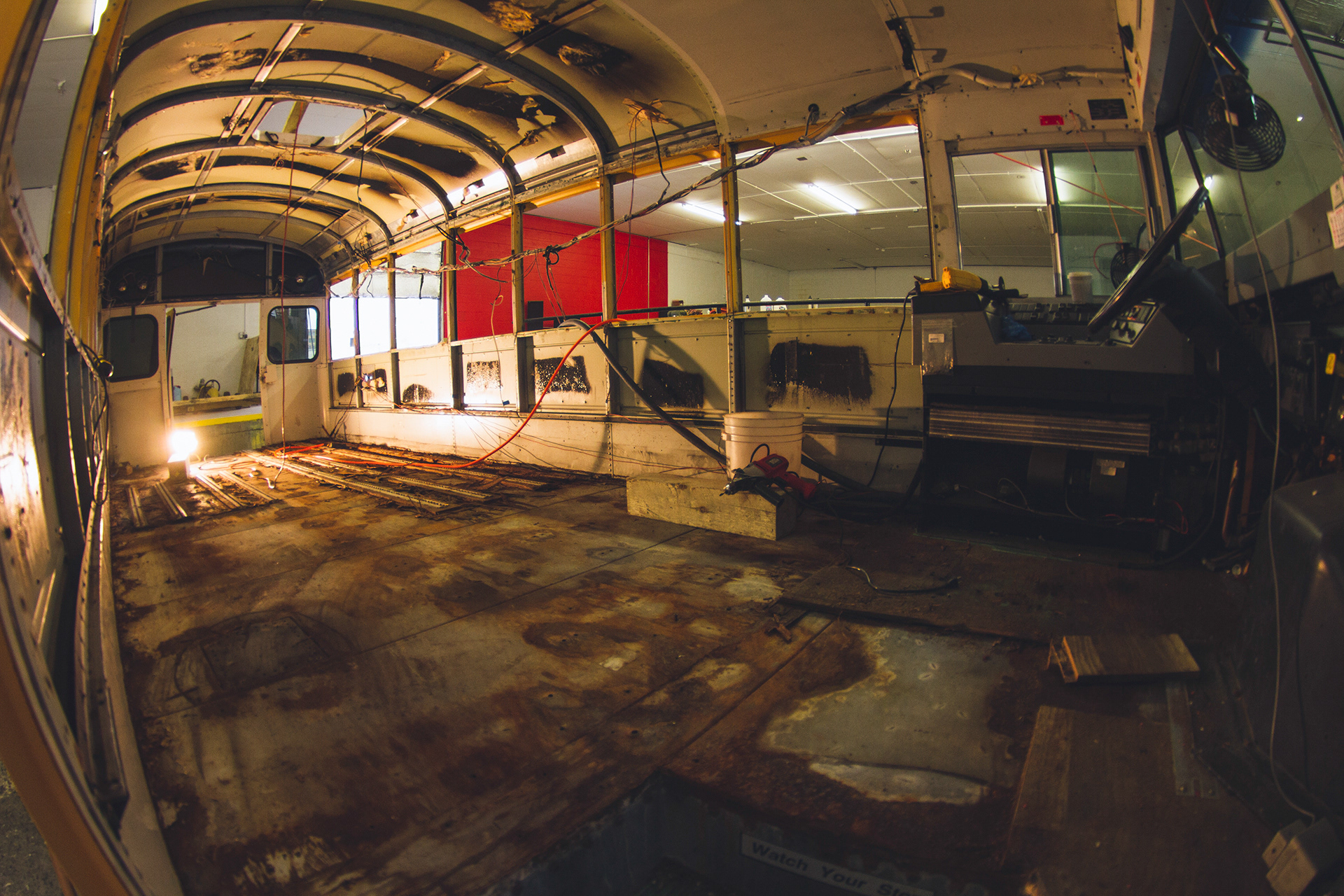
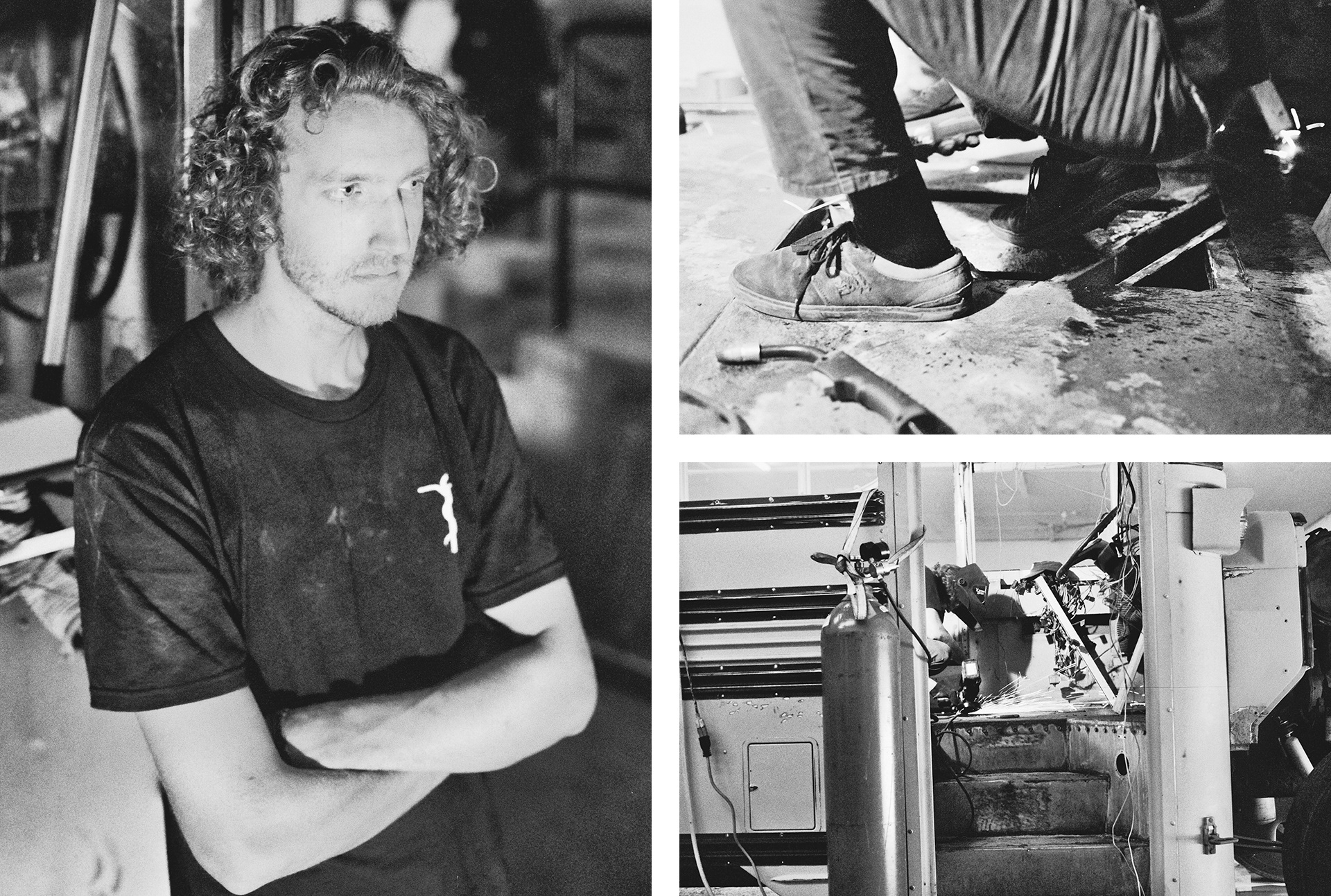
Once we had the floor exposed, we noticed the drivers side floor was pretty rusted and weak. We were afraid of the rust continuing and having a case of a Flintstones episode on our hands. Once we started cutting into the floor to replace the metal we found out it was welded and supported by the subframe which meant things got a lot harder. This was our first “in over our heads” feeling since we bought the bus. As we got further and further into the bus work, these feelings came up more and more frequently. Collin lost a lot of hope in that 2-3 hours of tearing the rusted floor out. Eventually it came out and a new piece got welded in. The floor was looking brand new!
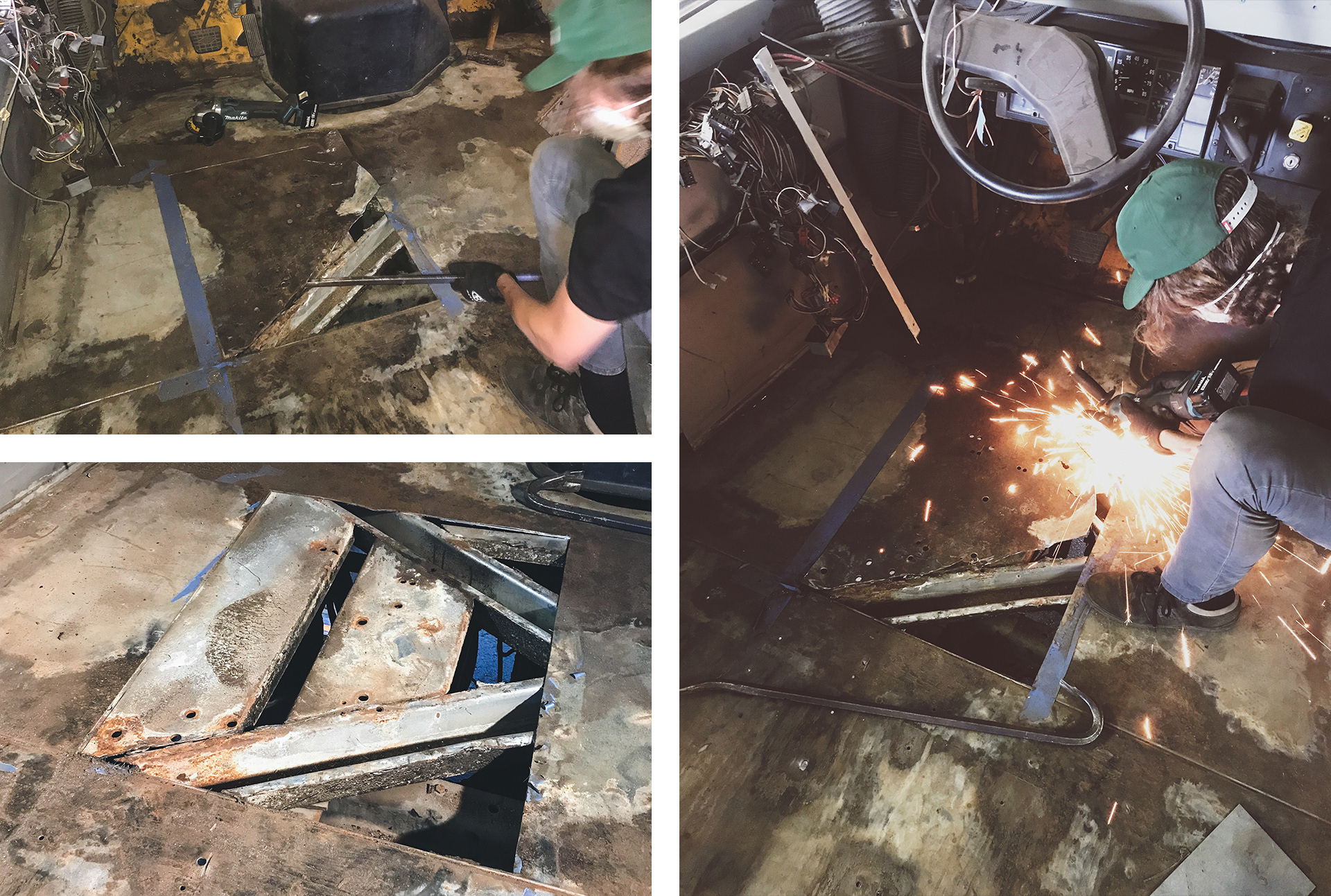
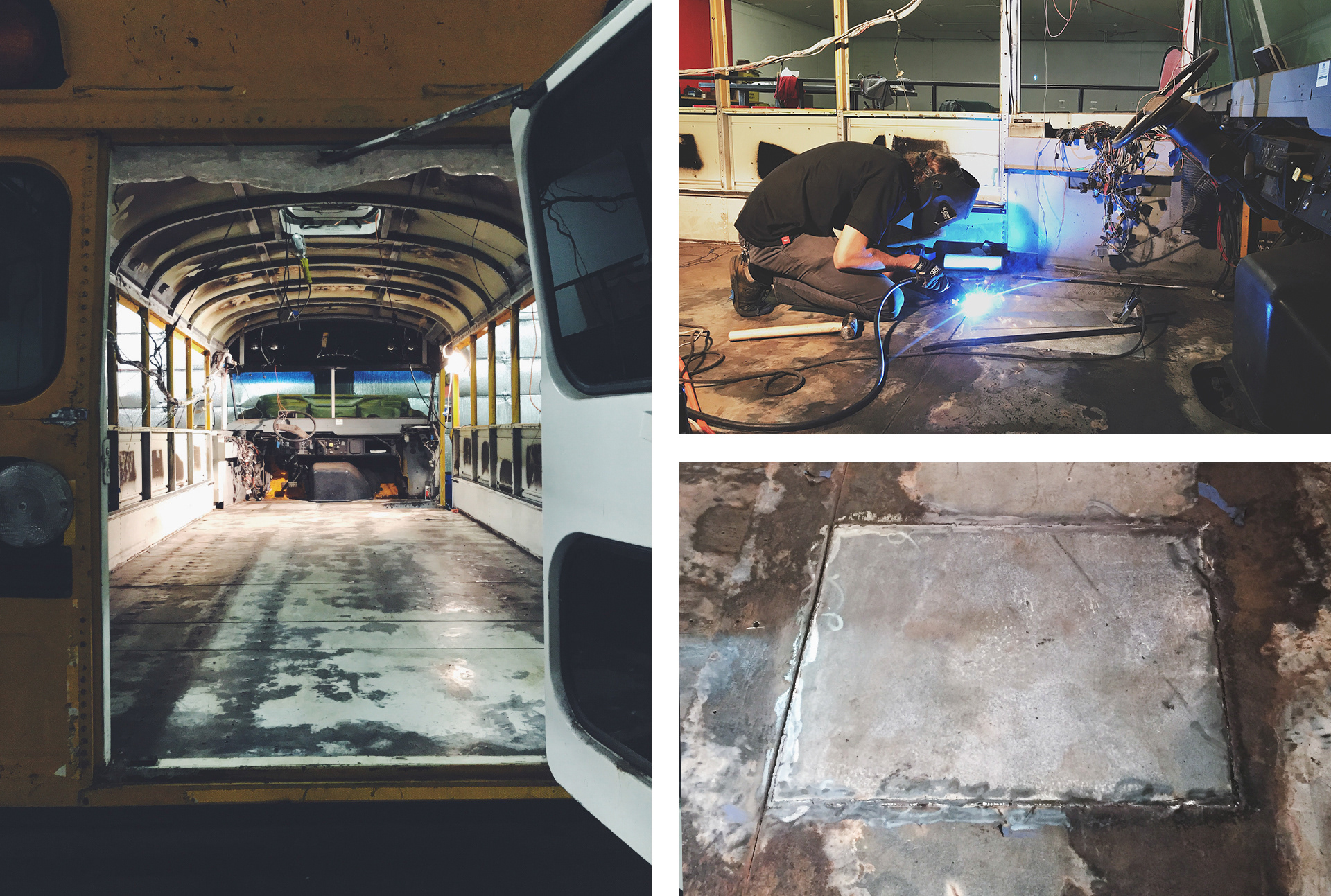
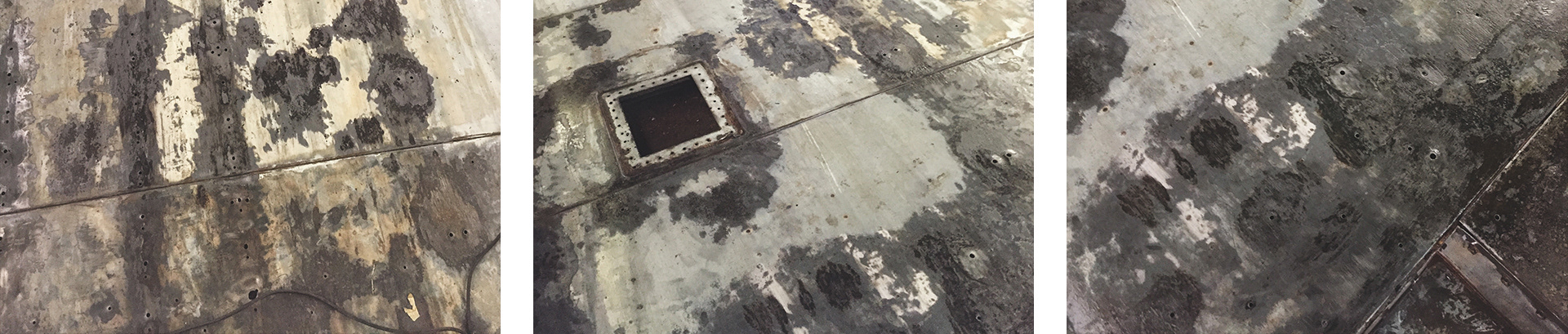
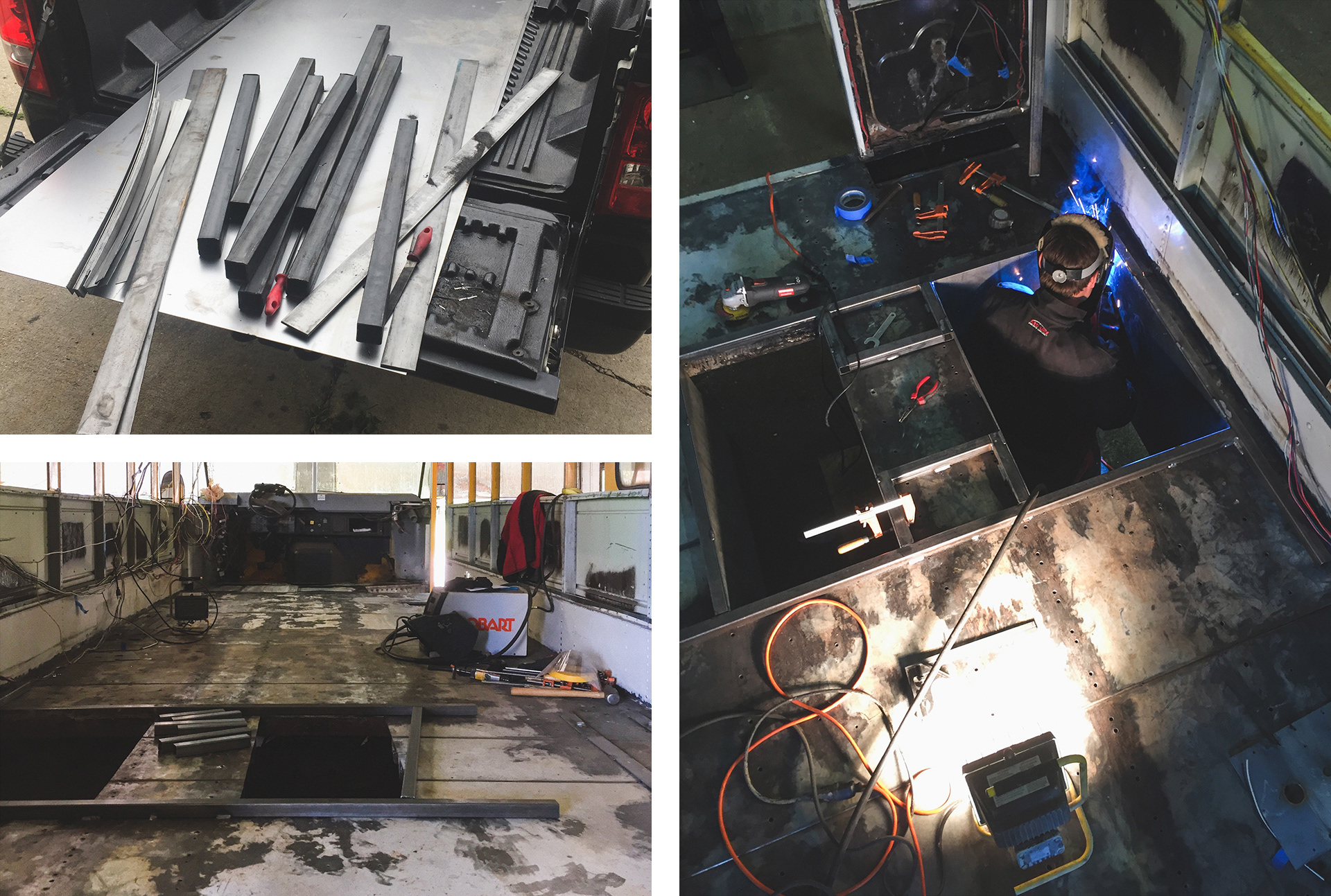
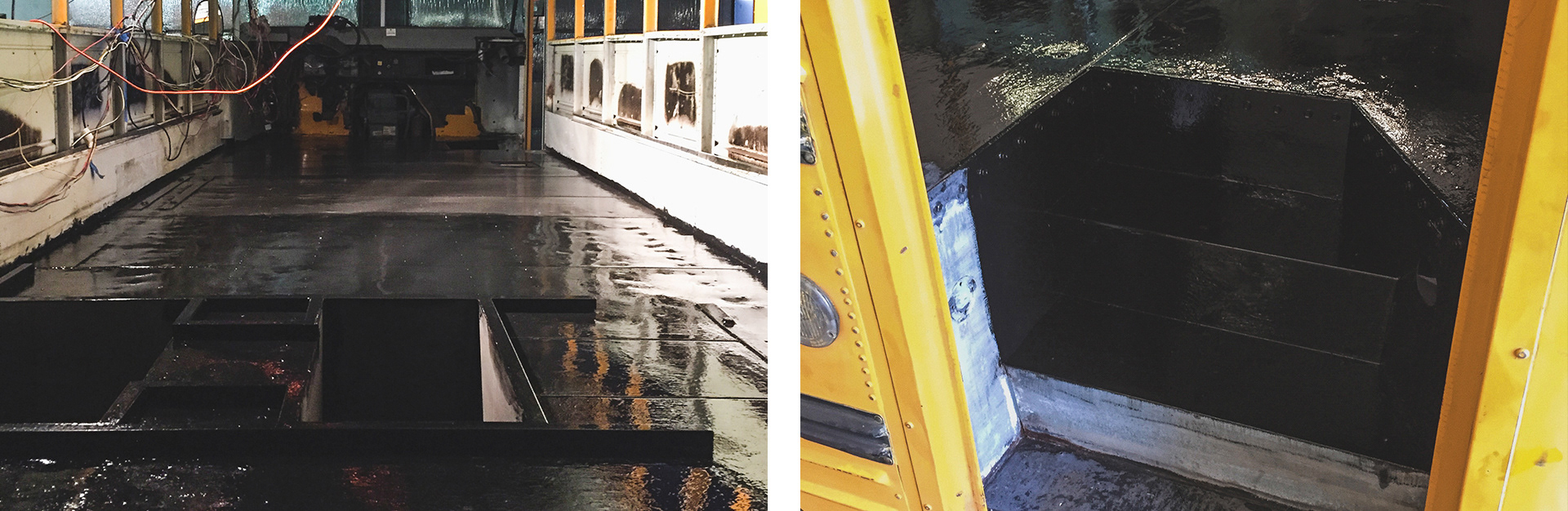
Since we weren’t just building for this years bus trip, we had to make time for our future trips which could involve being somewhere that doesn’t have clean water. Collin laid out two compartments that forced us to cut two holes in the floor. The holes then received walls and a base to create two boxes for grey water tanks. Braydon, the local DIY builder, lended his aerospace welding skills. He helped on multiple tasks with the bus like the side exhaust and toolbox. As long as the beers were flowing, the welds were stacking.
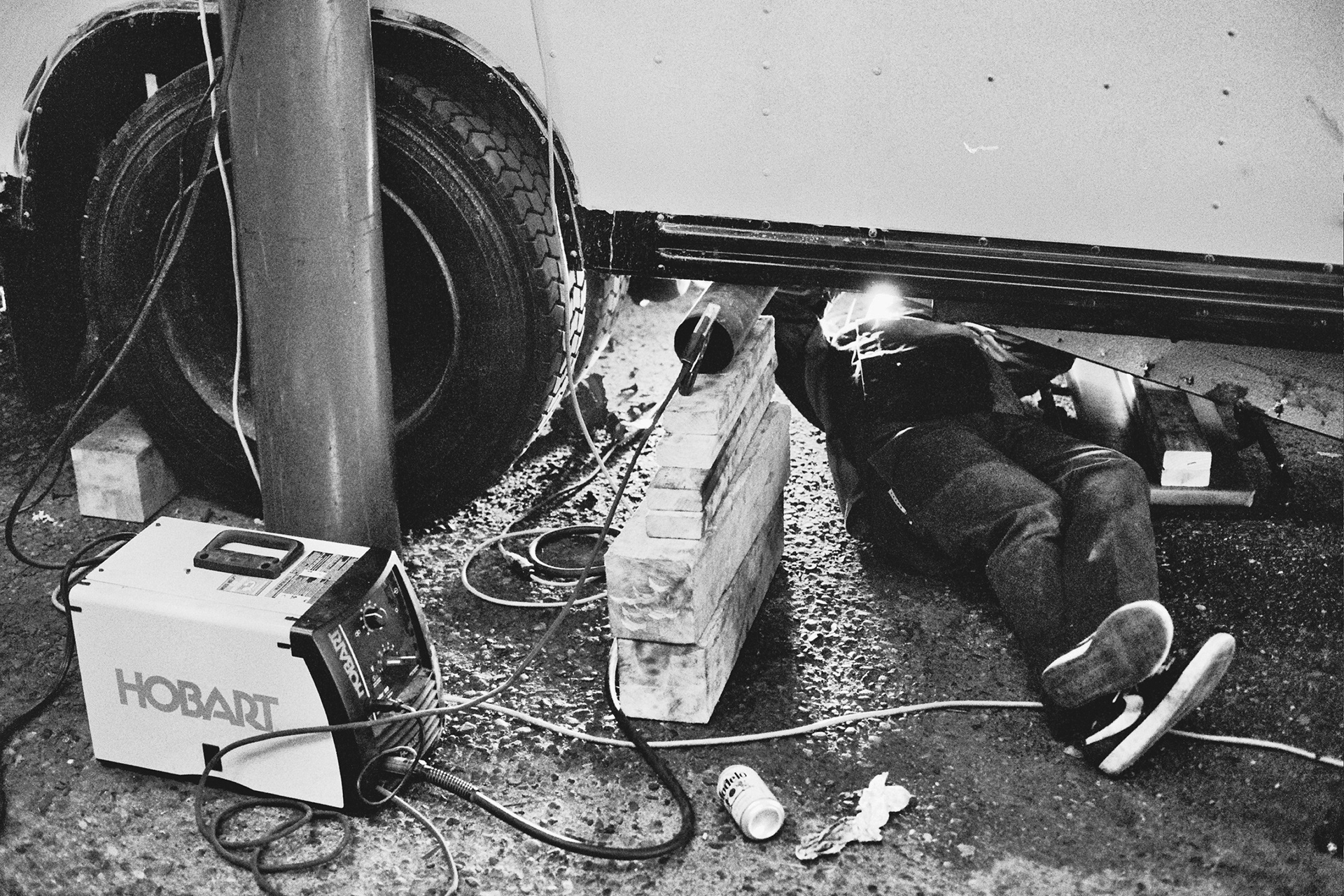
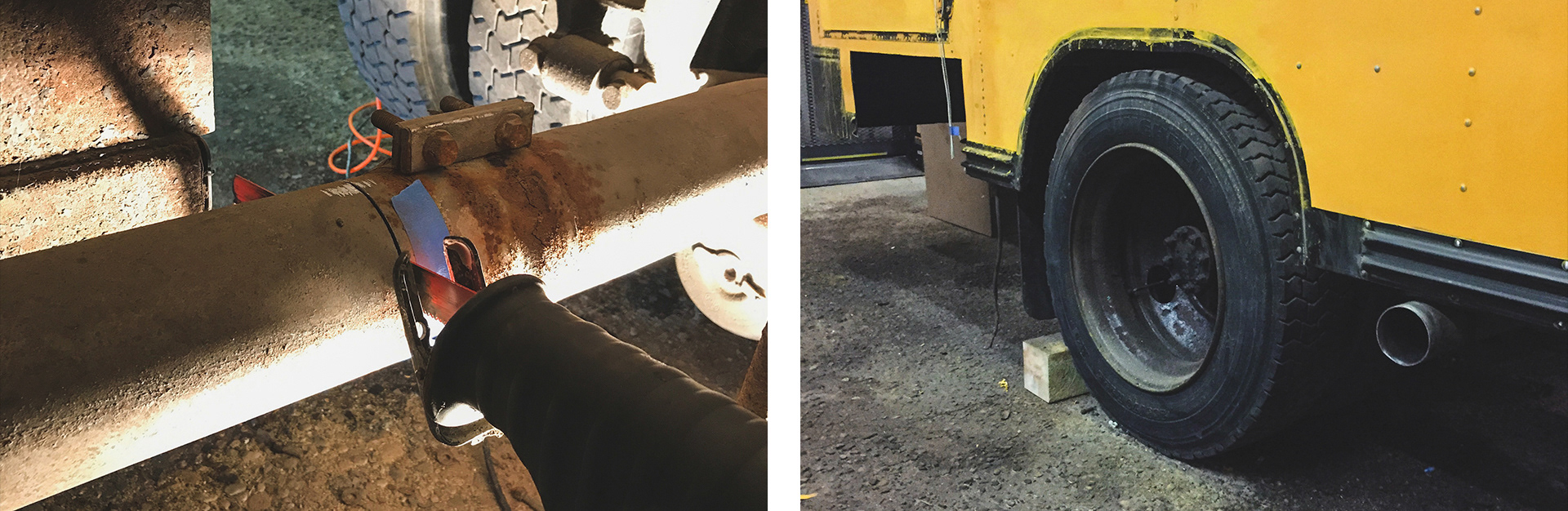
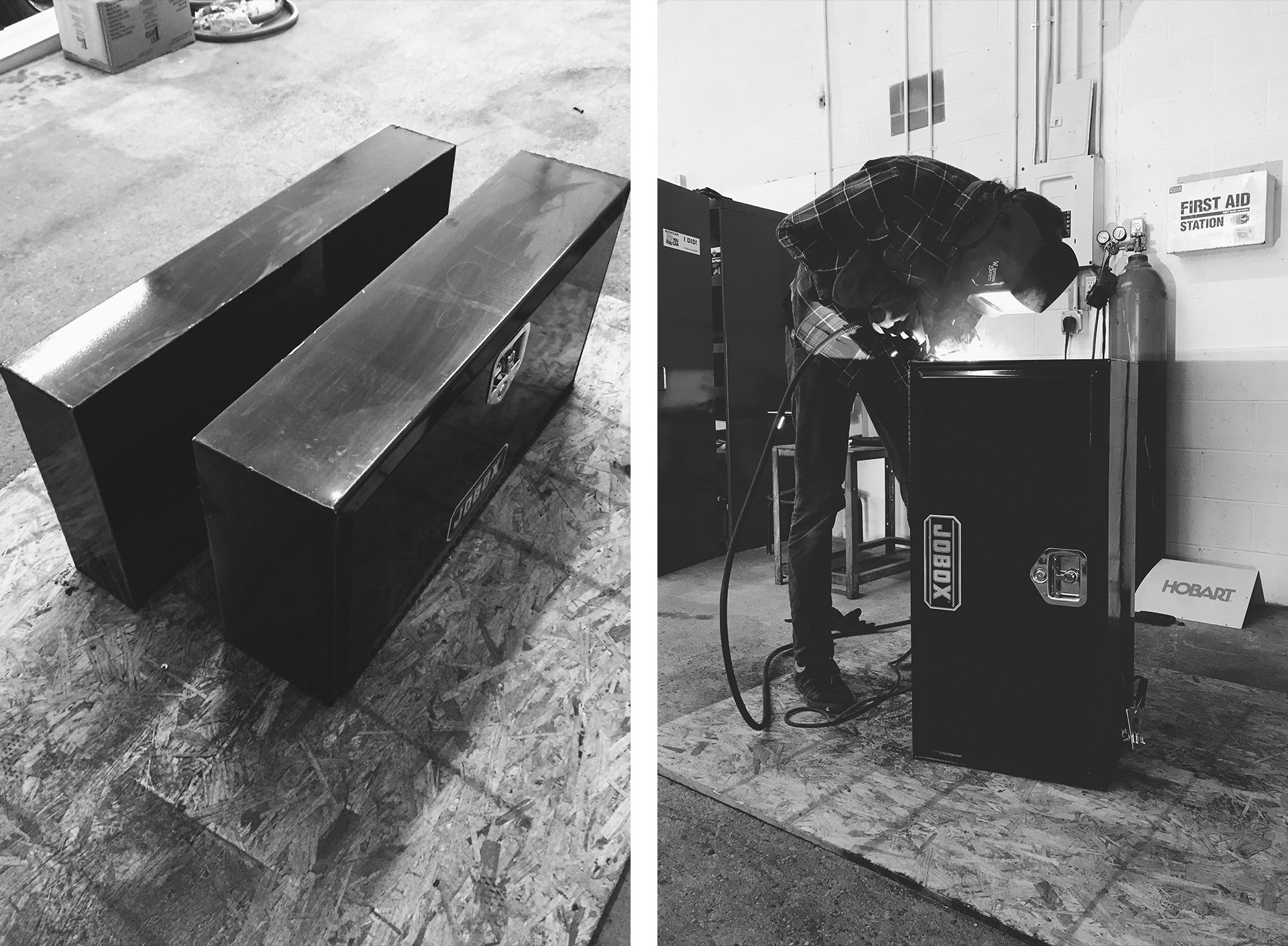
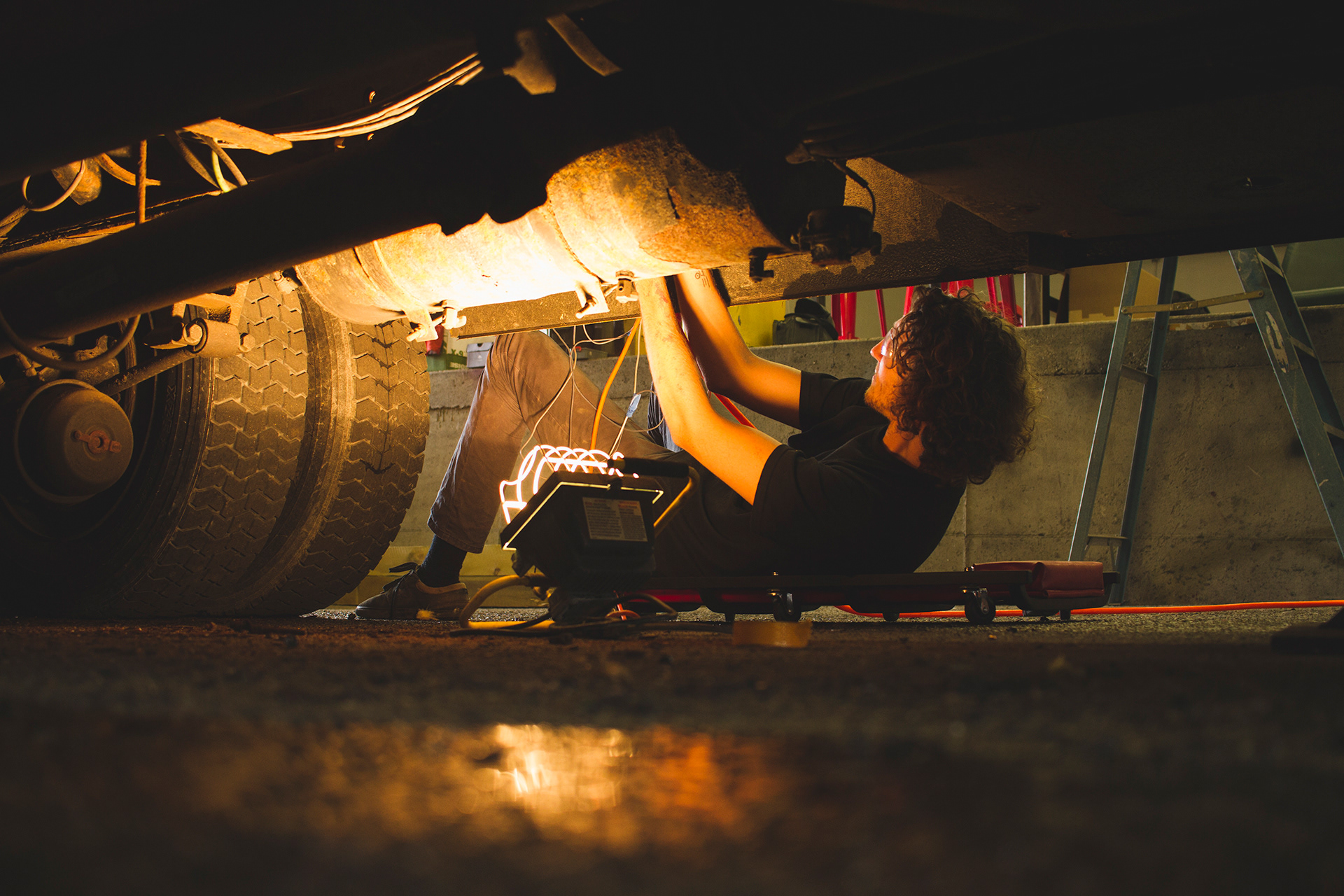
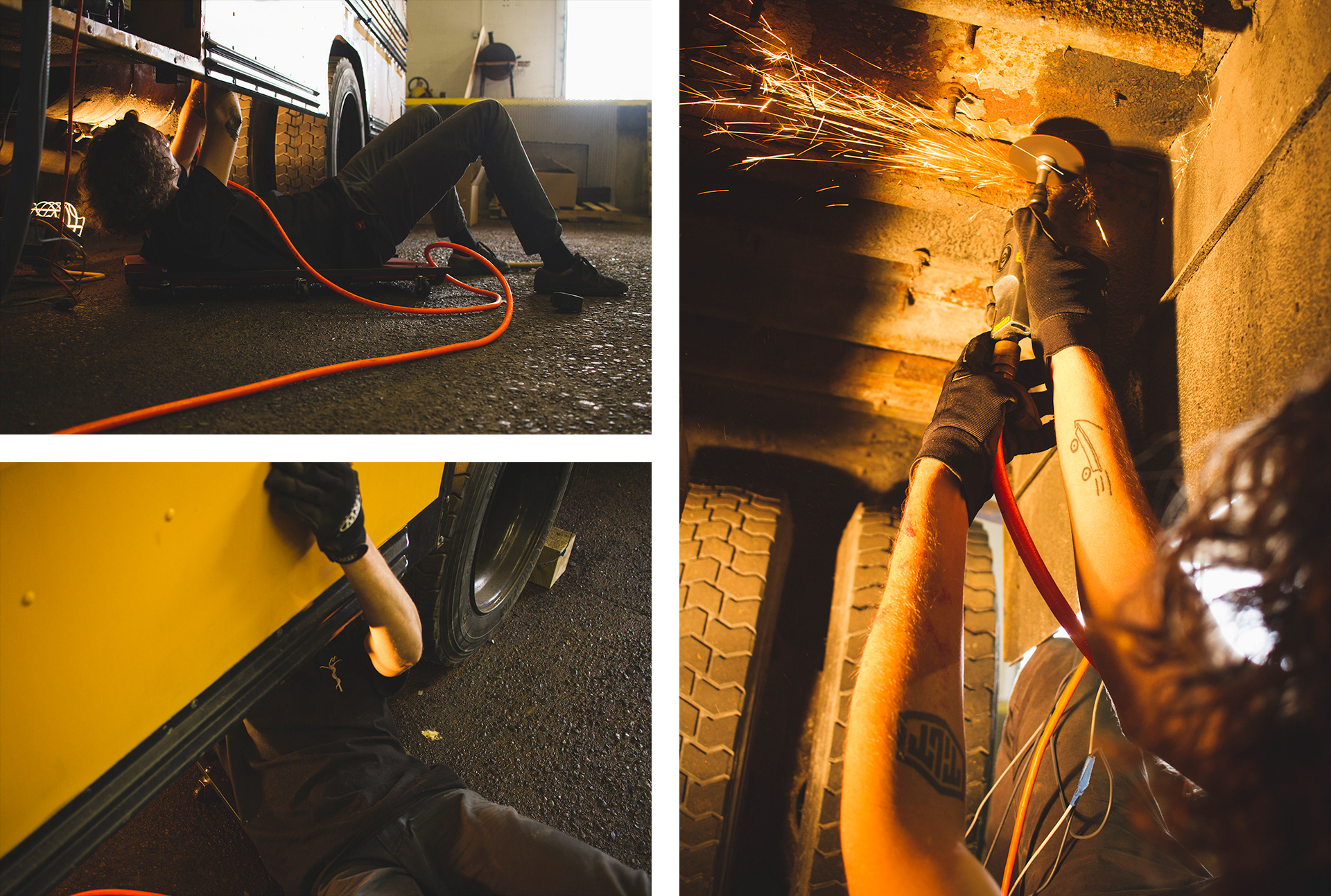

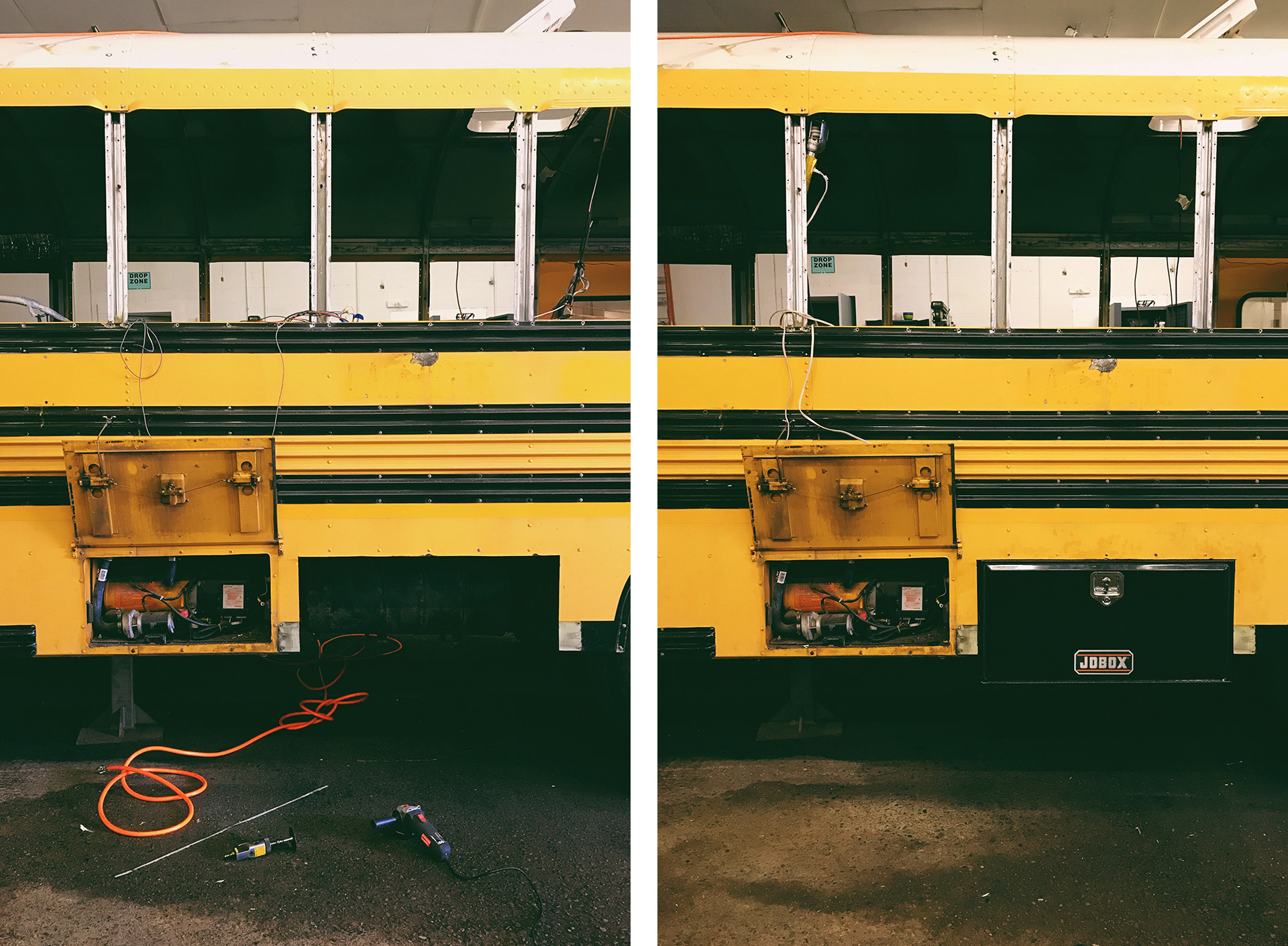
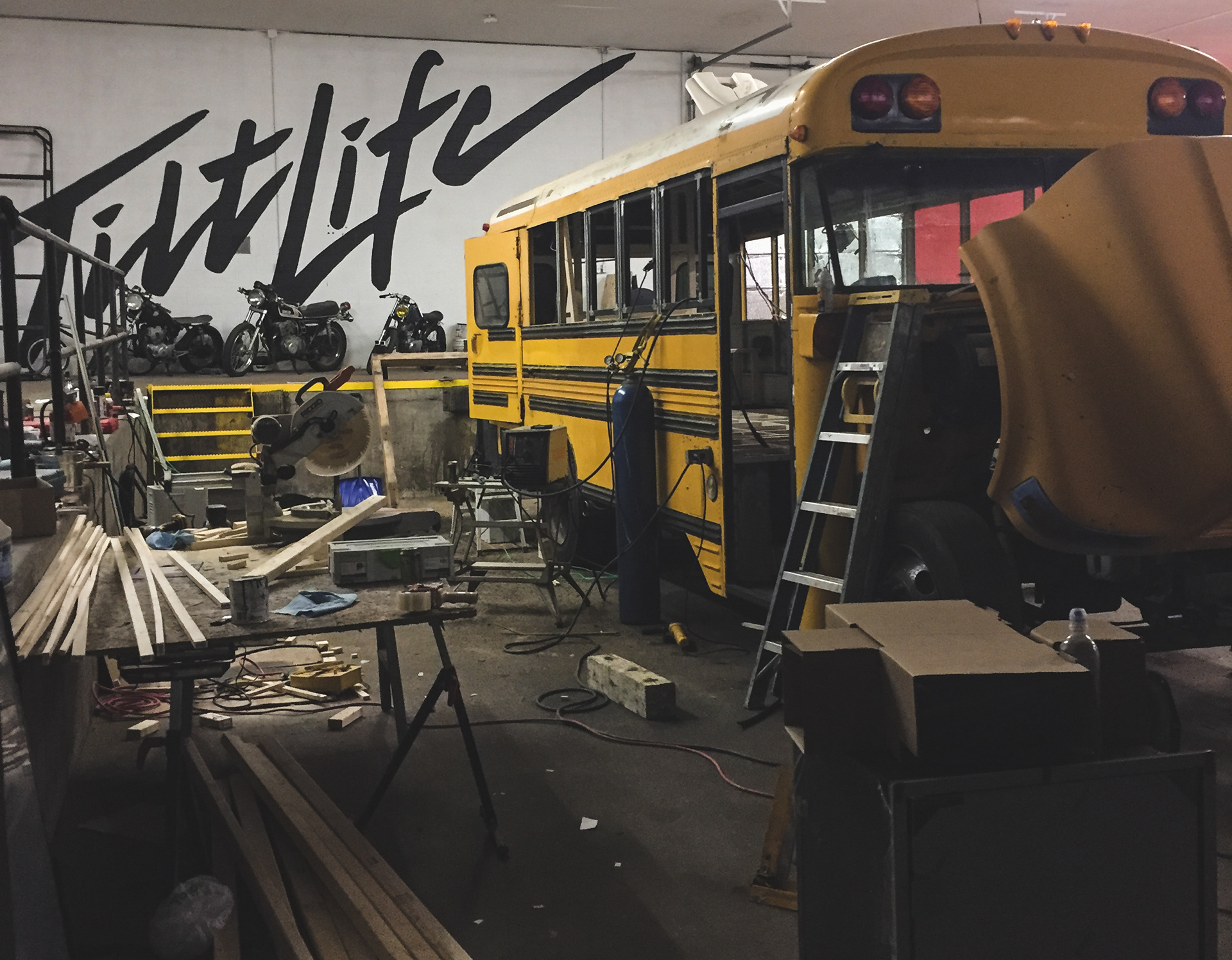
While things were happening on the outside, William was making things happen on the inside. We had a deadline for insulating the bus so he was working quick. The entire inside was gridded out and framed.
