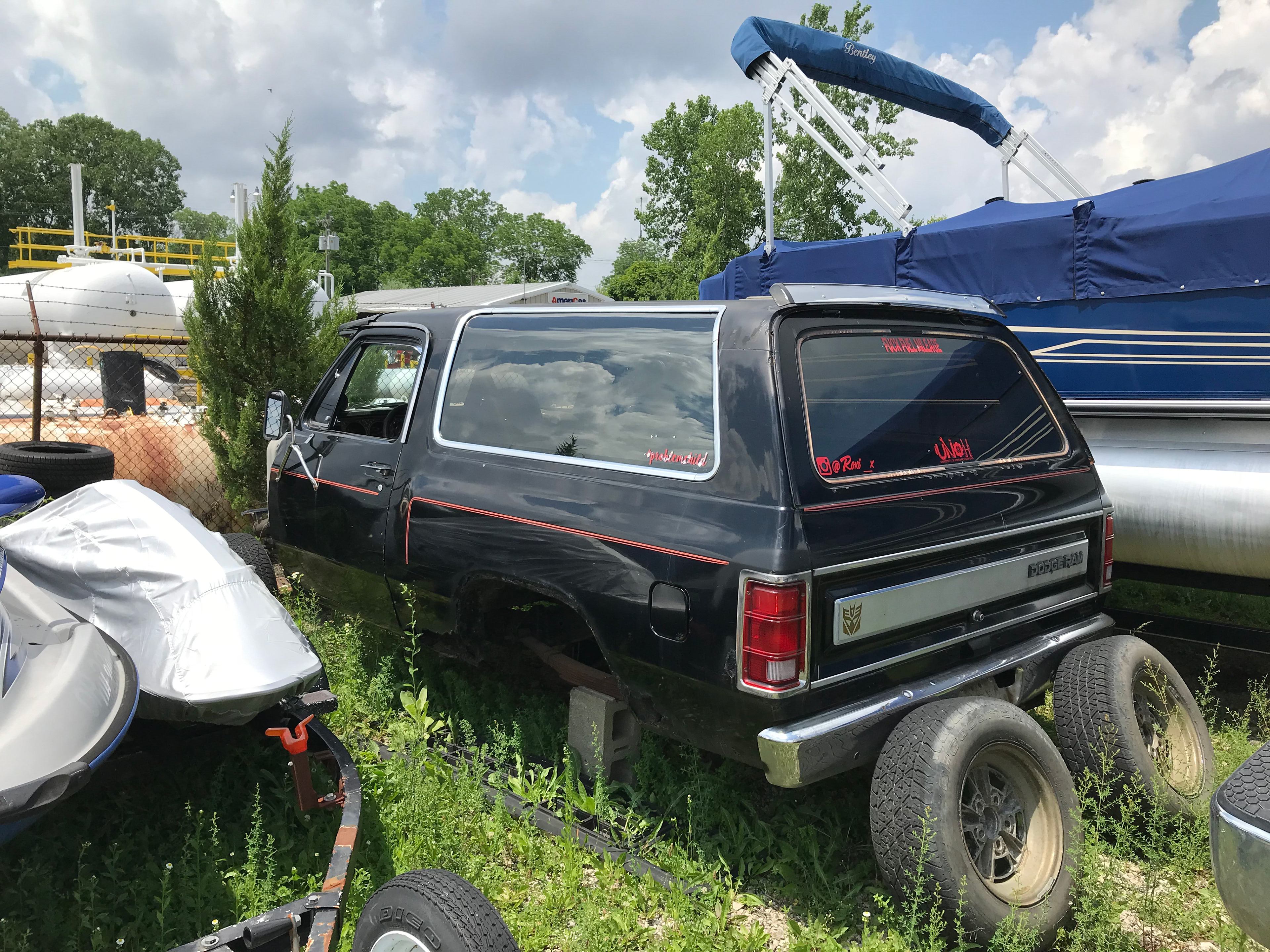
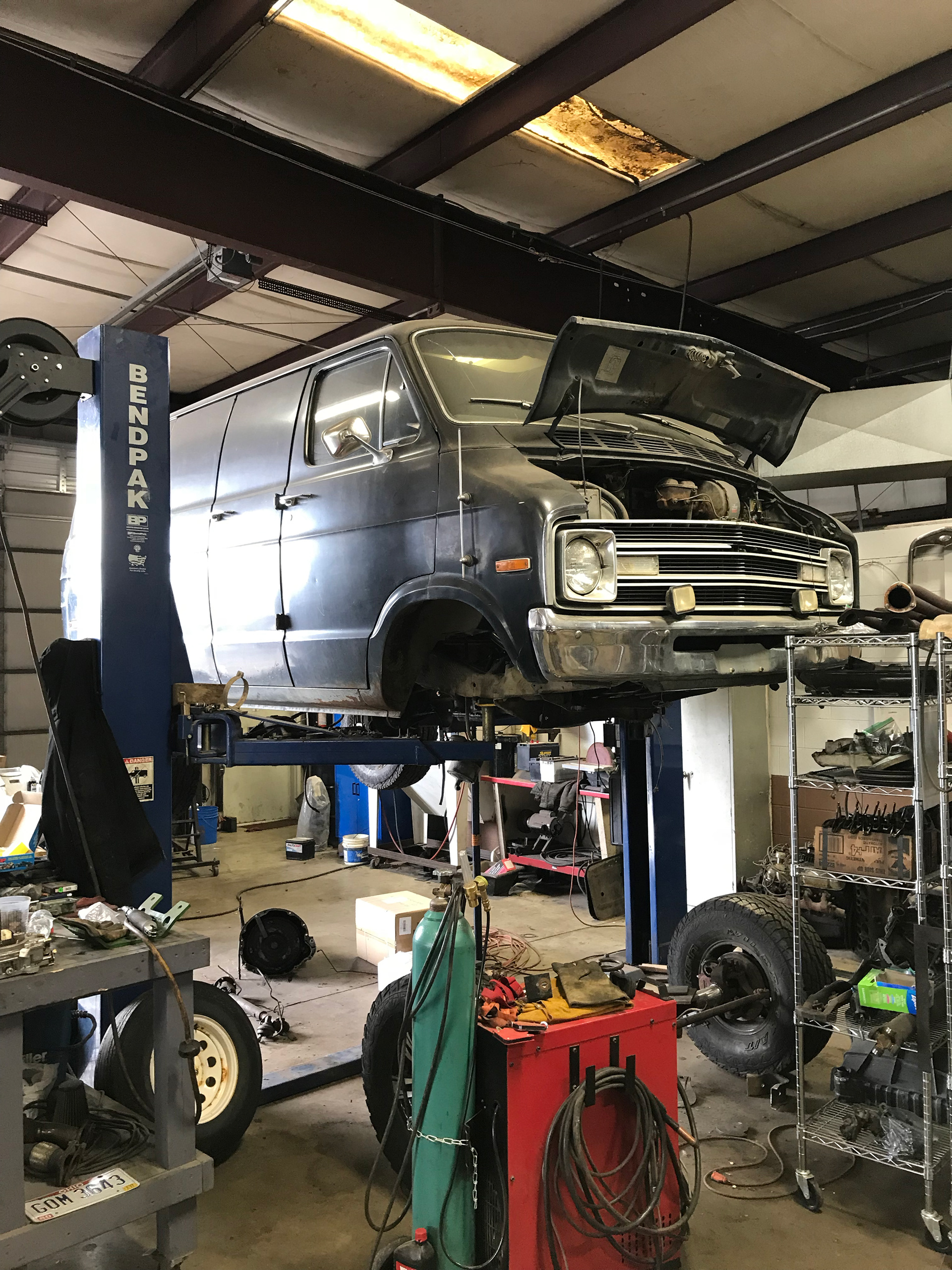
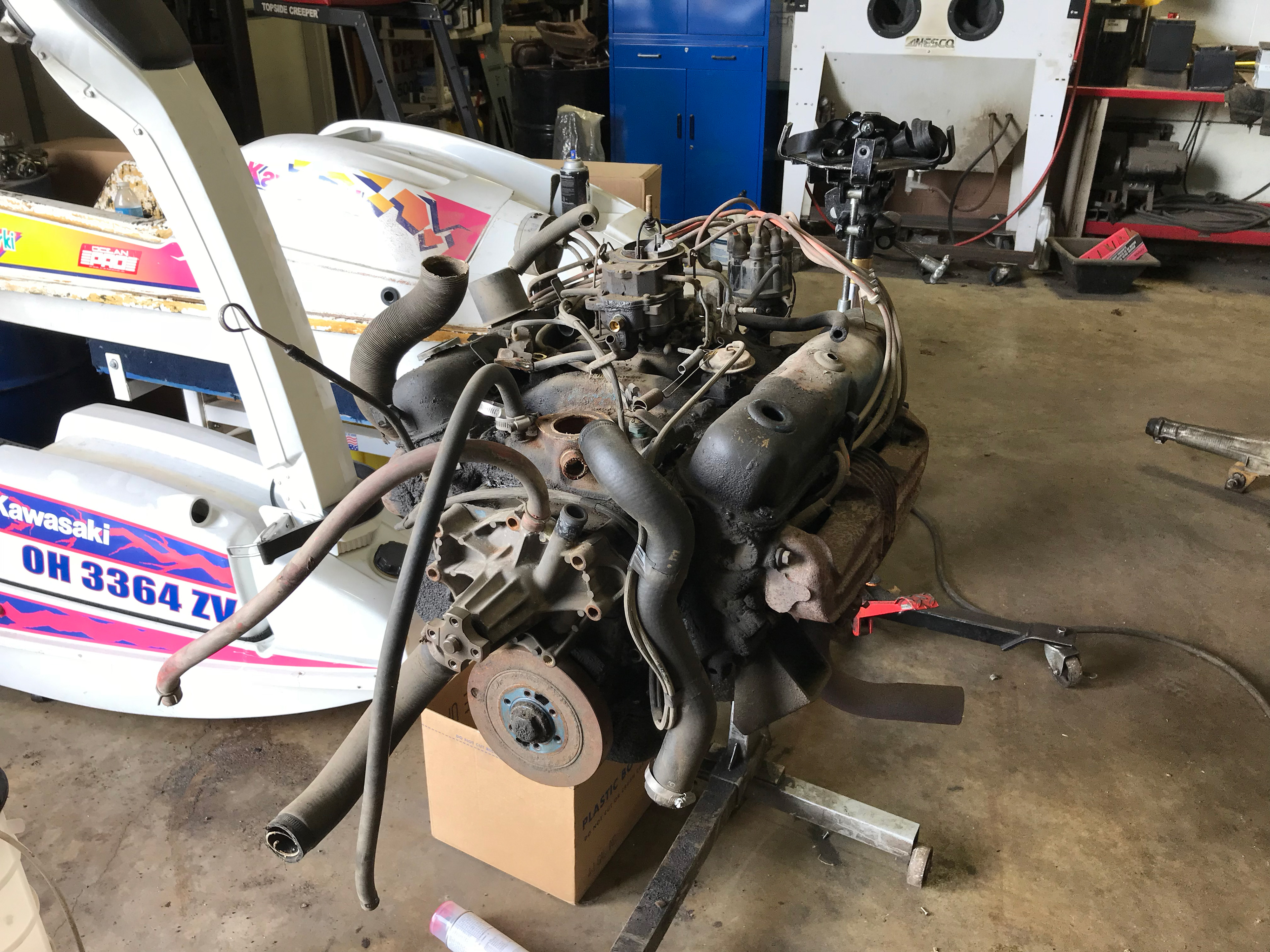