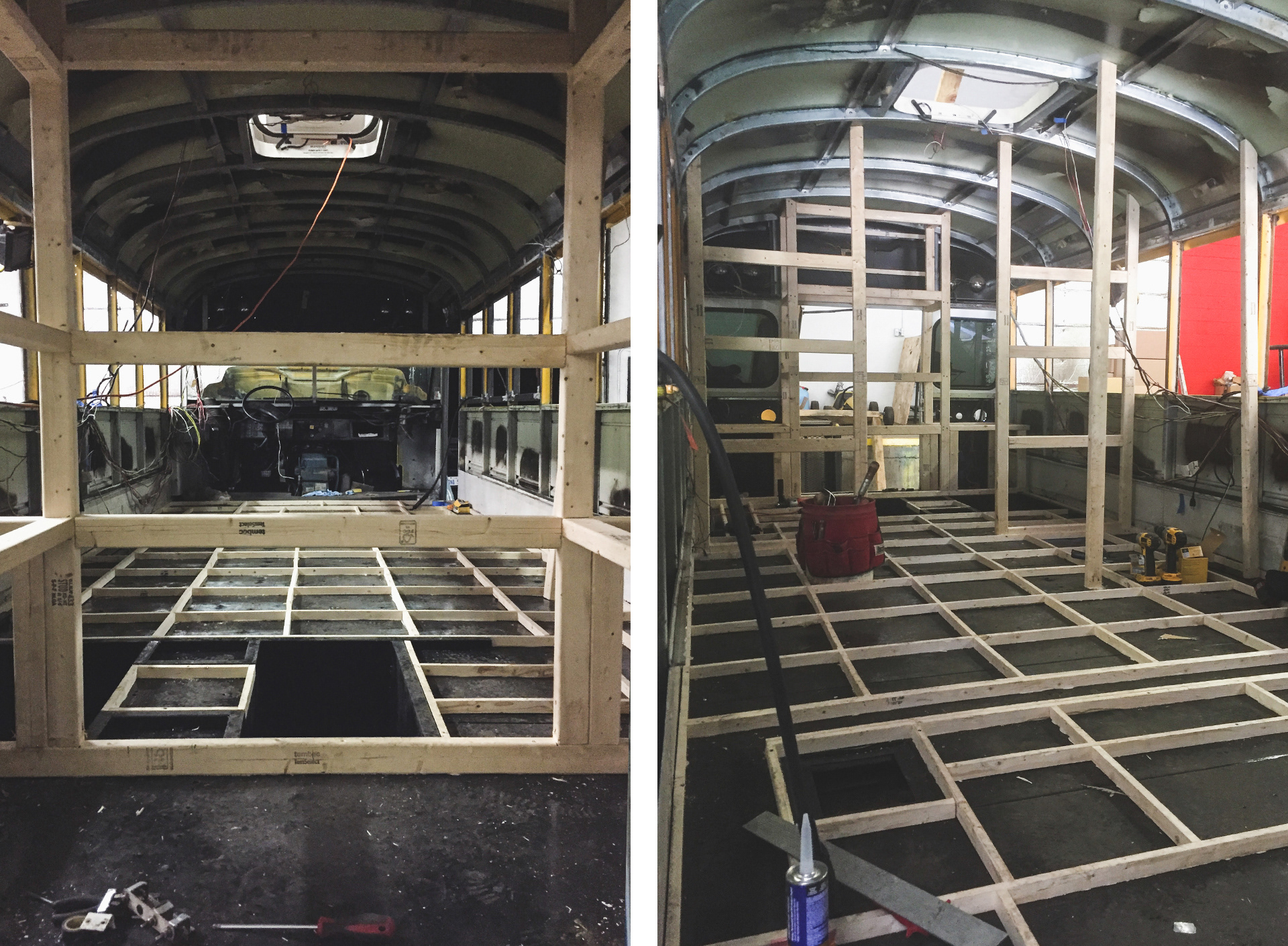
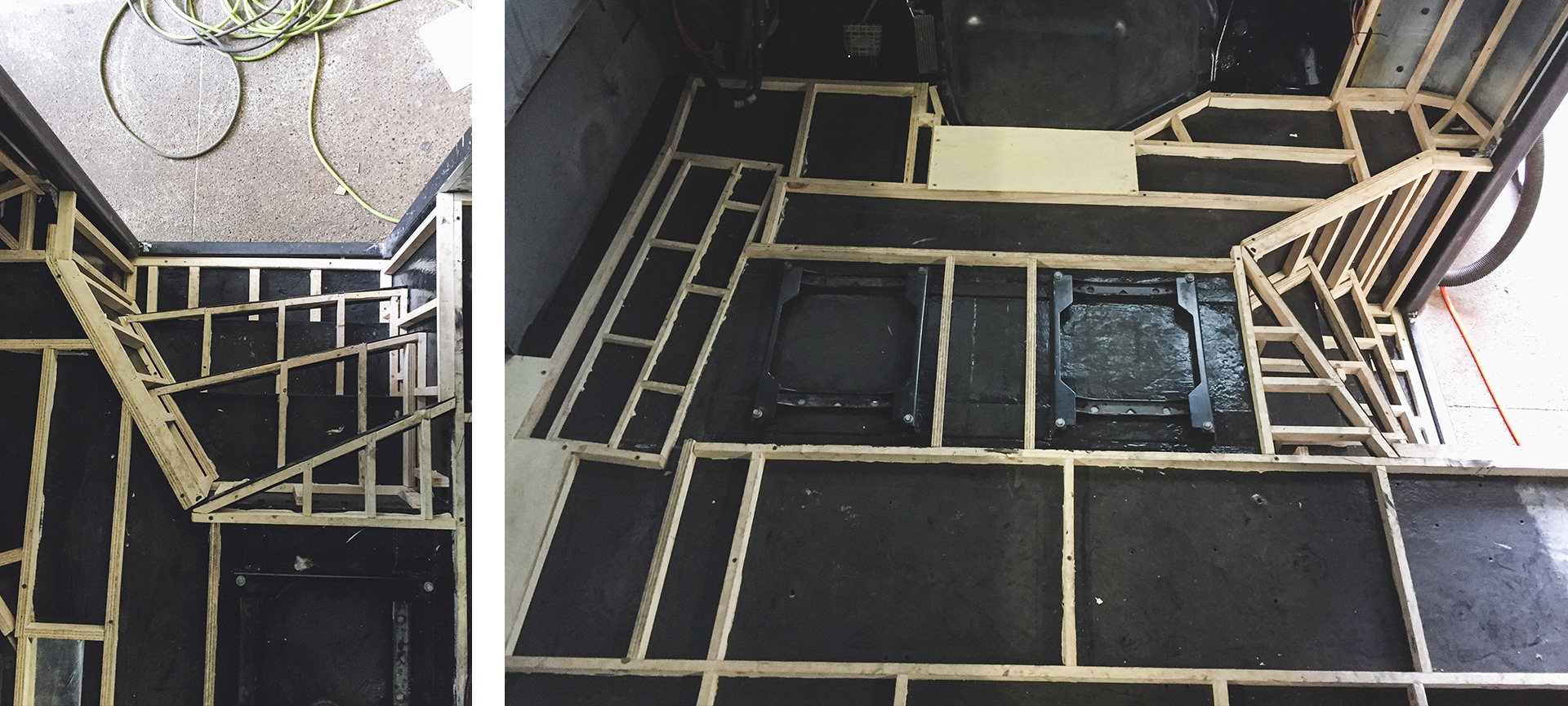
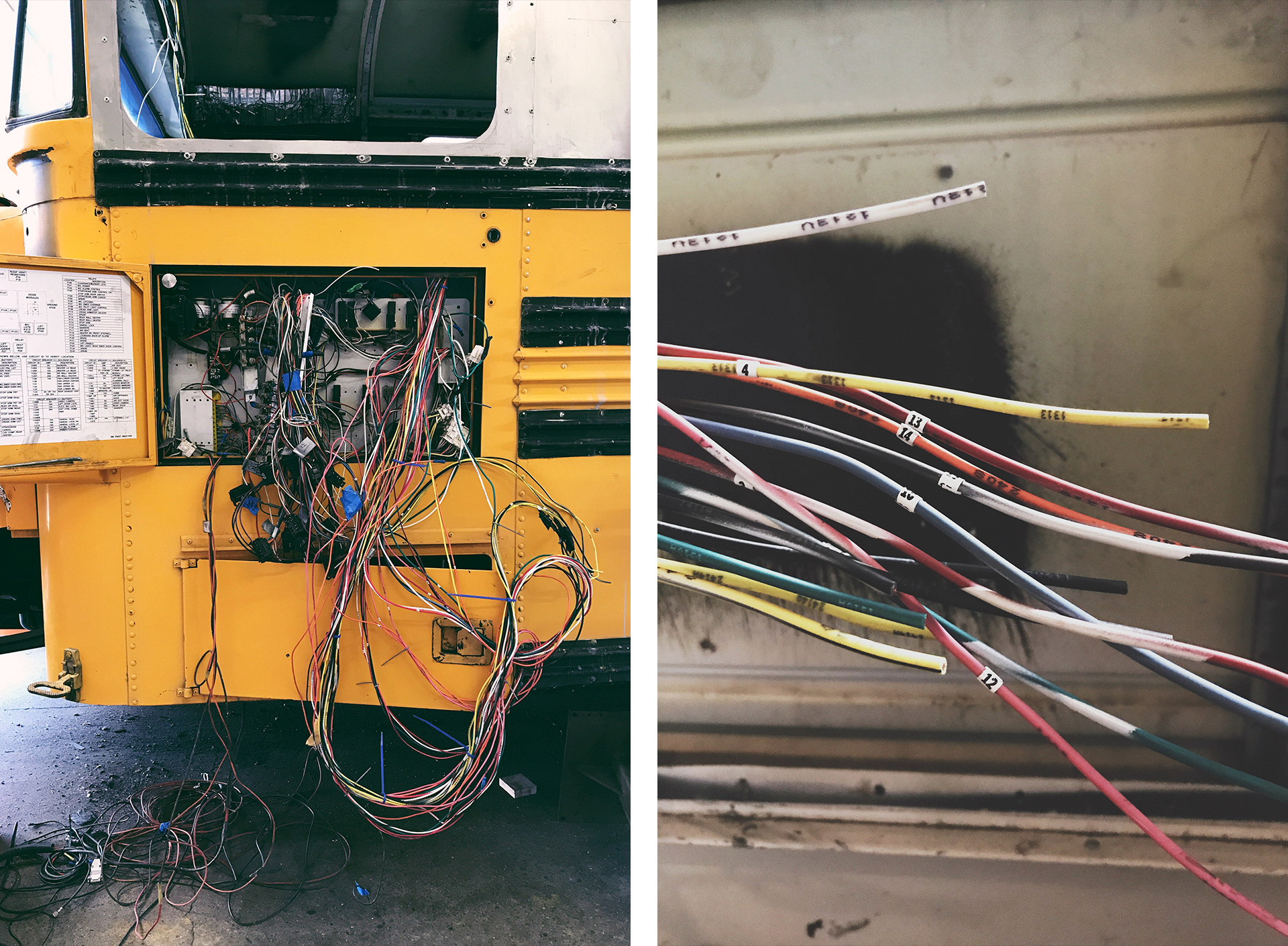
More wiring was taking place. Now that most things were stripped away, it was time to lengthen wires, run new wires and repair anything that needed repaired. It took Chris a little bit to wrap his head around things but it reminded him of all his legos he use to build back in the day. One wire at a time is the same as one block at a time.
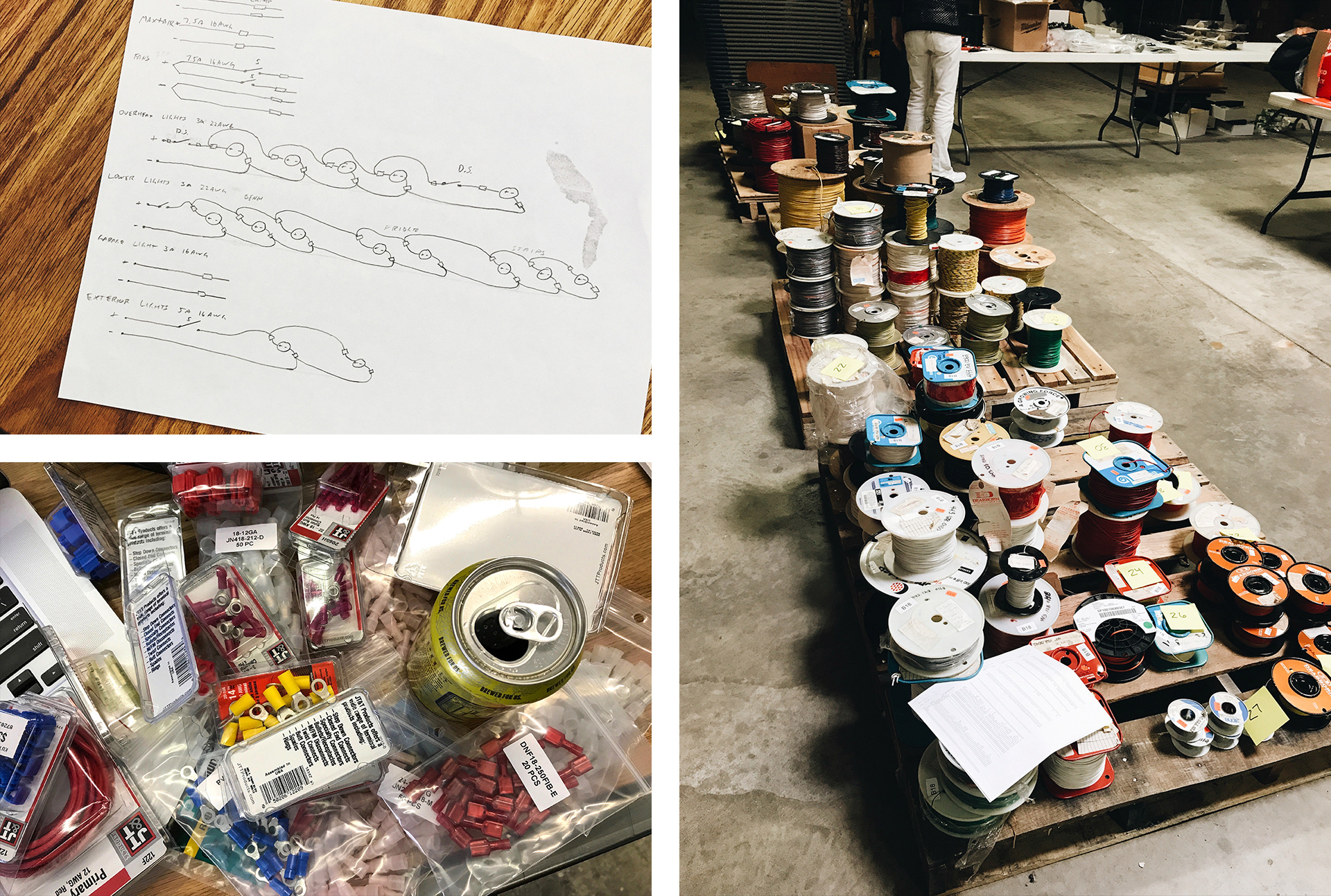
Collin started on the interior electrical supply since we wanted lighting, outlets to charge batteries, and a fridge. He welded a battery cage, painted it and then laid out switches and connectors to keep everything neat and safe. This would later go underneath the bench on the passengers side of the bus.
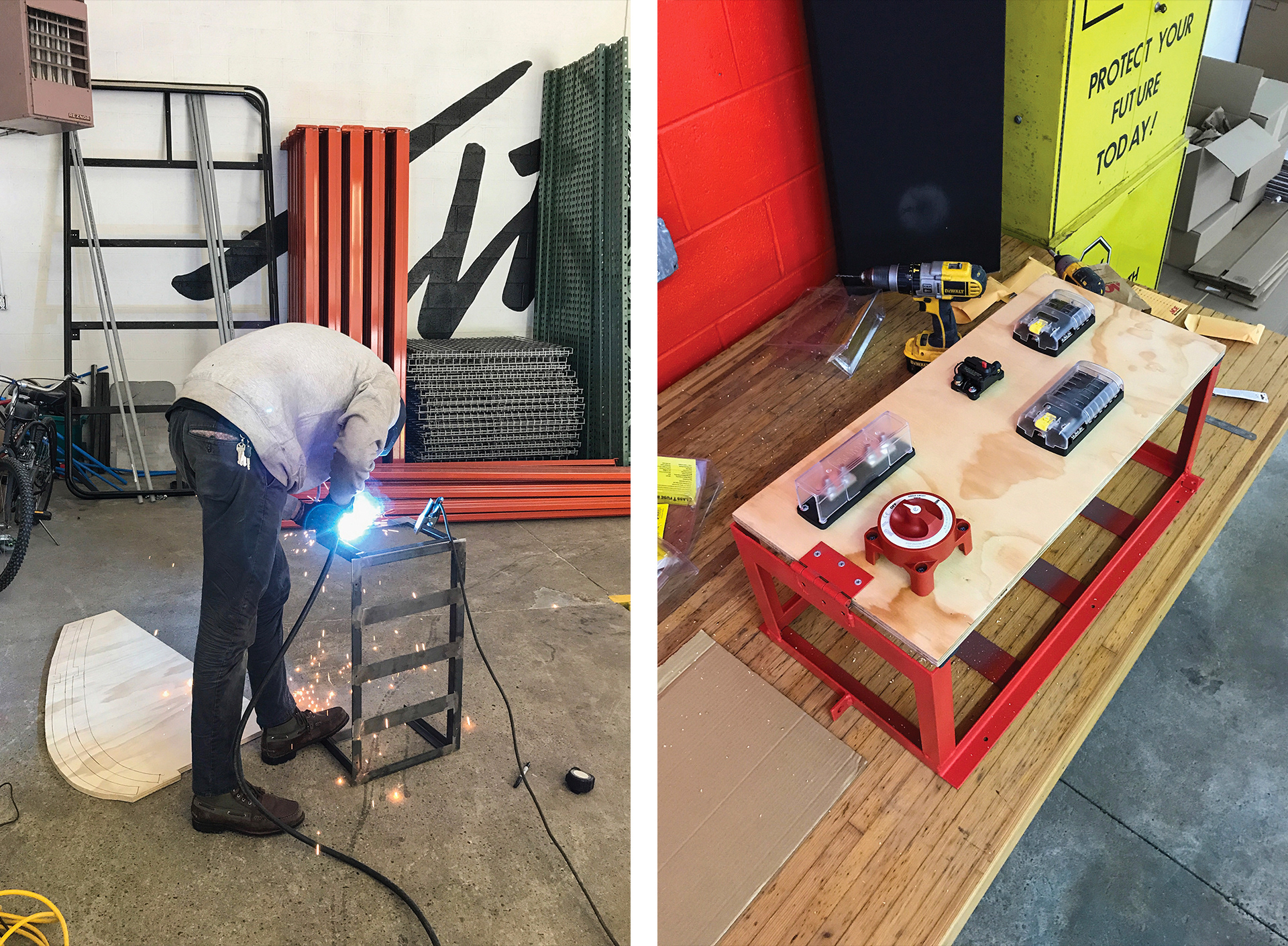
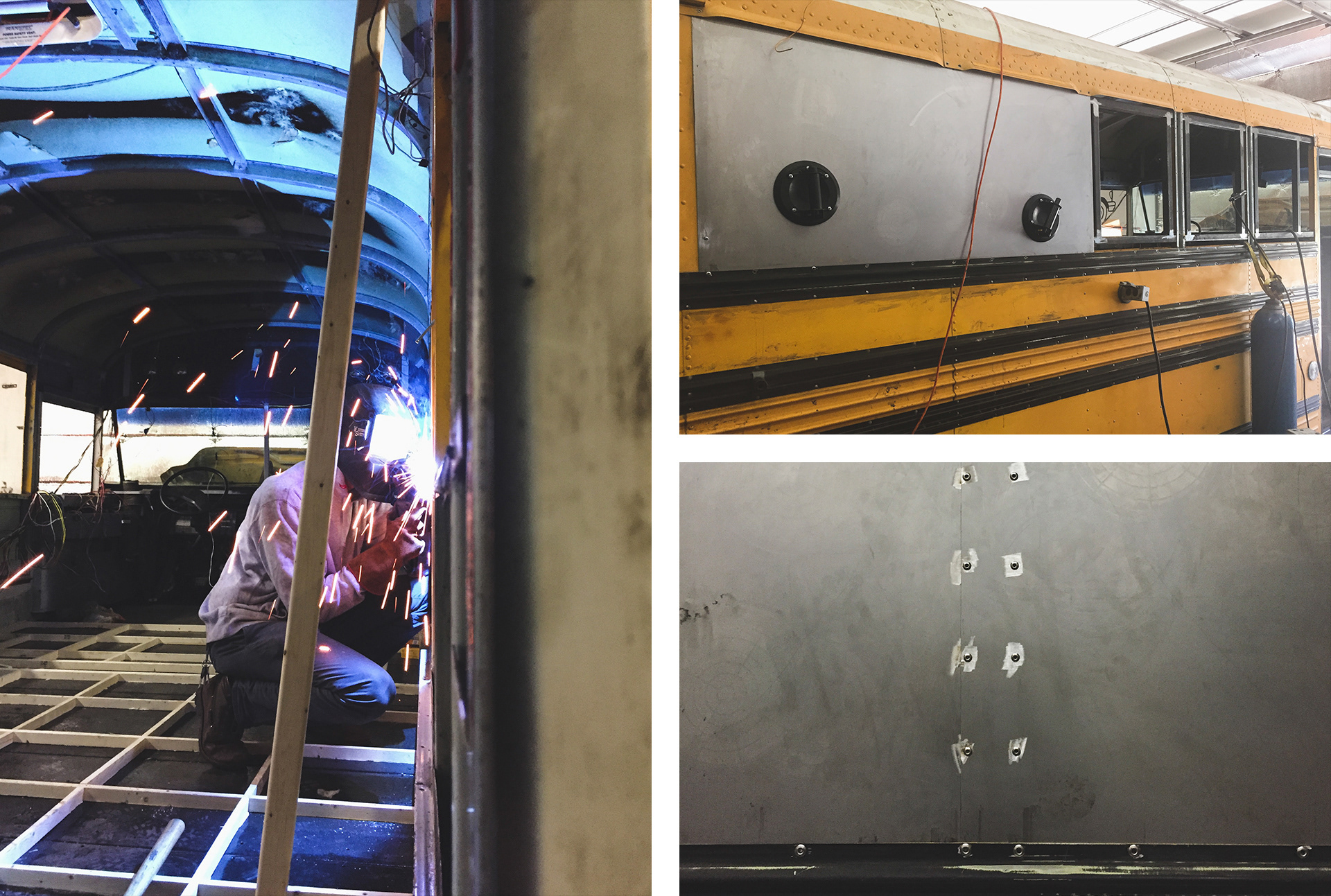
Since we tore out all the original windows because they were poorly insulated, we now needed to make a new way to hold the windows we bought online. Luckily the bus had a bunch of vertical support beams that we cleaned up with a die grinder. We then used sheet metal, 1 inch angular tubes, rivets and Collins welding skills to get the job done. Once the sheet metal was secured with rivets, we held up the new windows were we wanted them so we could draw an outline so we knew where to cut. We drilled holes and used a jigsaw to trace the line and ended up going through four blades trying to cut out all of the windows. It was ridiculous.
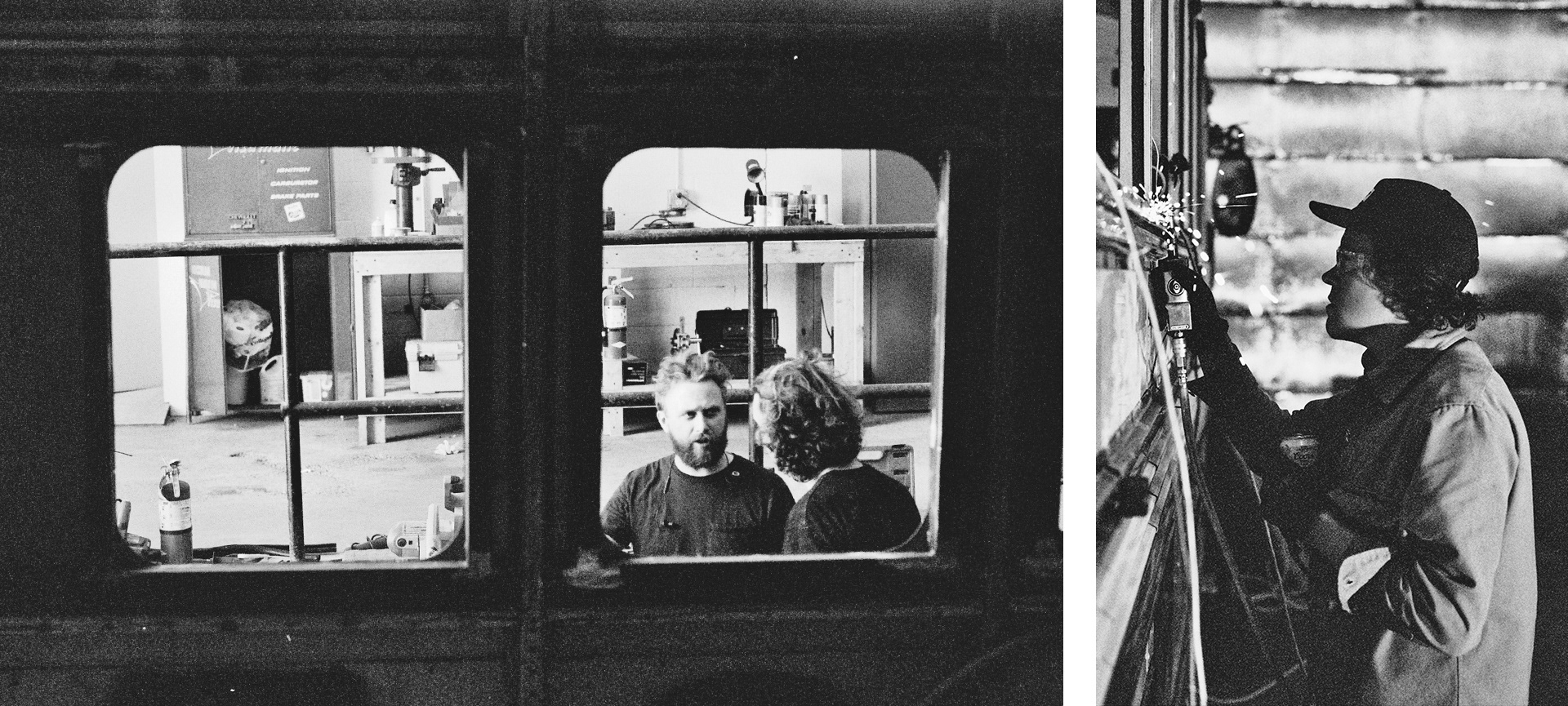
I basically moved up to Grand Rapids for a month and a half living at either Collin or Dante’s house depending on the week. It was sweet because I always wanted to live in GR for a couple of months because it was like a smaller Columbus and I have friends up there. The only thing that sucked about that is the bus took 90% of my attention, even my dreams weren’t safe. Eye twitch, you bet ya. My muscles were so sore that I was used to it and I started noticing how sore my bones were. Countless cuts, scrapes and bruises. I hit my head once a day and at most seven times in one day. I had an old sentry bar that was cut at the weld that I would use to beat up wood pallets with to get my frustration out. – Chris Martin
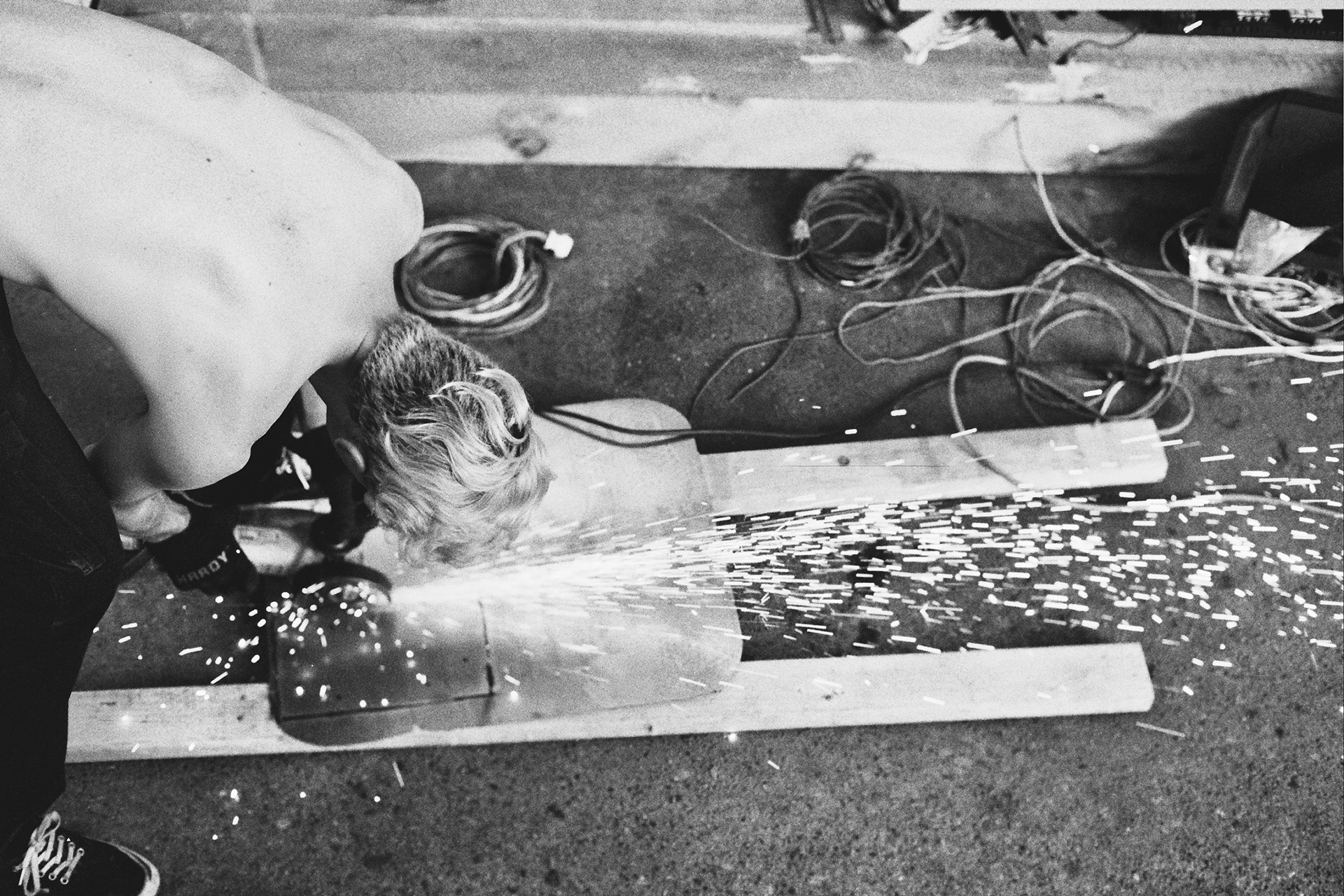
Some days, you'd walk into the warehouse with what seemed like a never-ending list of things to do. Yet, somehow you'd manage to check almost every single one off of the list. Those were good days. Other days, you'd have a list consisting of one or two tasks. You think "Oh, today should be easy. There's only a couple things on the list." Come to find out, that one thing ends up taking almost 7 hours to finish. Those were the days we'd end up working until midnight, just to wake up at 7am the next morning and start all over again. In conclusion, there was no "easy" day working on the bus. Every day was a struggle, but damn was it worth it. – Christian Dean
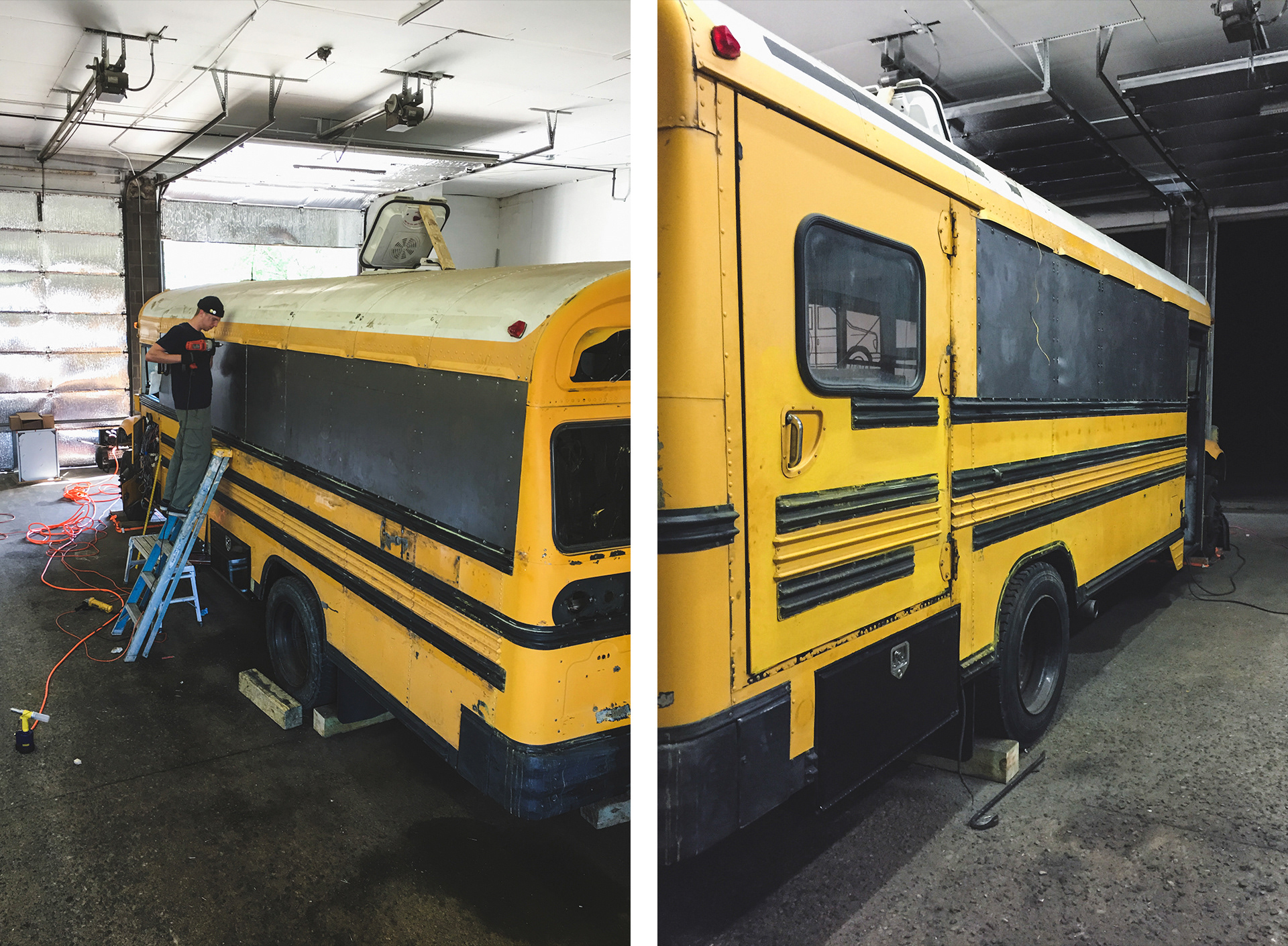
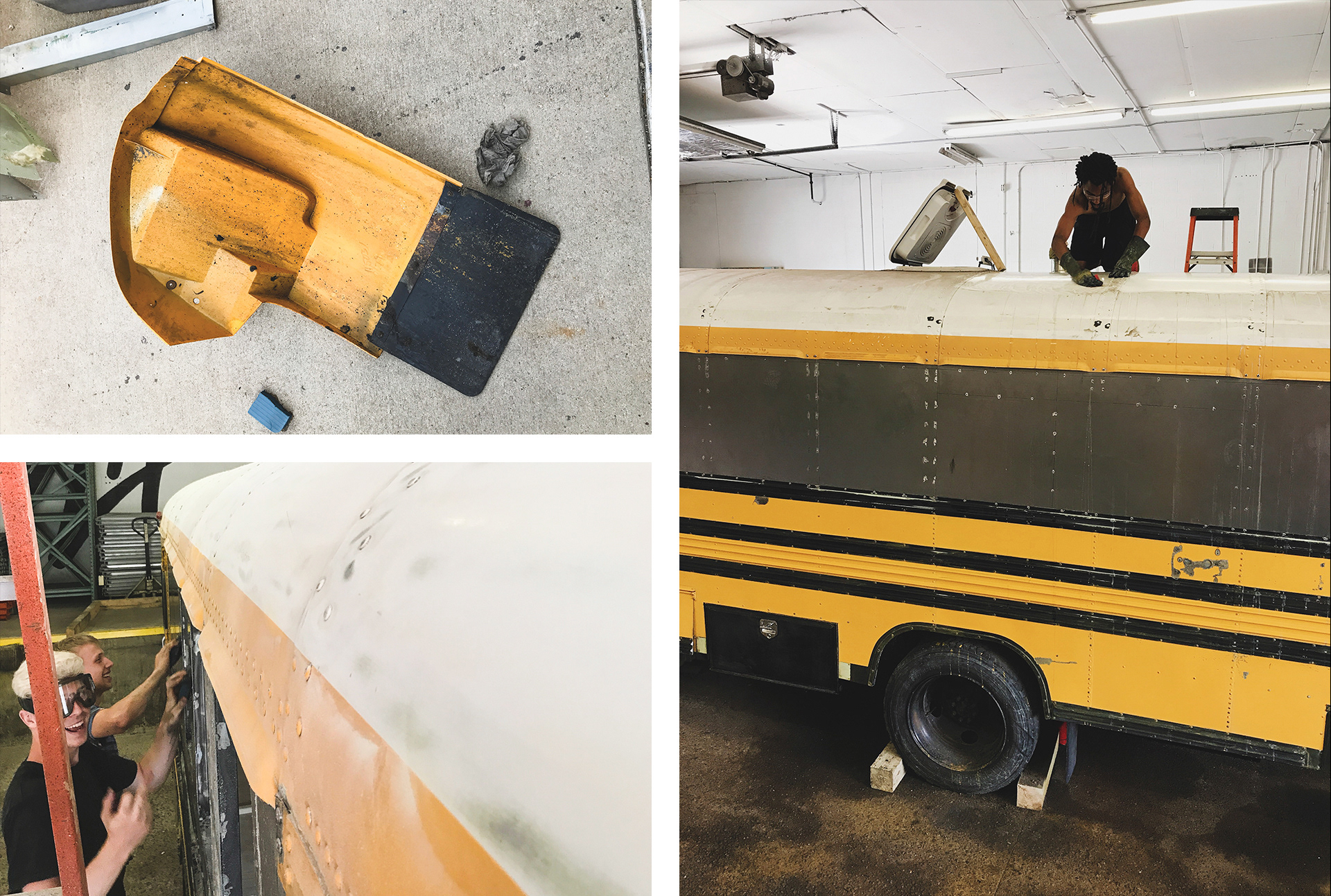
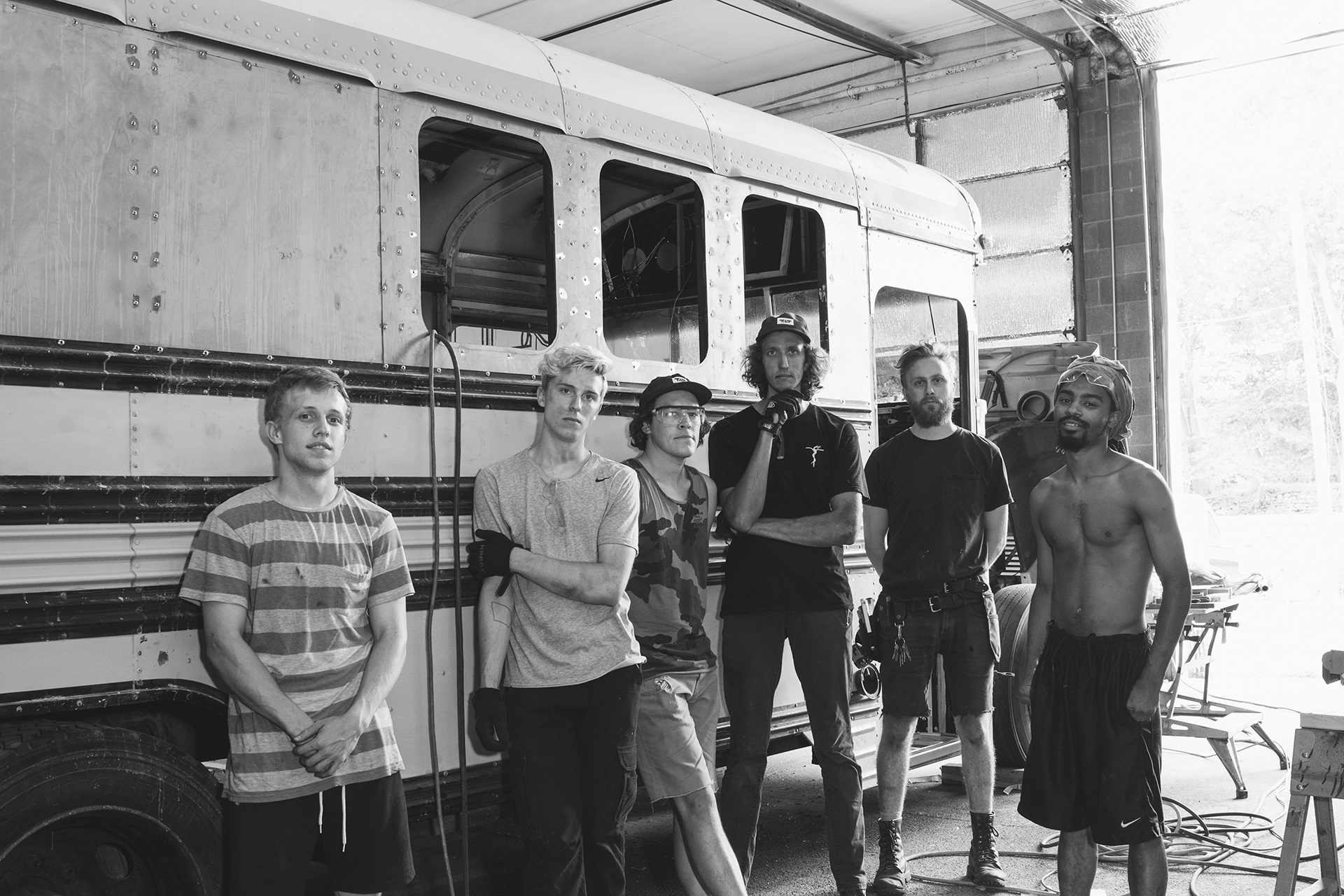
Most of the bus was wet sanded but for good measure, we did another round to make sure all rust was gone while making sure the paint would be smooth and ready for priming. This also was like a hand wash for the bus so we weren’t trapping any dust/dirt in with the paint.