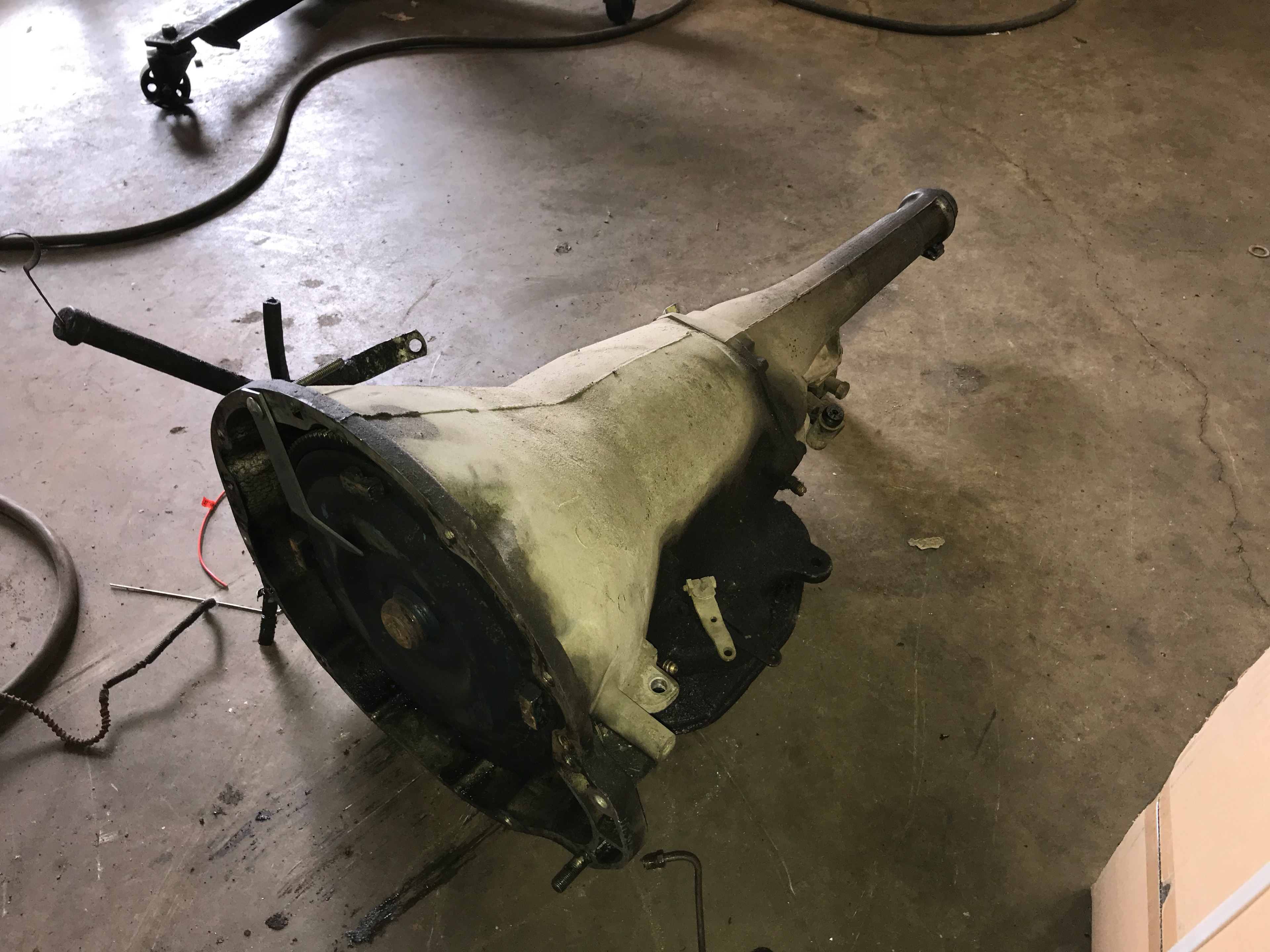
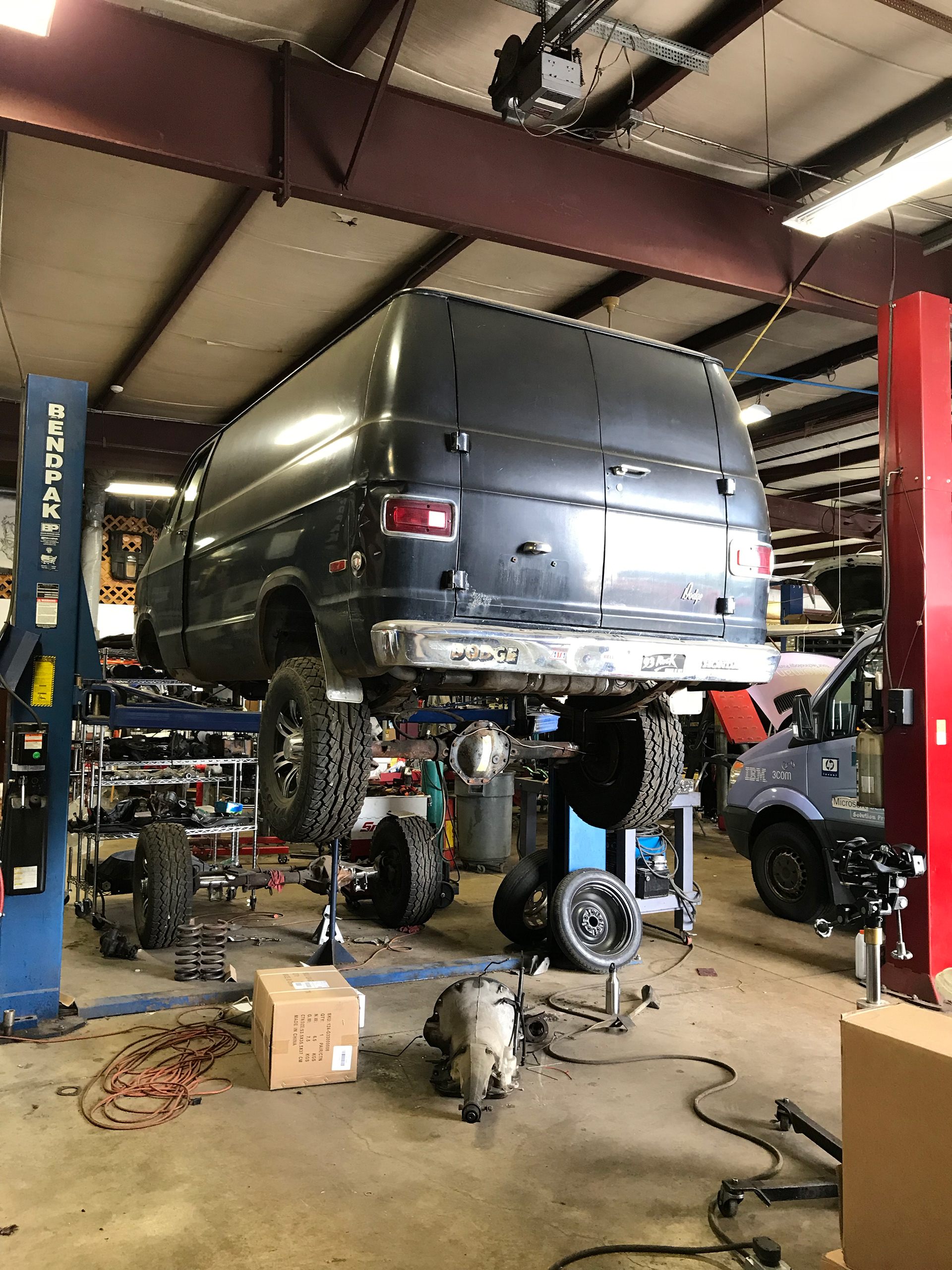