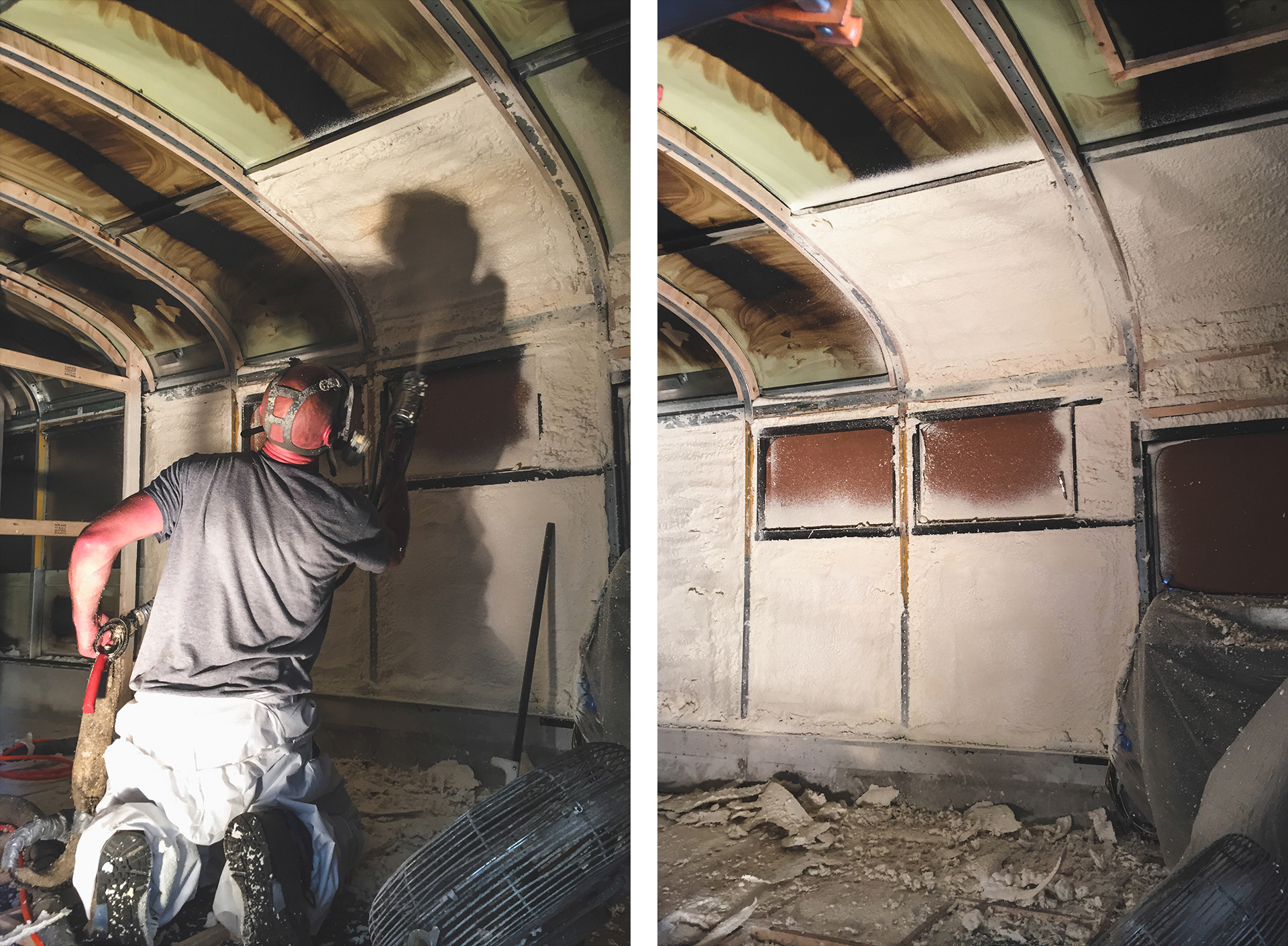
Here is where the fun really starts, The insulation phase. The insulation was sprayed onto the bus using an air compressor. The fumes were toxic so most of the team took the day off from the bus to catch up on other TILT related tasks. Since the insulation expands, William was in there trimming away so we didn’t loose sight of our grid we laid out. The foam cured for some time and turned into a solid. The insulation was laid on thick so we had to trim it down. William, Joe and Chris were selected as the three lucky candidates to tackle this. The first couple of hours, people weren’t wearing the right eye protection and the fibers would get in their eyes. This was a serious issue that made this task extremely daunting. Once we had snowboarding goggles and scientific goggles we were ready to rip. The trick was to use angle grinders with wire brush attachments. This would cut right through the foam and make things flush. It also chopped it up into a million tiny pieces that got everywhere. If you were in the bus during this, you would think it was a winter blizzard. Snow was flying every which way, it was almost magical if it didn’t keep getting in our eyes and sticking to our sweat.
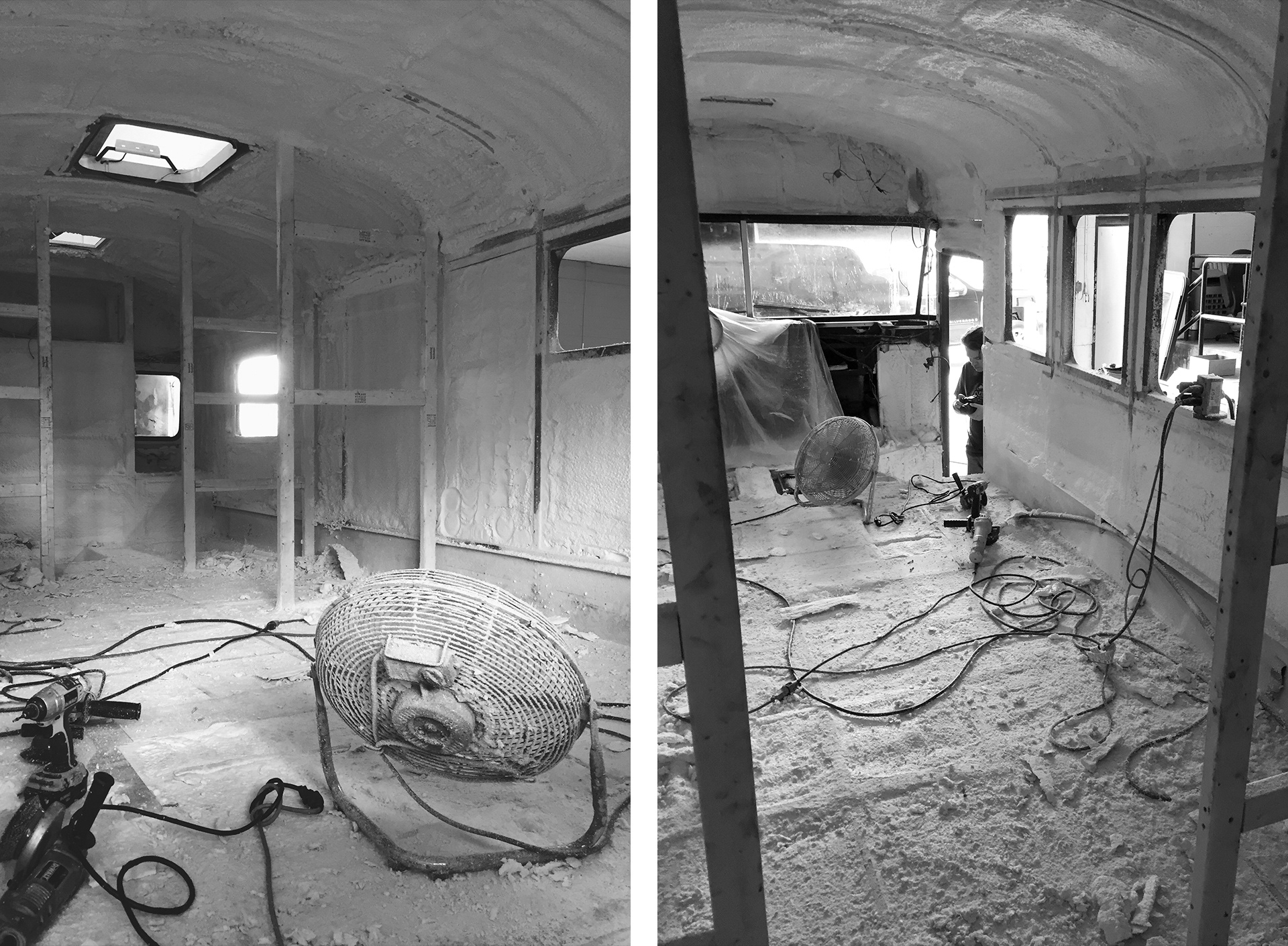
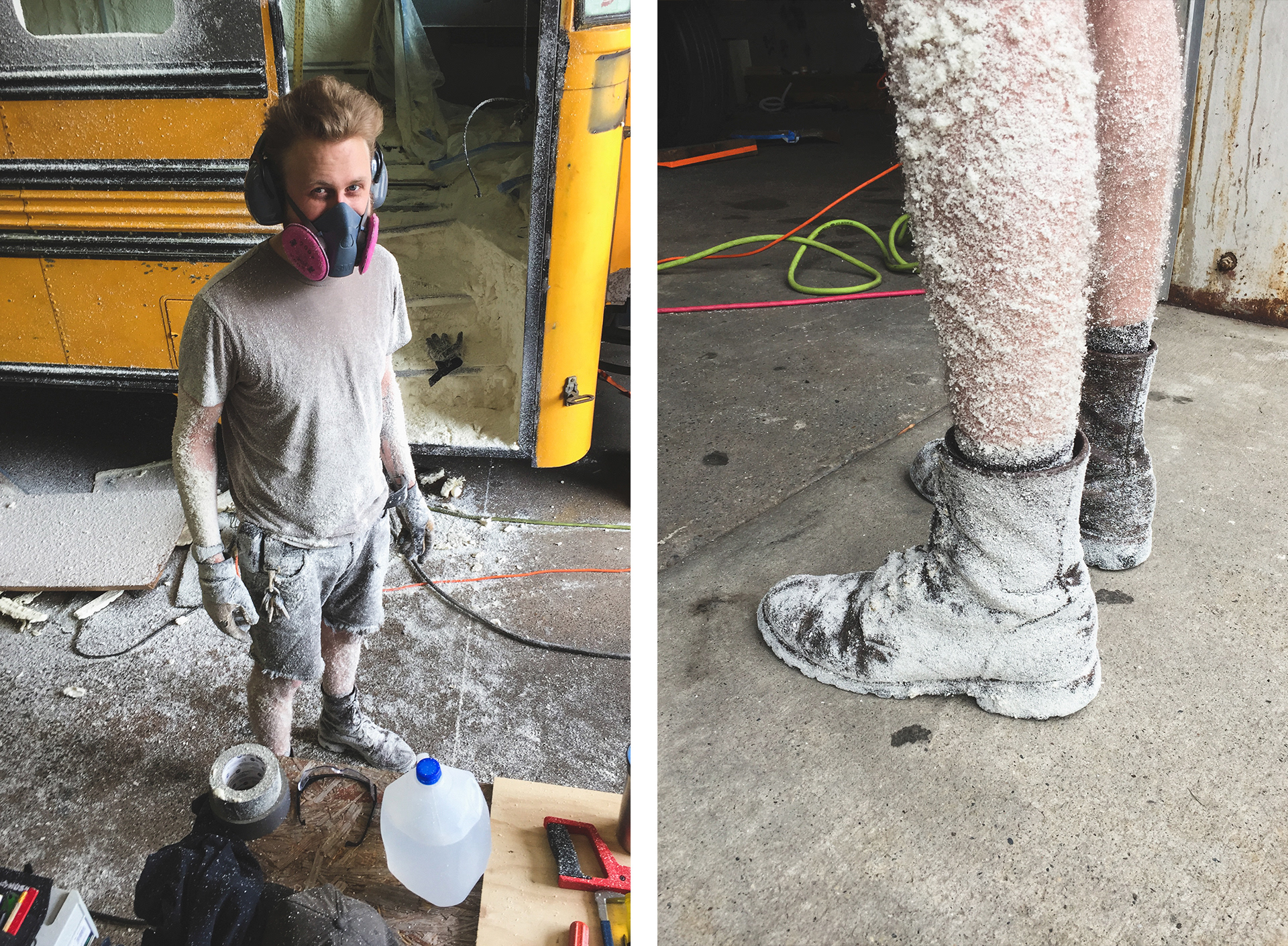
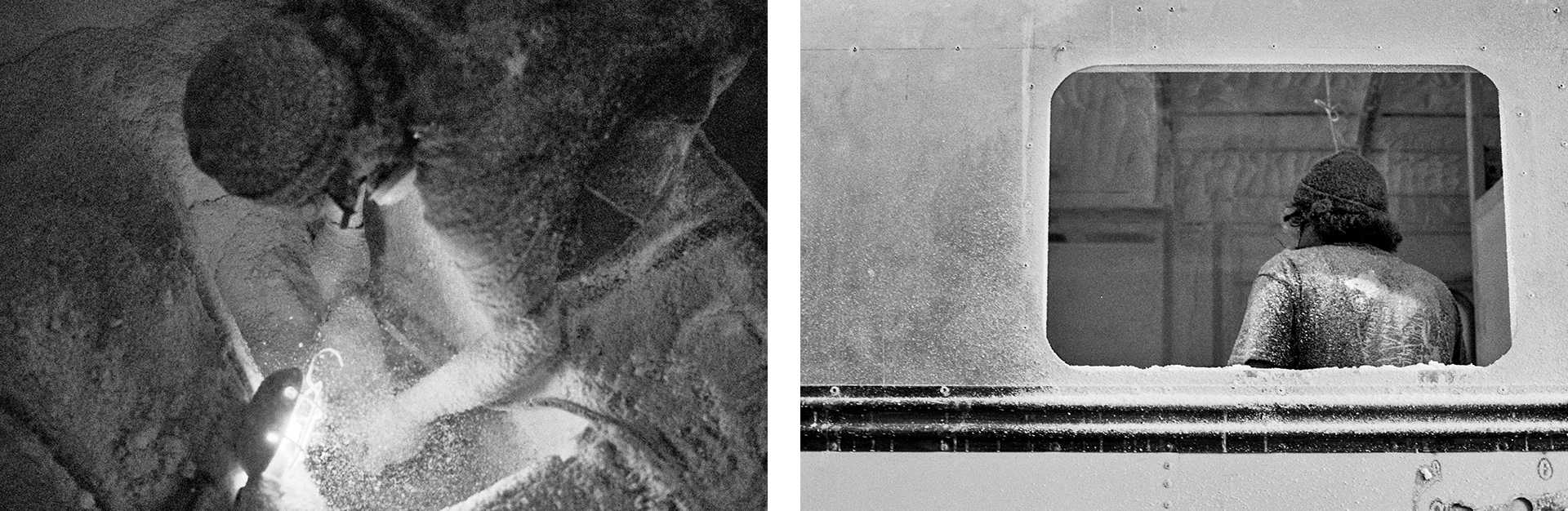
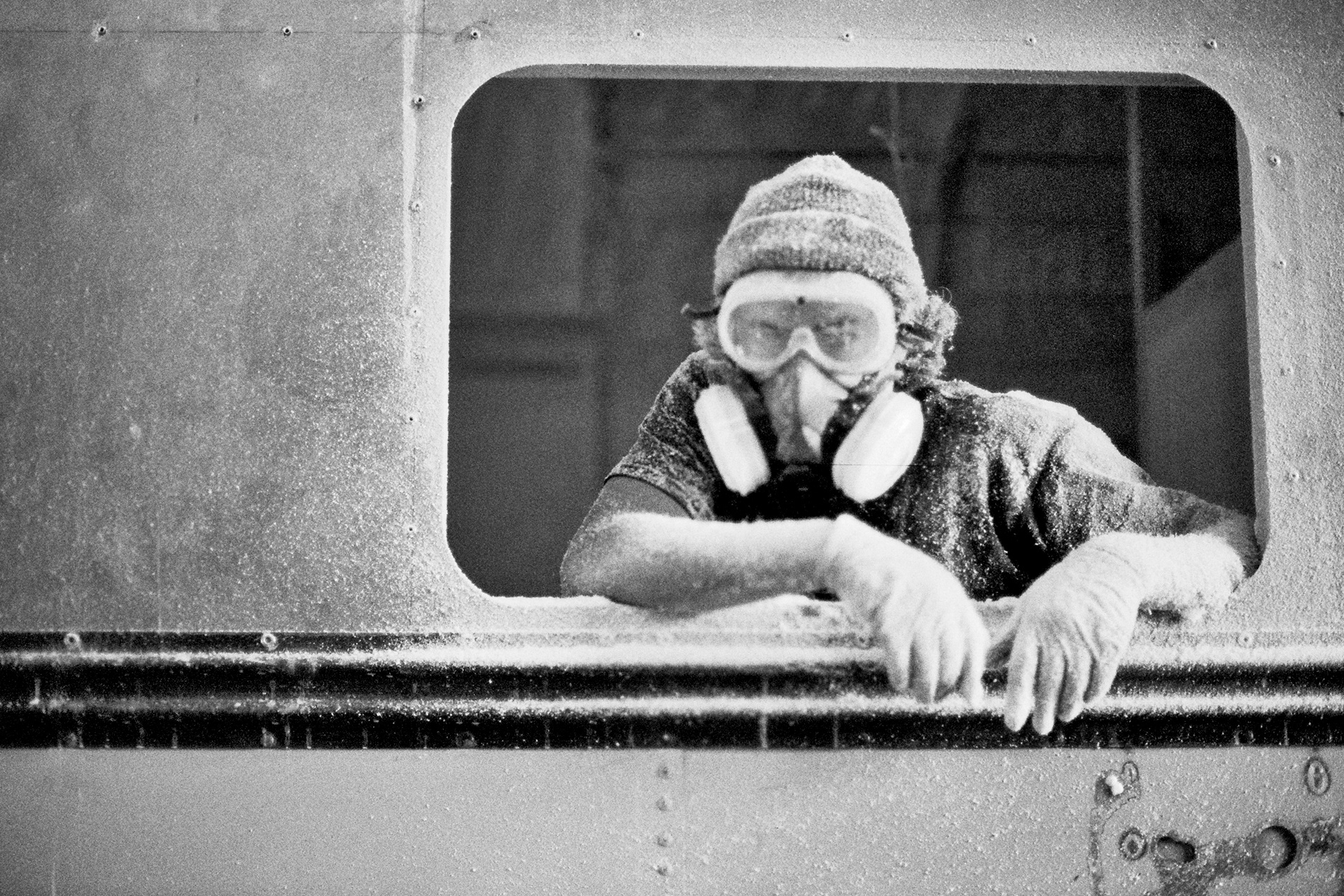
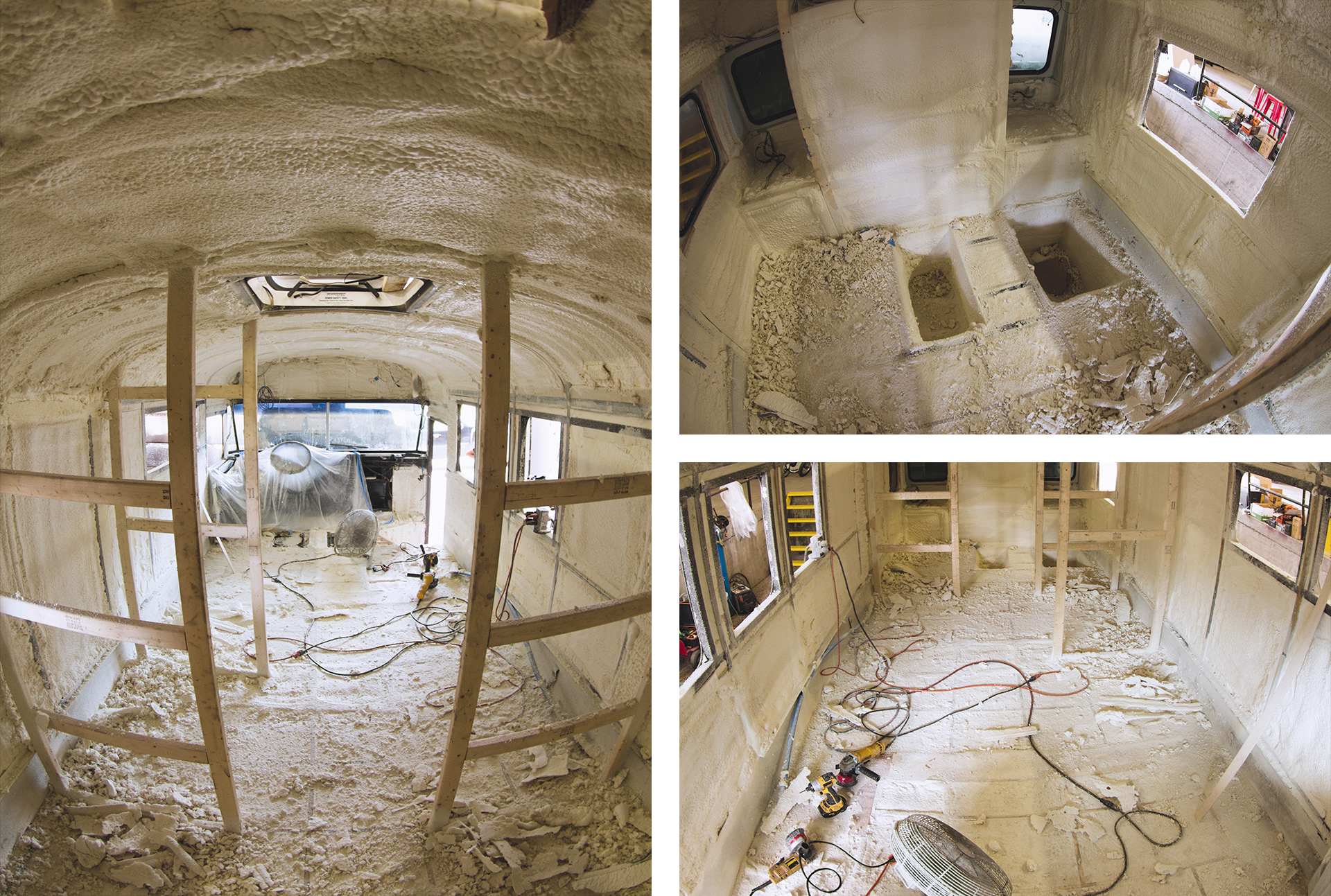
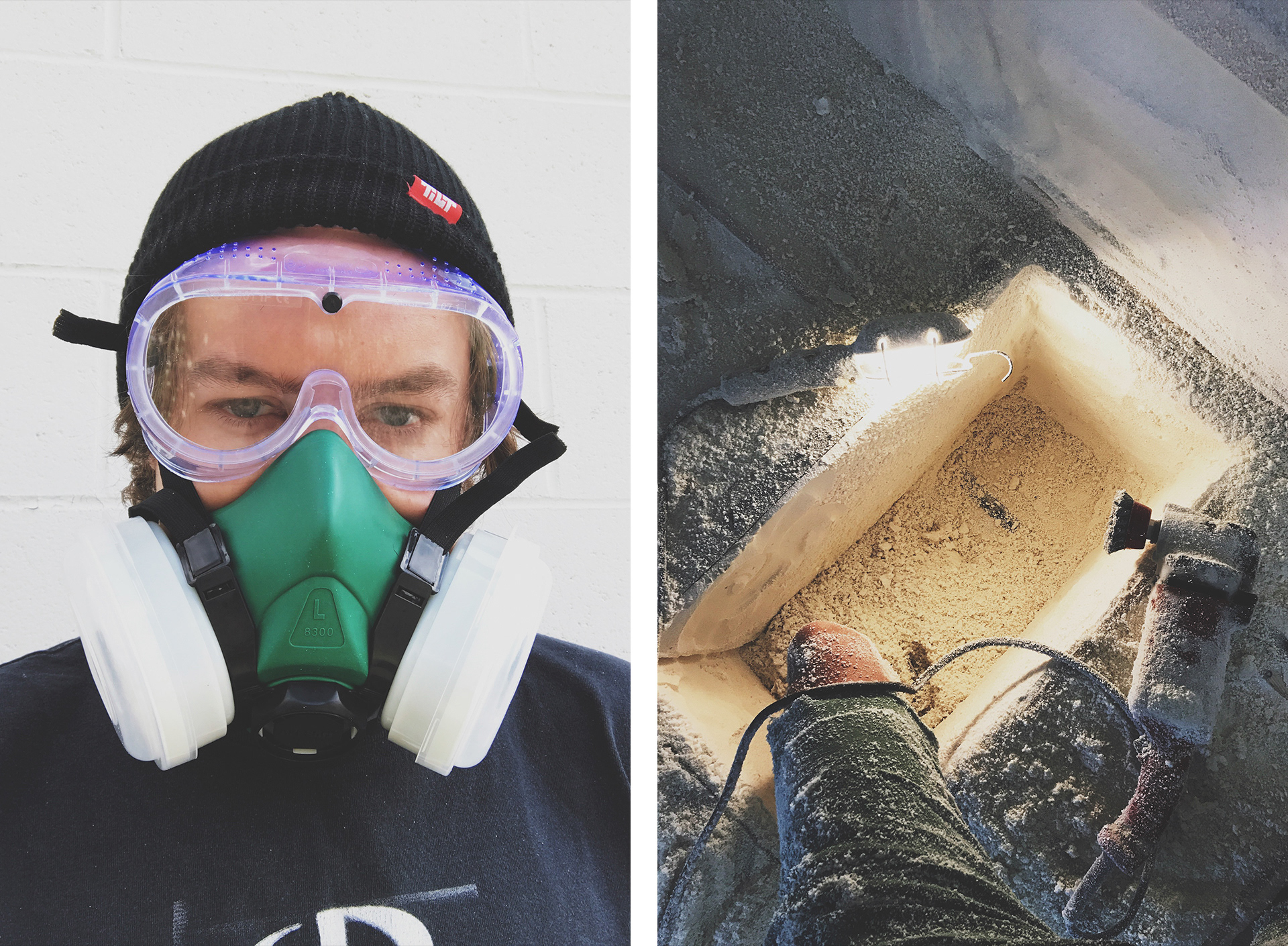
Every time we wanted to go to the bathroom or get thirsty or not wear sweaty goggles and mask, we had to go outside with the air compressor and blow away all the insulation off of us. It took maybe 5 minutes to get semi-clean but man did it feel great to be “clean”. Once we were done with our break, it was back into the bus to get dirty again.
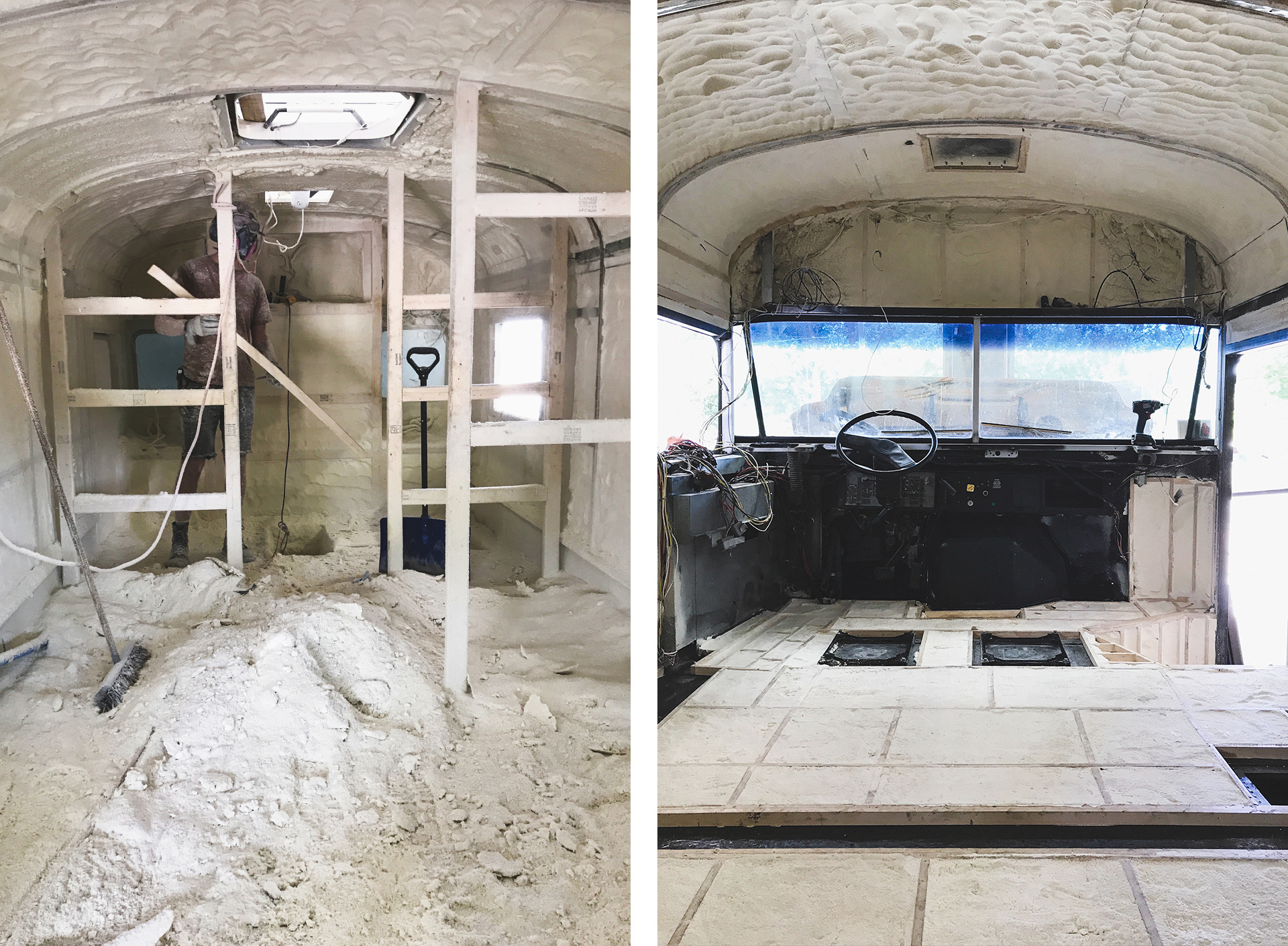
We had no idea how gnarly the insulation was going to be so it set us back a couple of days. We filled up three to five giant bags of insulation that we shaved off the walls and floor. On top of that, we needed to vacuum up the rest that was all over the floor outside of the bus to prep for painting. Somehow we lost the filter to the shop vac so we used a glove to keep things moving.
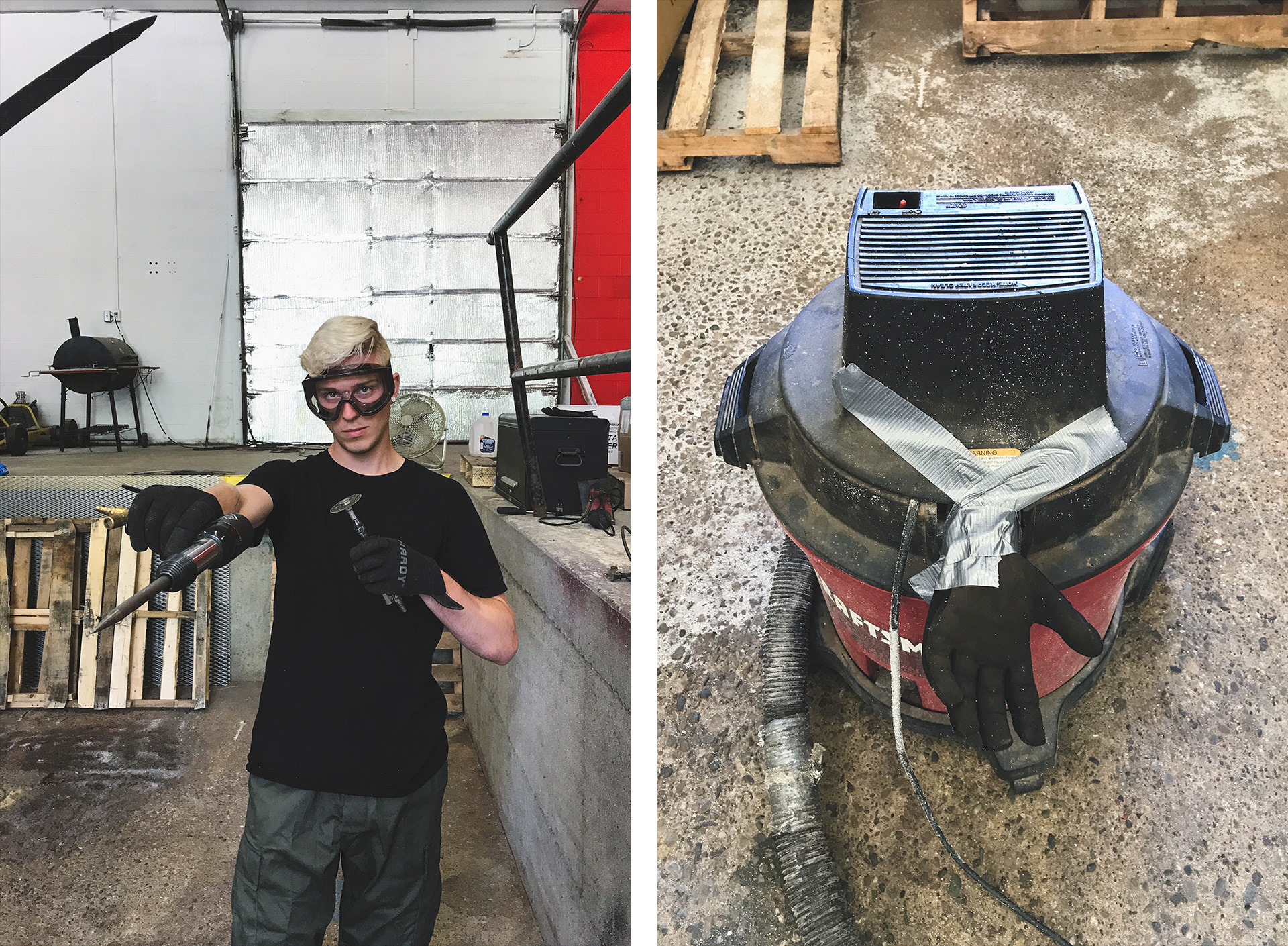
Things started moving really fast. Sub-floor was installed. The bench was constructed and ready for paint and cushions. The color of the bus was starting to change from yellow to grey. Originally we were going to prime with a spray gun but that was going to add a whole day to our timeline so we rattle can primed the bus. We underestimated how many cans this would take so we ran to home-depot four different times in one day. The total count was somewhere around thirty-six cans of primer.
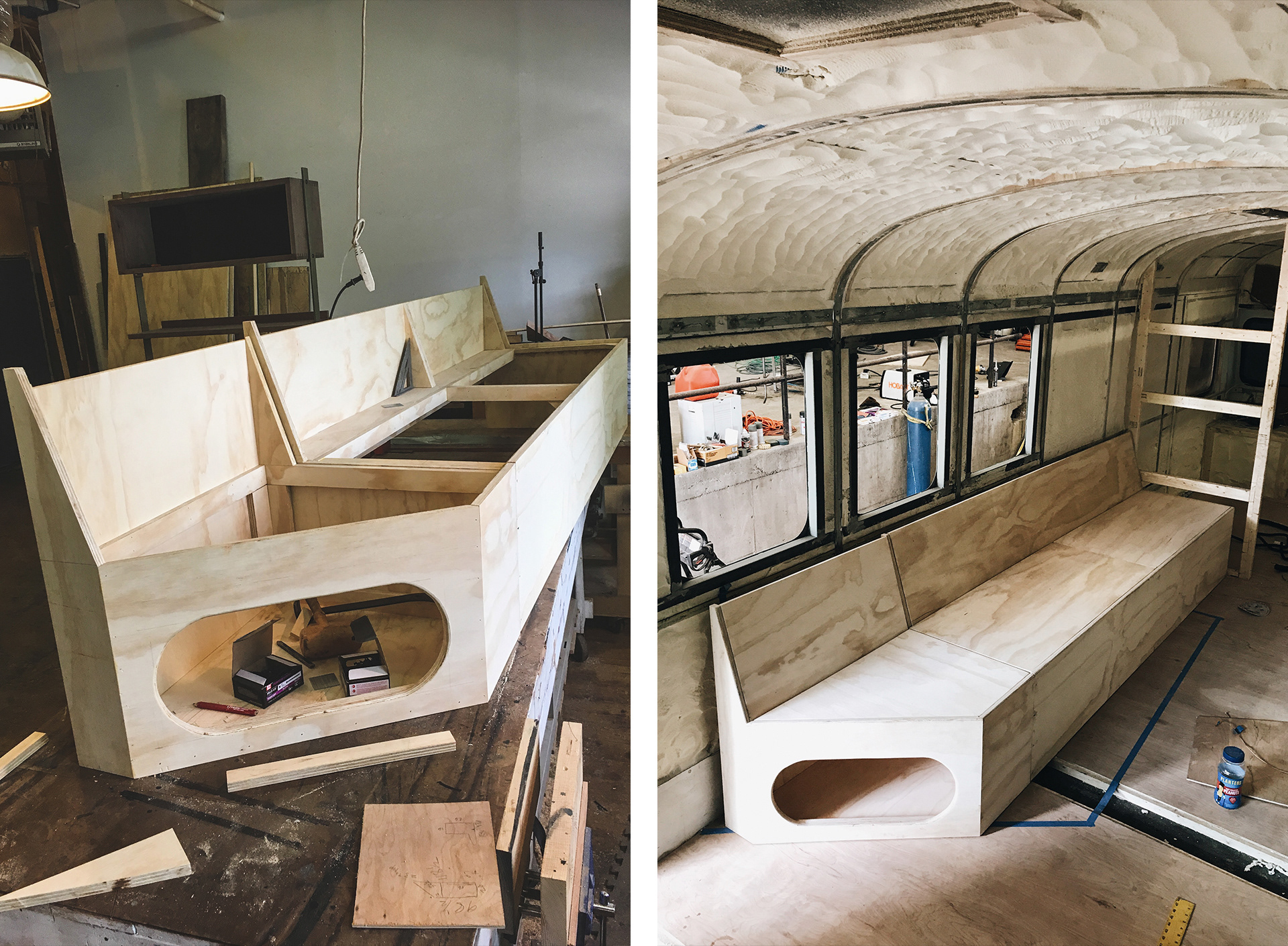
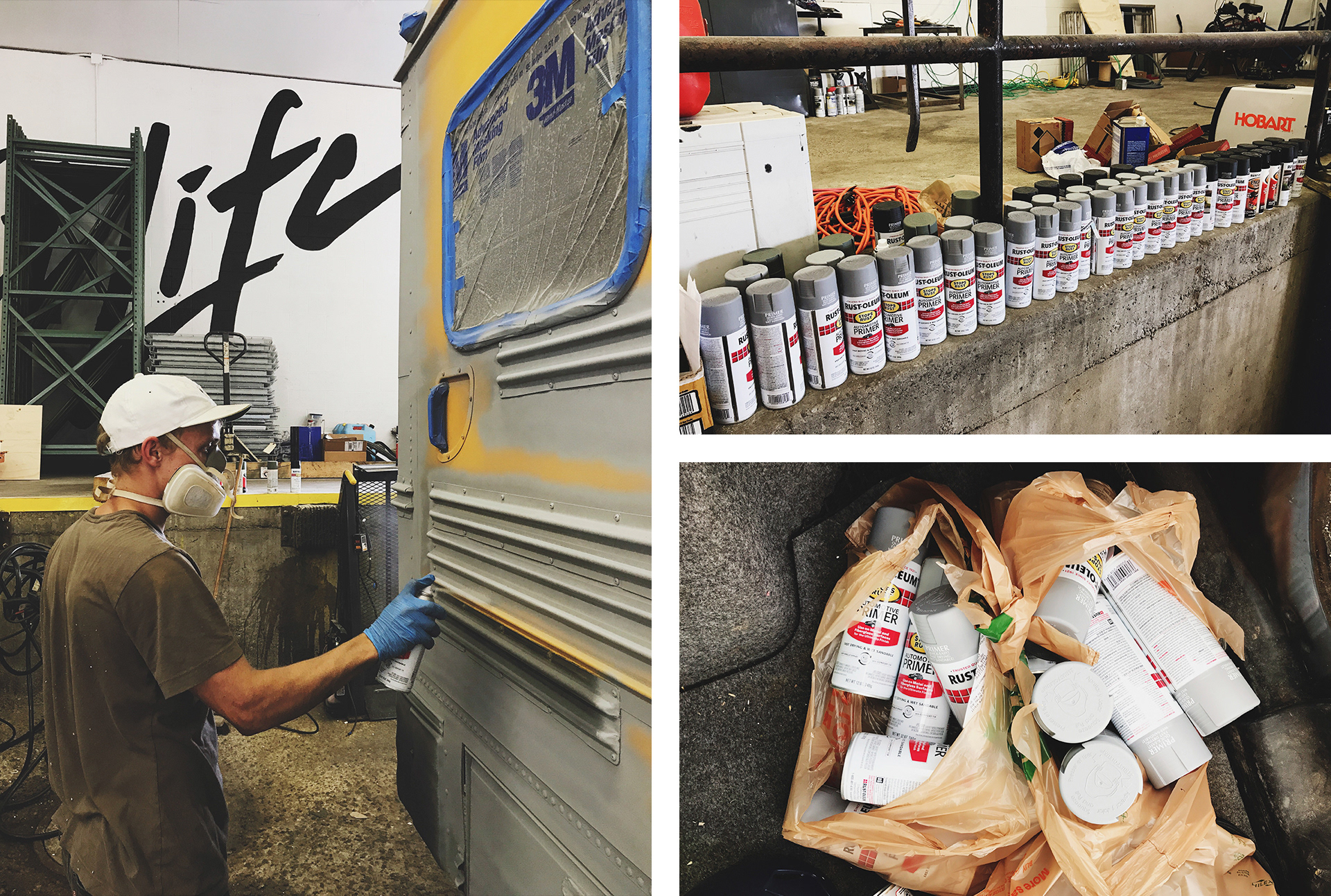
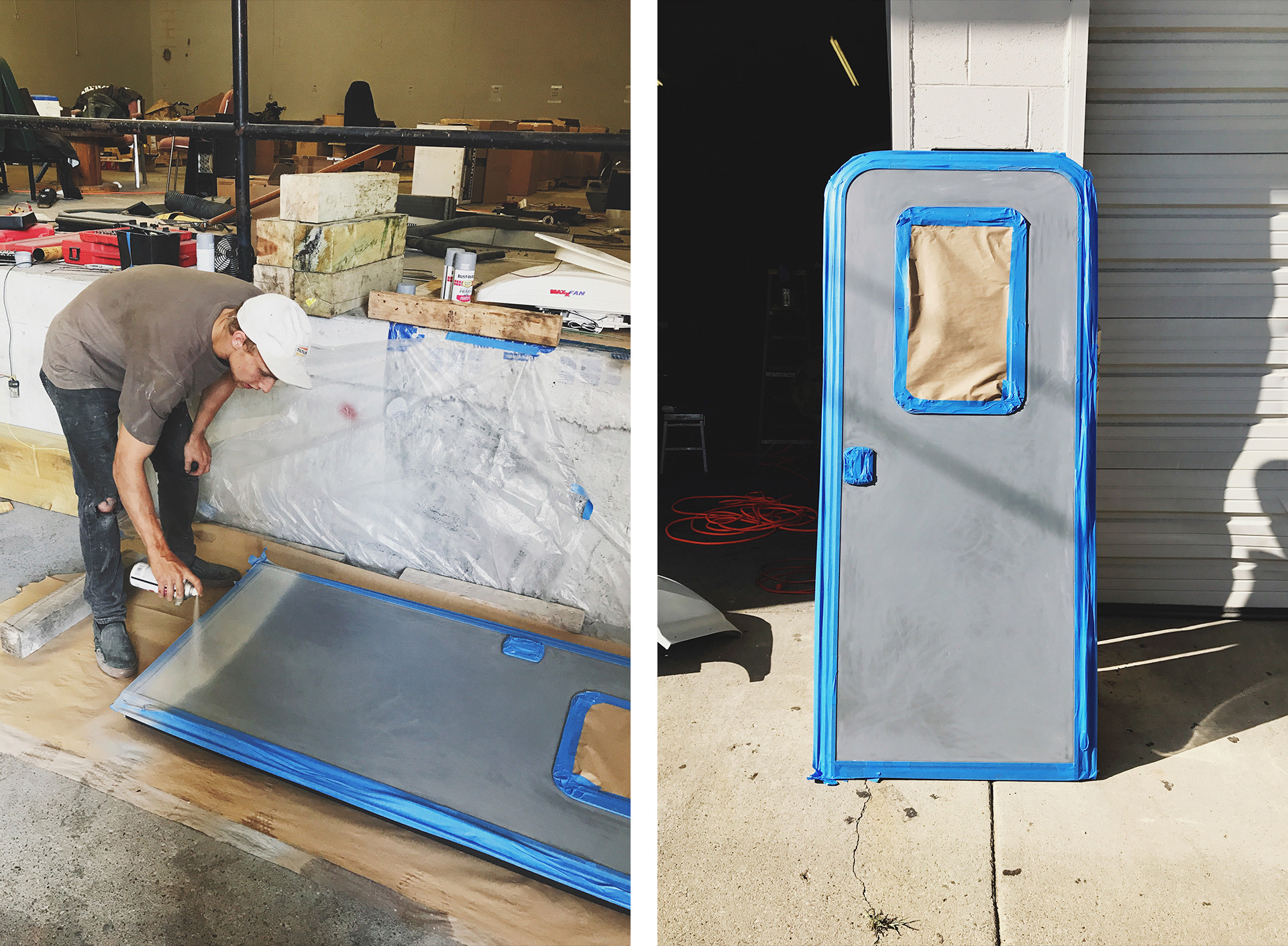
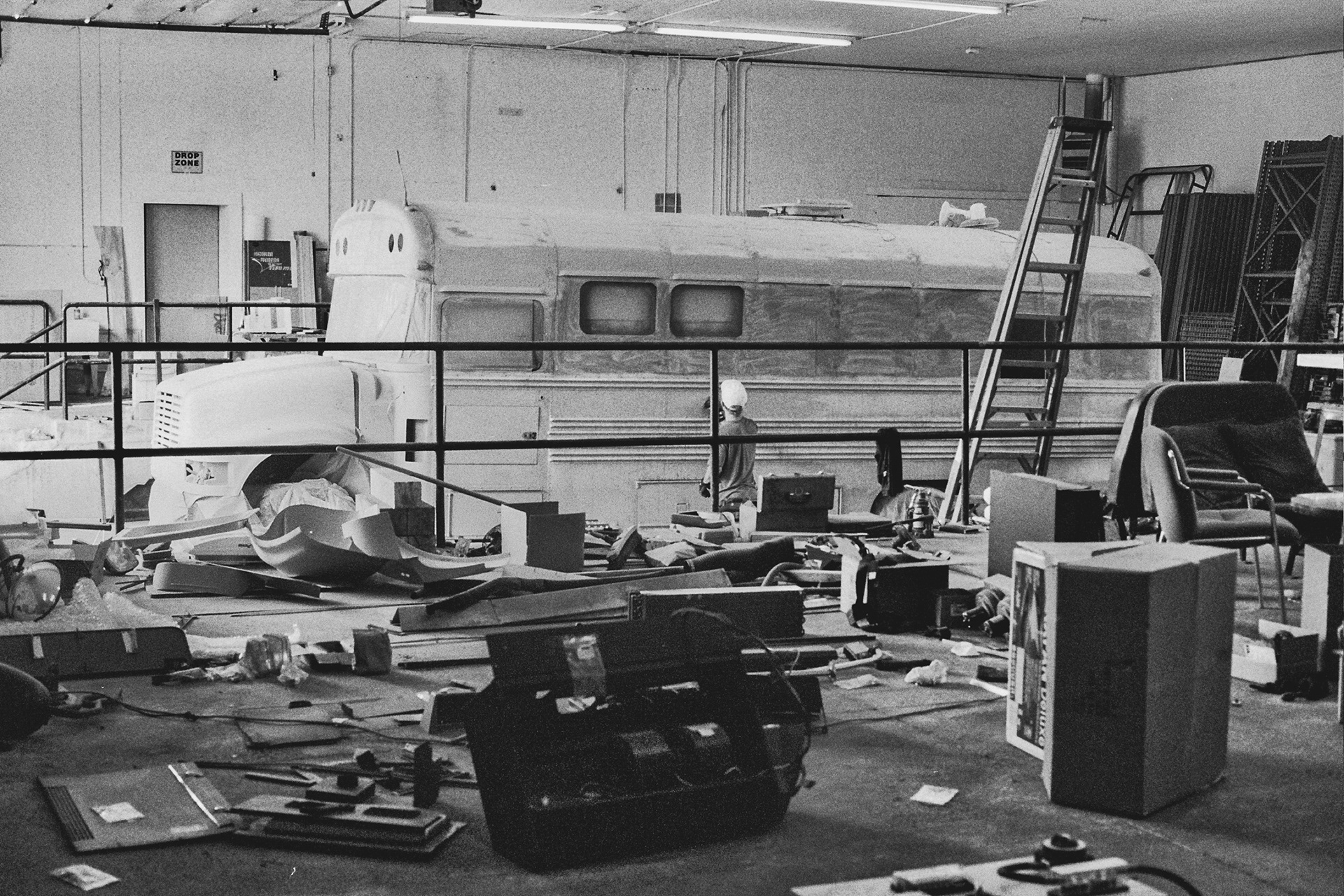
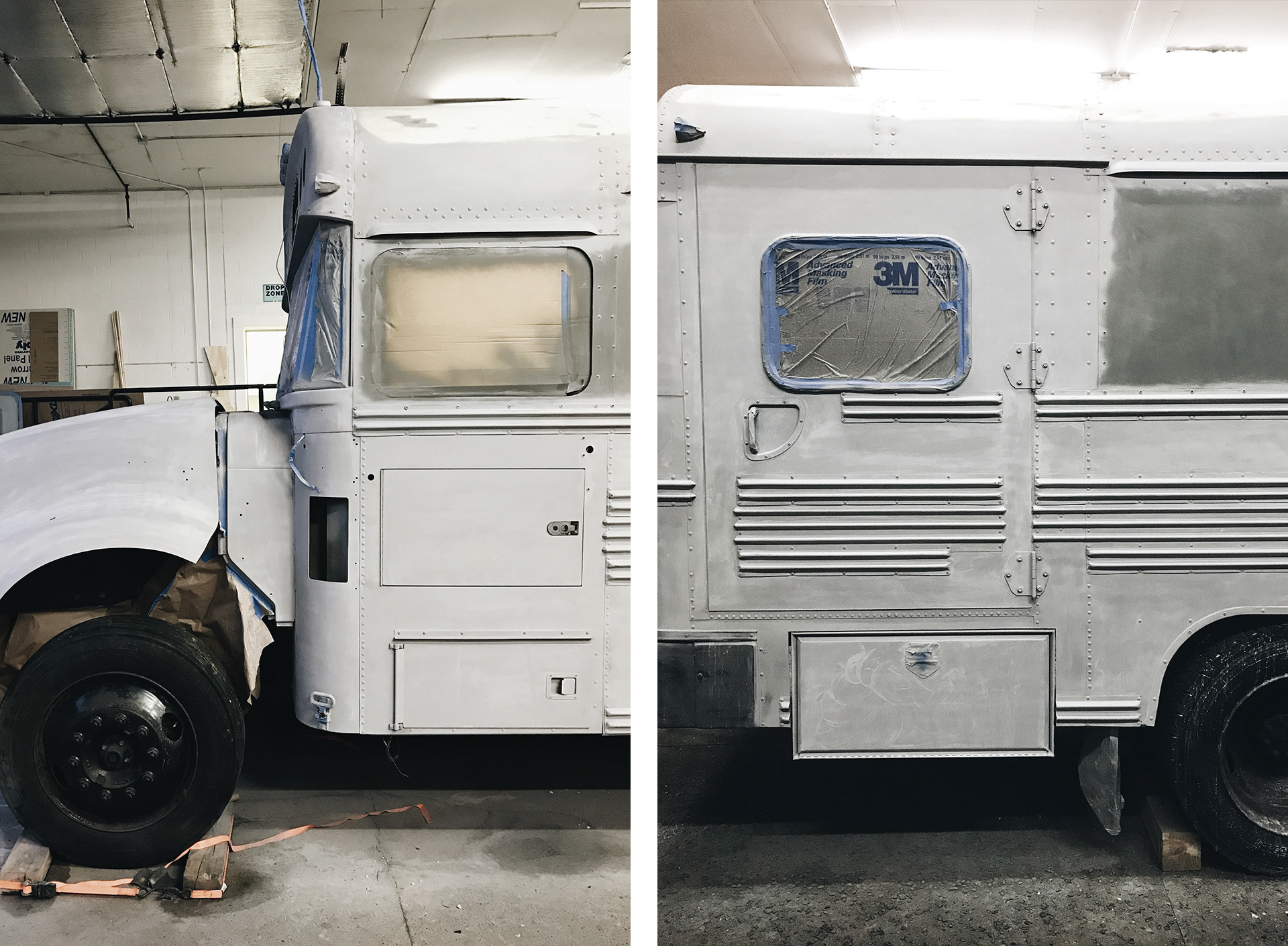
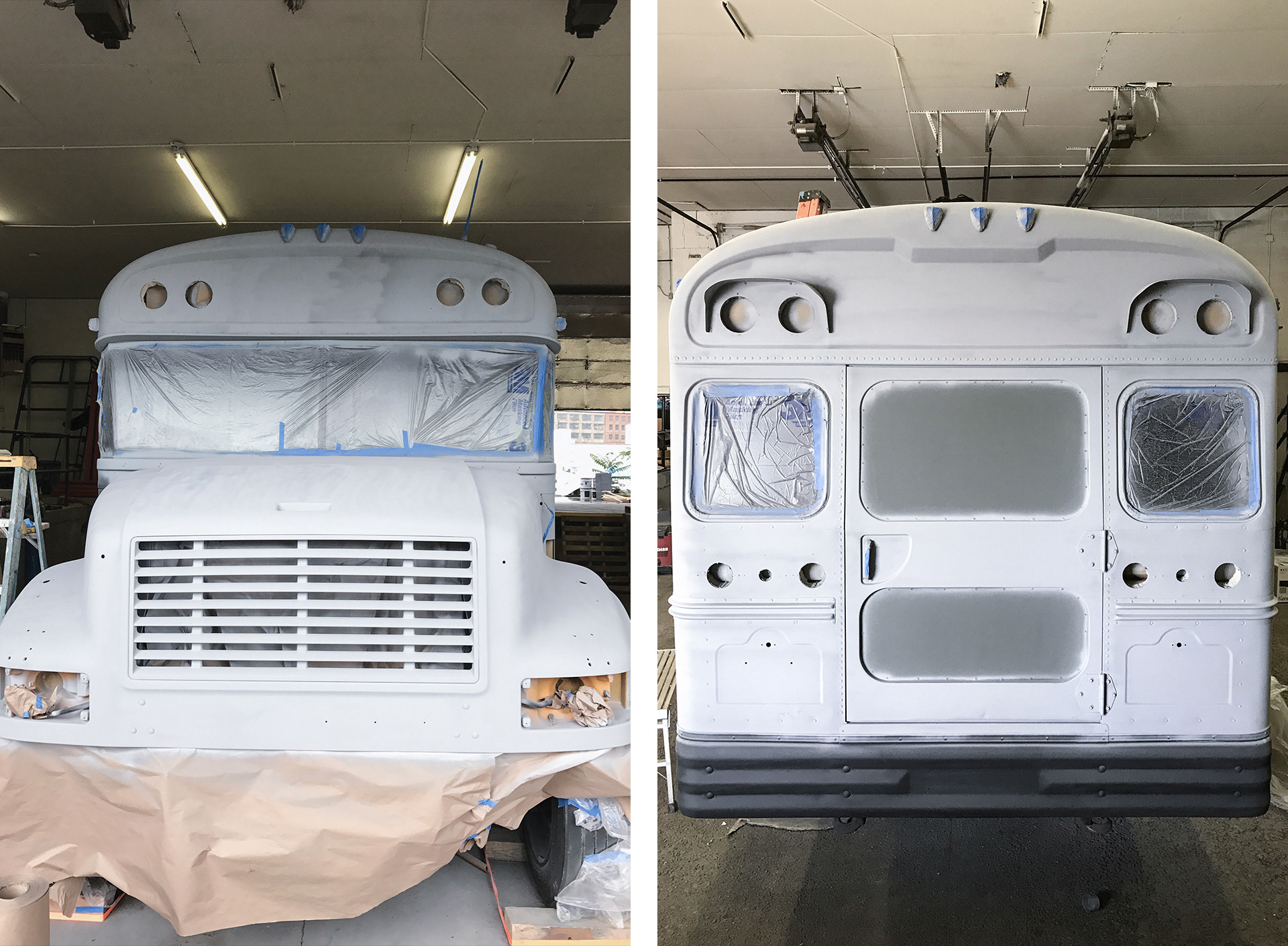
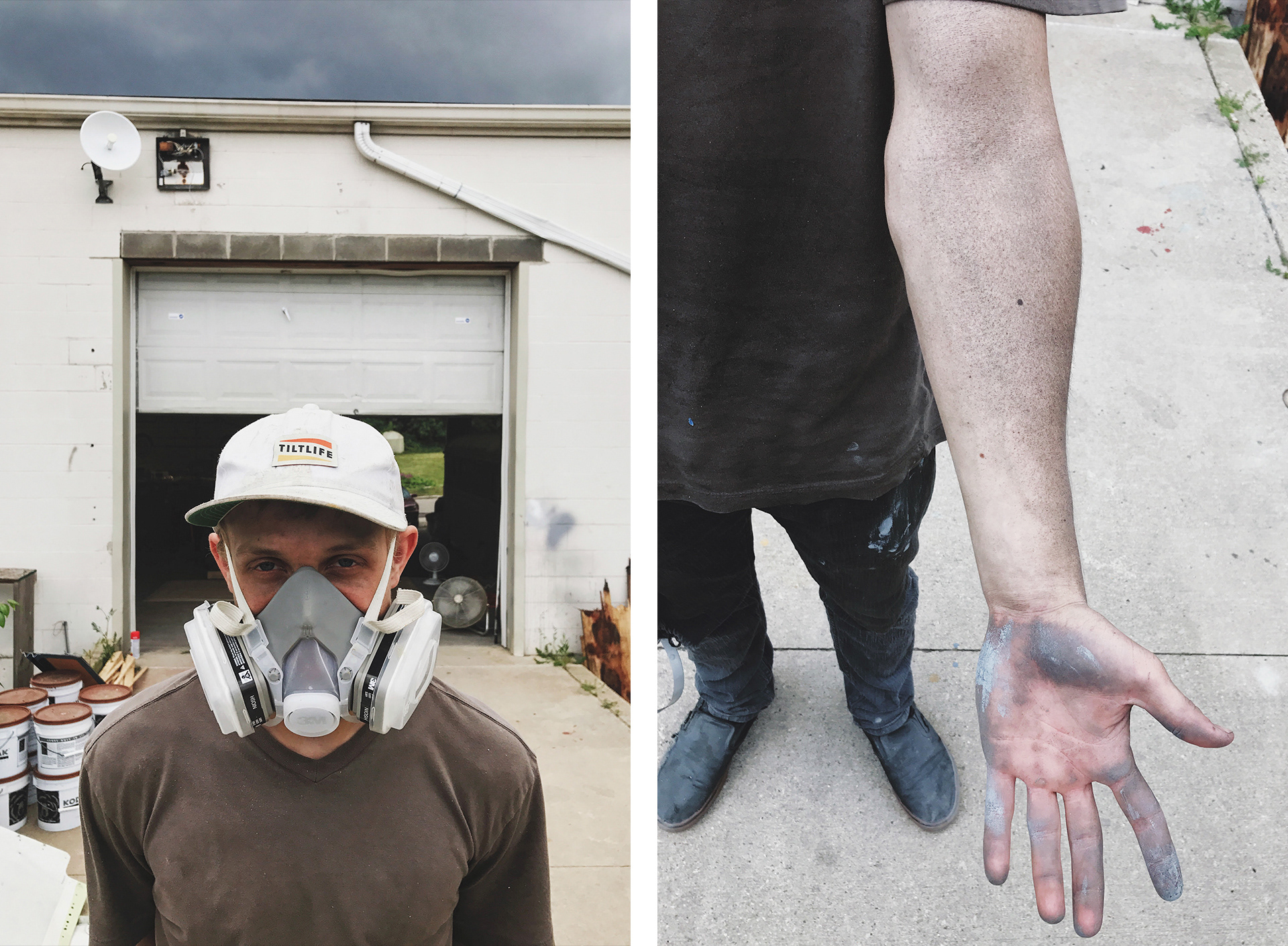
Joe was originally a painter before he got hired on at TILT so we had him pretty much prime the whole bus. It took all day because we kept running out of primer. By the end of the day, he was high from the fumes and couldn’t feel his spray finger. It might as well of been missing, that’s how numb it was. The outcome was a pretty well balanced base that we ended up wet sanding multiple times.
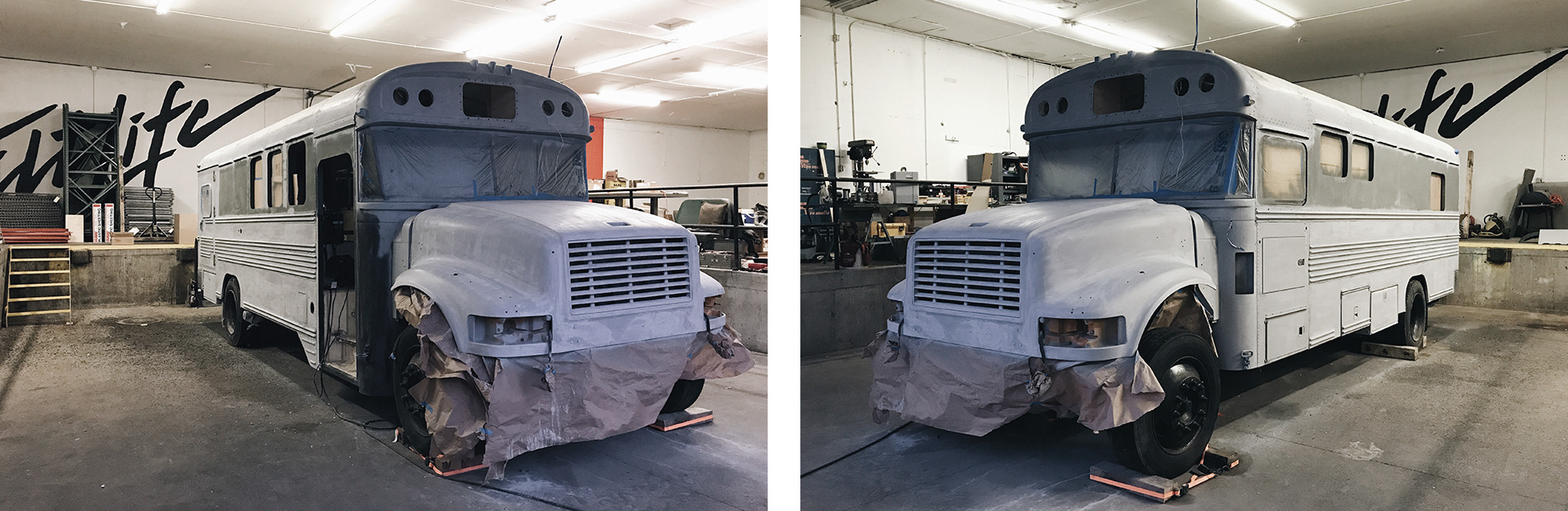
Last year we took a van with no AC up to Toronto and there was no way we were going to do that again. We bought two window AC units that would fit in the bus but we needed to make vents for it to breathe. Holes were cut out of the rear and front tops of the bus. Fancy vent covers were put on and boxes were made to house the AC units. We turned one unit on while we were working on the bus and it felt amazing. That was the only time AC was on in the bus. The boxes were too tight and would suffocate the units and force them to over heat so they never made it on the bus. The bus later cruised through 106 degrees Fahrenheit. For some reason, TILT keeps going on trips where the heat waves are hitting. Last year was the midwest, This year, the west coast.
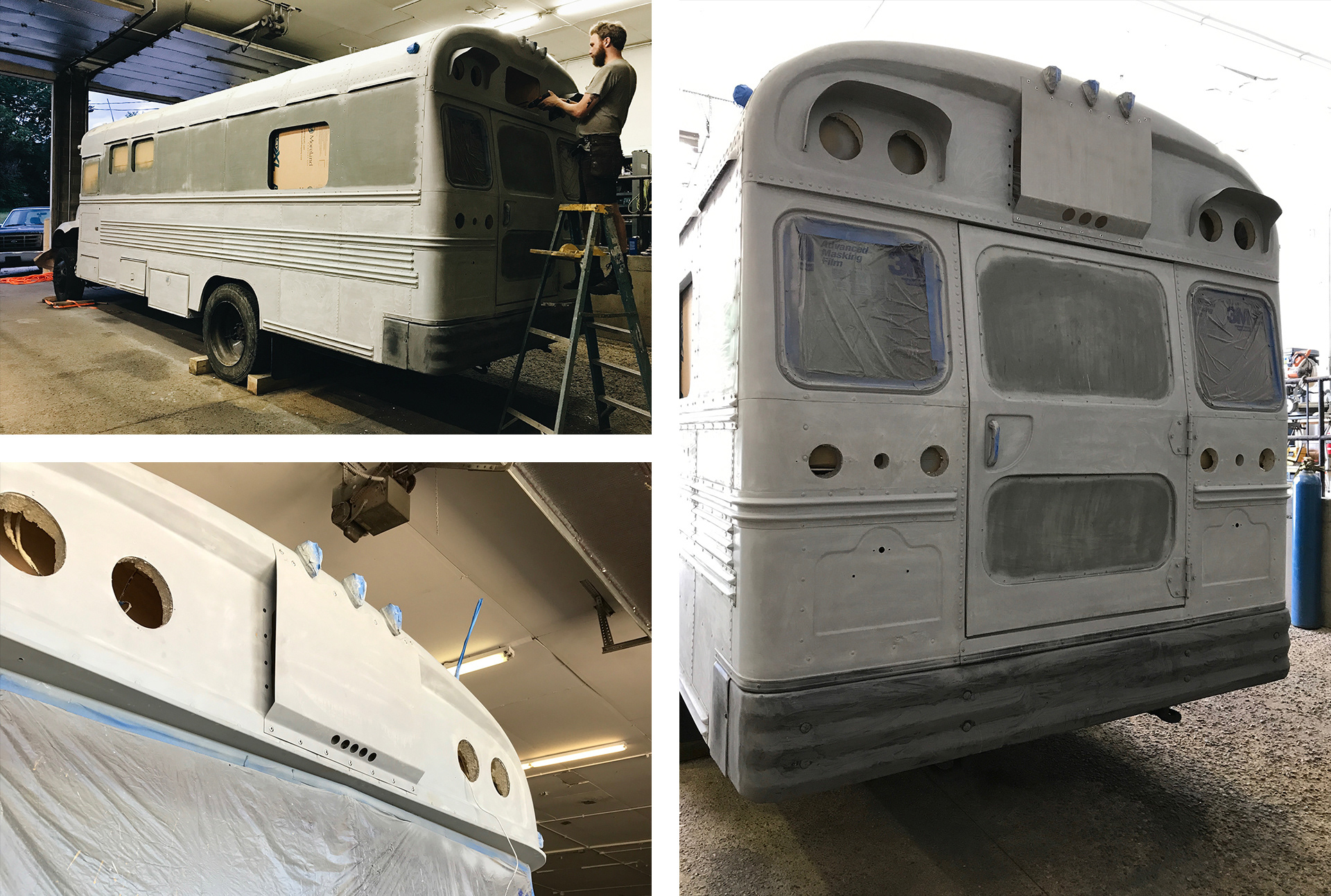
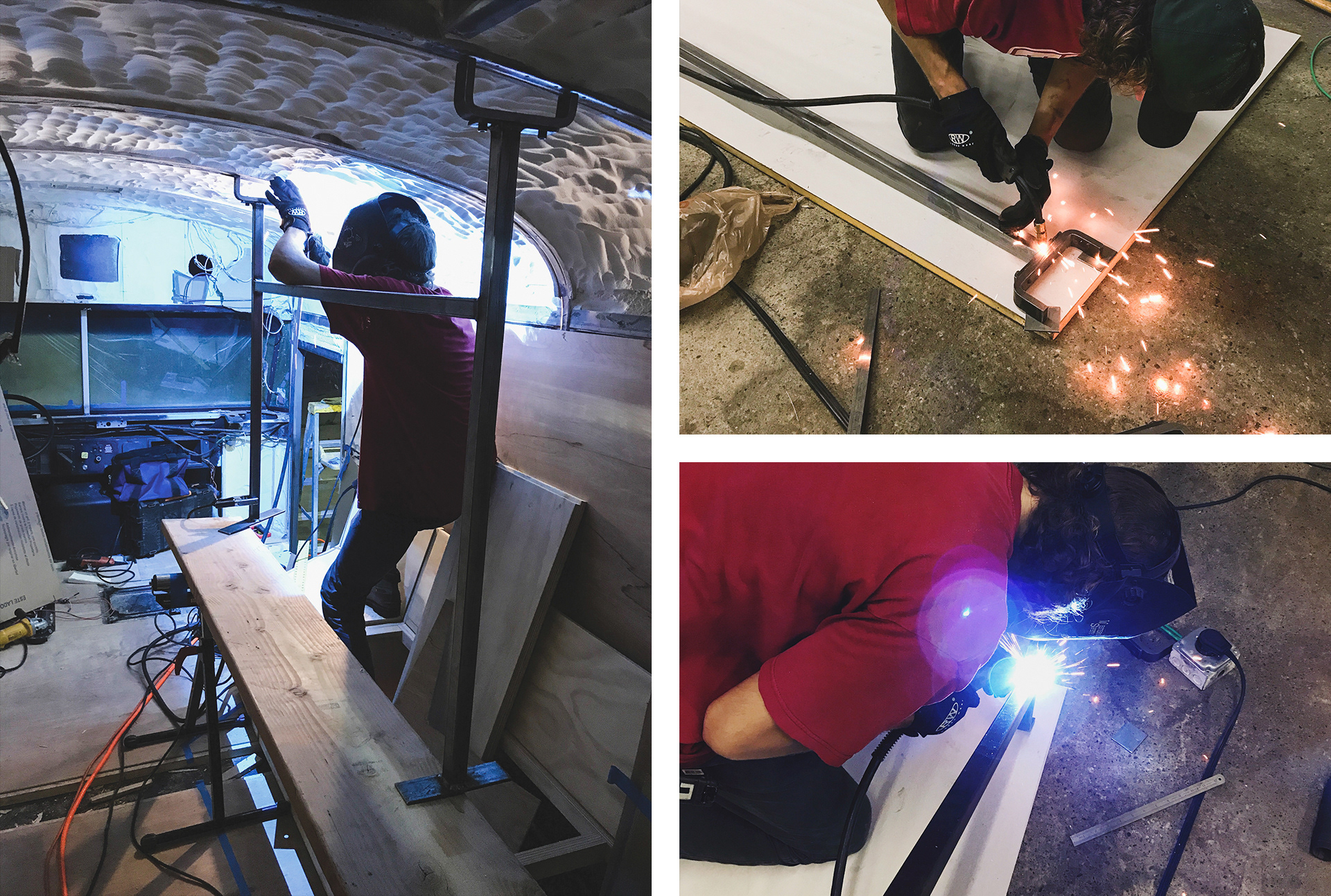
After a long day of work, Collin and Chris stayed at the warehouse till 1am to build the support for the table. We kept thinking of the right way to do this and Collin’s final answer was to hang it from the ceiling so there weren’t any leg supports to get in the way. We didn’t exactly think about how the bus vibrates when it is moving and will make the table shake but it looked cool and thats really all that matters. Since the bus wasn’t leveled, welding the support to the ceiling was a bit tricky but the end result was flush.
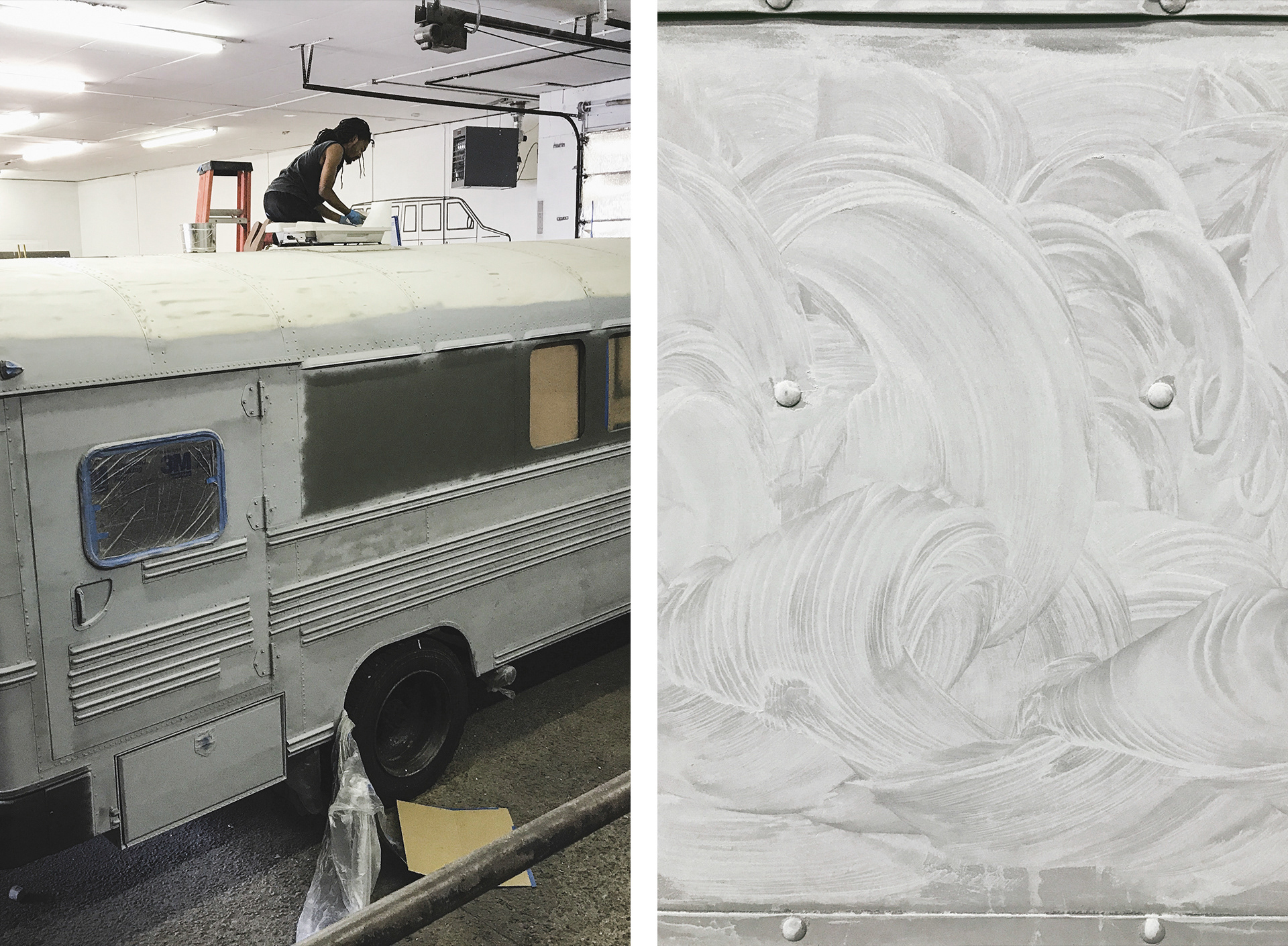
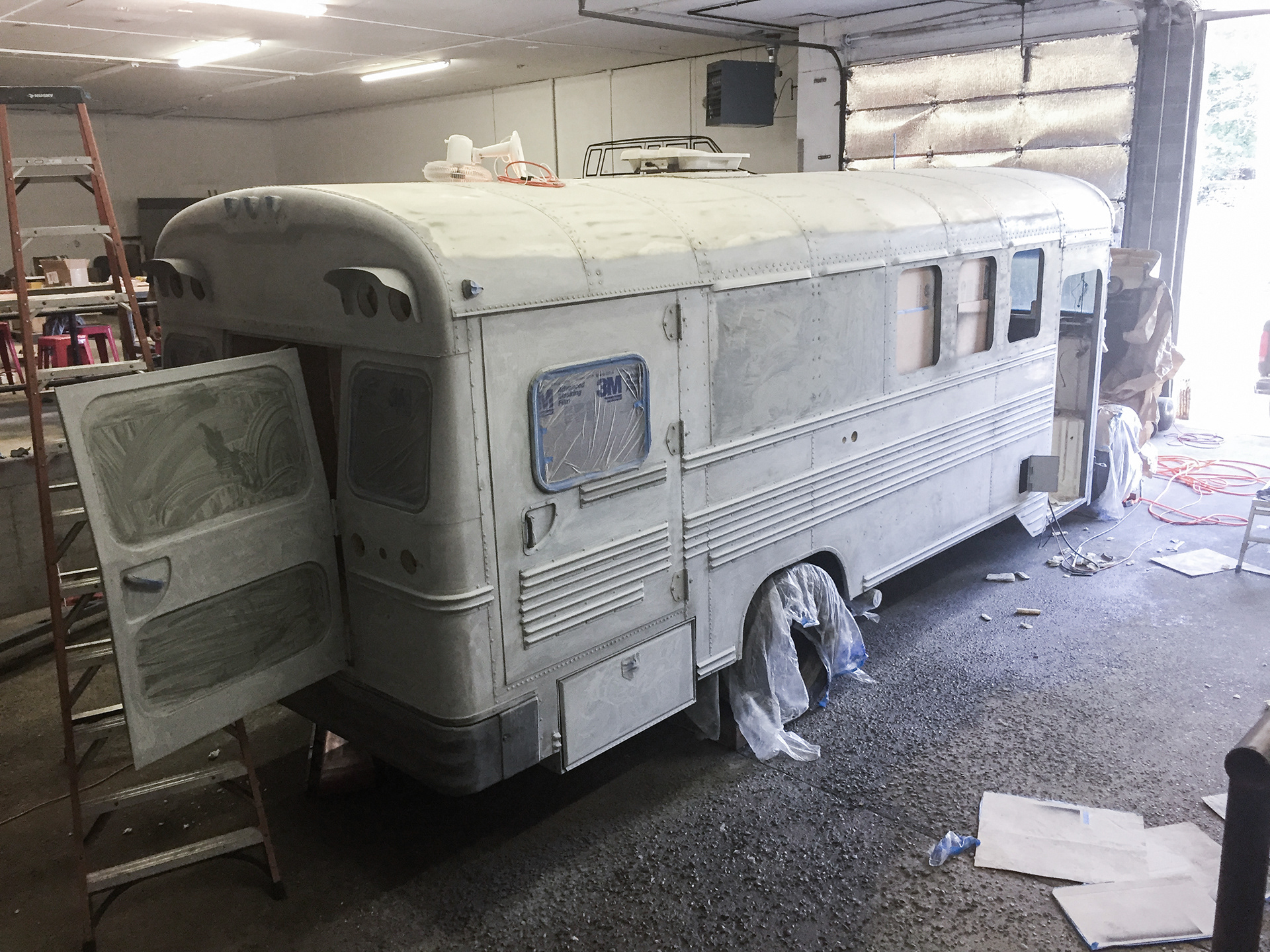
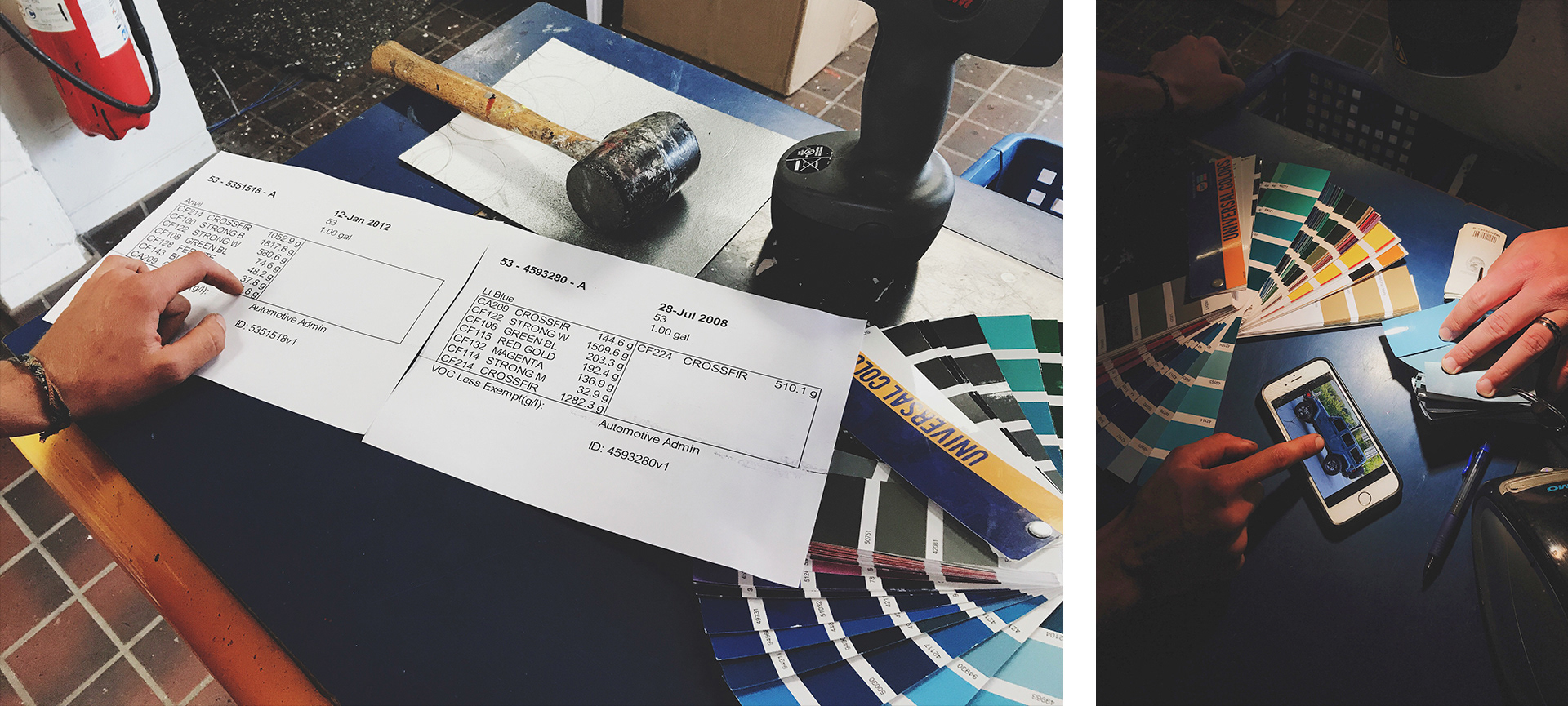
The color of the bus kept changing. It was originally suppose to be a blue-ish grey but army tan kept getting thrown into the mix. We purchased our paint at Napa. They had break downs of the paint and what goes into them so we kept narrowing down which colors. After about thirty minutes of holding up the line we finally went for it. The color had a little too much magenta in it once it dried but still looked great.