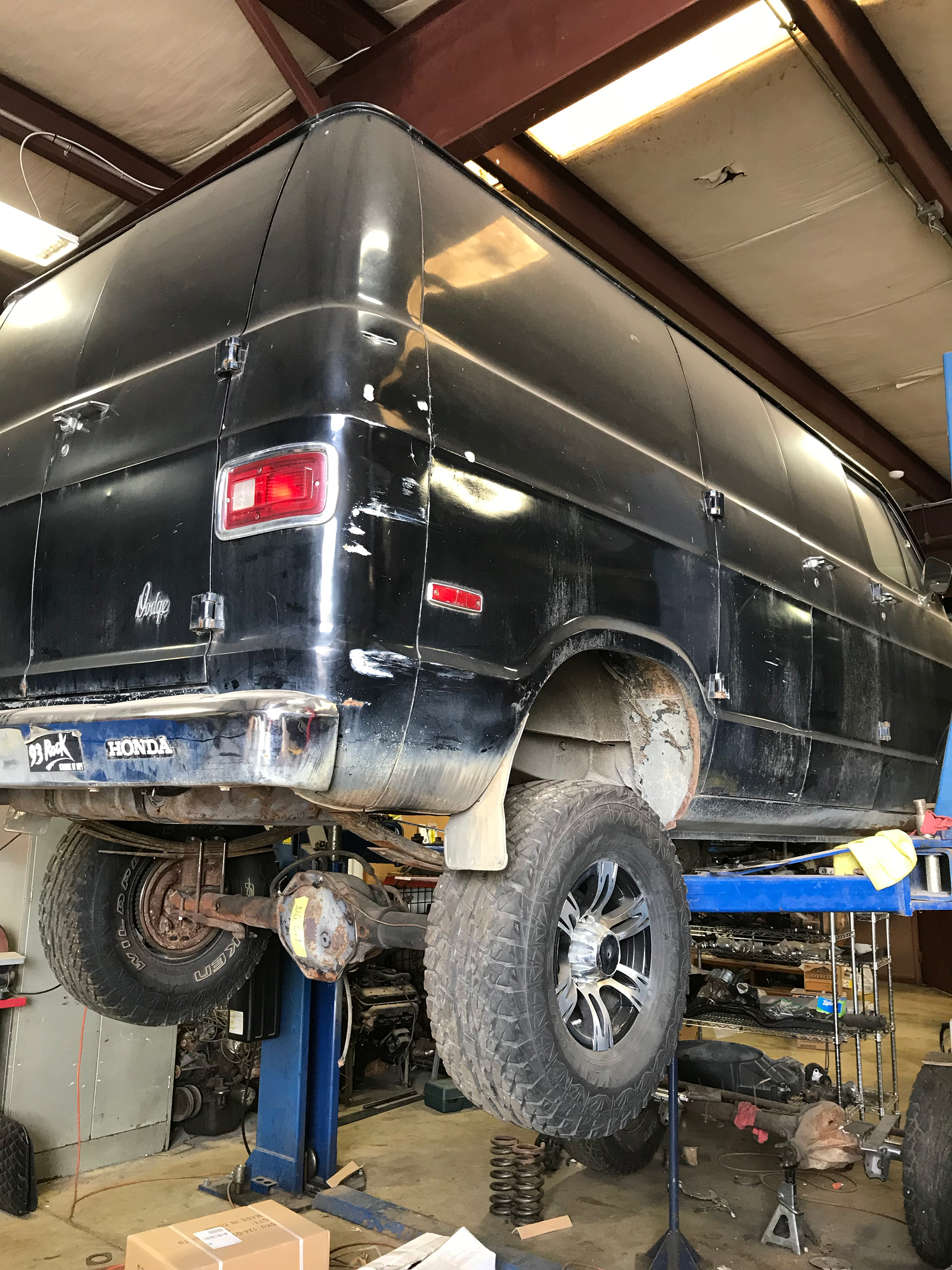
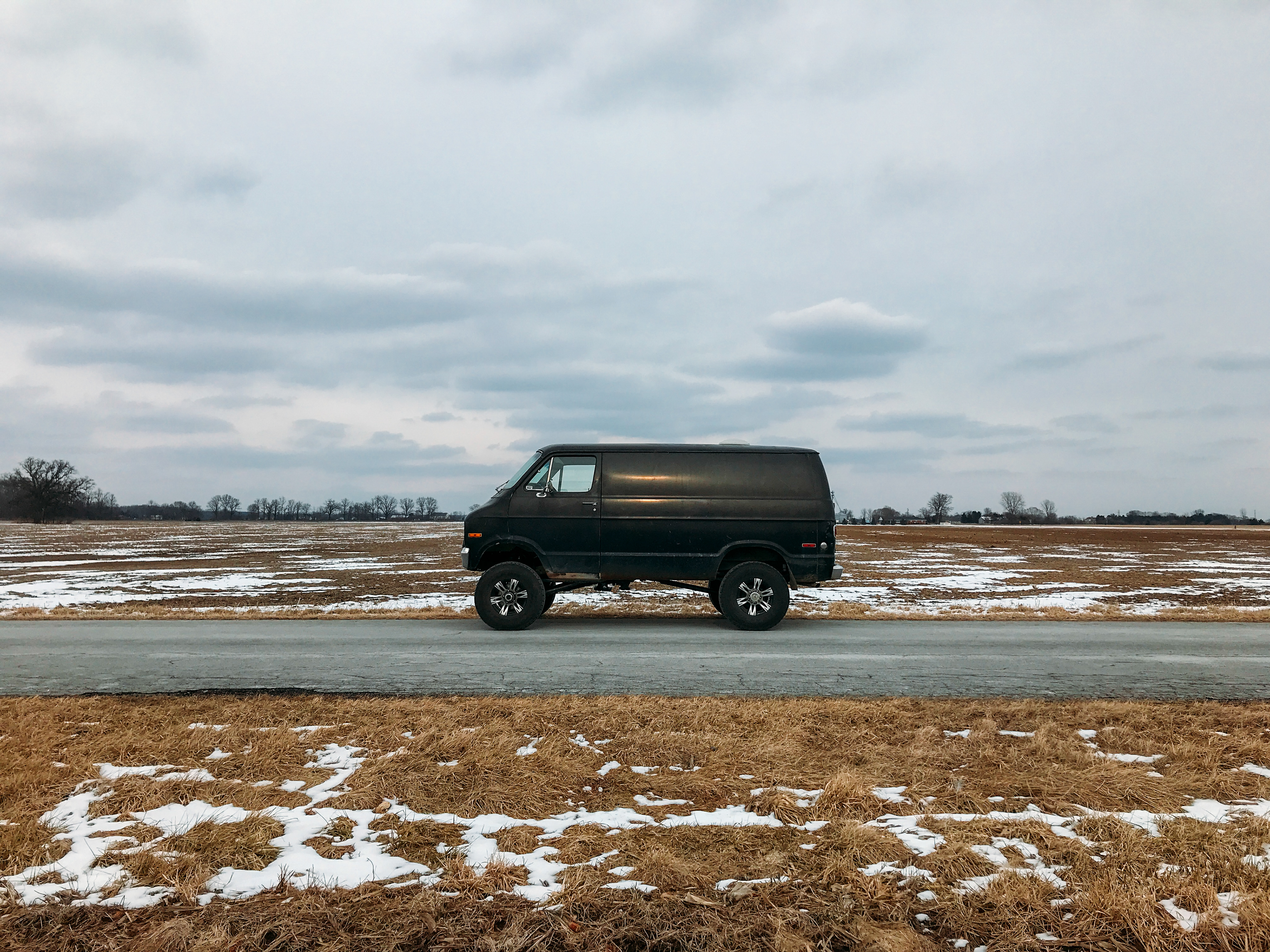
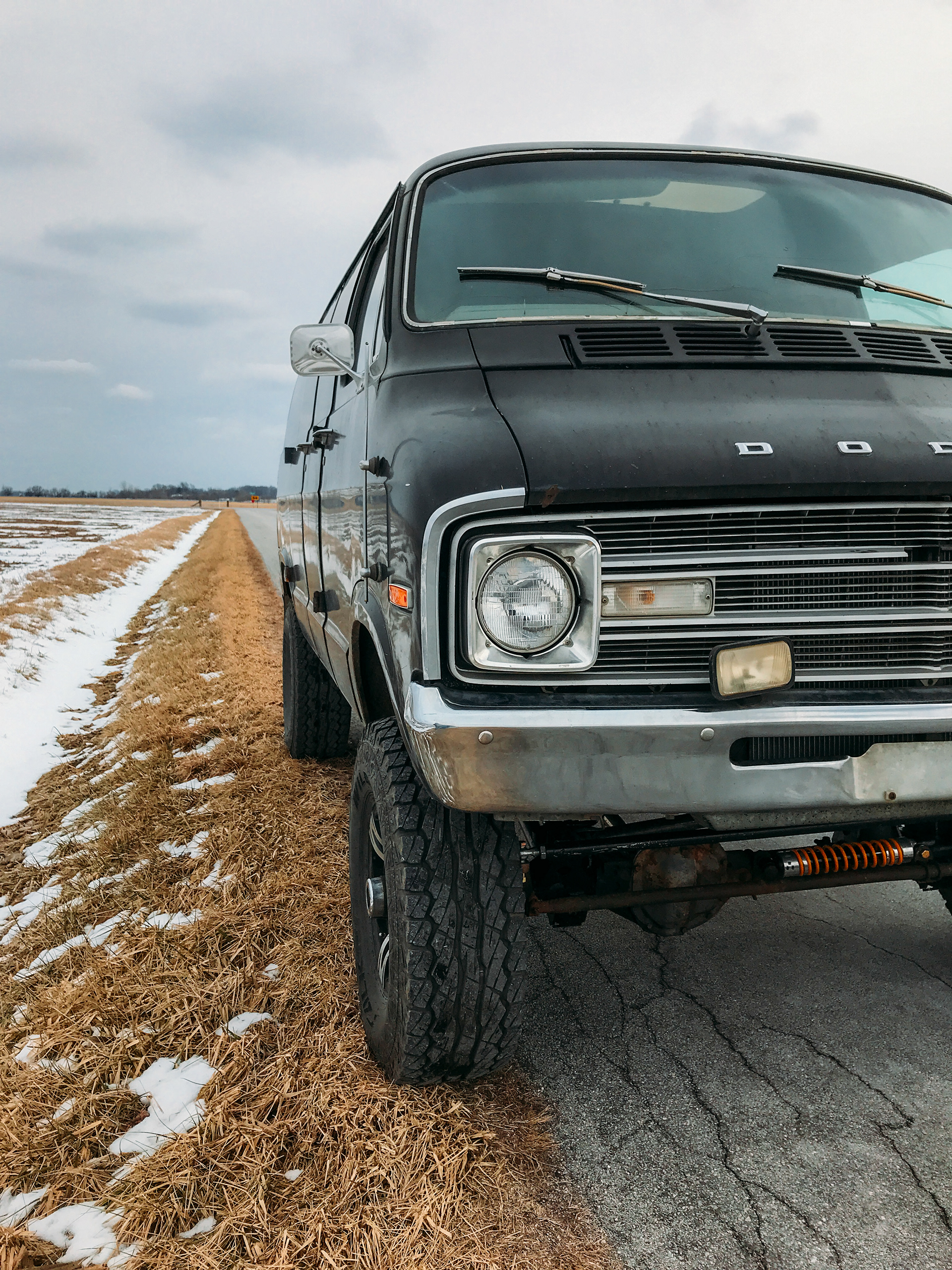
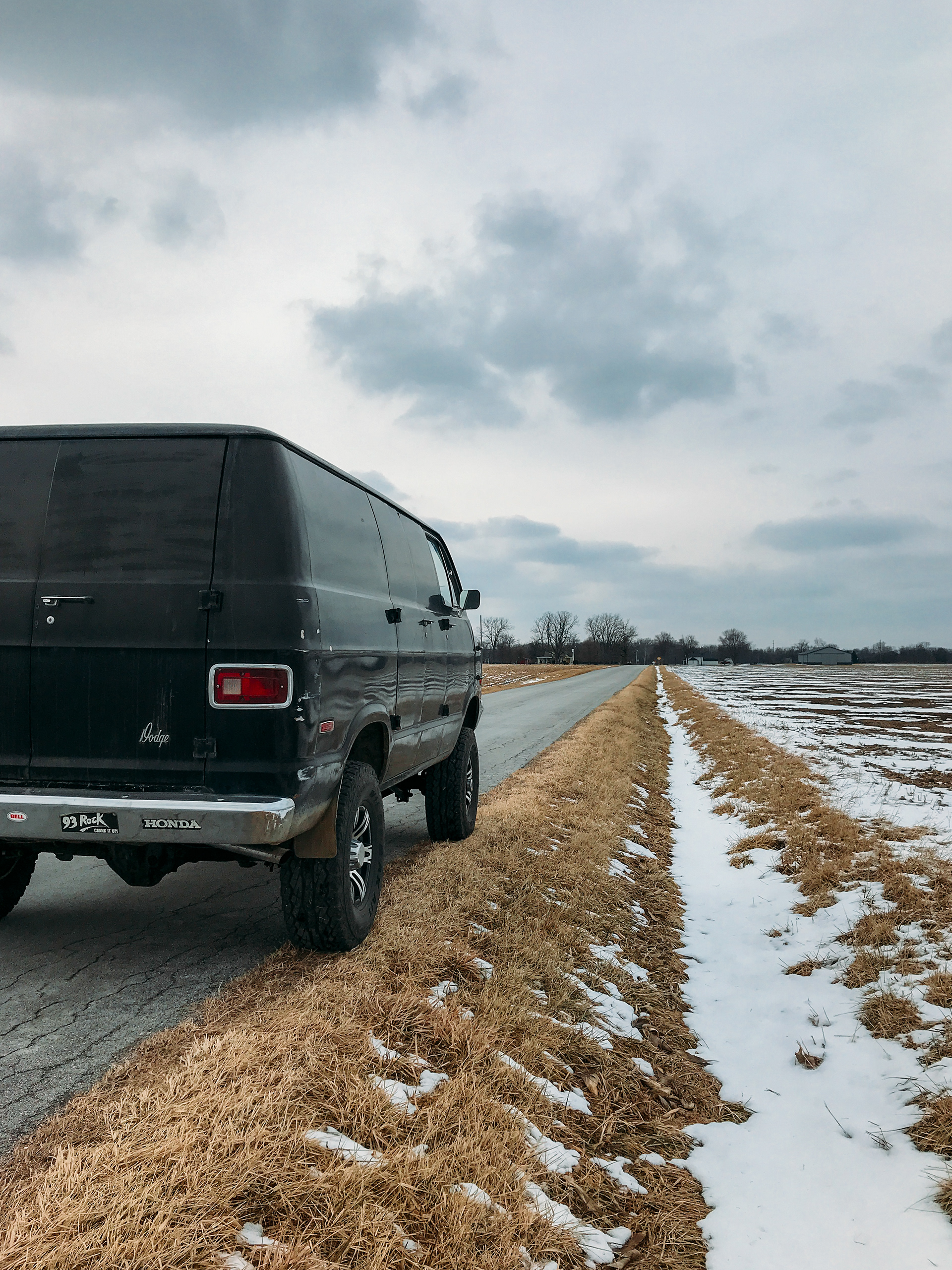
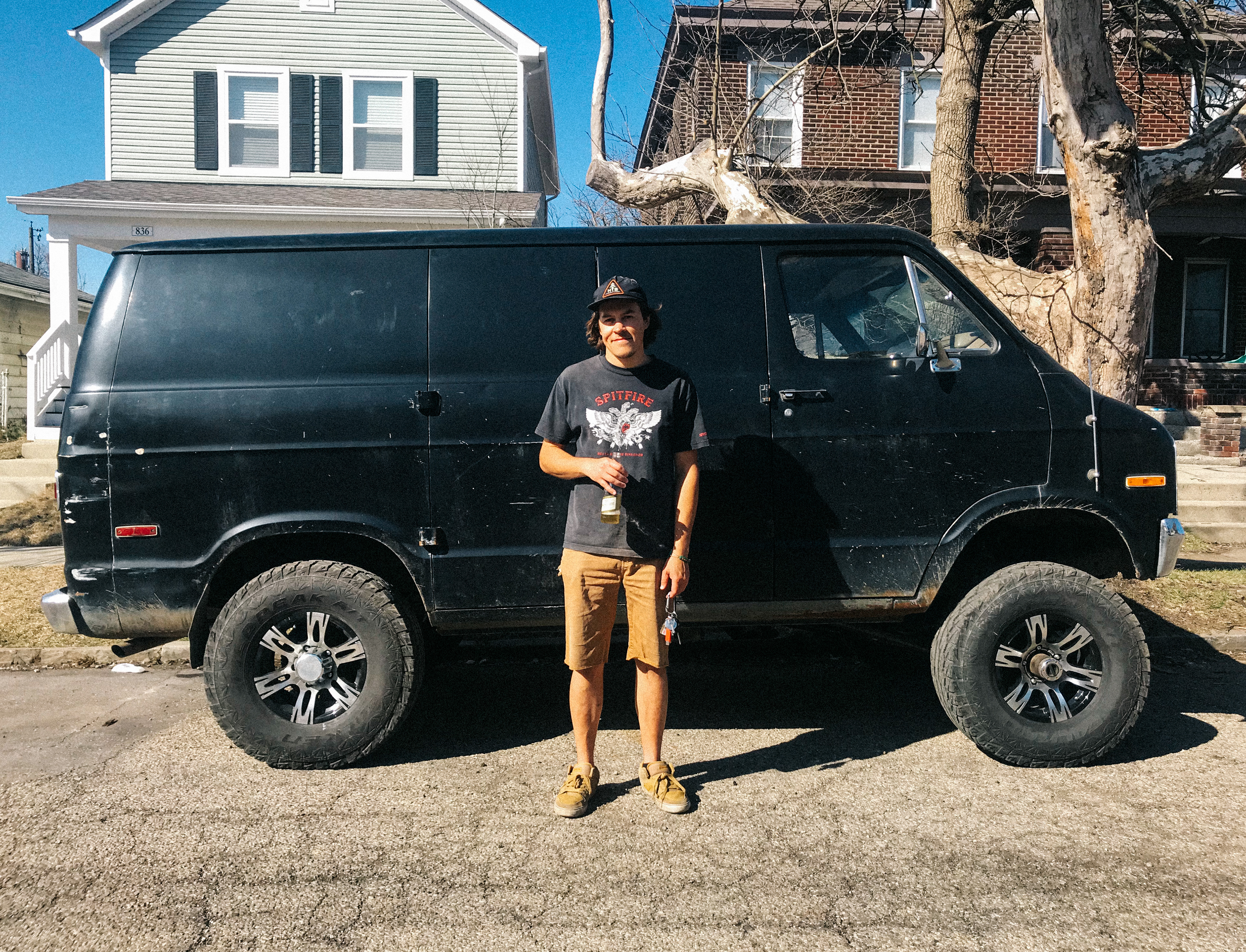