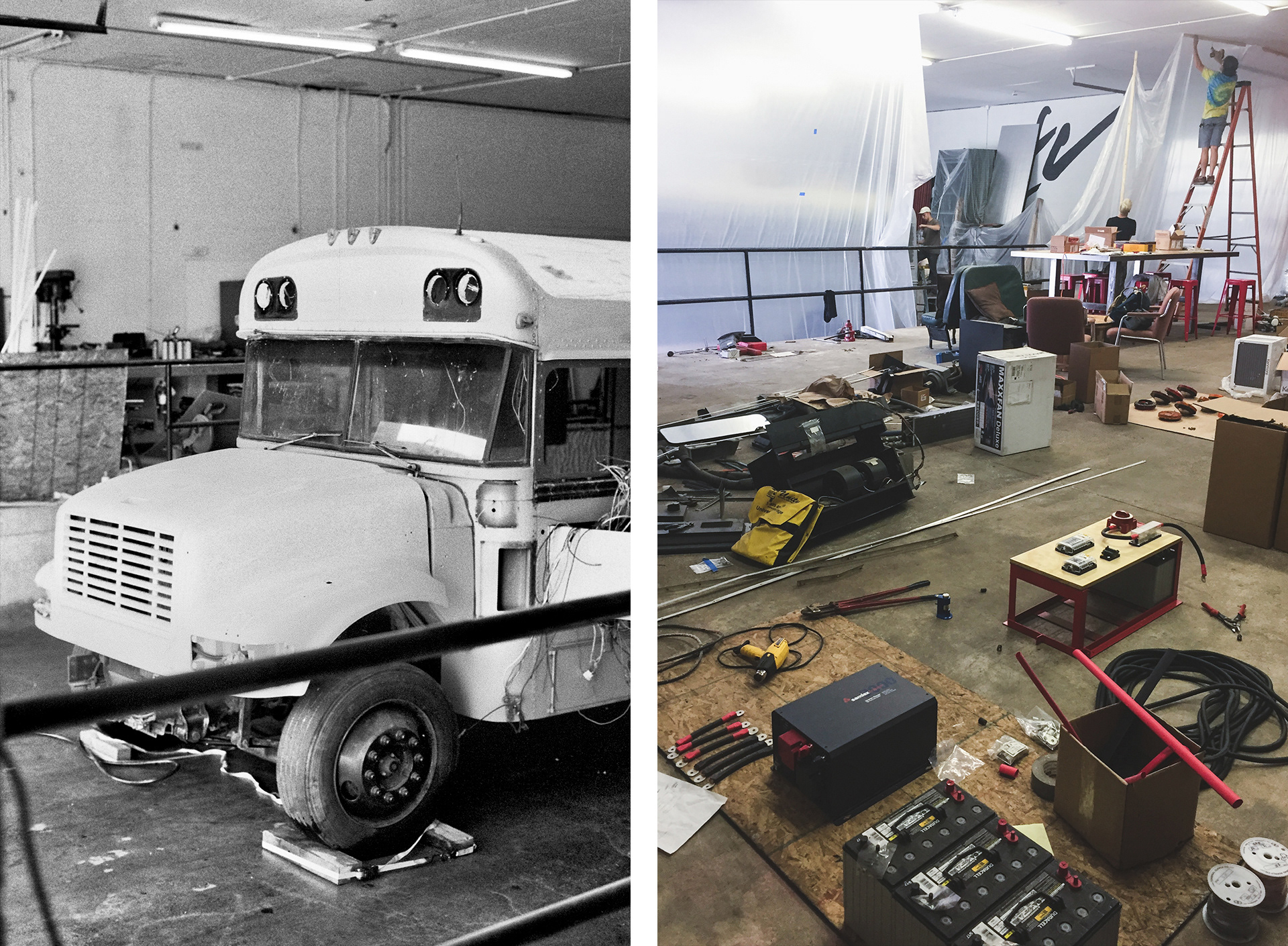
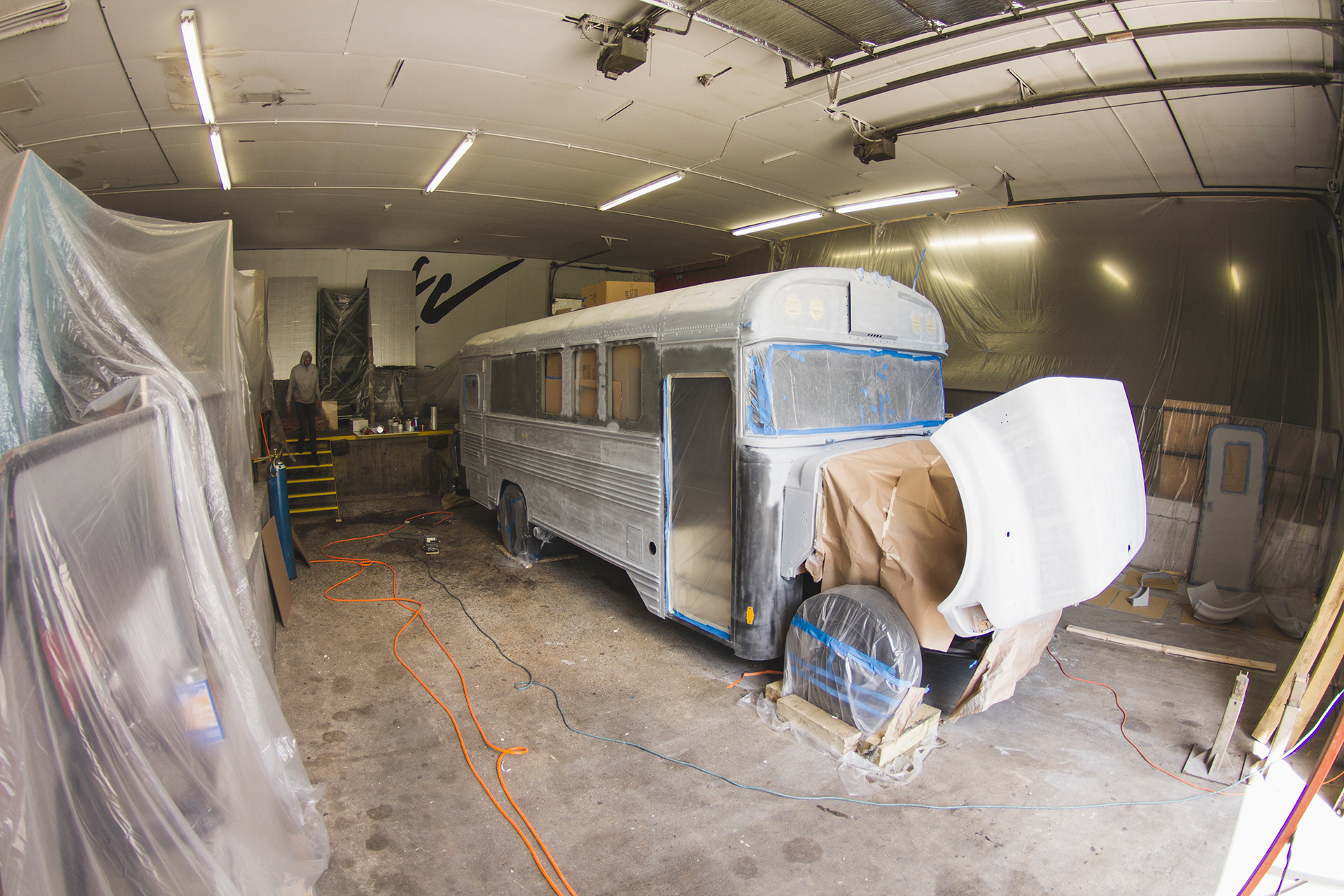
On Friday we didn’t get as much as we wanted to get done so we were forced to come in early Saturday to set up the spray booth. We got giant rolls of plastic sheeting from Sherwin Williams which was walking distance from the warehouse. Wrapped pieces of wood up in the plastic and then screwed them into the ceiling. As we were almost wrapping up, we ran out of hardener which thickens up the paint and allows for the paint to harden before it drips. No paint company is open past noon on Saturday so we were pretty much screwed until Collin remembered he had some hardener from when he painted his civic ten years ago. The hardener was the same formula, just ten years old which we weren’t really sure what that was going to mean. Turns out it wasn’t doing its job as well as it should and we ended up with some drip marks. One of these days we will buff them out. Painting the bus took awhile and we knew it would be an all day task but we still expected to get out by dinner. Ended up being 9pm till we got out of there, just in time for some Founders food and brew.
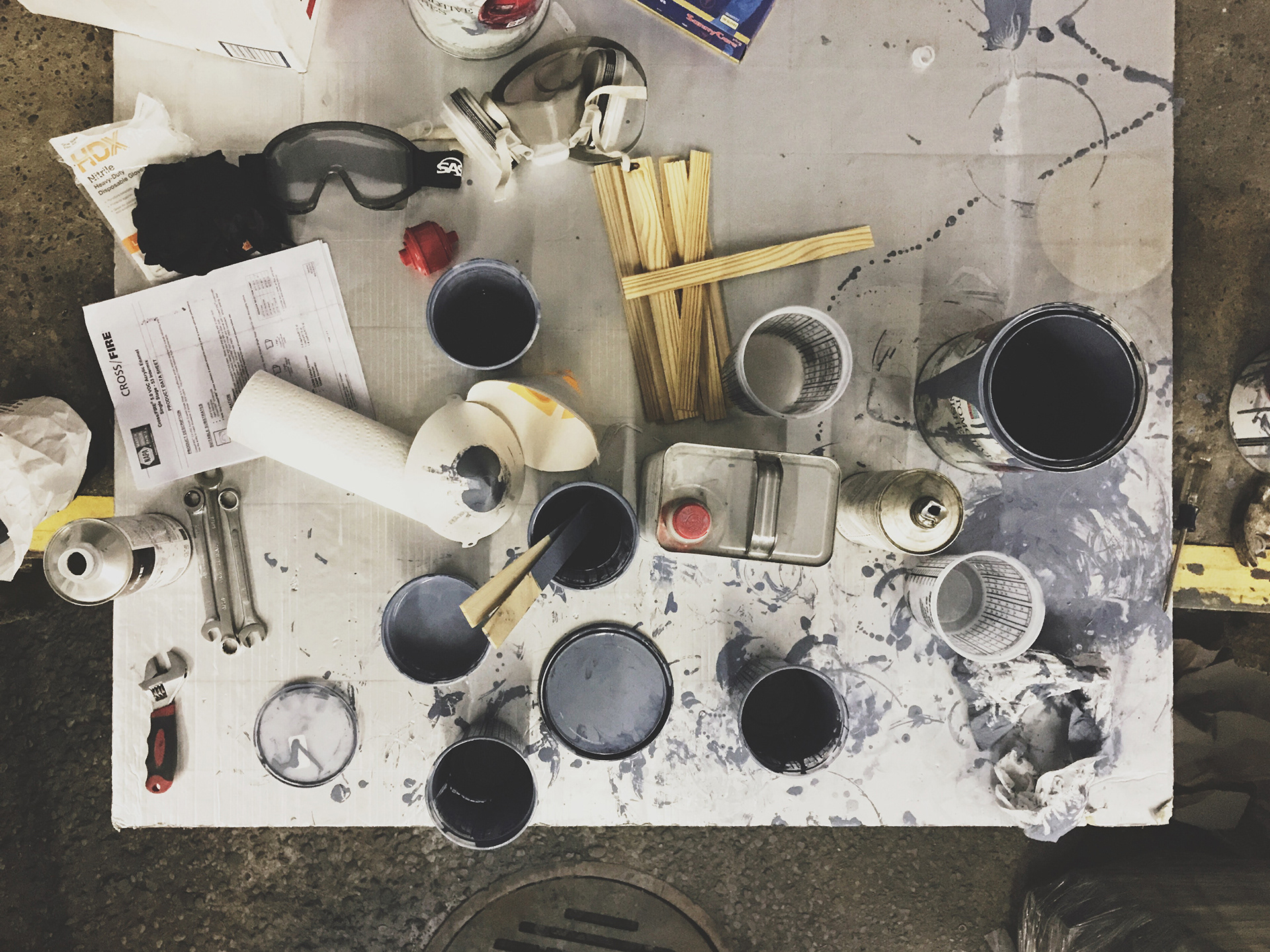
No one sprays a bus with automotive paint due to the size of the vehicle. Well, we did. Chris and I wore proper masks with separate particle and organic vapor filters. I had a small leak in mine. When we took a break in-between coats I couldn't help but comment on how loud the birds were chirping. I realized I was lit on the fumes and couldn't stop laughing. With the mask fixed, we went back in for the second coat. – Collin Snoek
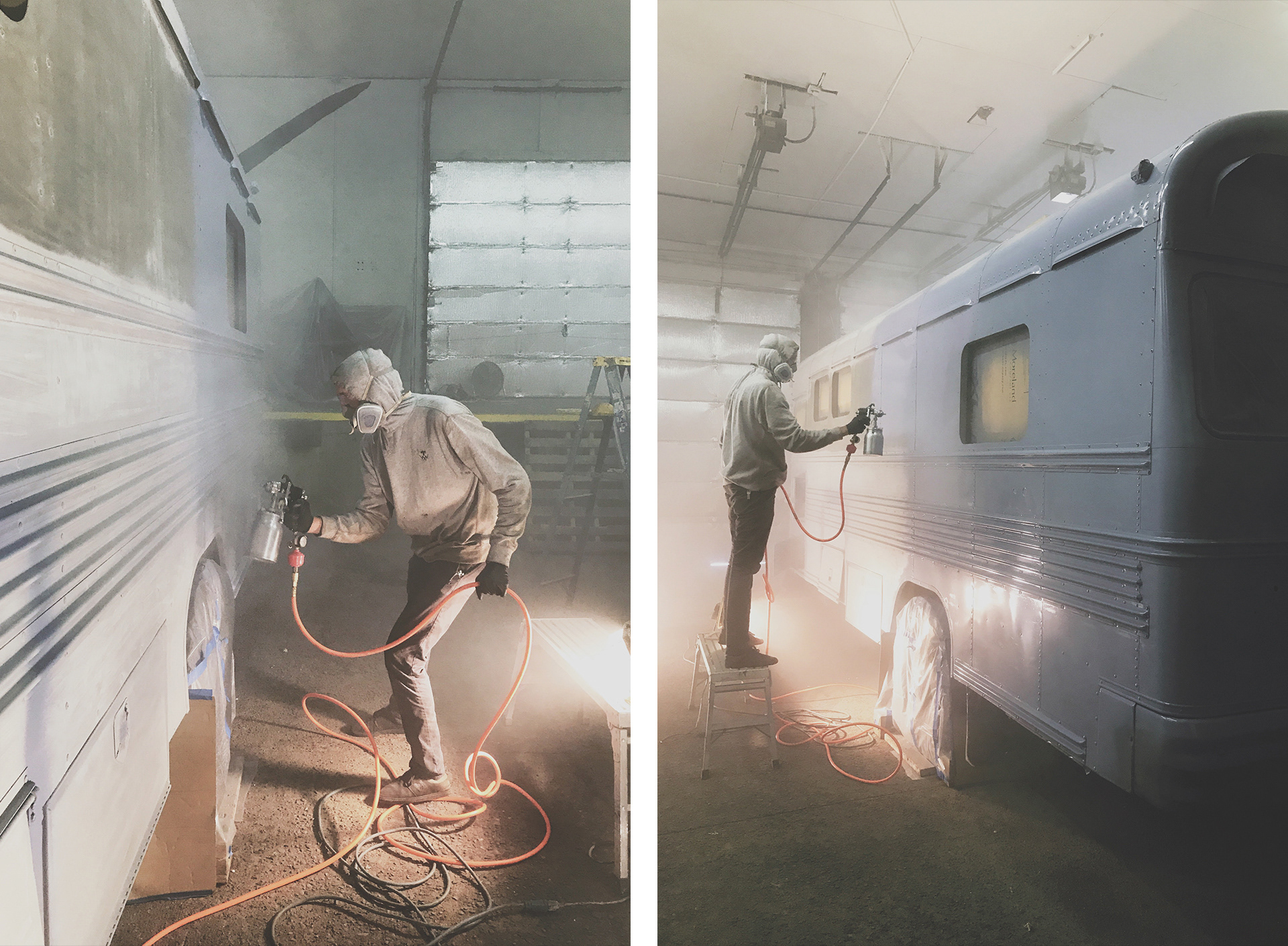
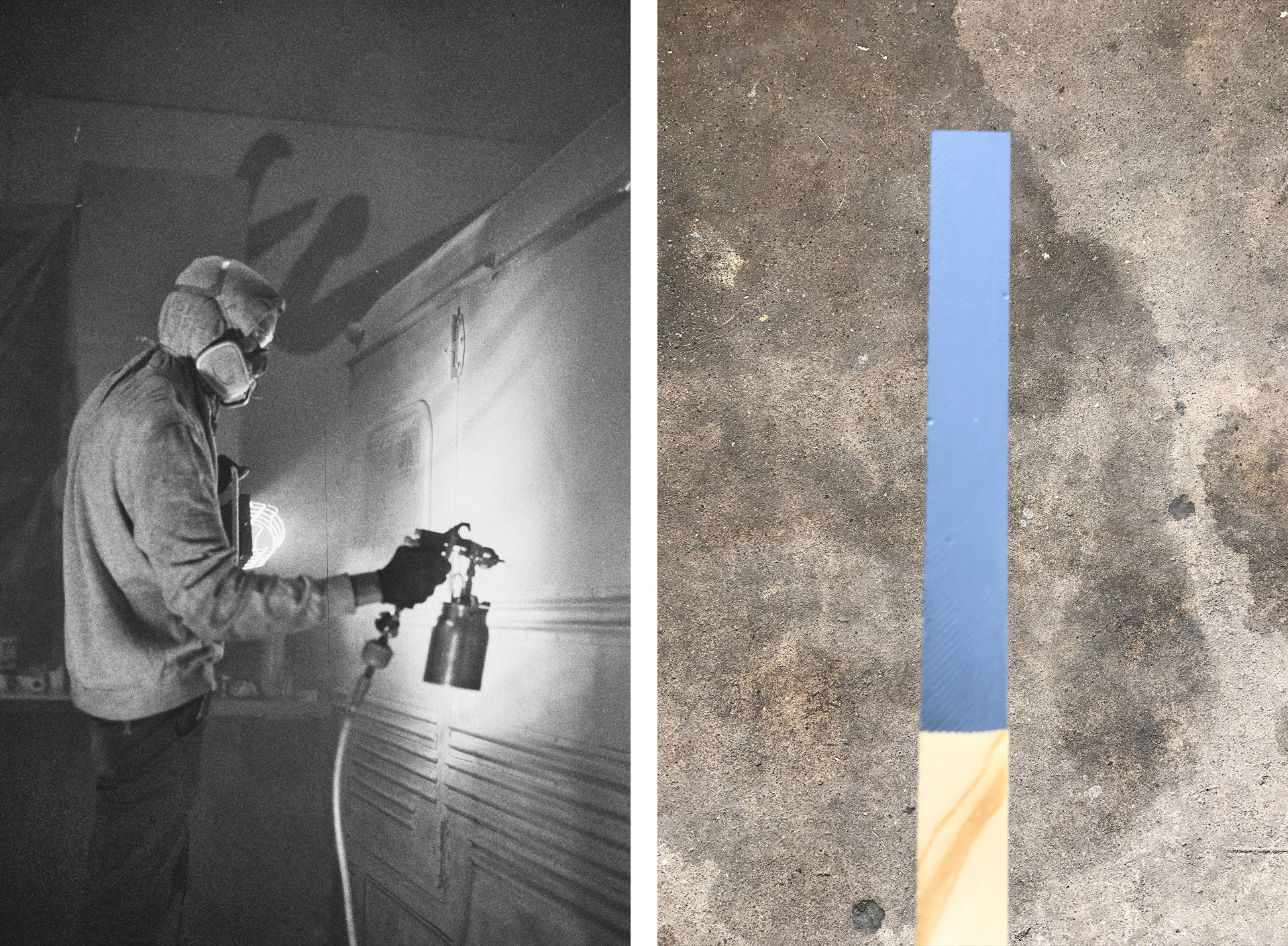
We didn't know if we'd have the bus leave on our originally scheduled date, which was a very bad thing because some of the riders' flights were counting on us leaving in time. With the team showing up, it was a nice boost that only lasted ten minutes and then it was back to work while giving them tasks to start checking off.
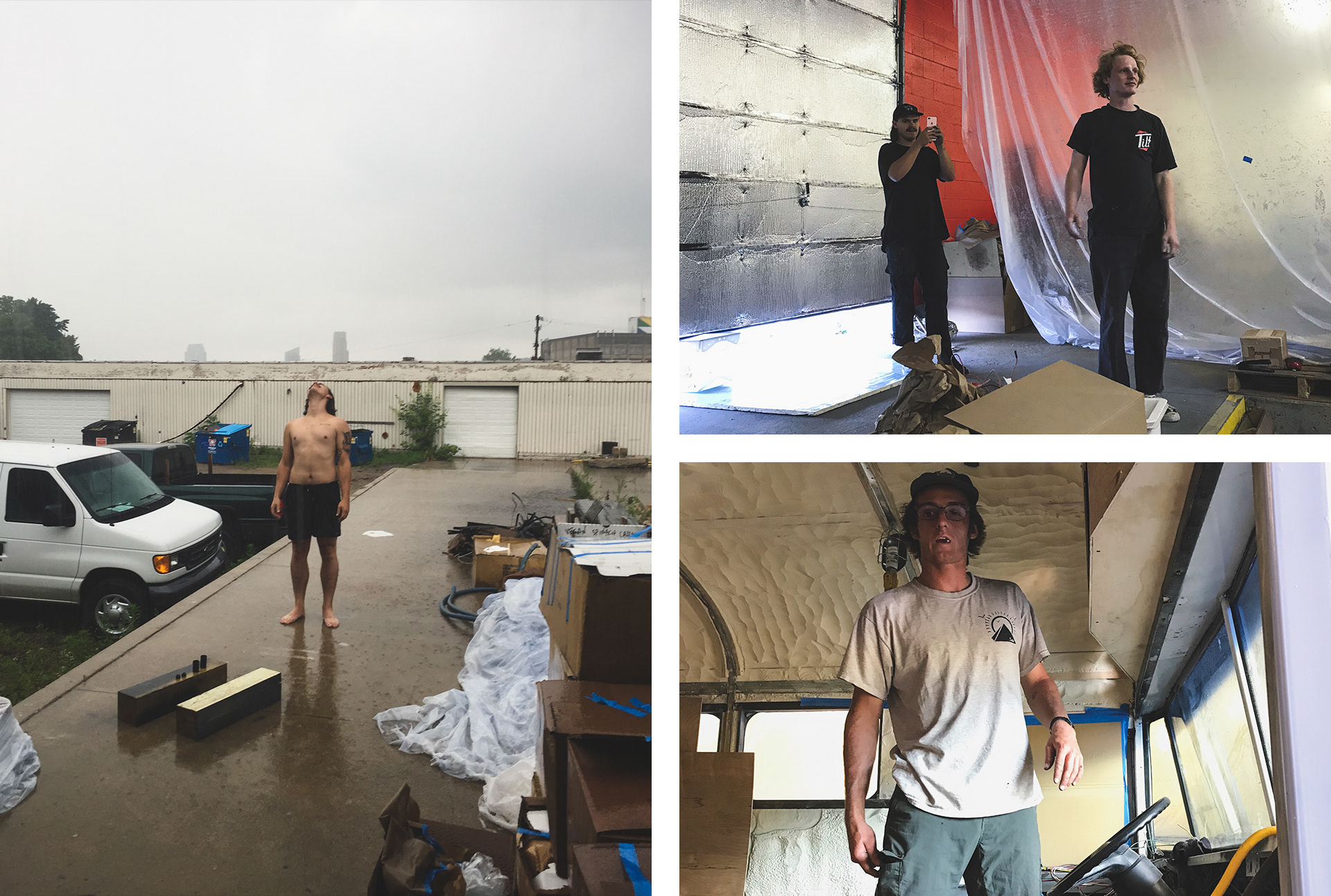
The team really didn’t have a place to stay so they were staying at the warehouse. The early crew would work on the bus in the dark with a flashlight but come nine A.M., it was all power drills and lights. Since they were living there, they had no where to shower. It ended up raining one of the days so some of the dudes took advantage of the situation and got their shower in. The trash begun to get out of control with a mixture of normal life and bus life. The warehouse was the worst we have ever seen it.
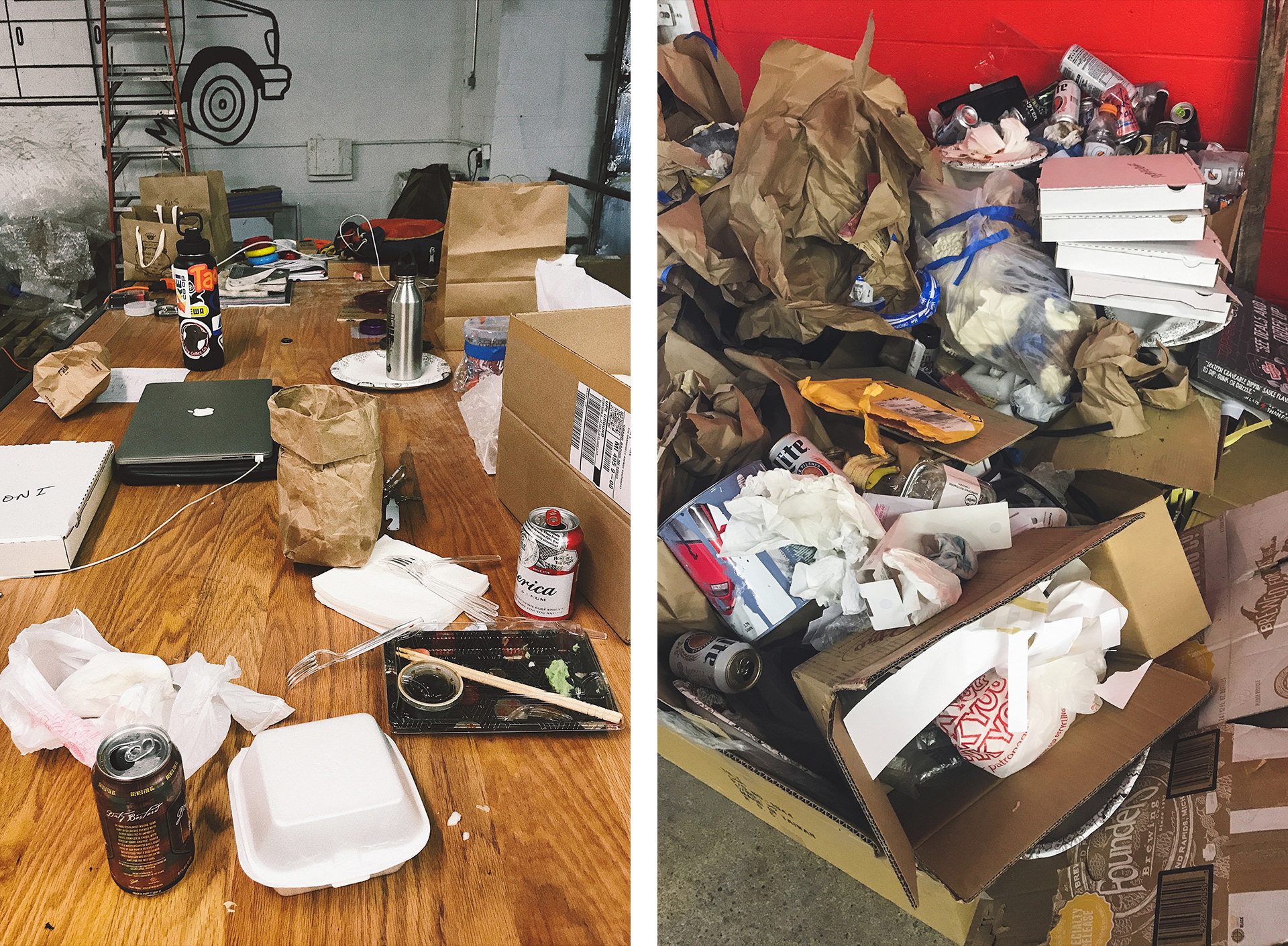
A select group of people were down to feed us and keep us hydrated while we were killing ourselves on the bus. Ray & Michelle Snoek (Collin’s parents) made a bunch of homemade pizzas for the entire crew one of the nights. Michelle would randomly drop off breakfast for us. Jess & Dante would cruise by and feed us more pizza. Jason, our buddy that works at Founders Brewery dropped off a box full of beer. There was normally always something to munch on or drink while the chaos was happening. This helped out a ton because when you’re busy, it’s crazy how many times you forget to eat.
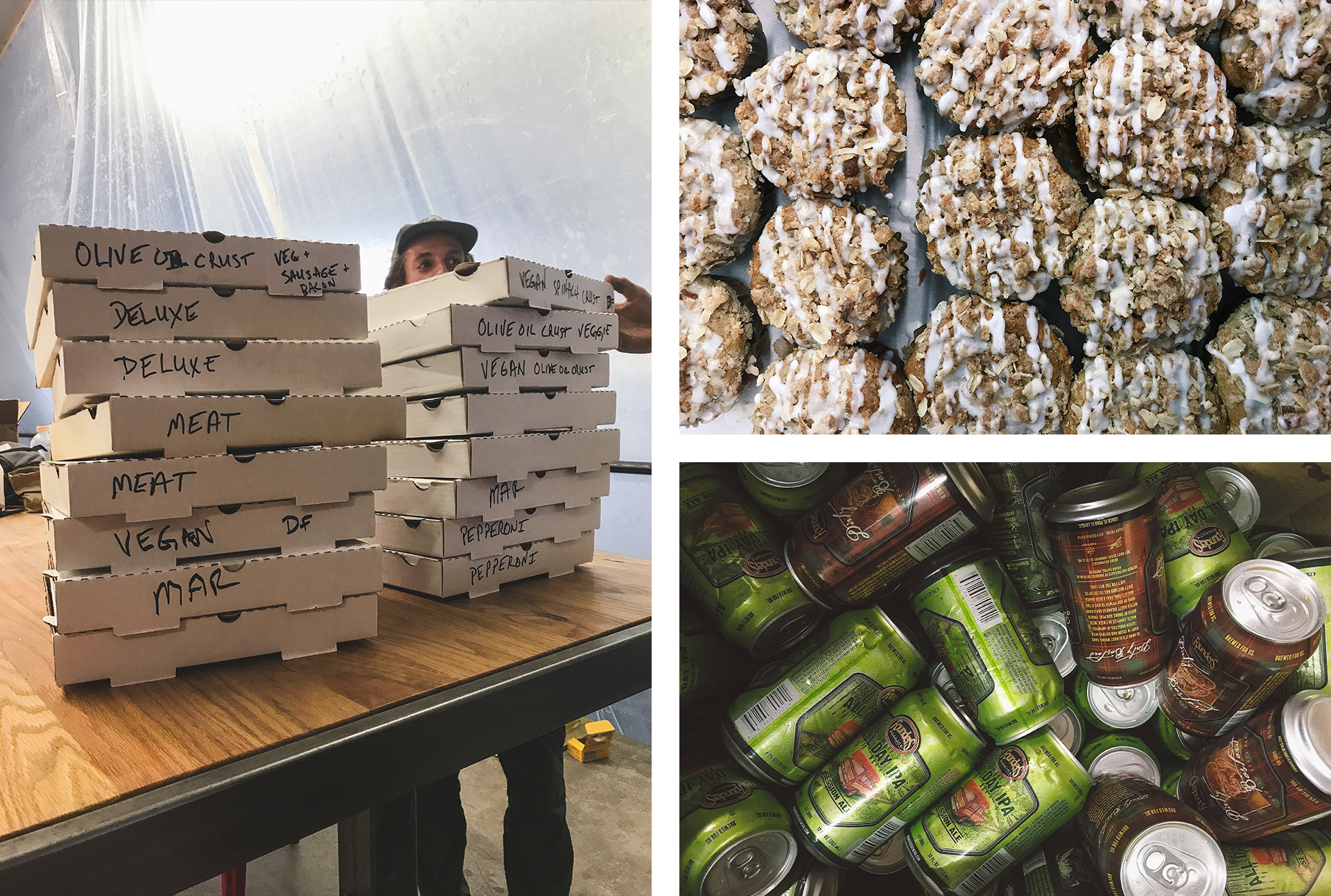
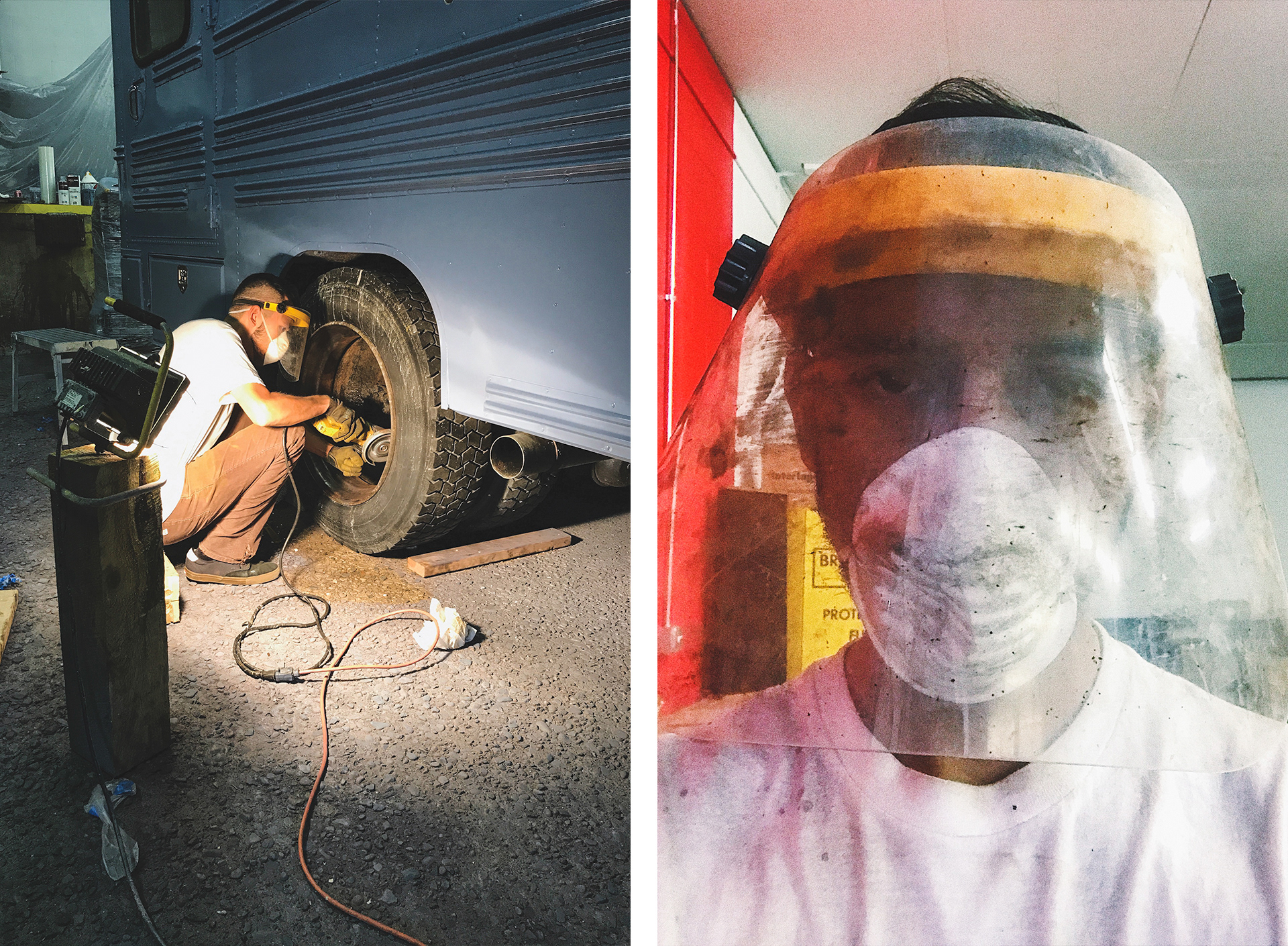
Mike was back and worked on sanding the rims with Stevie. Not an easy task, but then again, what was on the bus. They got a fresh coat of black automotive paint along with the bumpers and additional metal trimmings.
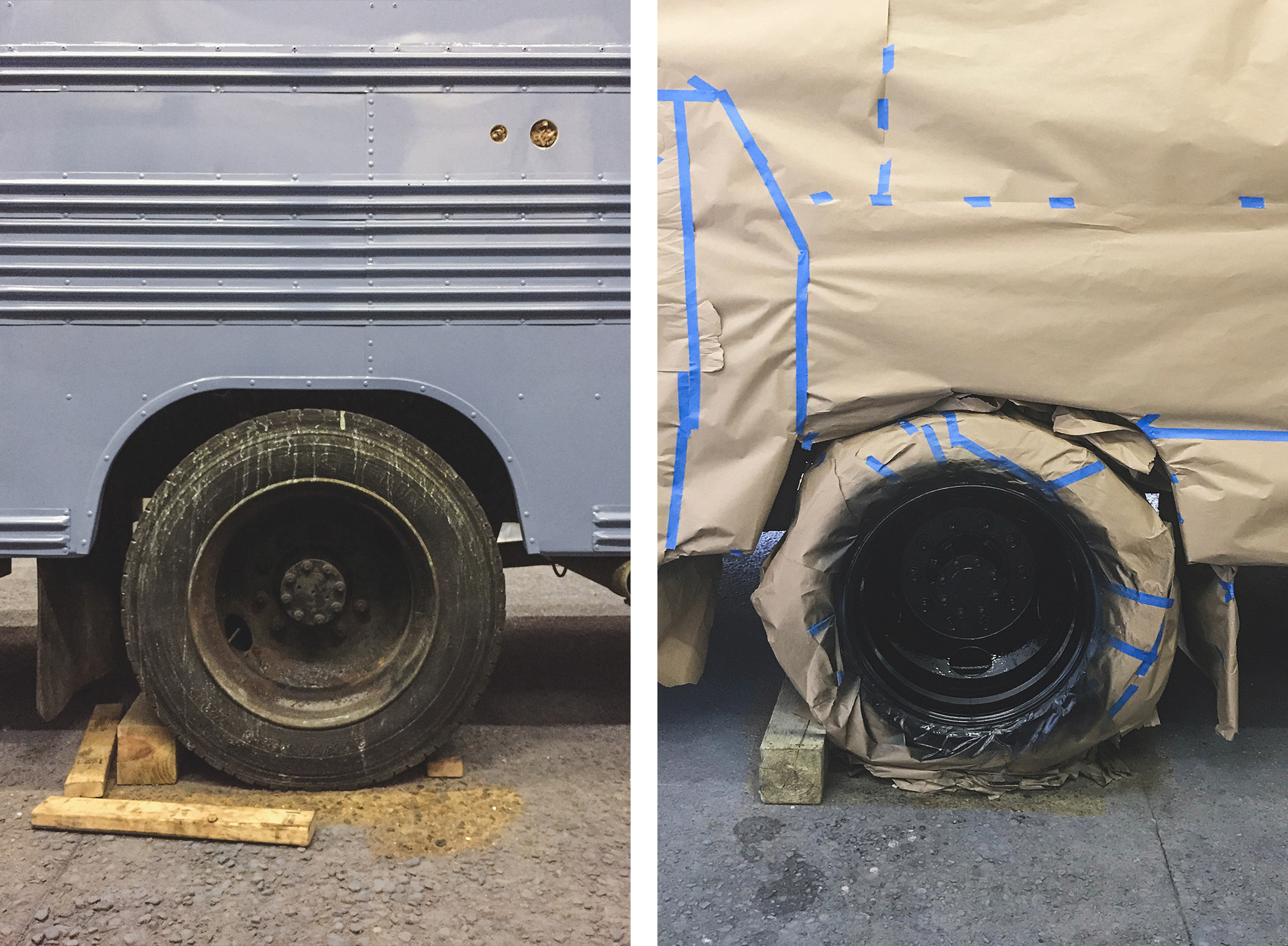
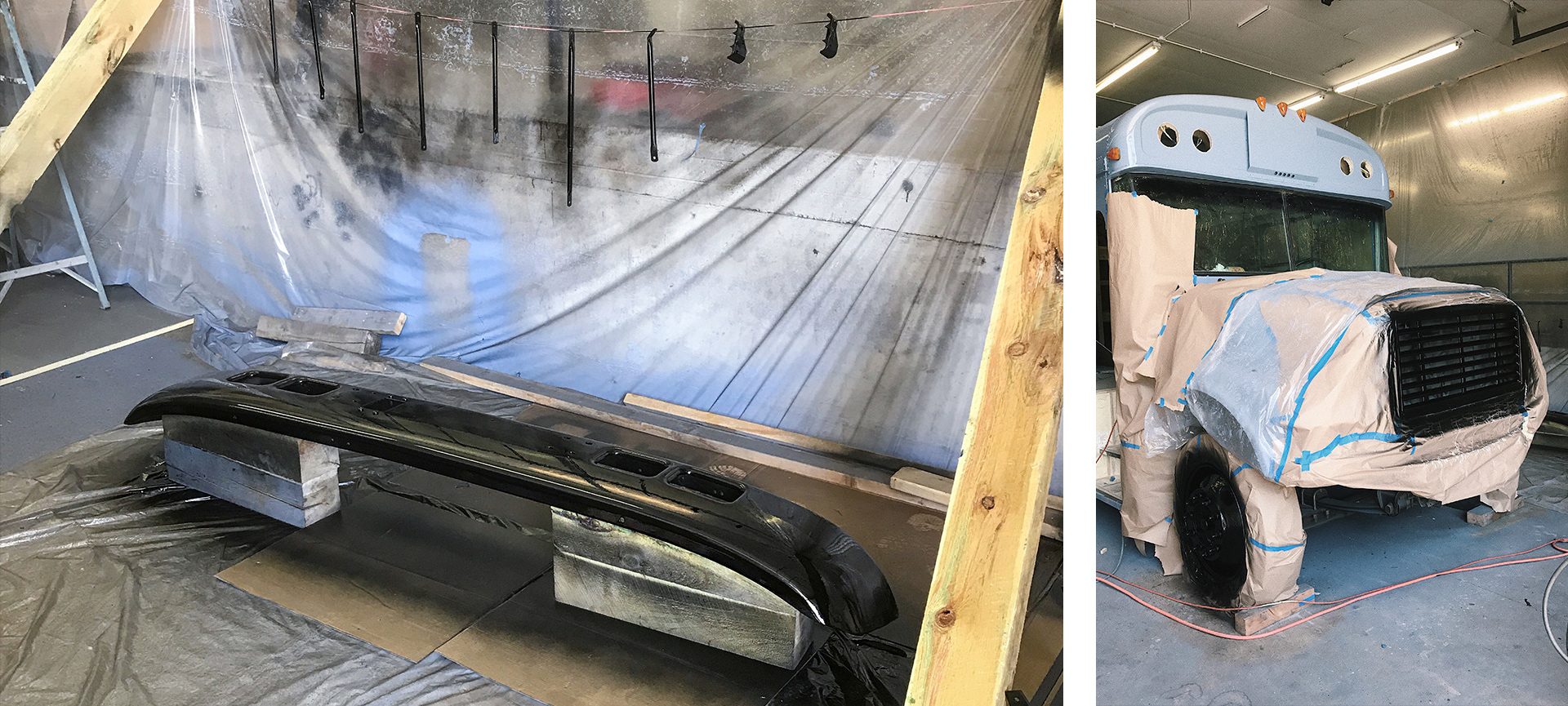
The roof got a couple coats of reflective paint that strengthened the roof and protected the bus from getting any hotter than what it already was. This was a crucial move.
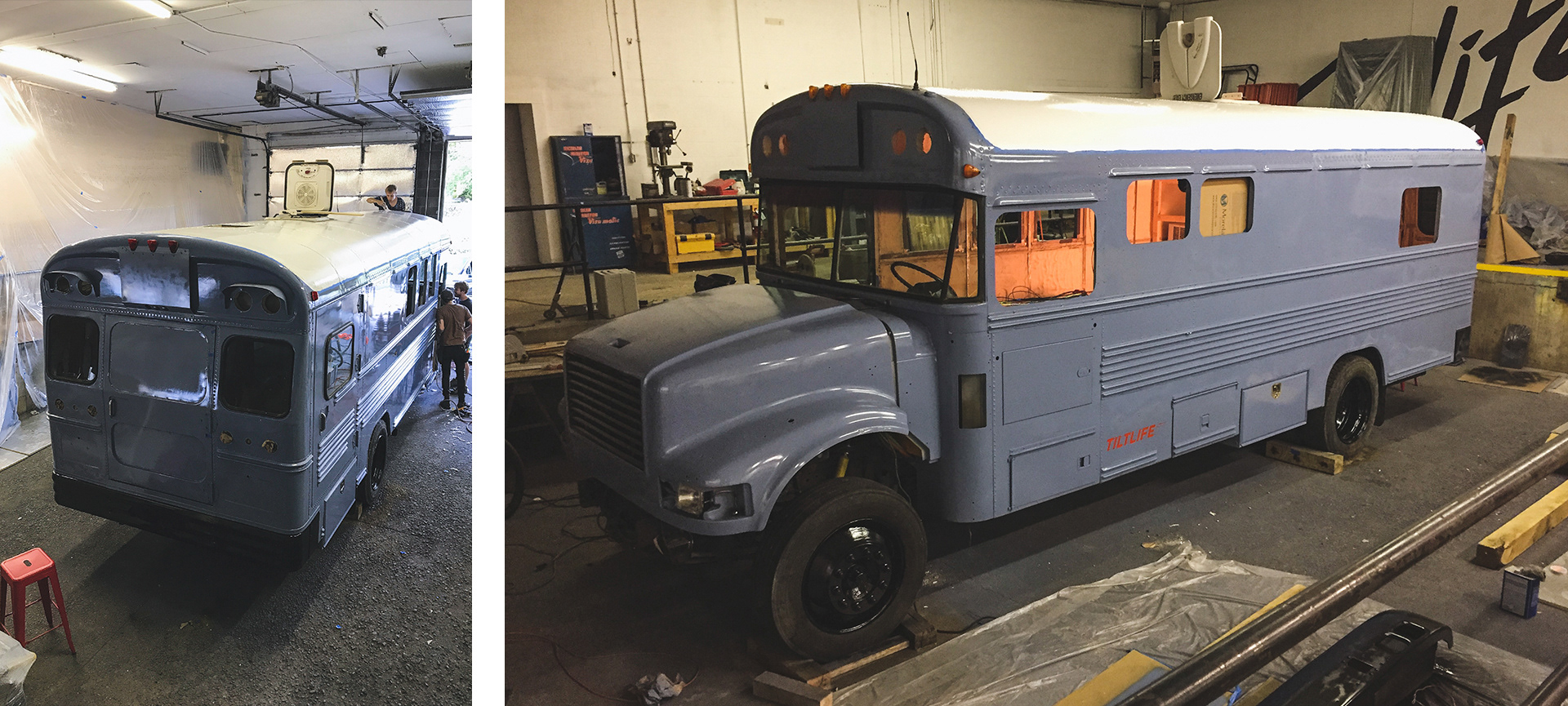
The most brutal part of the entire build was the end. The last week of building the bus was definitely the most productive, but at the same time, the most intense and exhausting. Everyone involved was both physically and mentally drained by the time the bus was ready to get on the road. Normally the warehouse has 1-3 people there at most and during the last week there were so many people and cars.
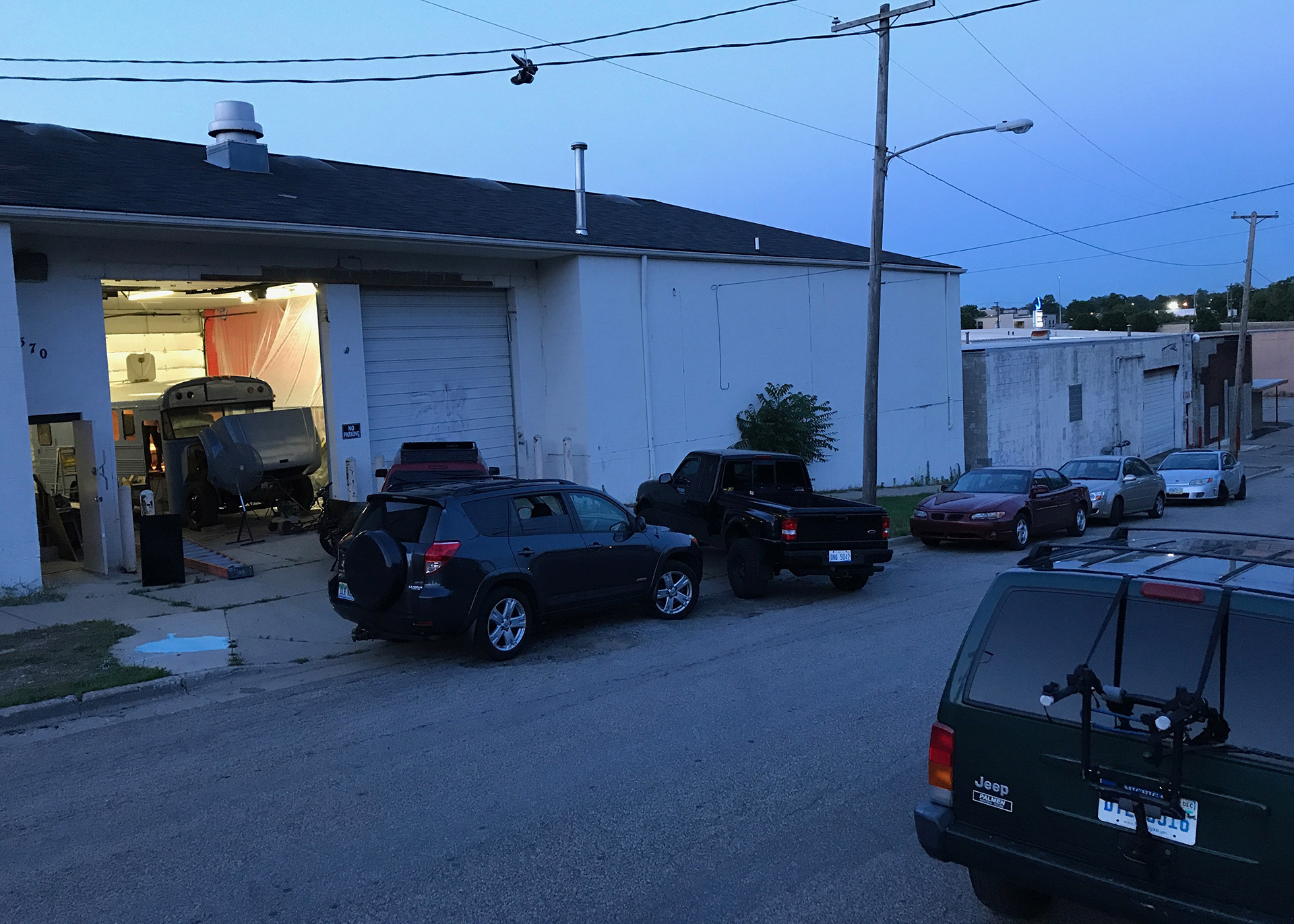
The closest I've come to crying over spilled milk is dropping a gallon of paint on the ground and losing my shit. – Collin Snoek
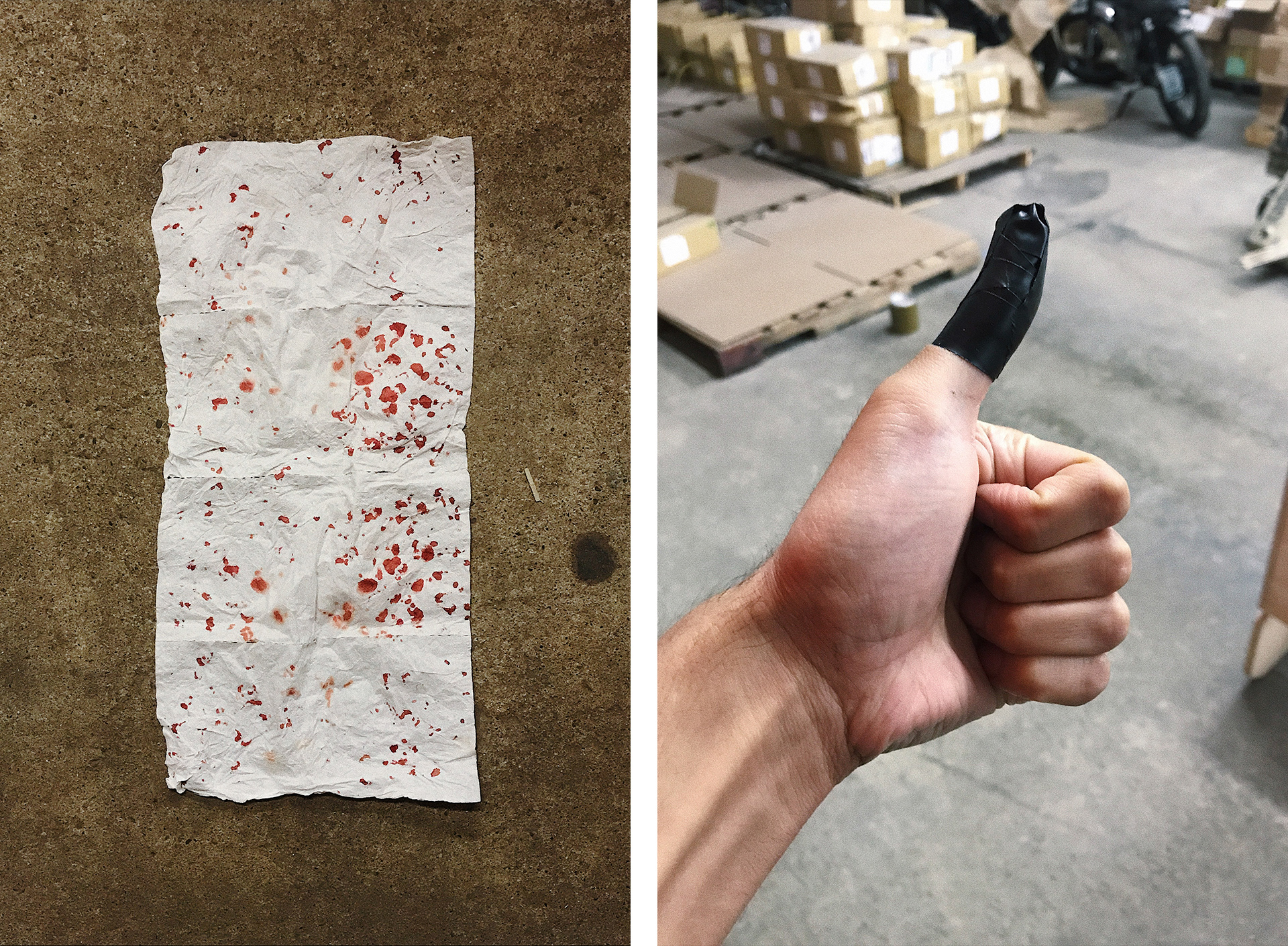
Mike ended up cutting his finger while he was working on the bus decals. For some reason his thumb wouldn’t stop bleeding so he kept taping it up with electrical tape. It was pretty funny but it worked.
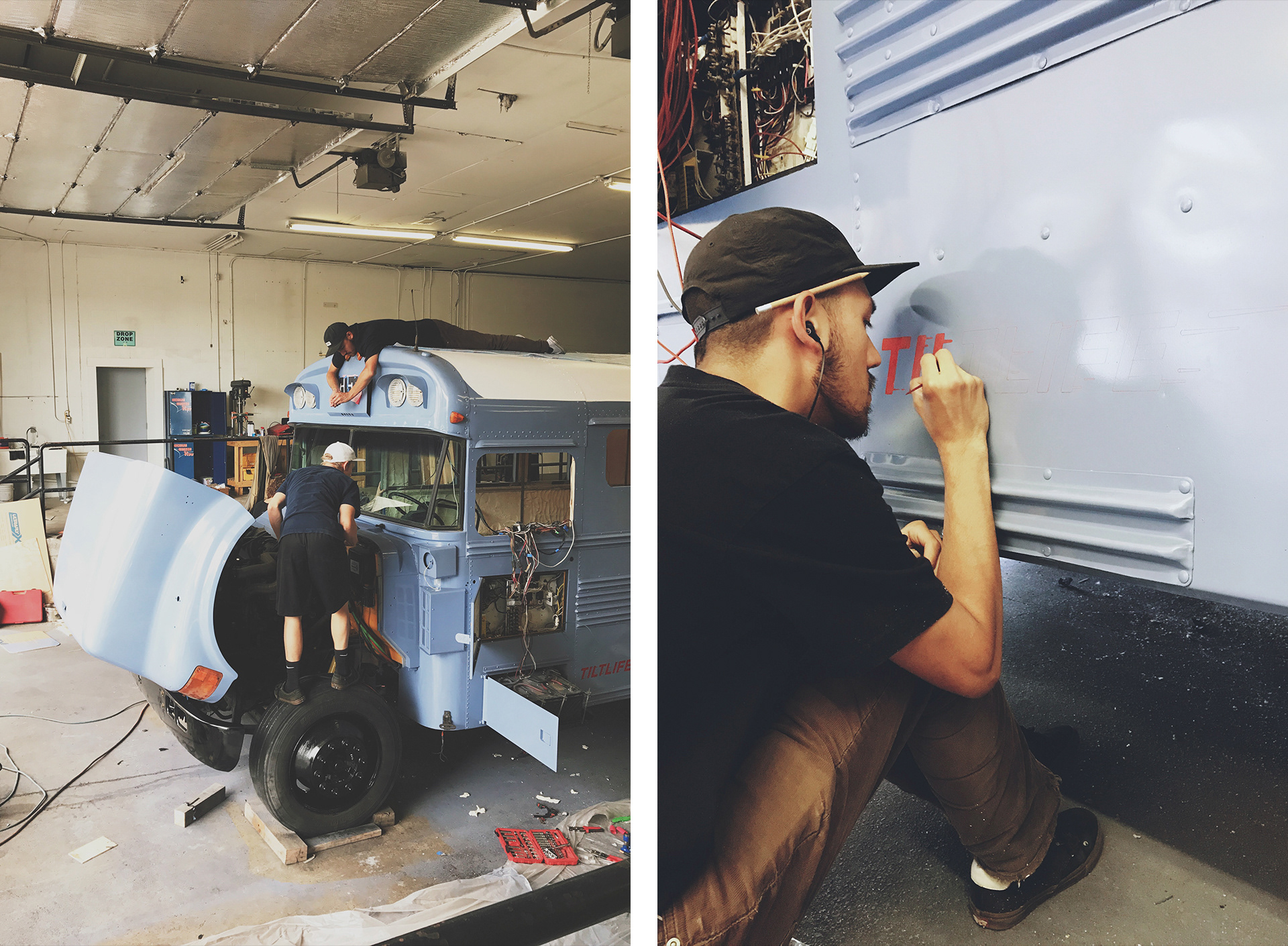
Jordan would come in whenever he had spare time and just get right to it. Painting the red lettering on the bus right next to him, I saw the progress he would make every hour. I would get into my zone and paint for a straight hour or so and when I’d get up to stretch, I’d be amazed at how much unnecessary wiring he’d removed and cleaned up. He’d just quietly kill it. The difference was insane at the end of it all. – Mike Spizzirri
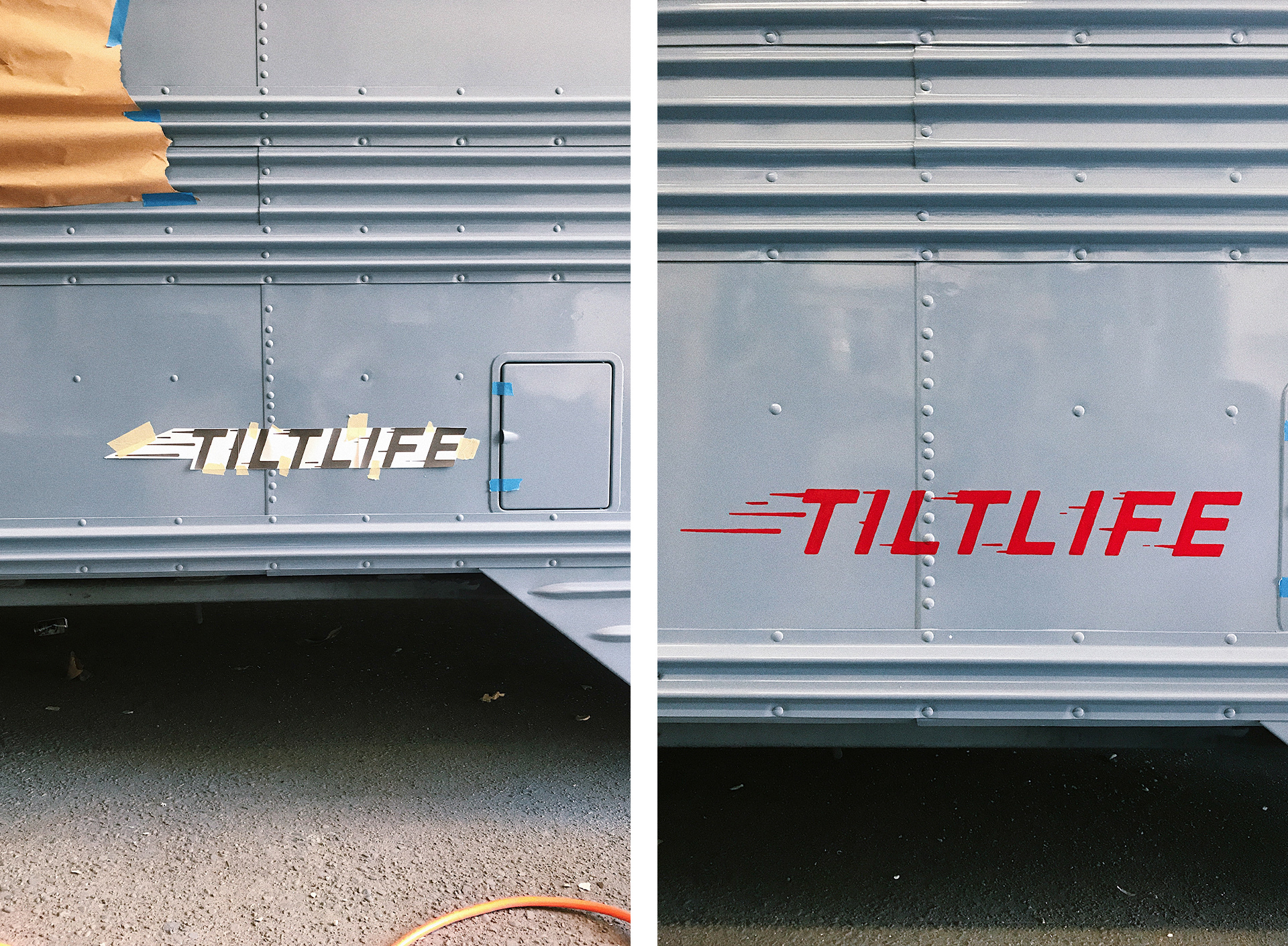
I have done a ton of loose sketching and drawing in my life, but when it comes to Tilt, I strive for everything I design to be pixel perfect. It’s a gift and a curse. Collin and Chris would be the first to know. This was why the idea of hand painting clean graphics on a bus that’s constantly being worked on, boarded, shaken, and tore apart was terrifying to me. I’m always up for a challenge, and I tend to do absolutely anything and everything I can to prepare before I make the first move. In this case, transferring all my drawings and taping straight edges off helped a ton. After that, it was all about a steady hand. – Mike Spizzirri
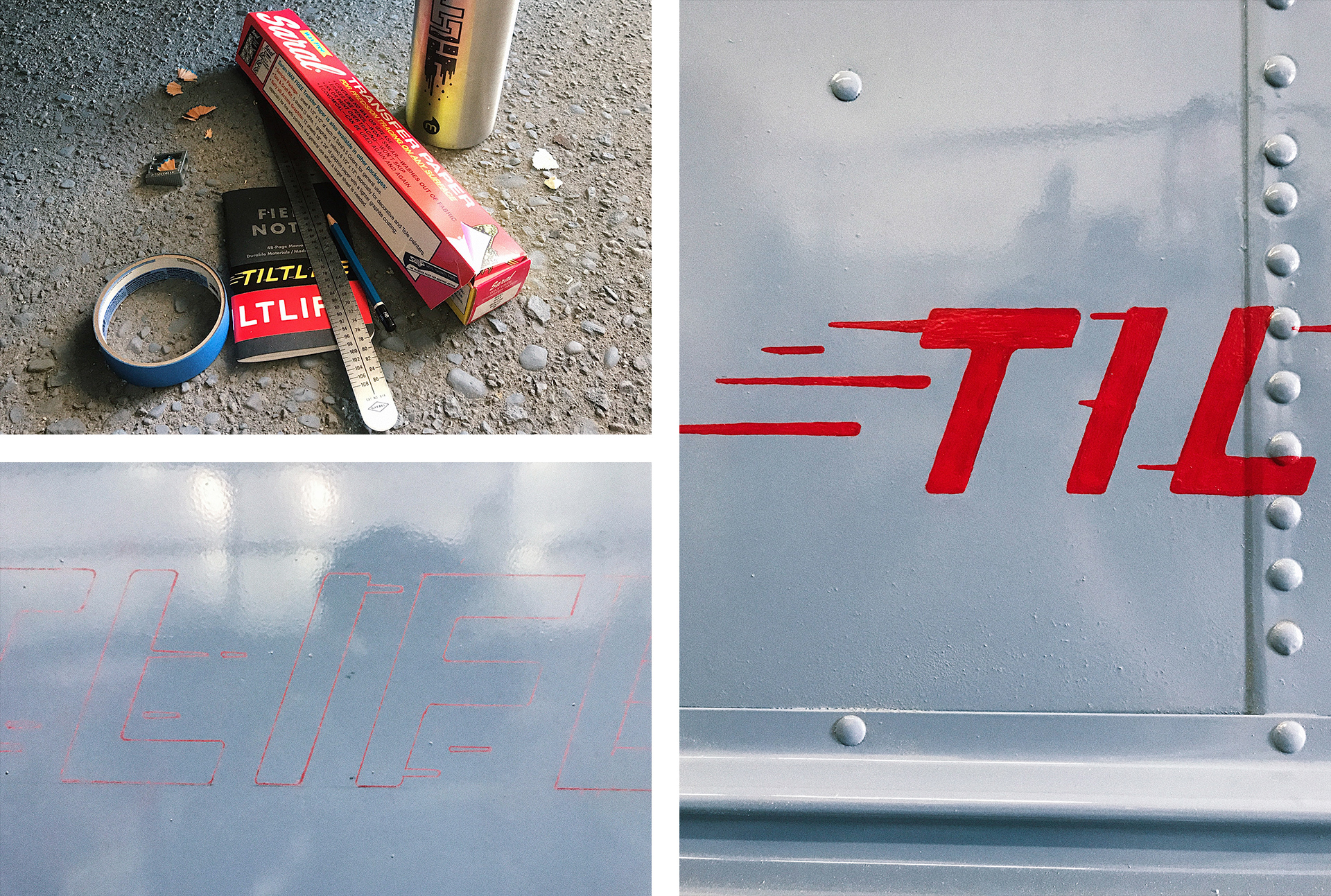
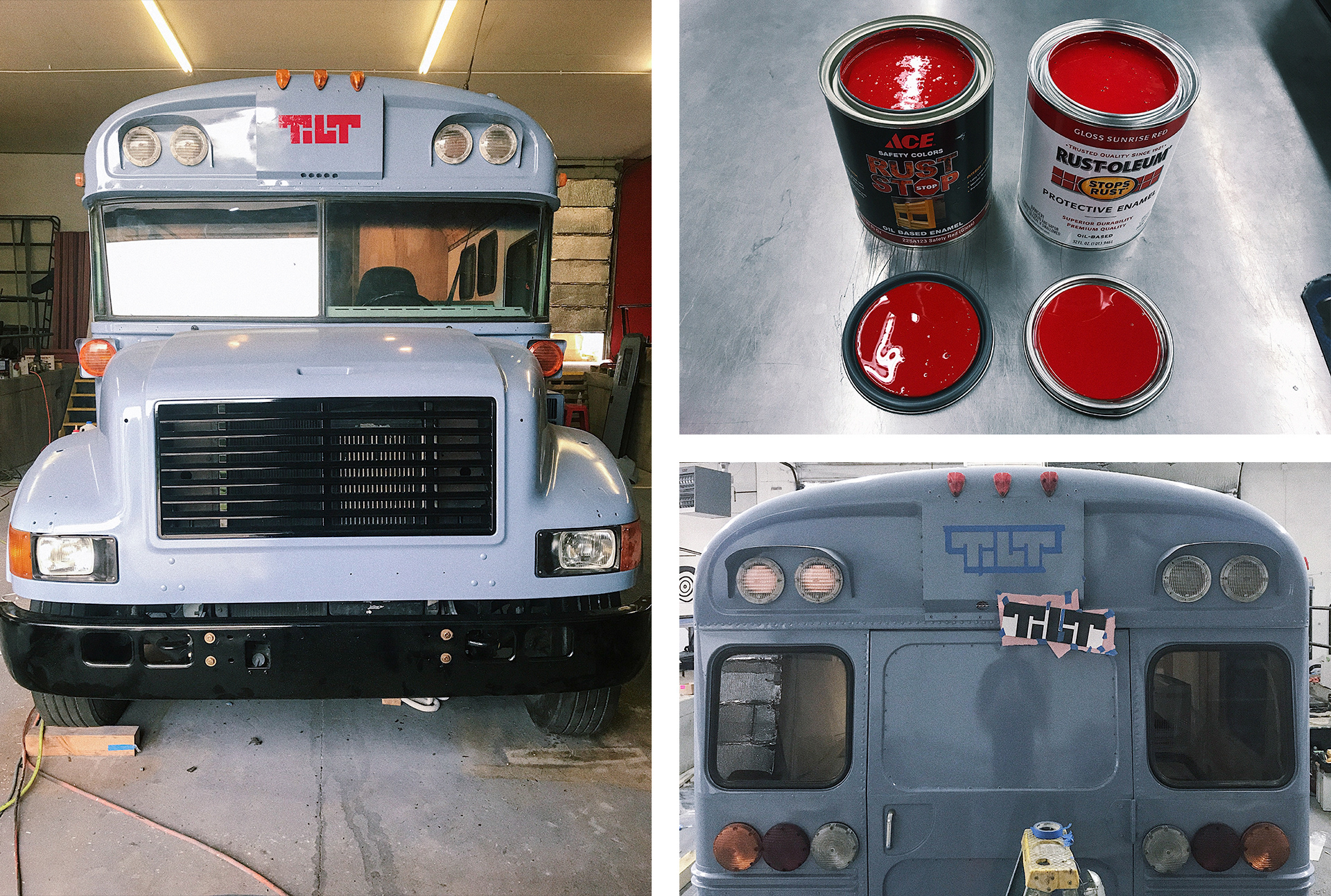
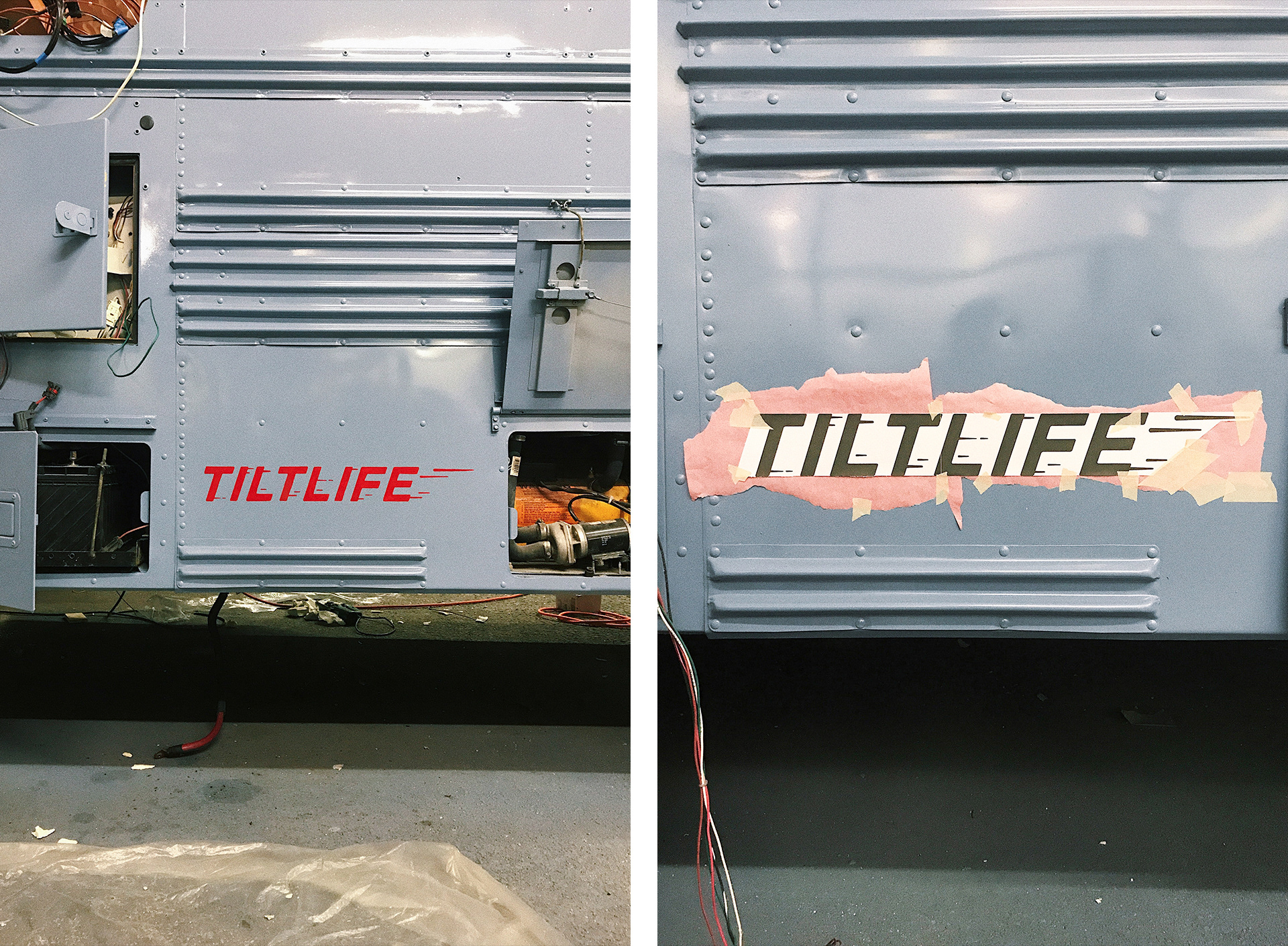
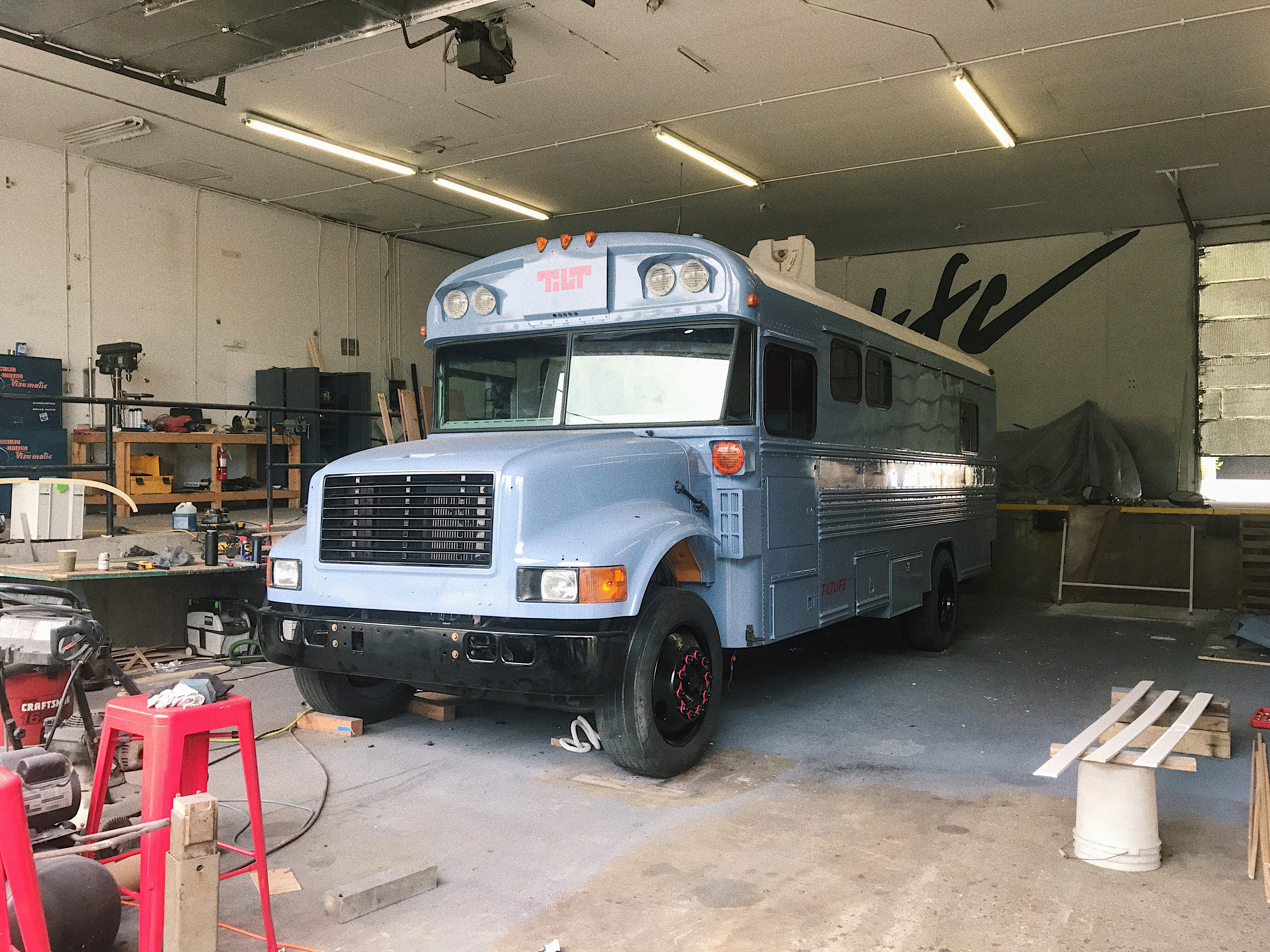
Unfortunately, I wasn’t able to be a part of the bus trip, but the bus got a part of me! My lettering design made it all the way to Portland! – Mike Spizzirri
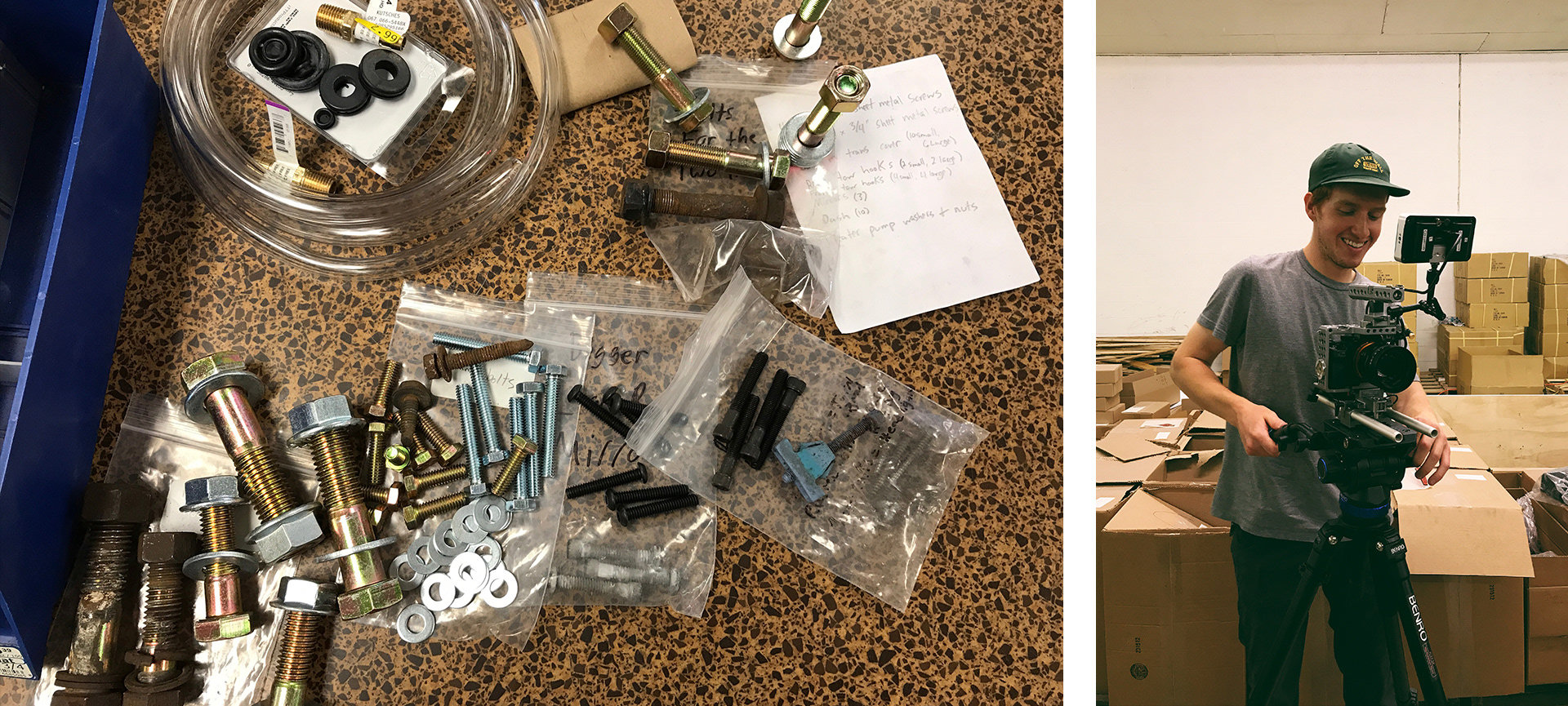
We tried to save and label all the bolts that came off the bus but with multiple people coming and going and moving things around, we lost a bunch. We had a box of misc bolts that definitely helped out but we still needed to make multiple trips to Kutches Hardware, a local hardware store that frequently hooked it up with hard to find bolts. Chris ended up running there every morning on the last week like he was grabbing coffee for the crew.
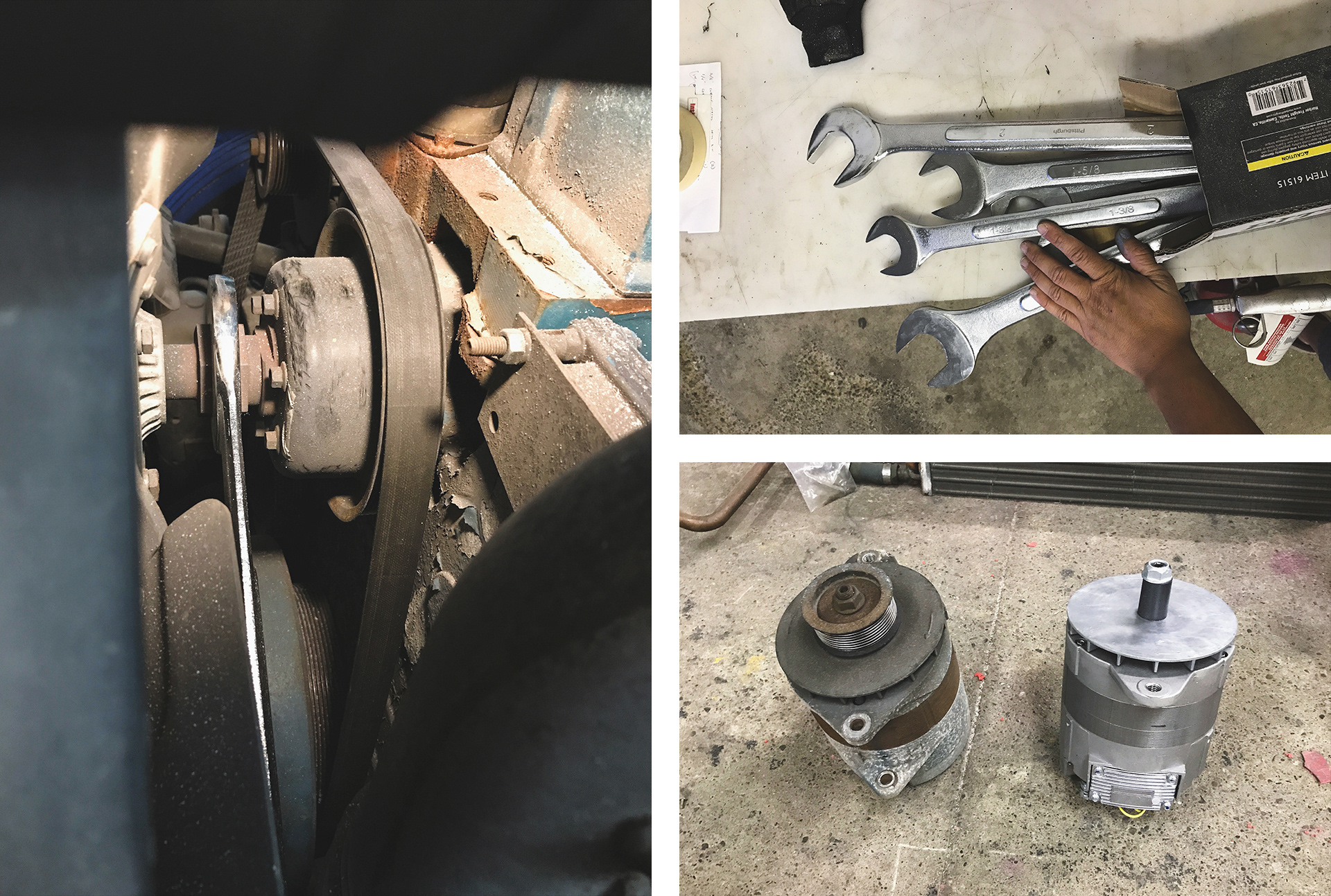
Trying to be preemptive, we replaced the alternator and serpentine belt. For some reason the serpentine belt was the hardest to find around town. Both being super simple to change minus the pulley on the alternator. We didn’t have an impact drill so we tried doing it by hand which was impossible so Andy had to take it home to get it off. Andy stepped in rather late on the build and that is because we didn’t know we needed him. He ended up wiring the audio, interior lights and inverter.