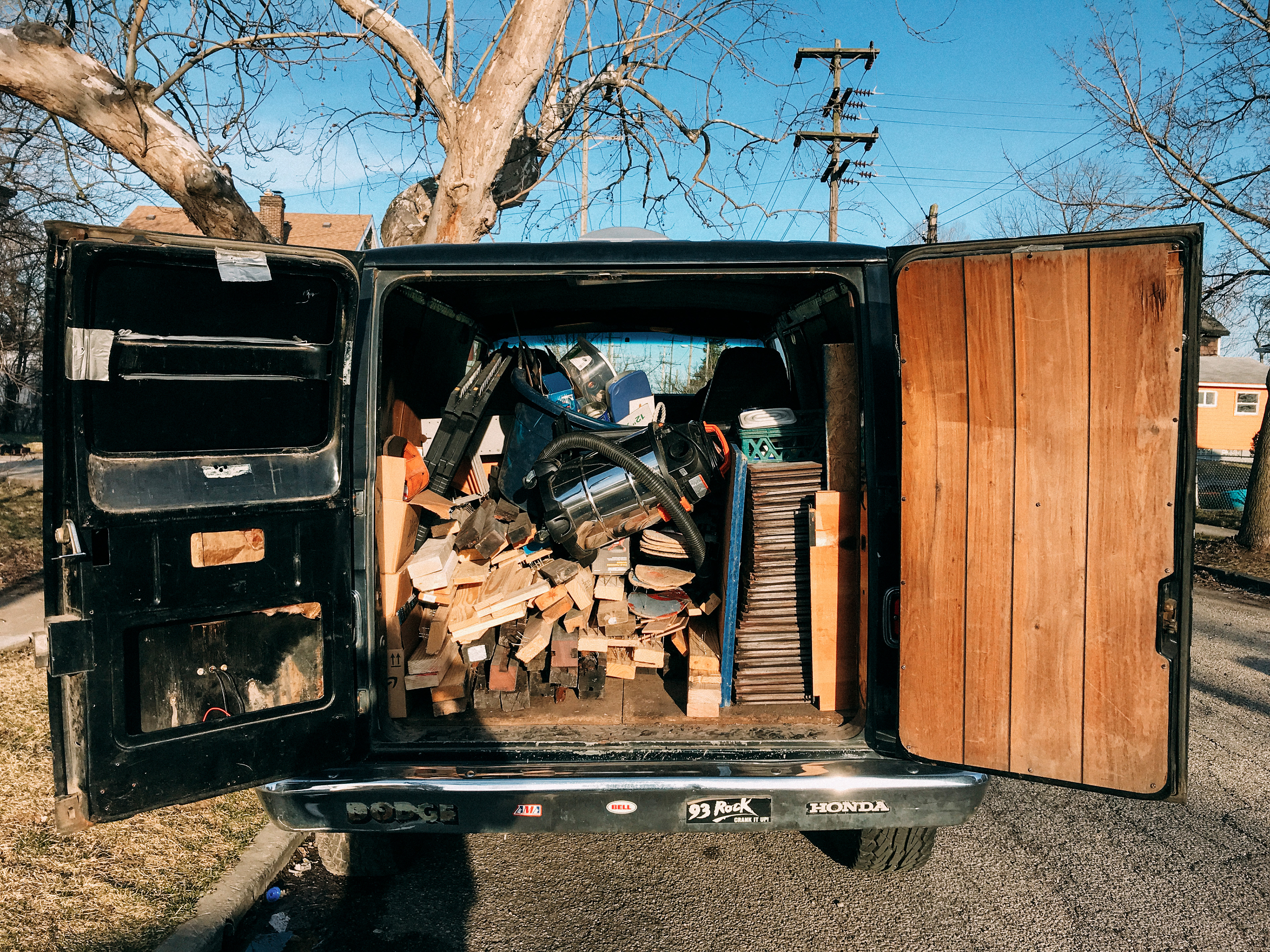
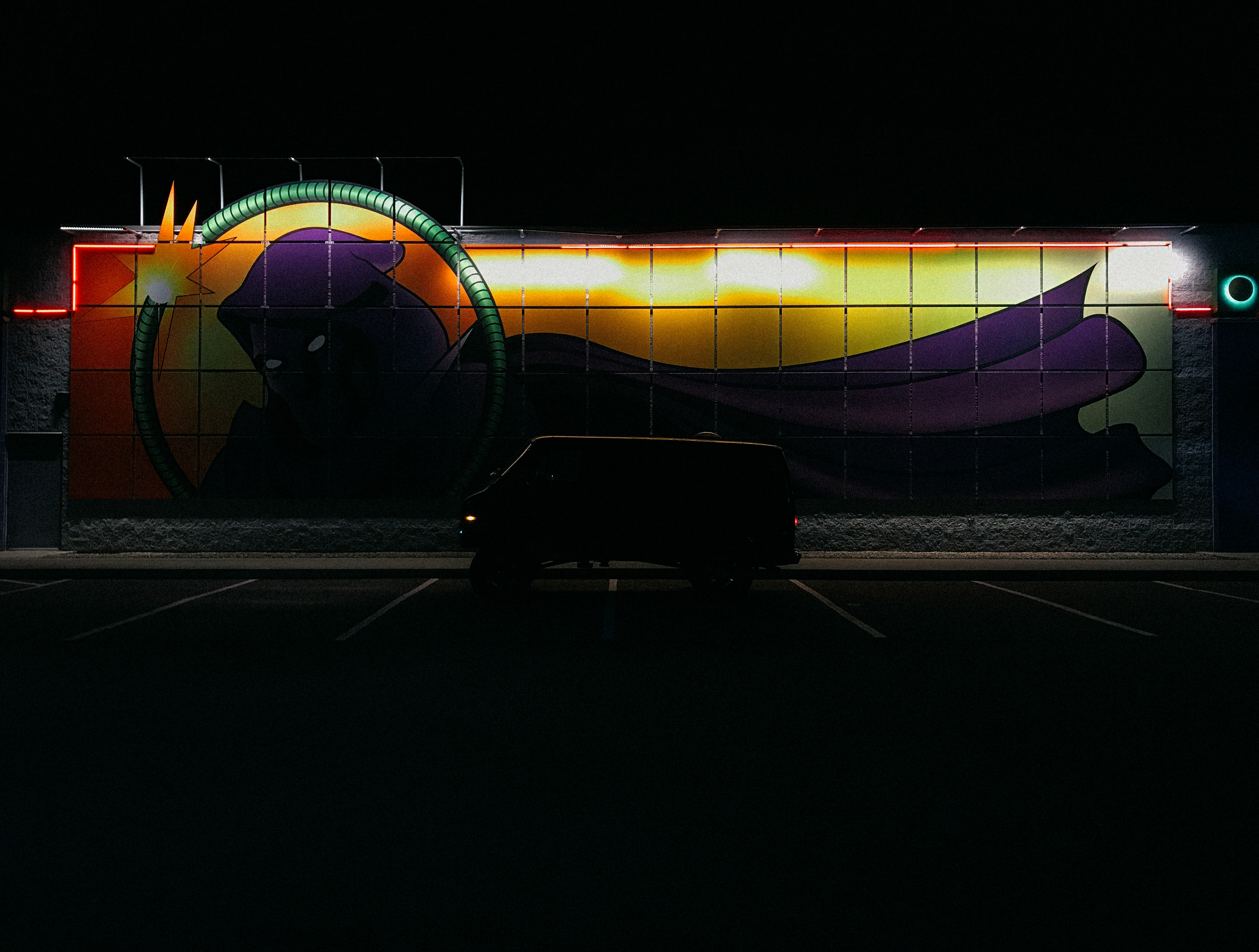
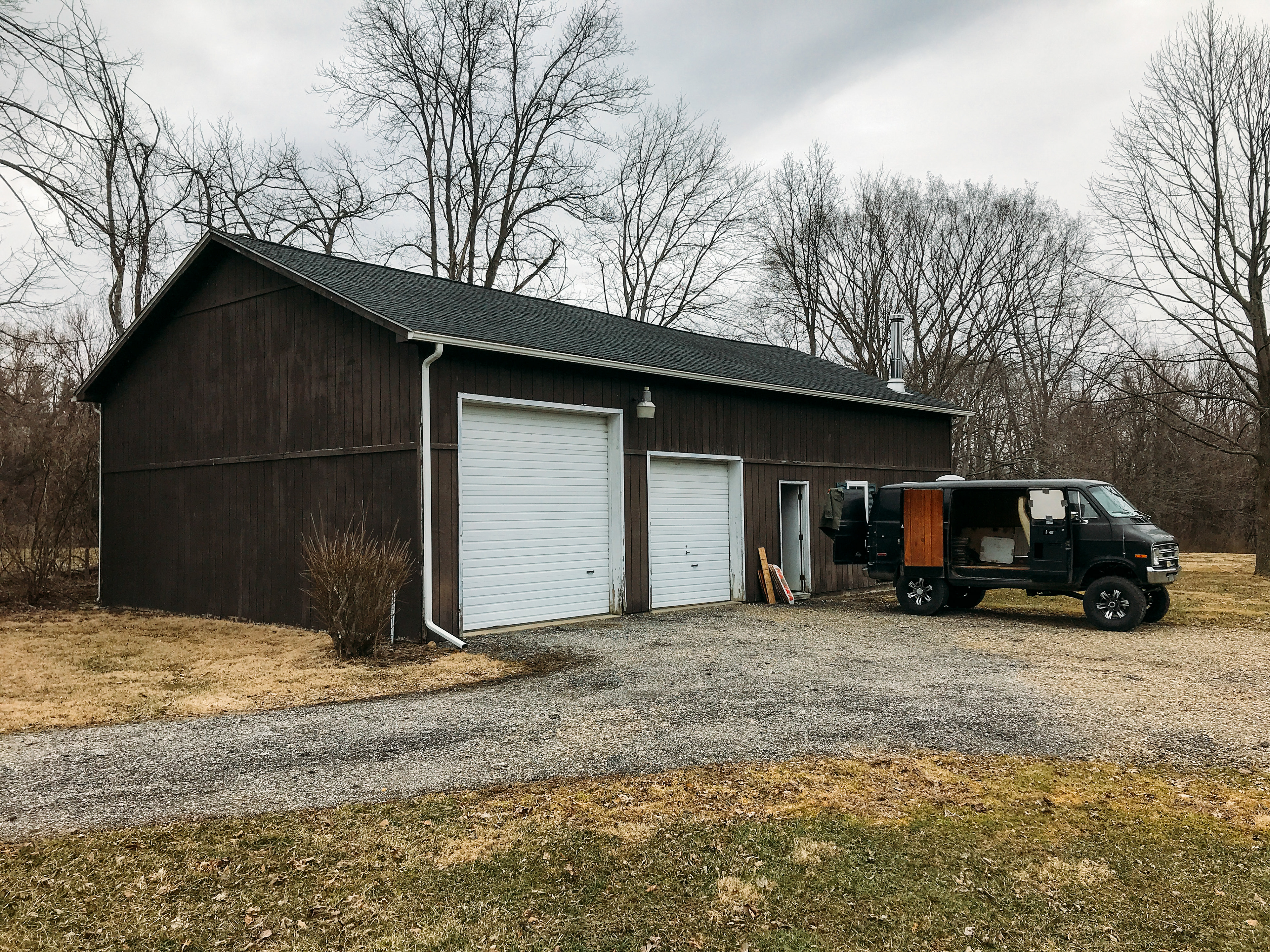
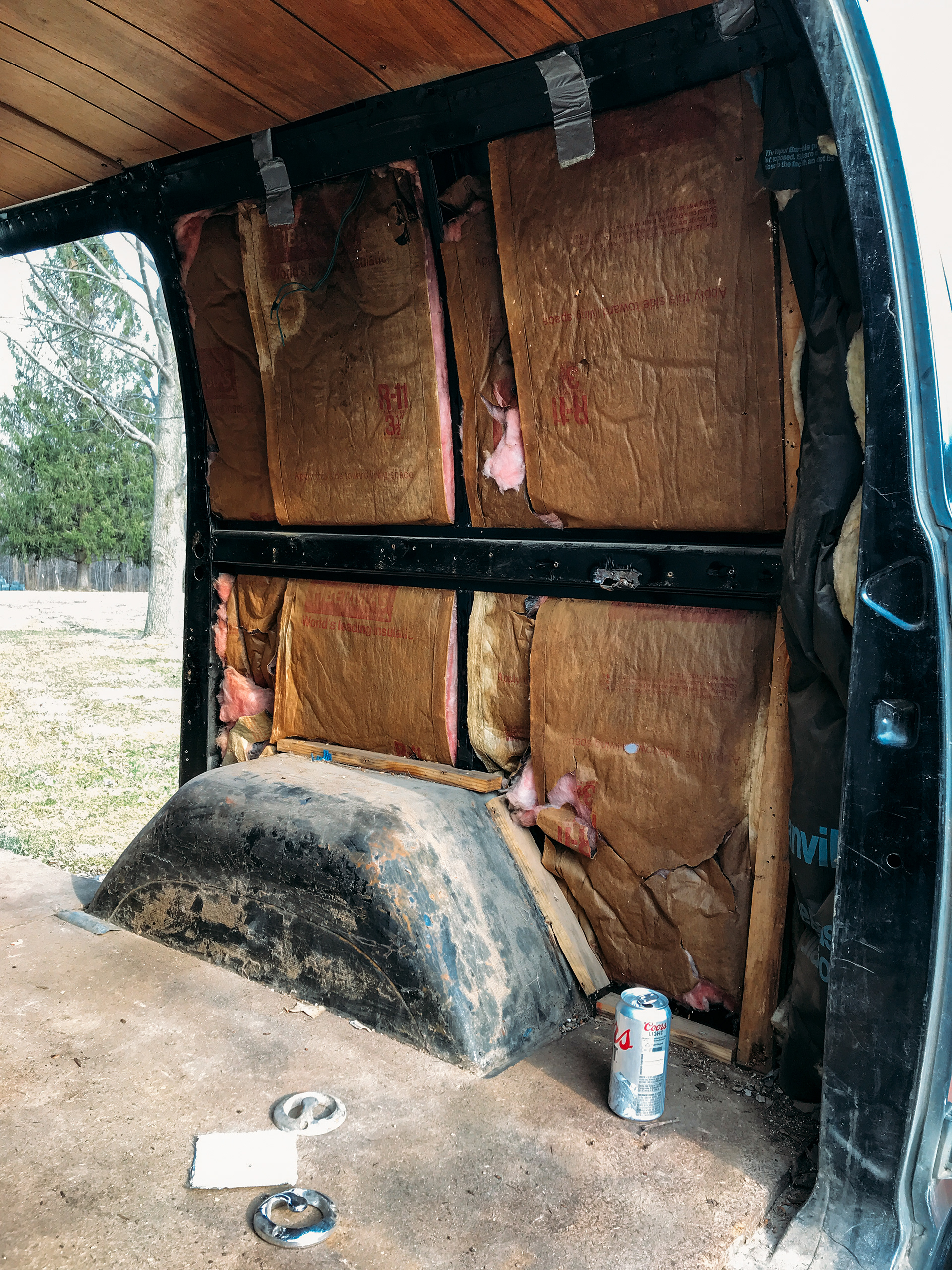
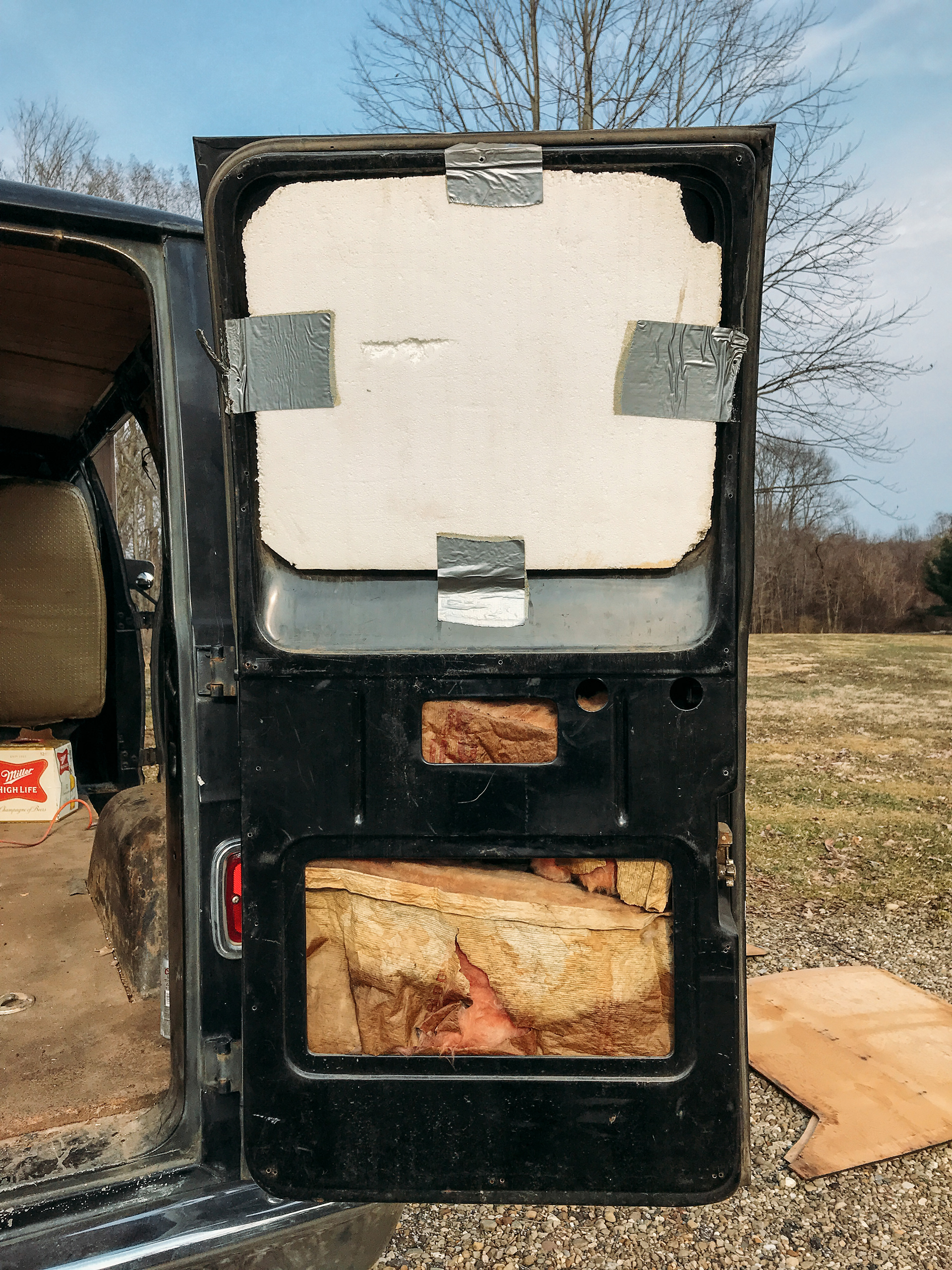