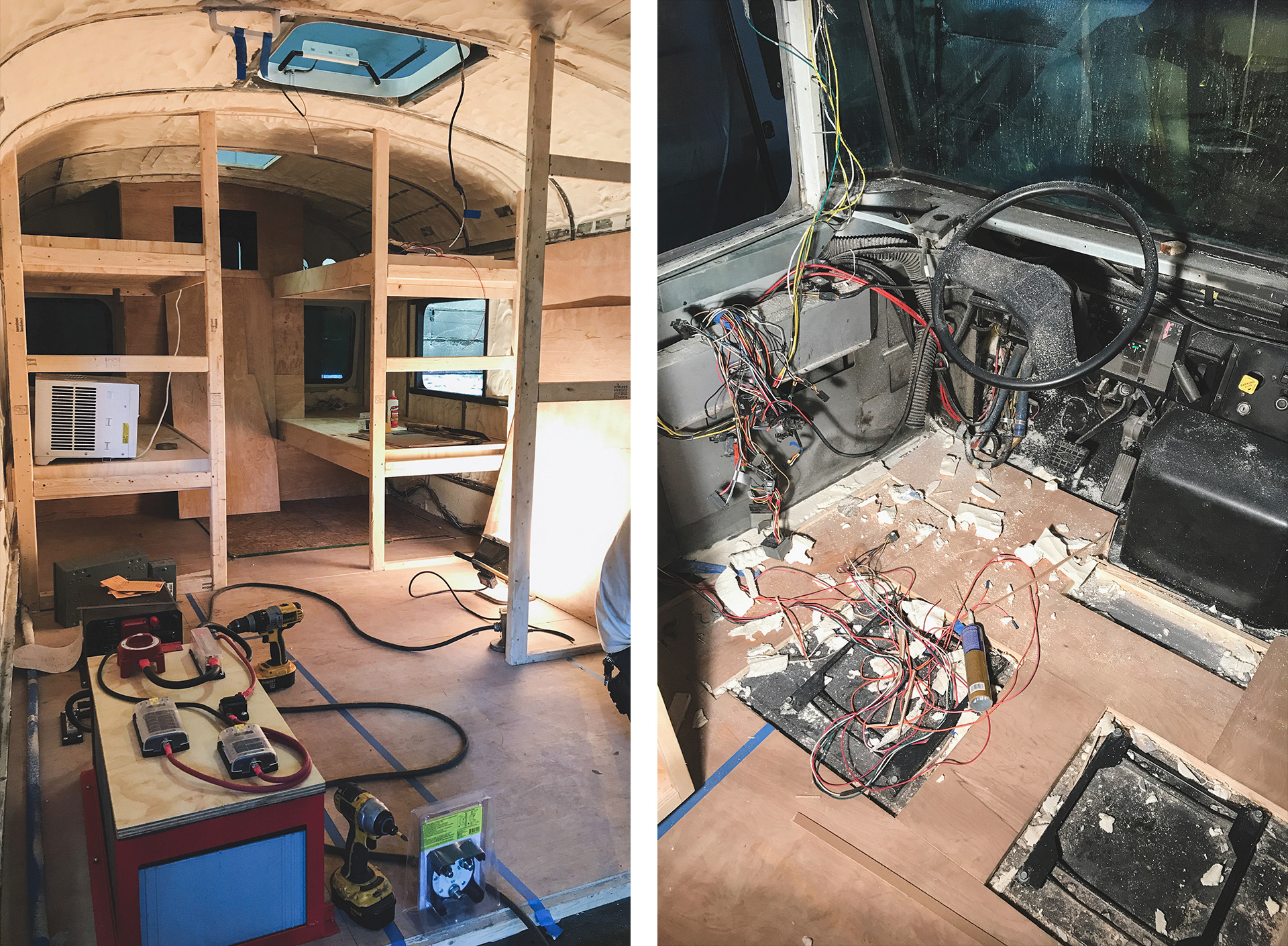
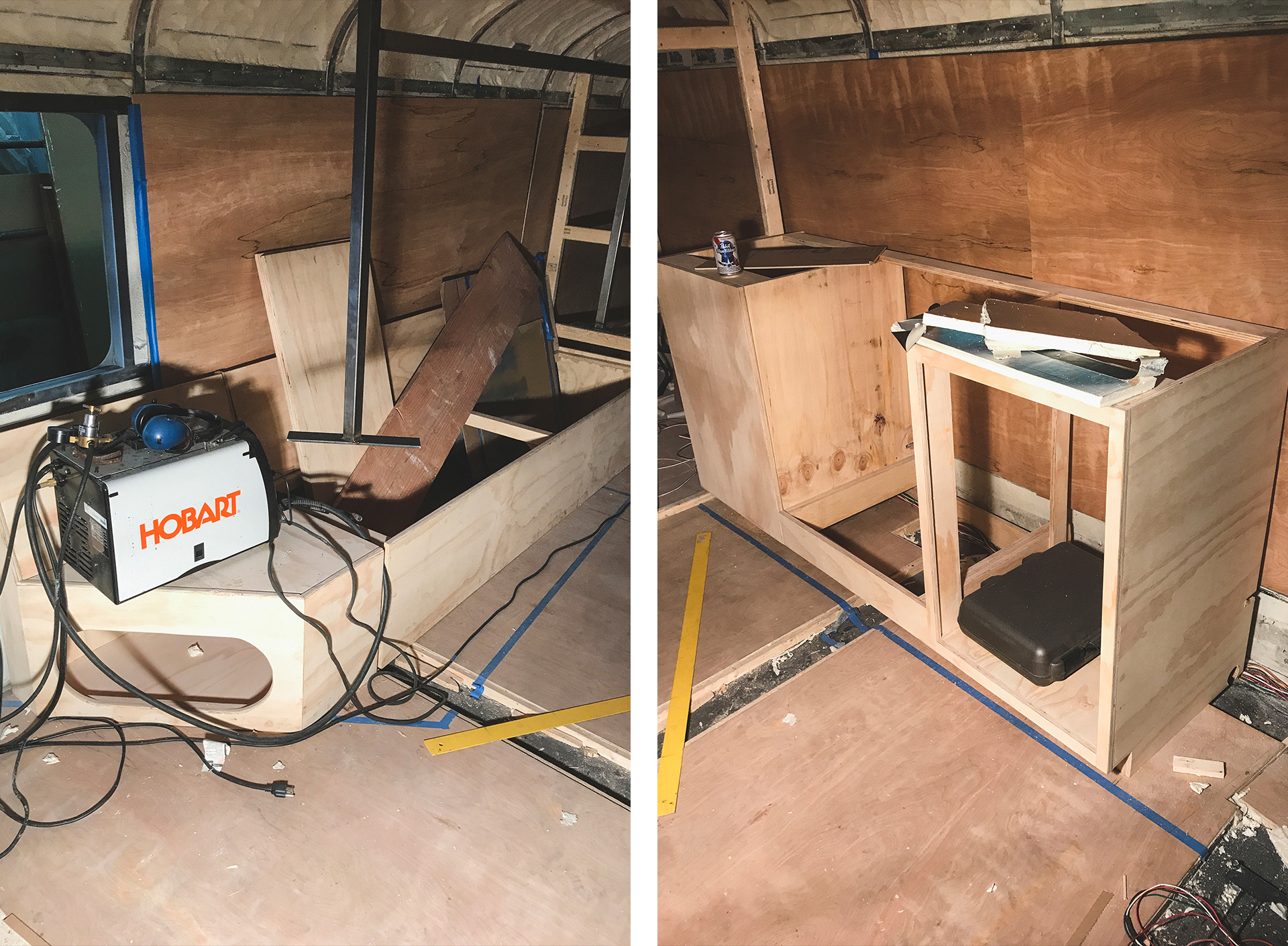
I sprained or broke my hand (no time for the doctors visit to know the difference) while being in GR so every once and a while I would get a massive build up of fluid in my hand while I was working on the bus. – Chris Martin
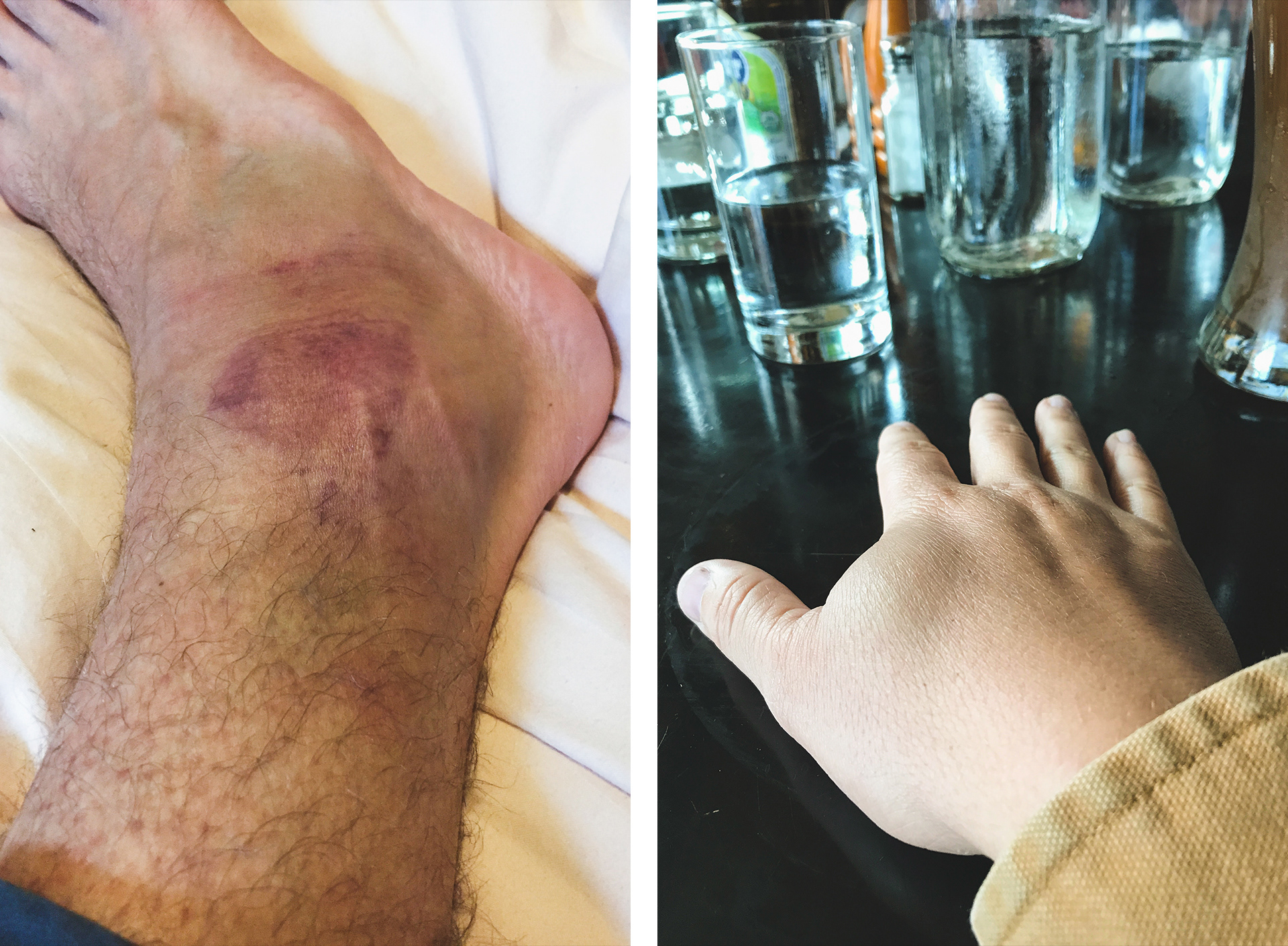
Towards the end of the bus build I was pulling such long hours that I became a hazard. I've had a dislocated toe for over a year, and the constant physical work on the bus was taking a toll. My work boots were on my feet so much that an infection grew and worsened from the movement and sweat. The toe became infected to the point that I had to take a break to run over to the ER. The ER held me for extra time because my vitals were off. After a while they warned me about pushing myself so hard and reluctantly let me go. Soon after that, I was hopping down from the bus late at night. When I landed, my ankle popped sideways and rolled. I was exhausted to the point that my basic motor skills were diminishing. – Collin Snoek
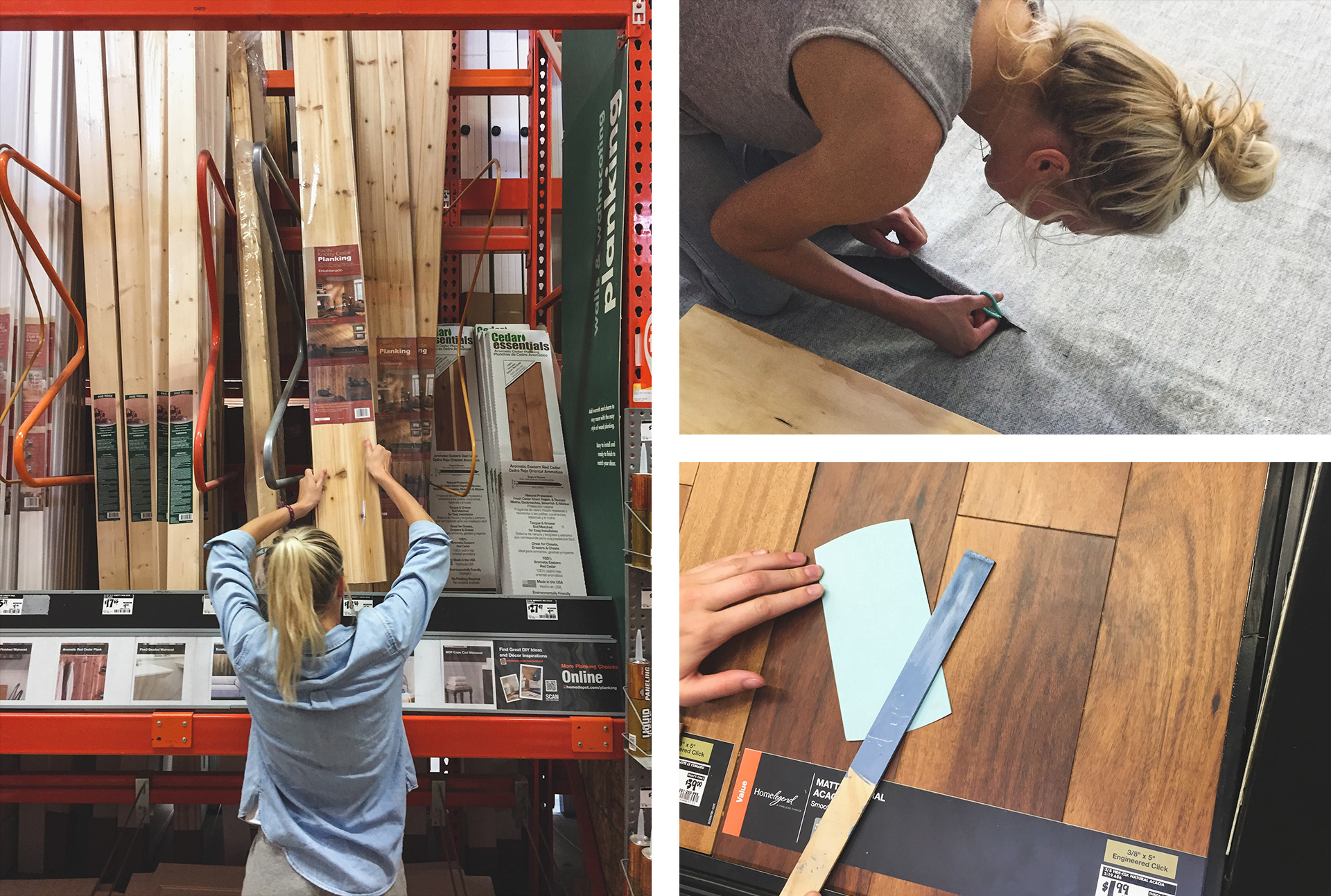
Jess lended a helping hand by choosing colors, wood and fabric for the finishing touches. She ended up sewing the cushions for the bench and helped paint the cabinets and bench with Tom K. The funny thing is, We bought two different options for the floor because we thought the first option was going to take to long. Turns out we didn’t use either and just painted the floor grey so we could get the bus on the move. Just adding one more task for when we have some spare time to work on the bus again.