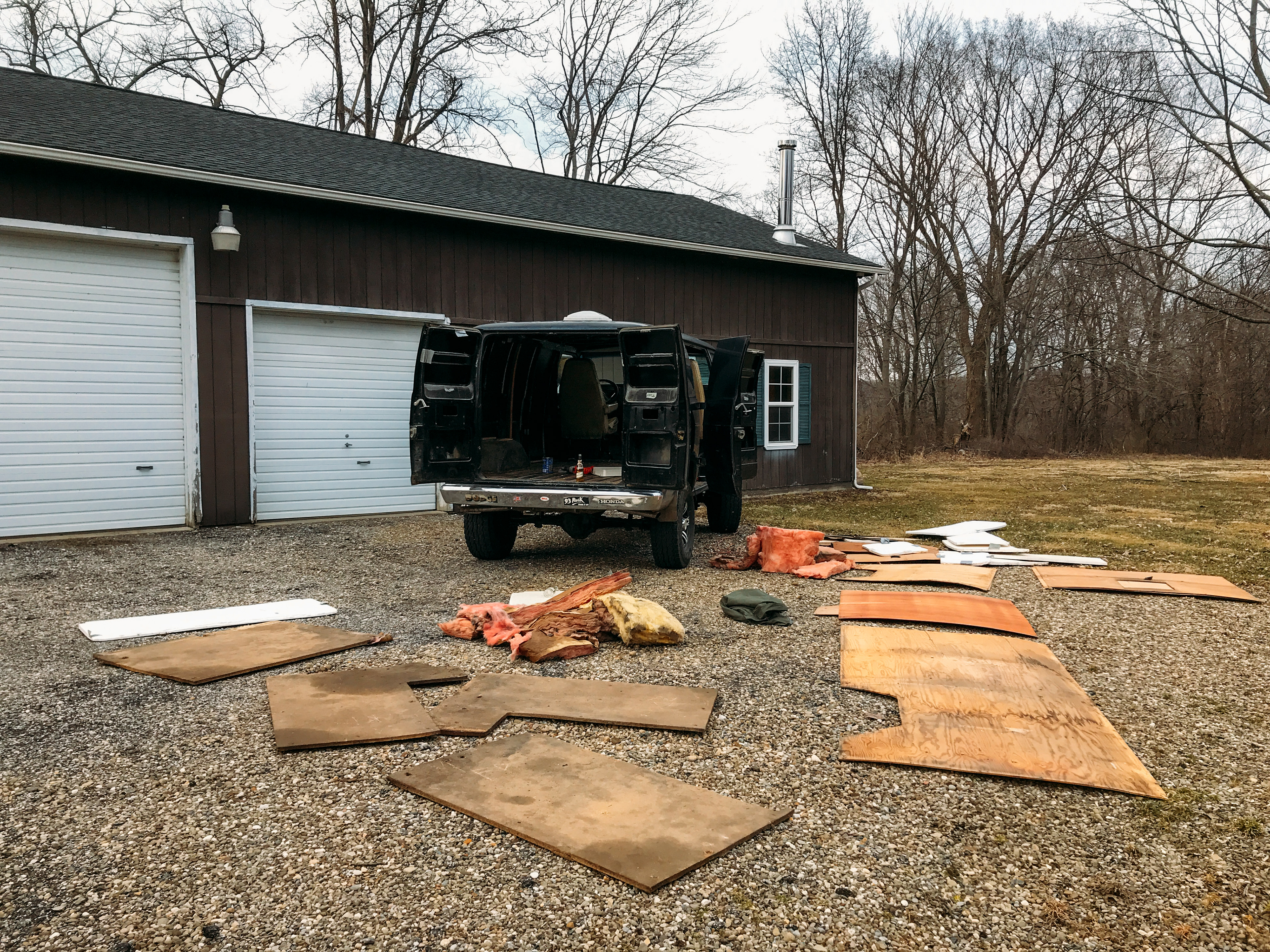
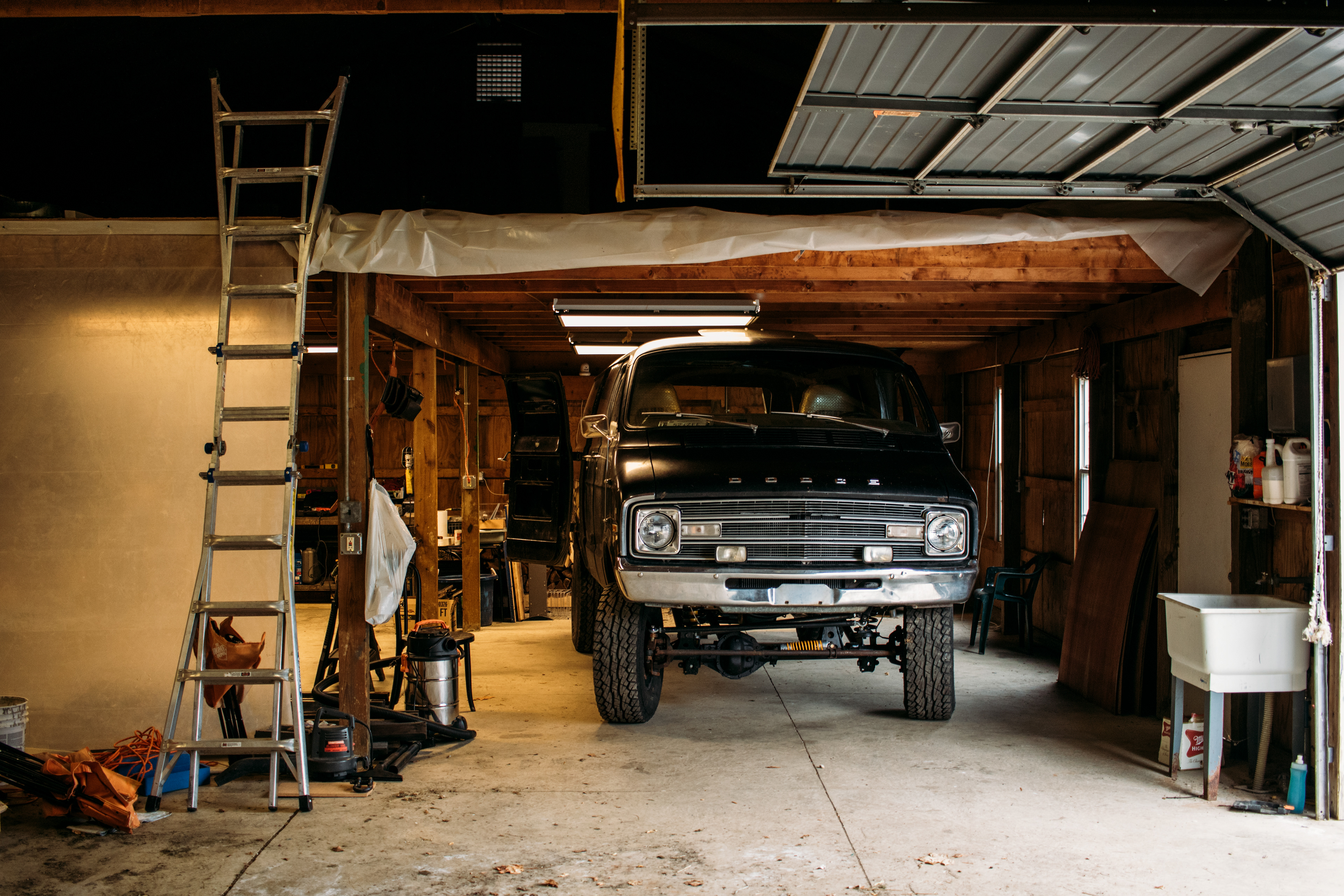