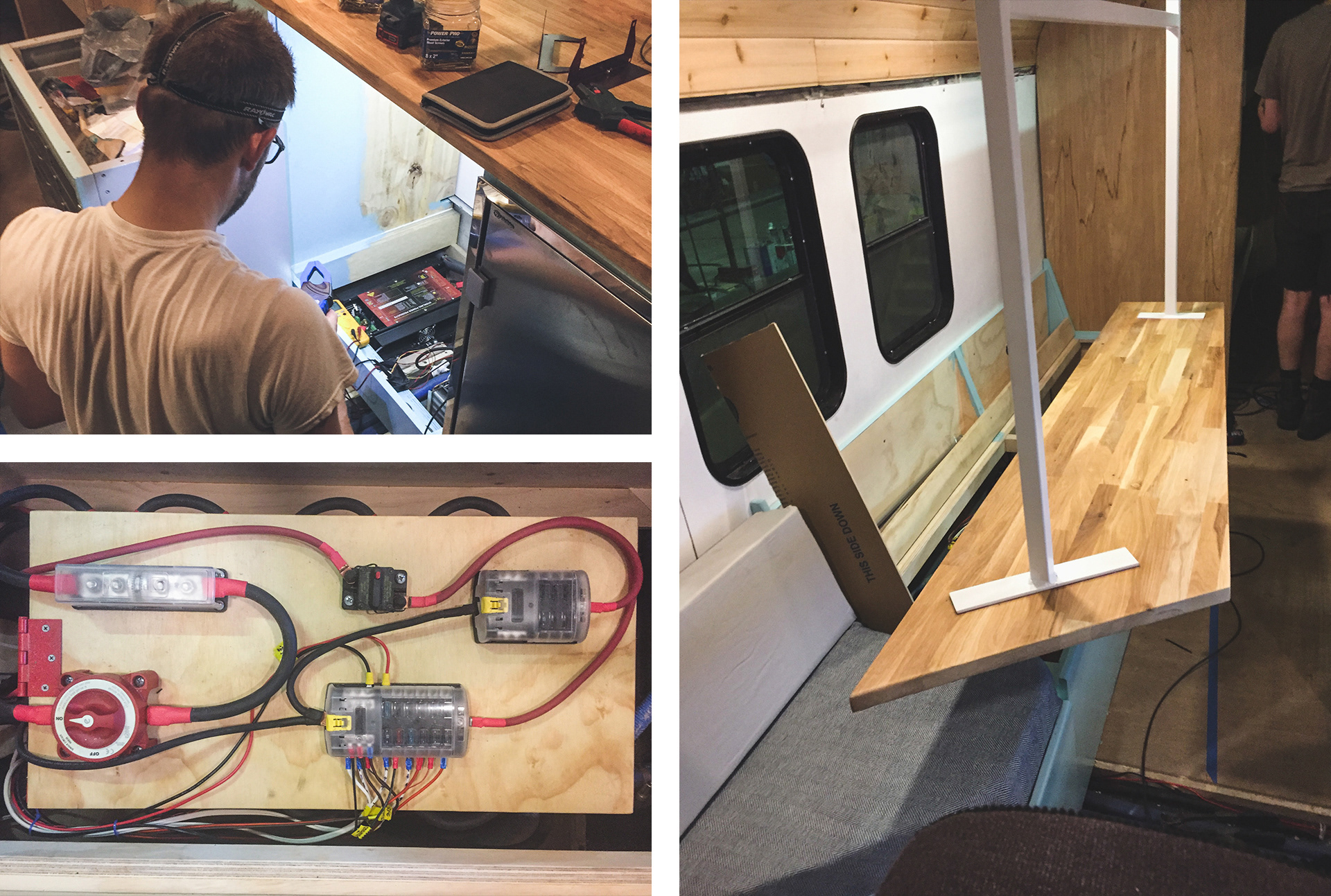
The bus was never fully completed because riding and traveling was more important than spending another week fine tuning everything. The bus had sat for almost 2 months with the batteries disconnected, the motor worked on, random wires missing and some how it started. Everyone in the warehouse couldn’t believe it. From there it was, do what you need to do to get this thing moving.
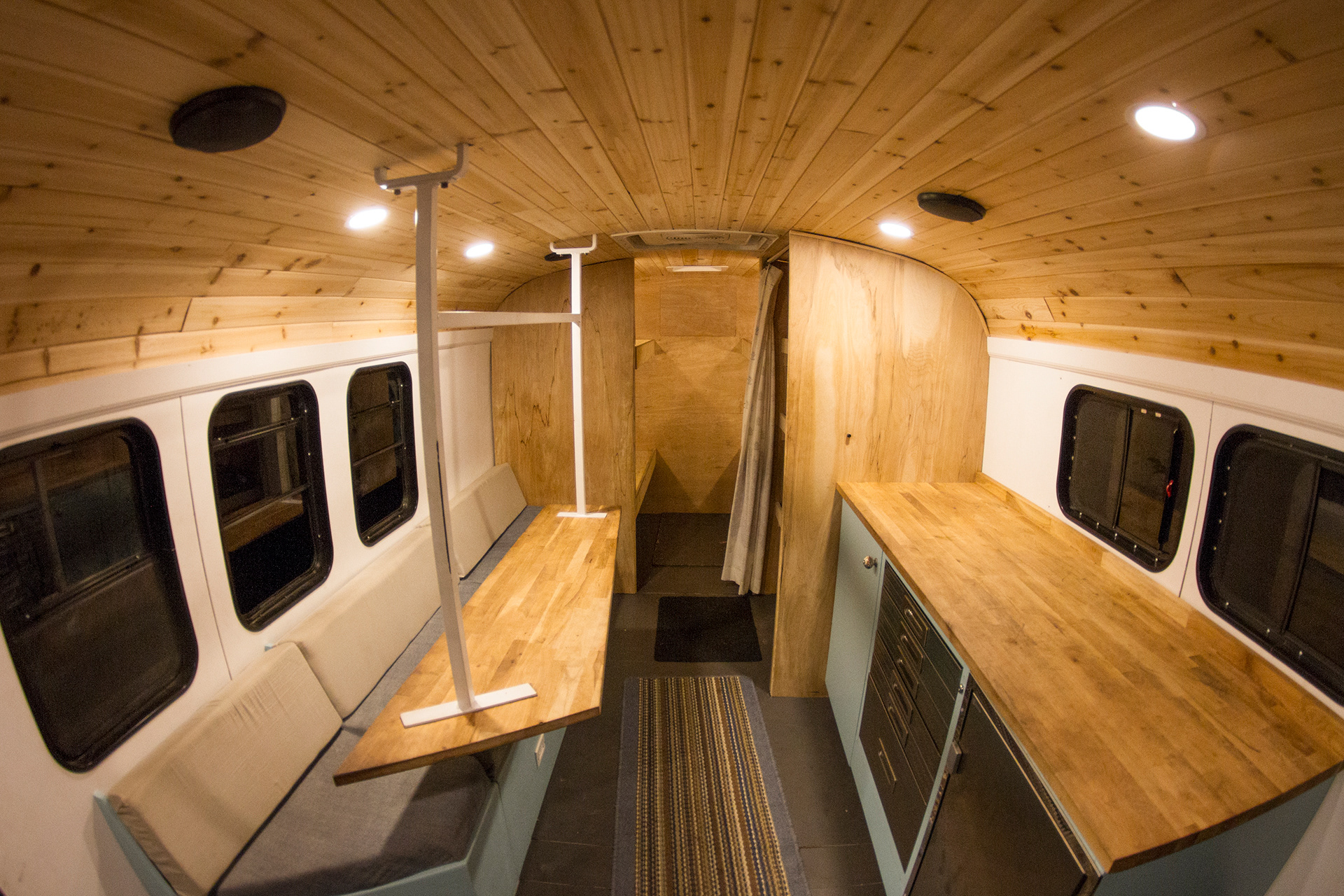
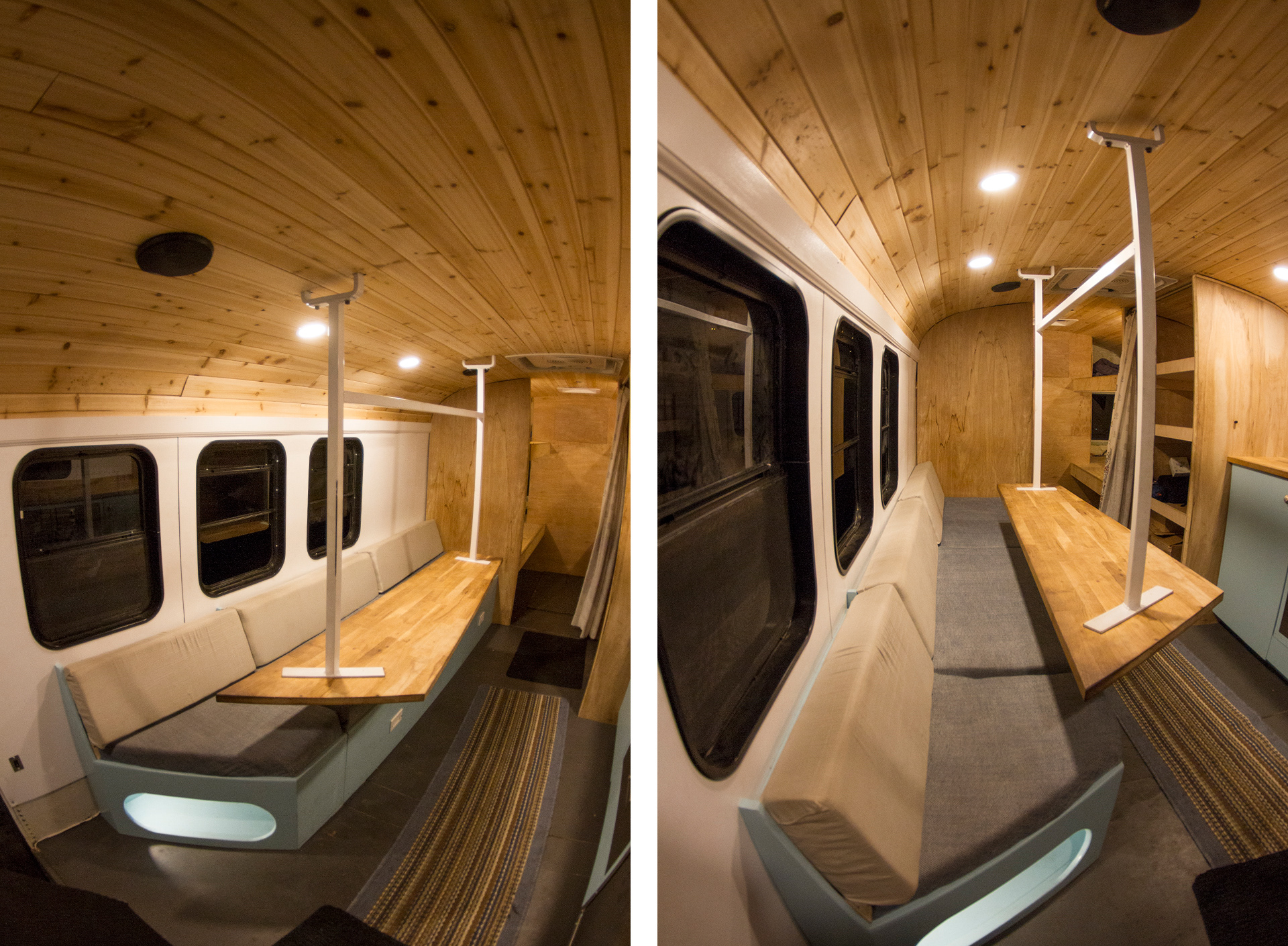
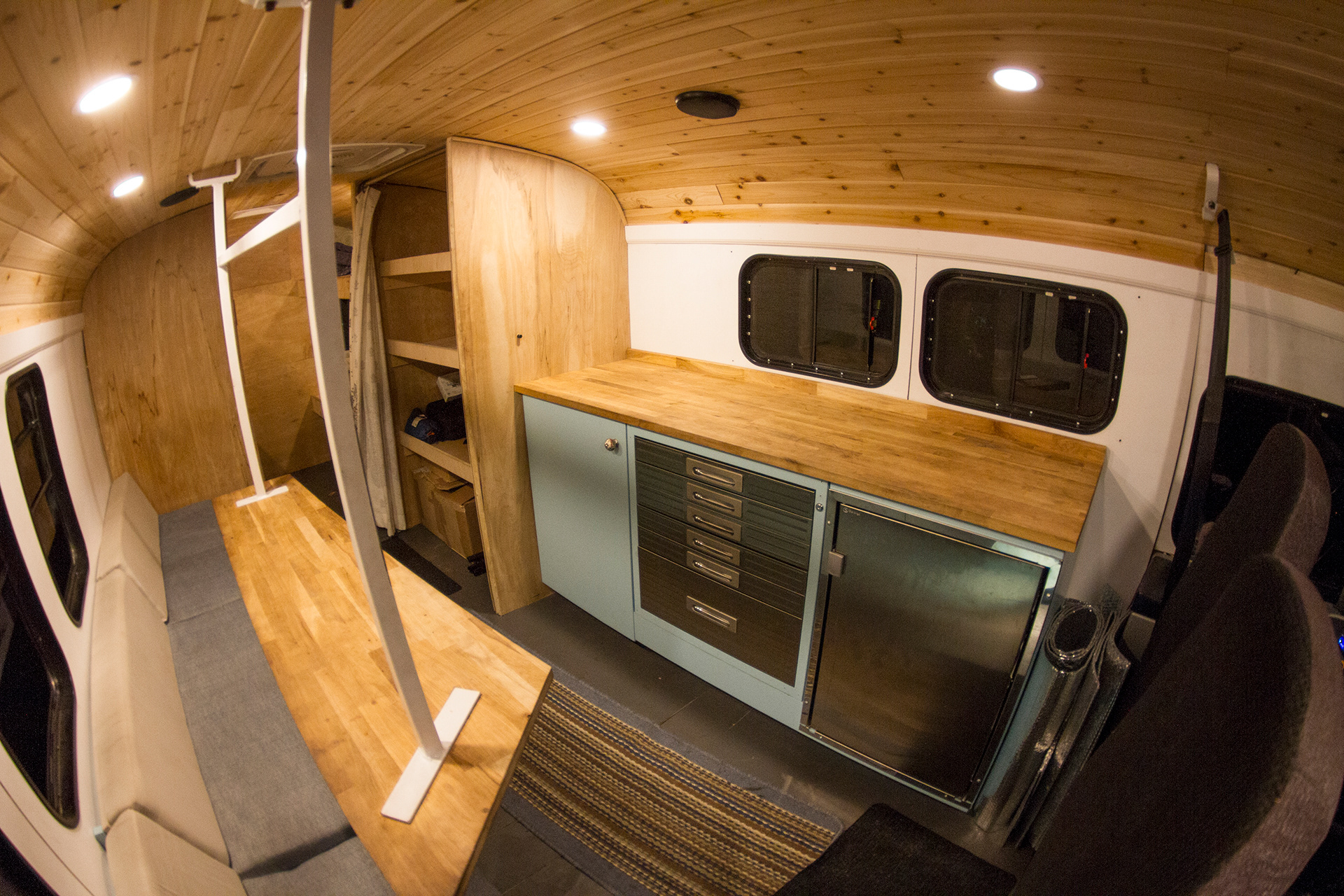
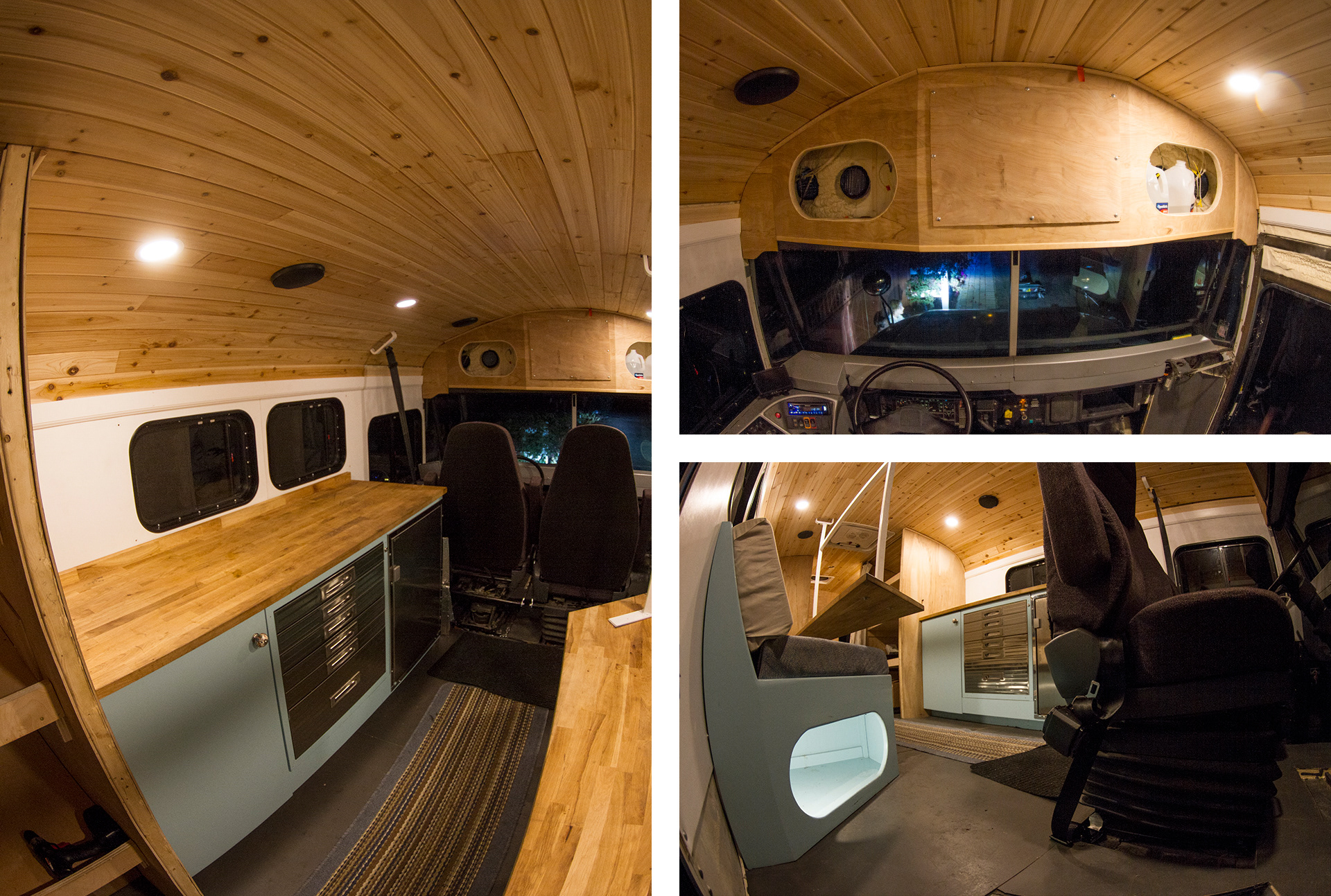
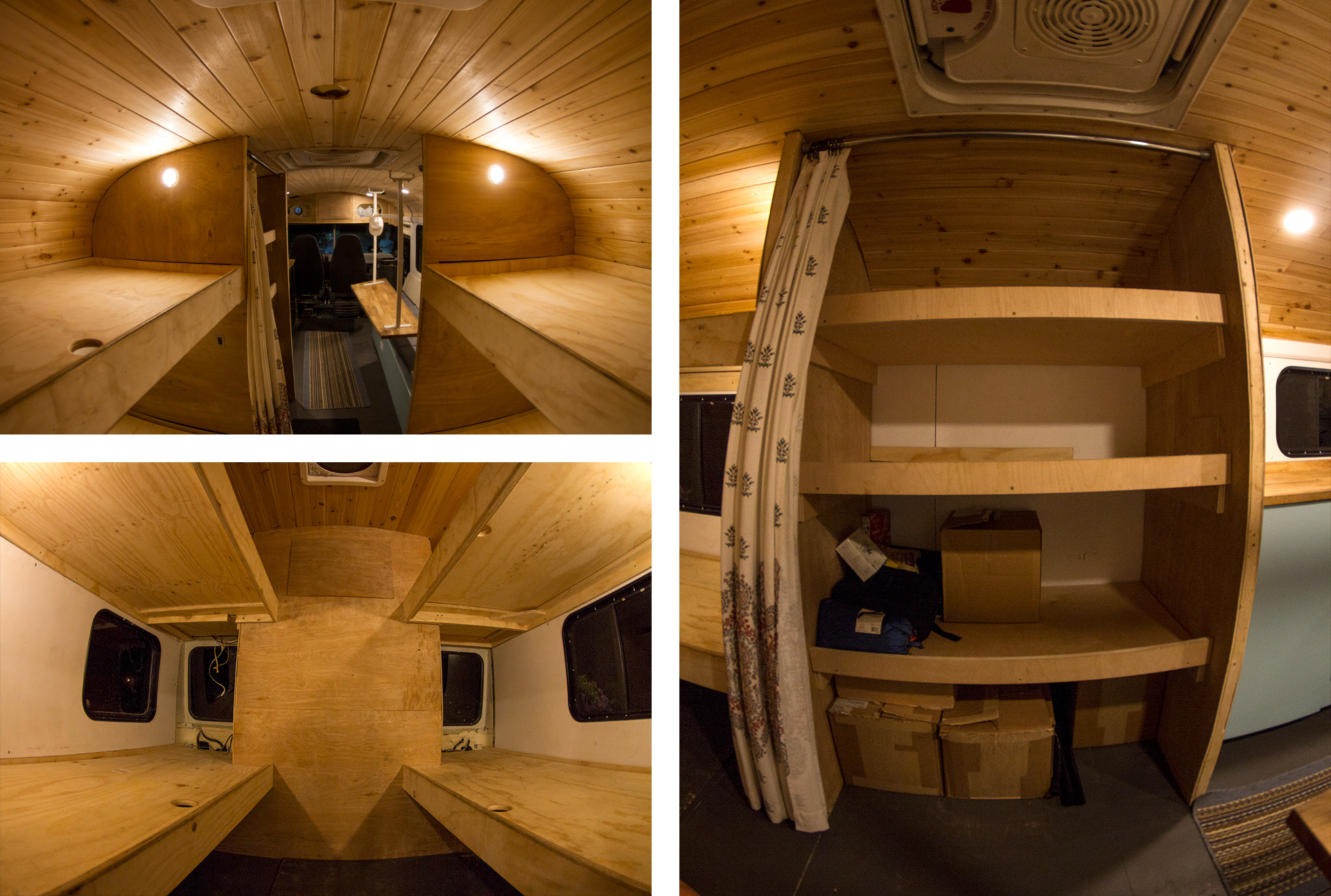
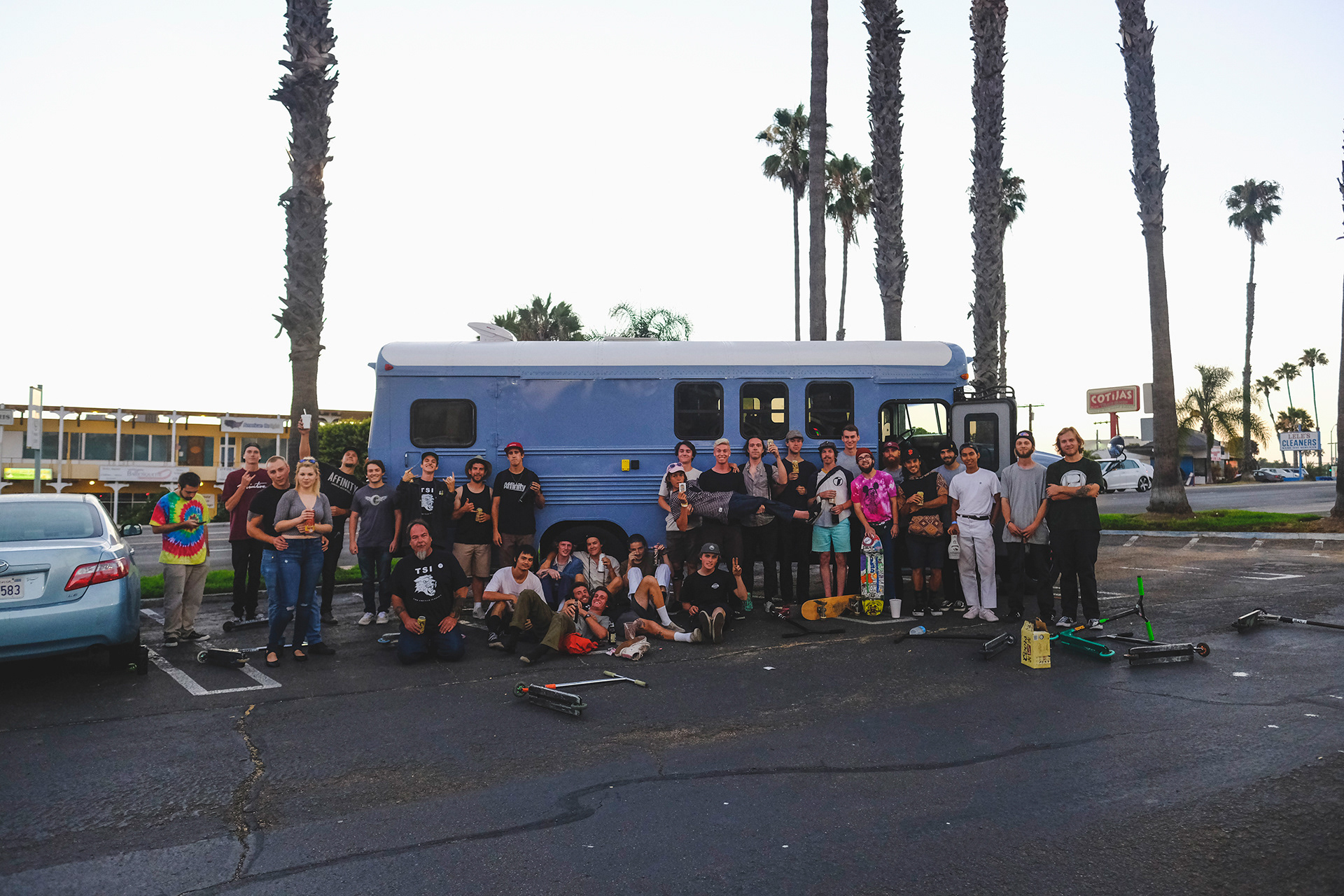
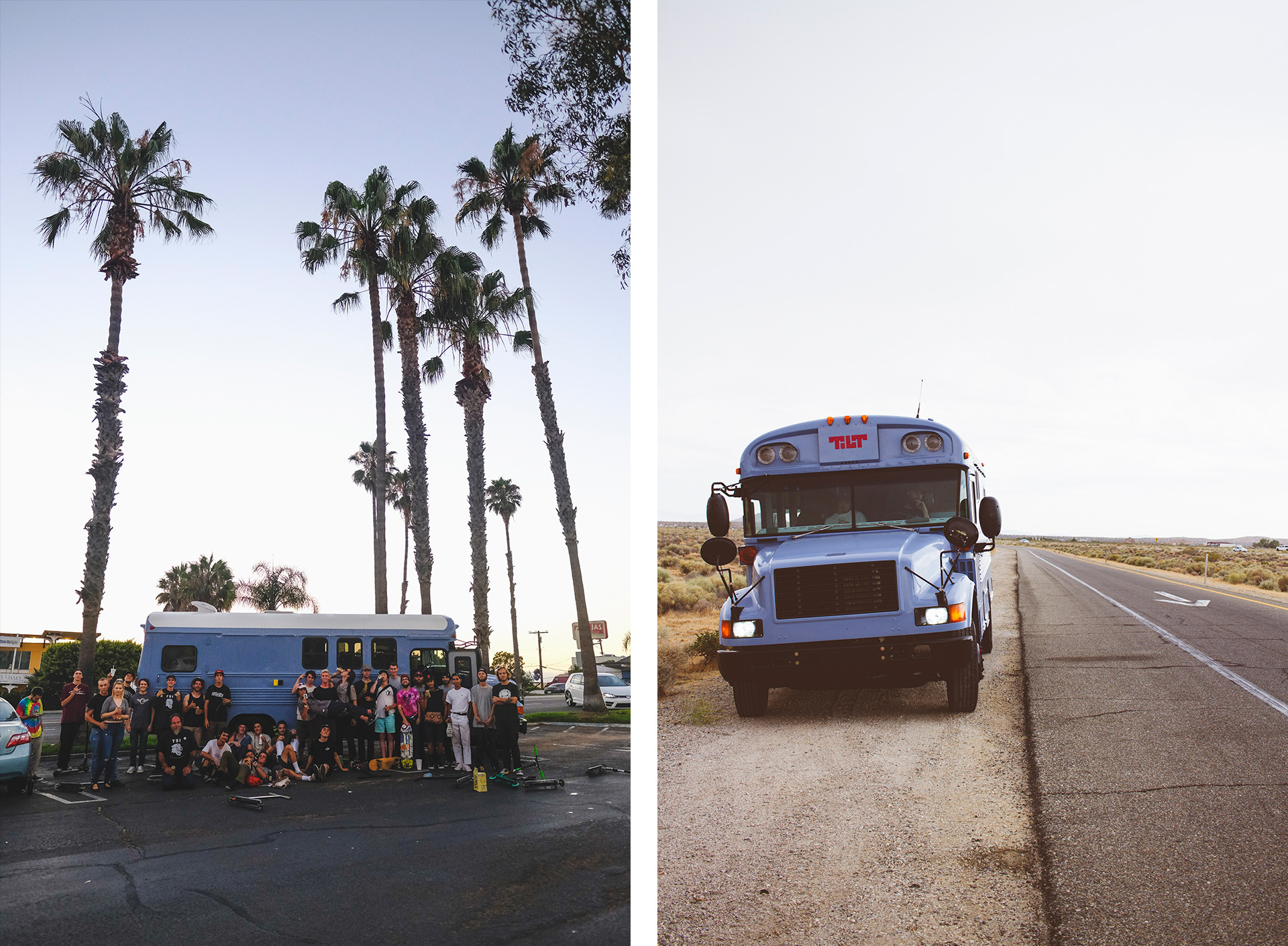
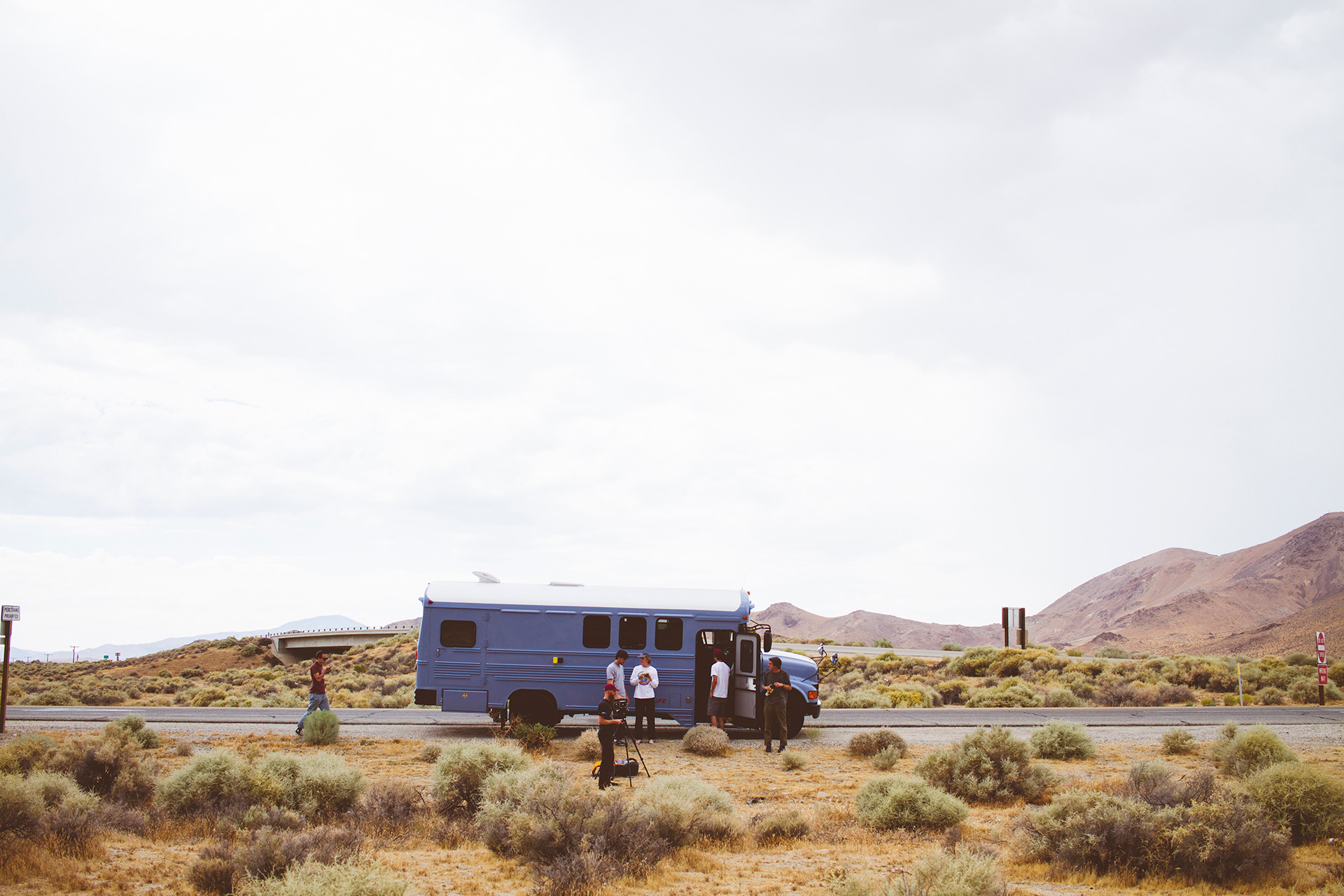
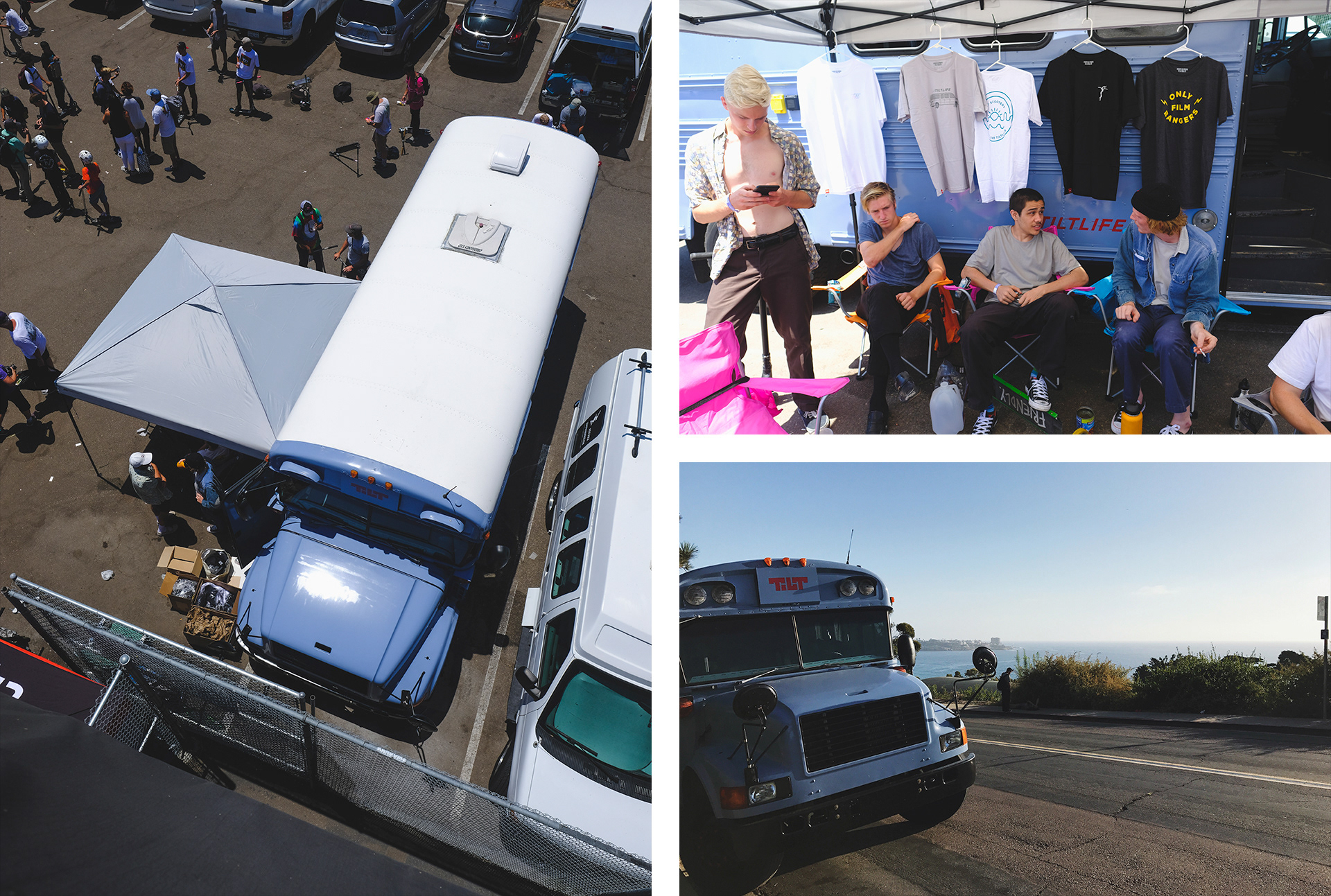
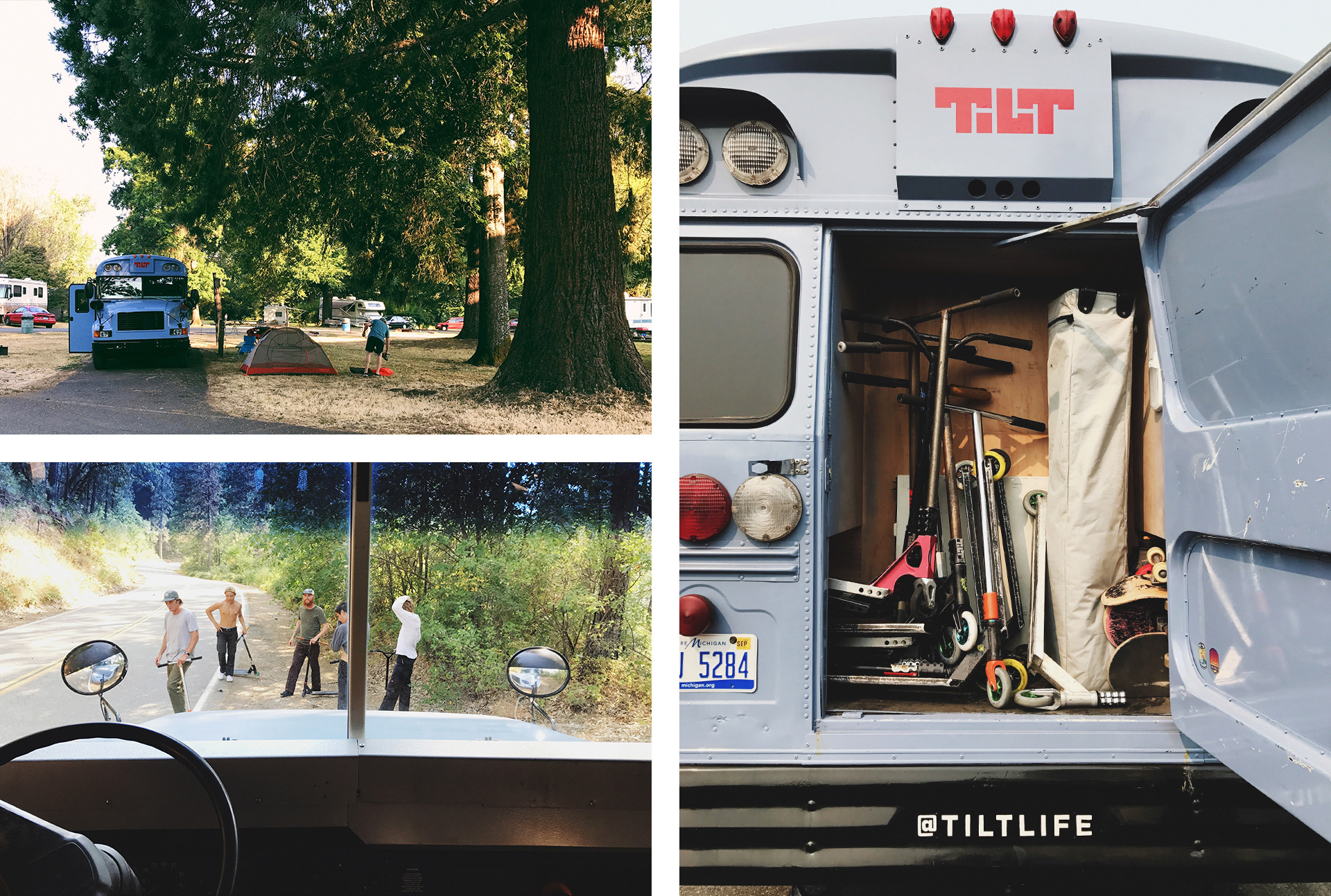
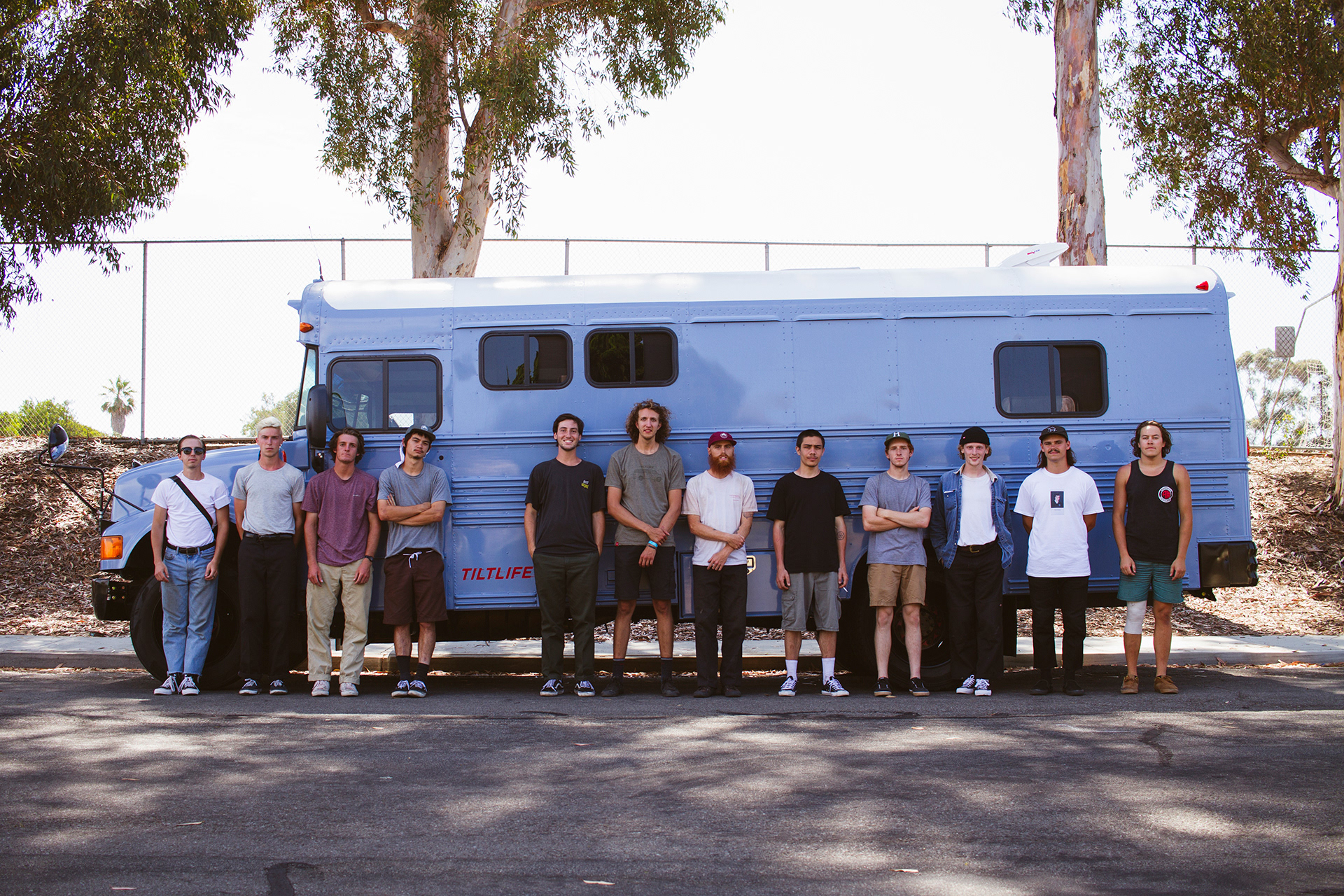
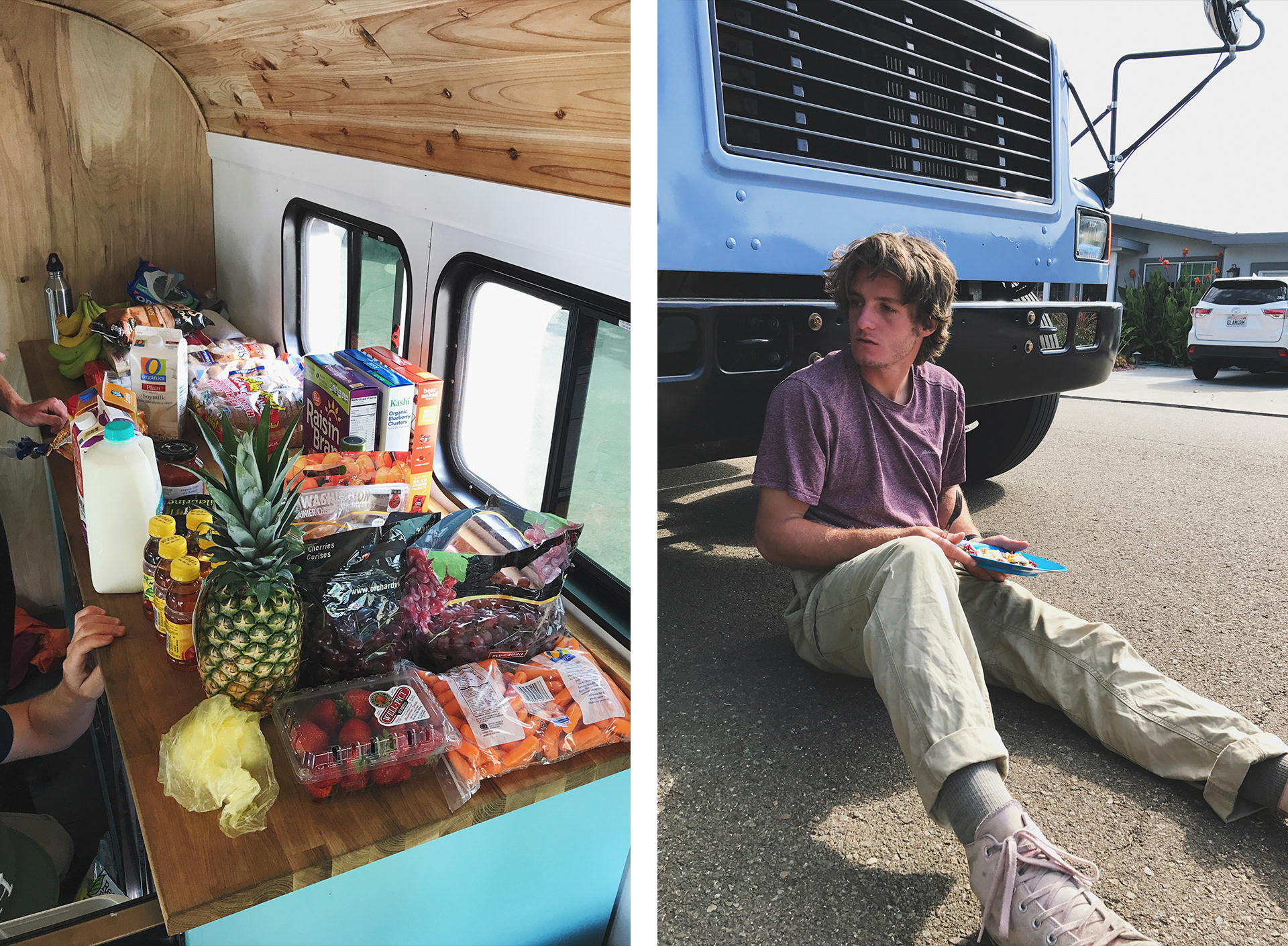
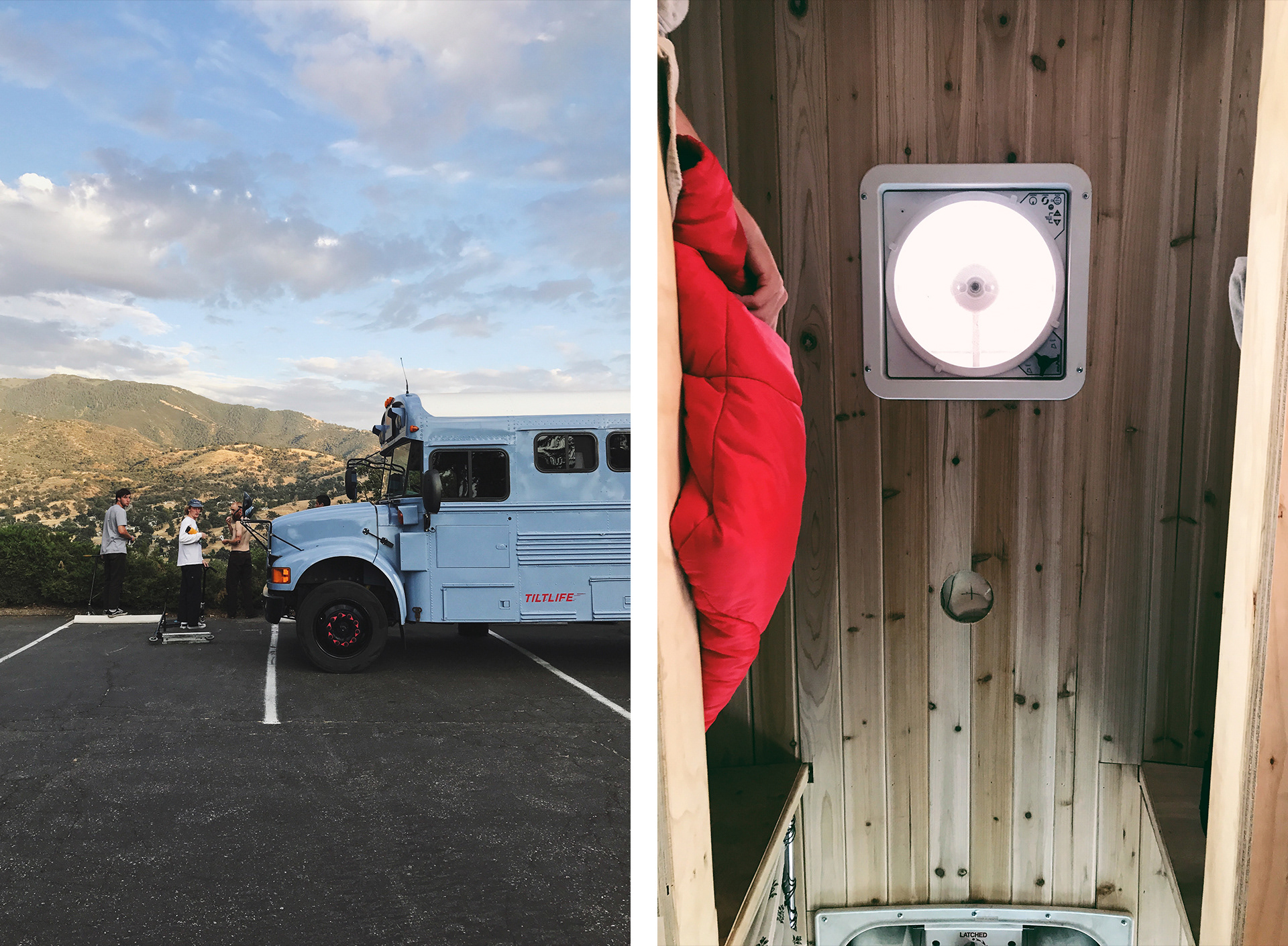
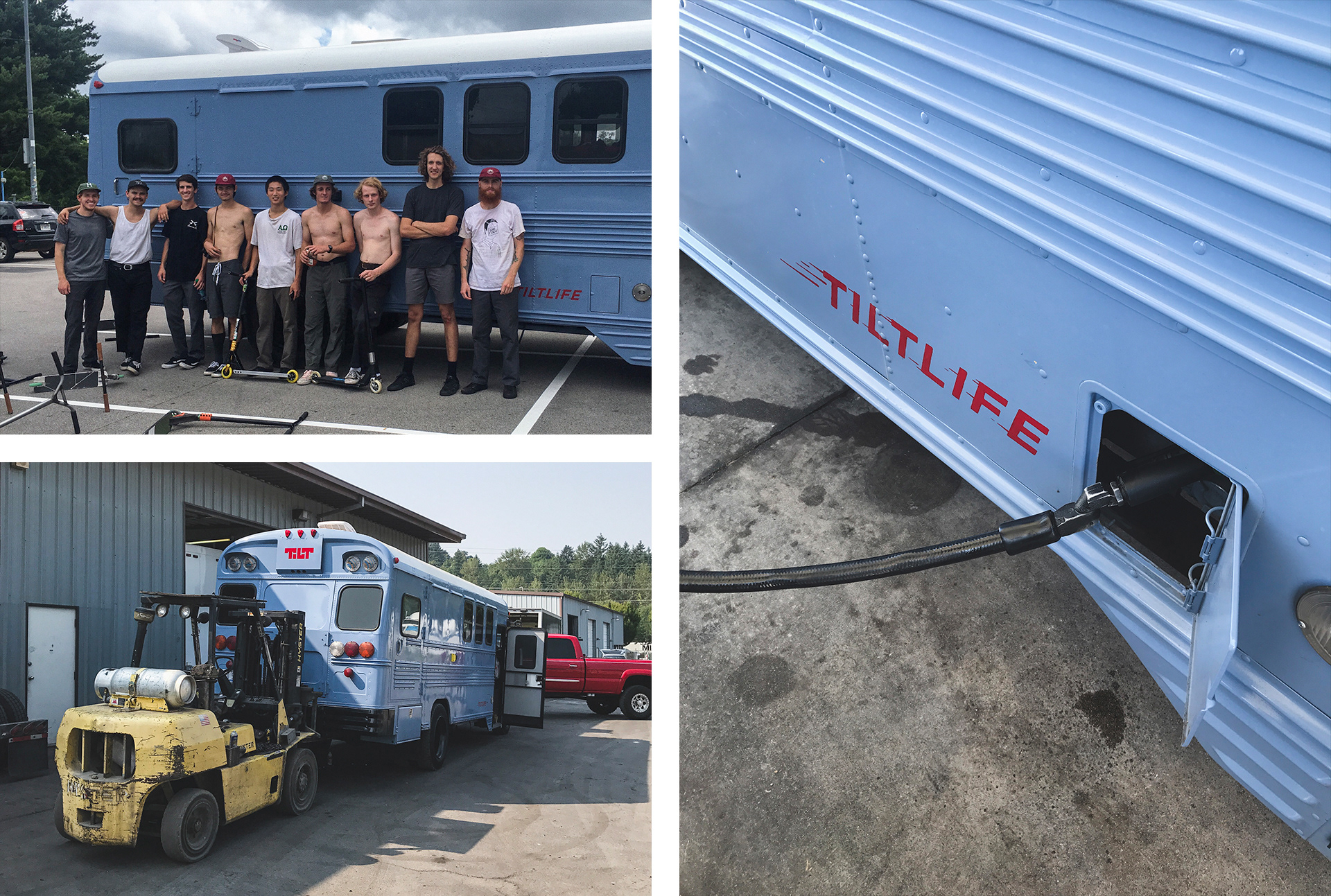
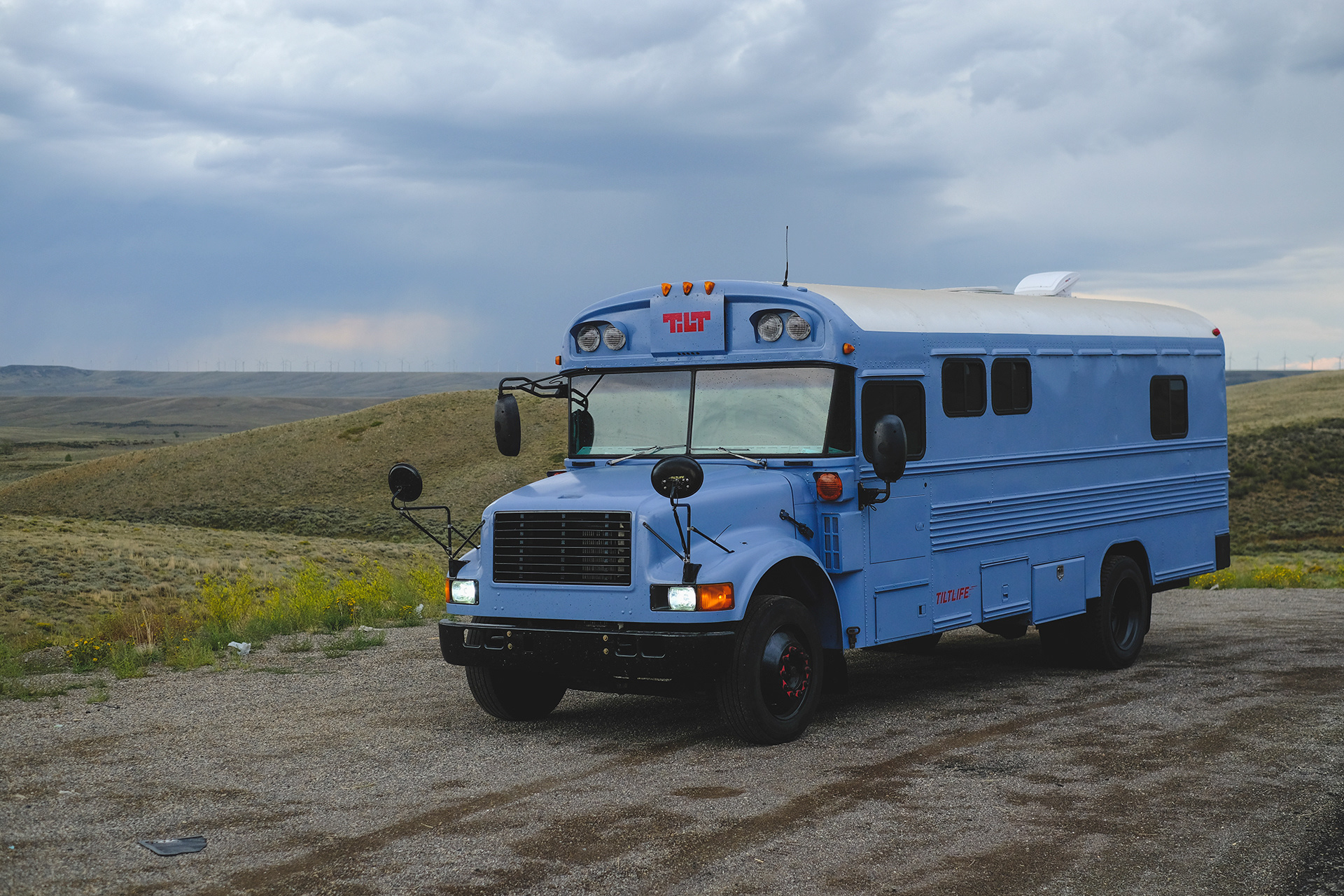
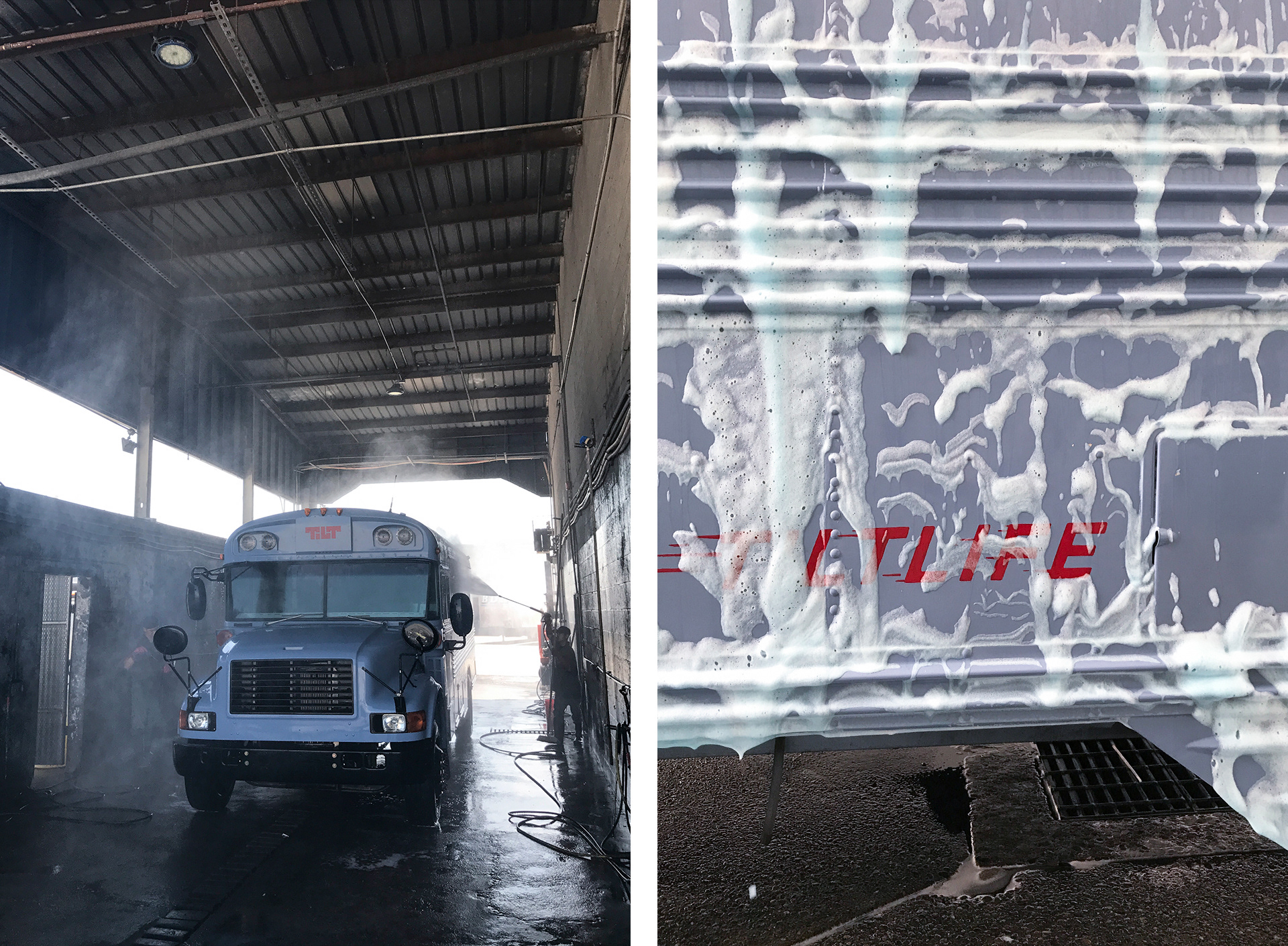
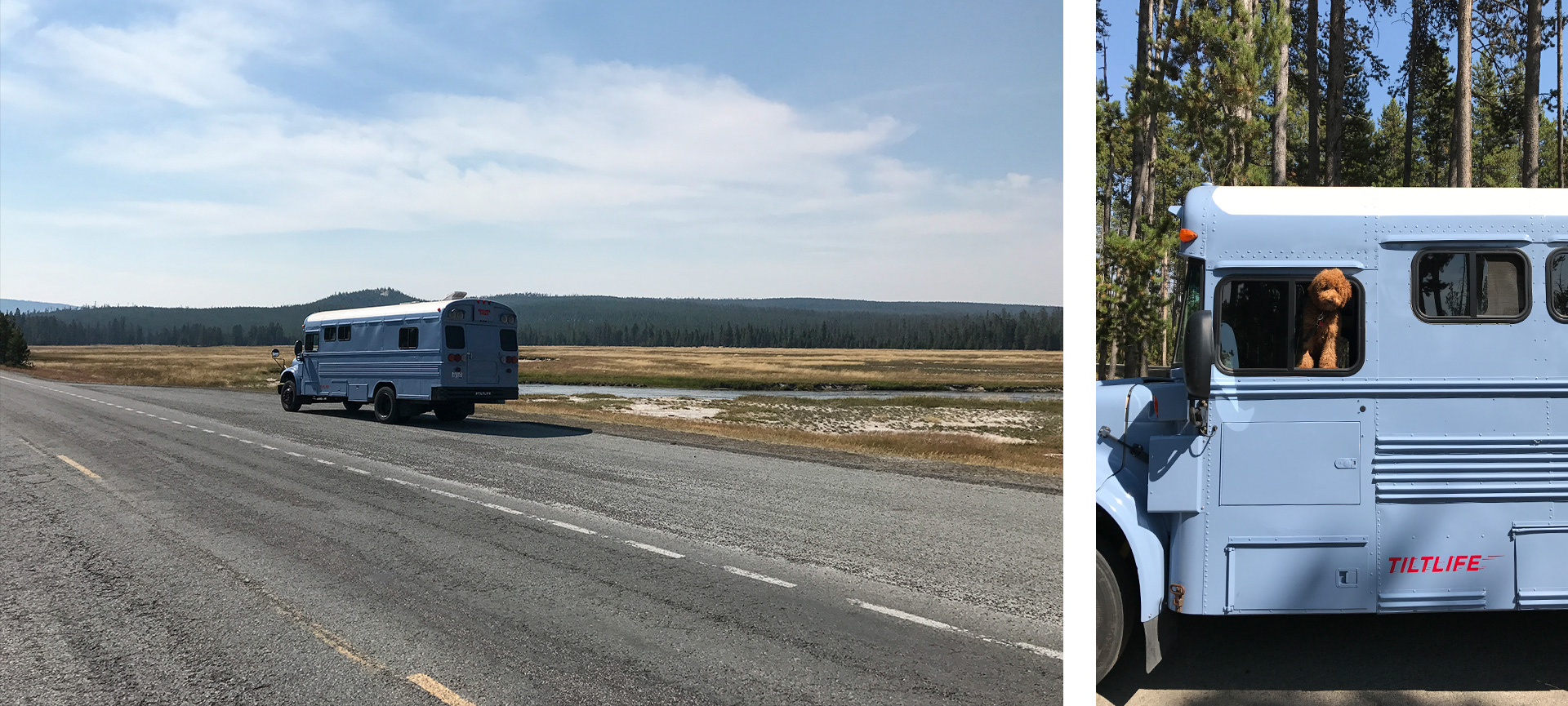
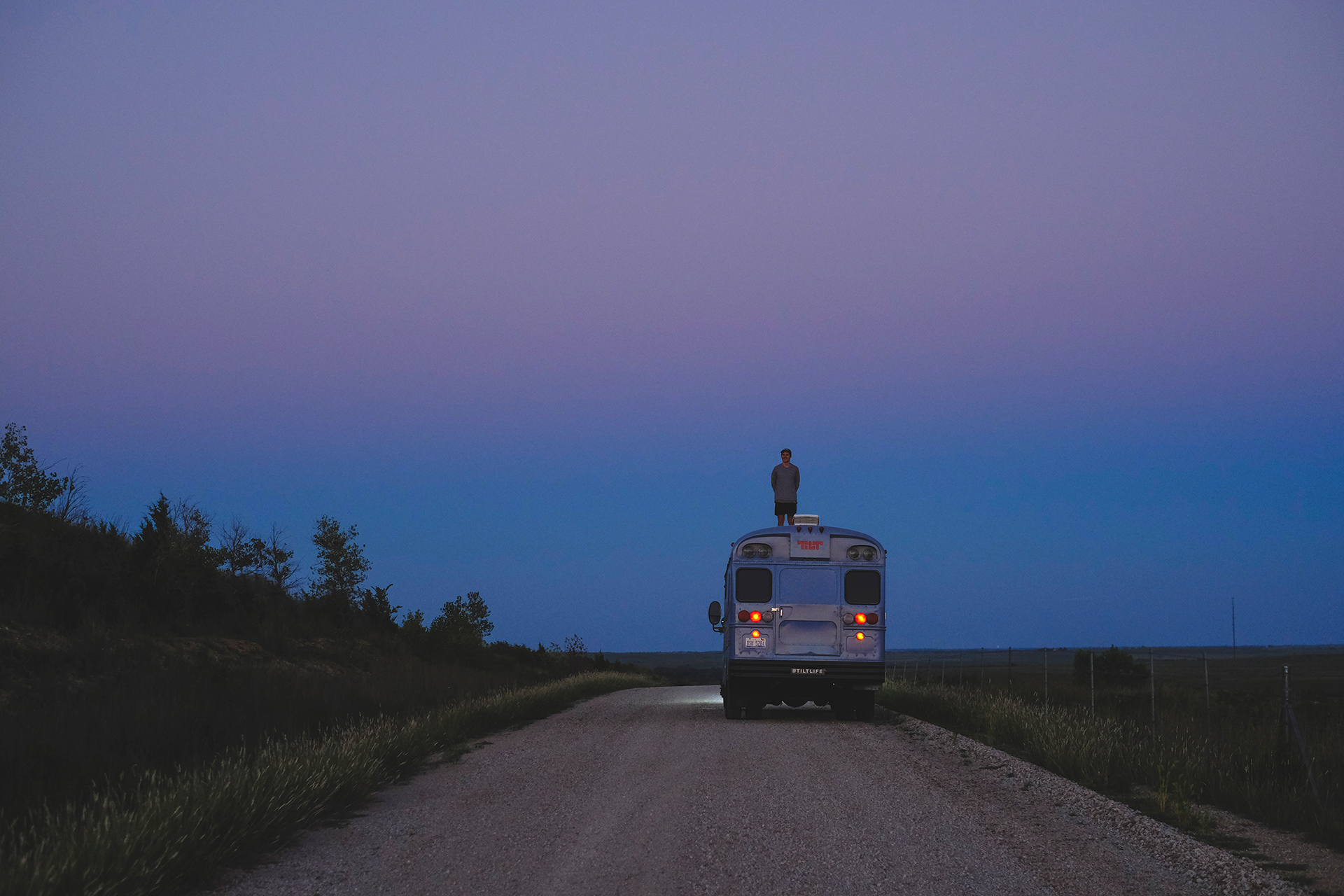
During the build, everyone that worked on it, their regular lives didn’t matter. It was strictly work, sleep, eat and shower. Lots of times we would forget to do the last three so the people that care about us were forced to make sure we were taken care of. We would like to thank you all for putting up with us and helping keep us alive during this chaos. Michelle Snoek, Ray Snoek, Jessica Nail, Heidi Snoek, Dillion Vrosh, Jason Vrosh, Christine Martin, Kelsie Garrett, and Amanda Astroth.