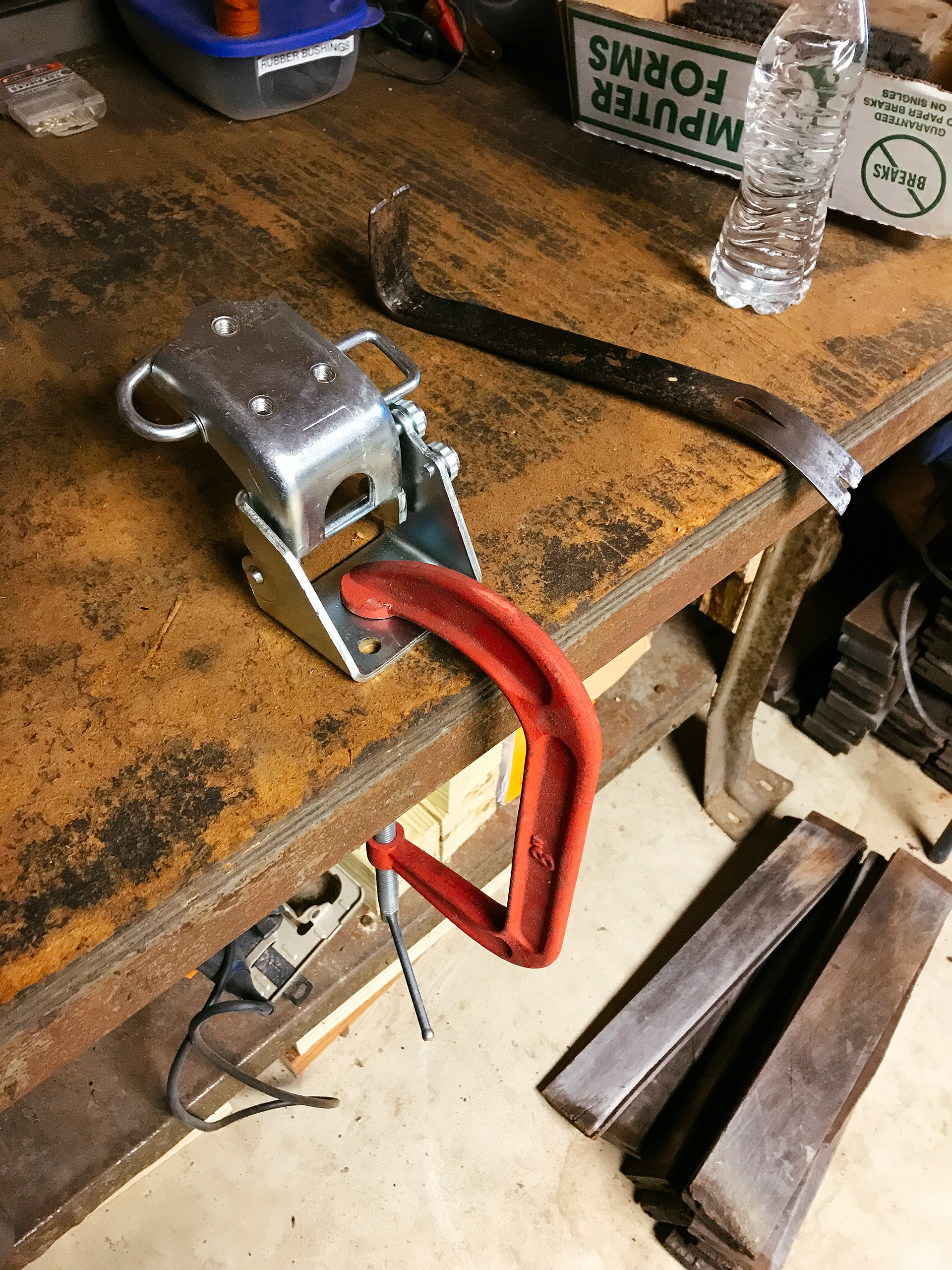
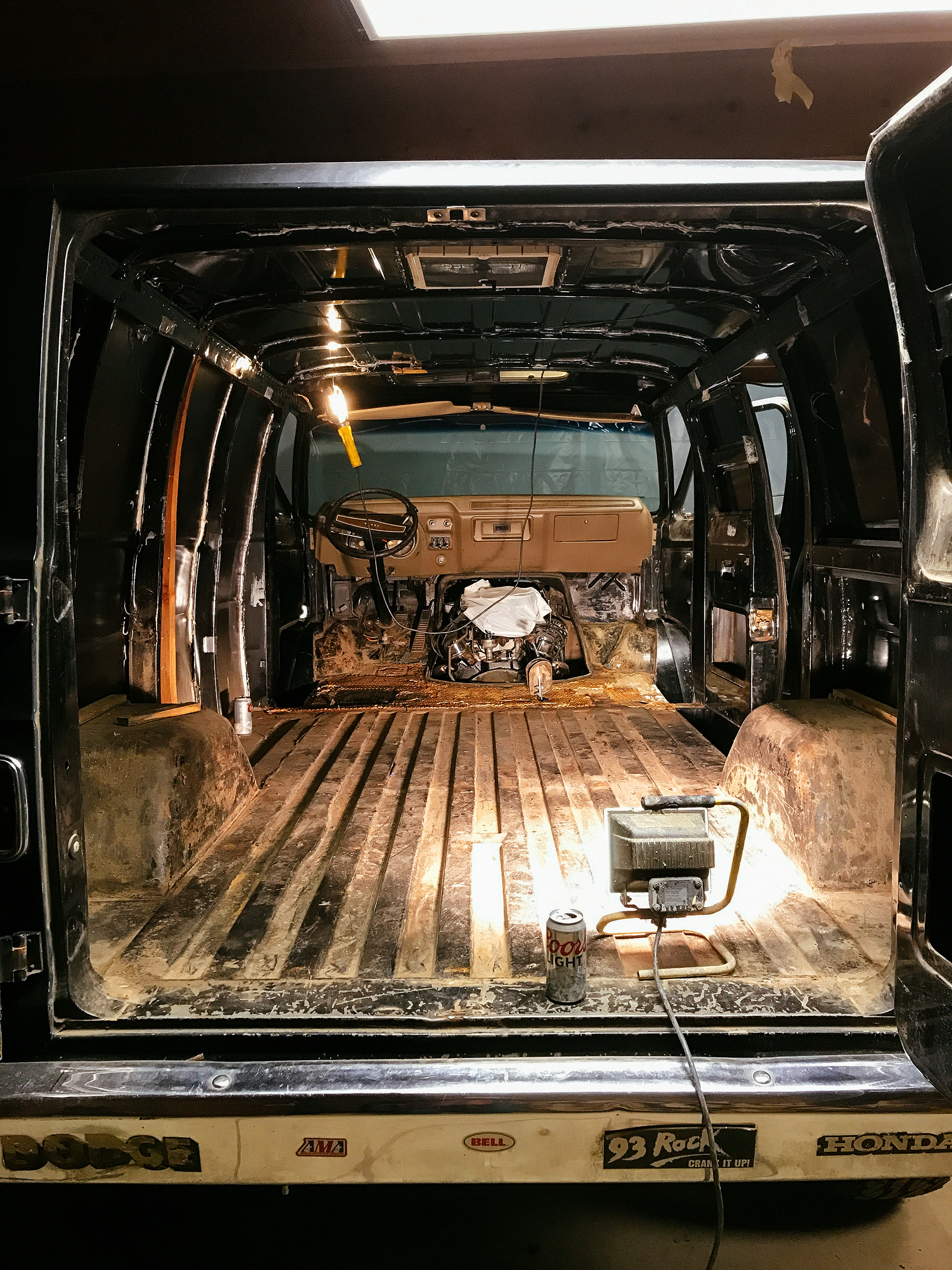
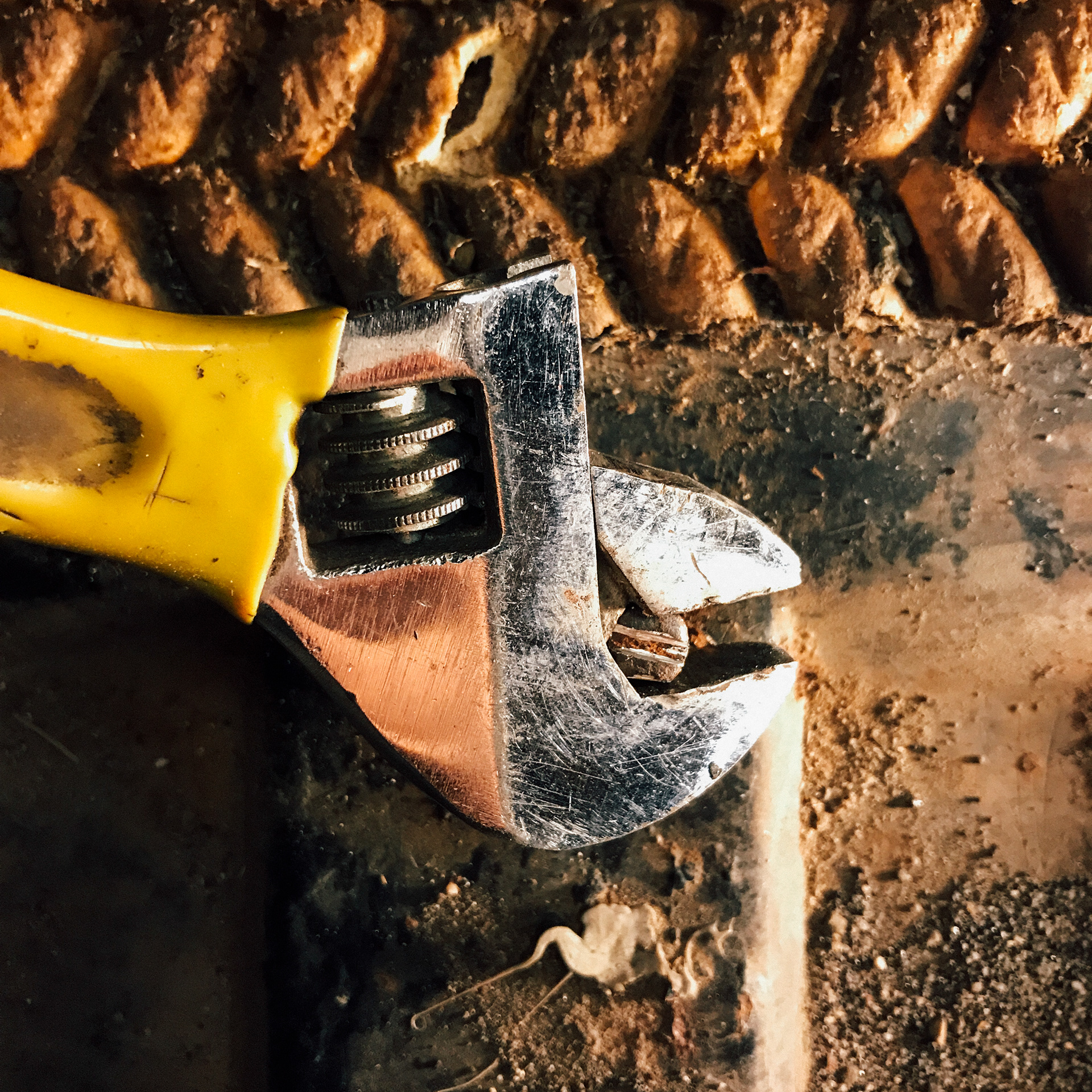
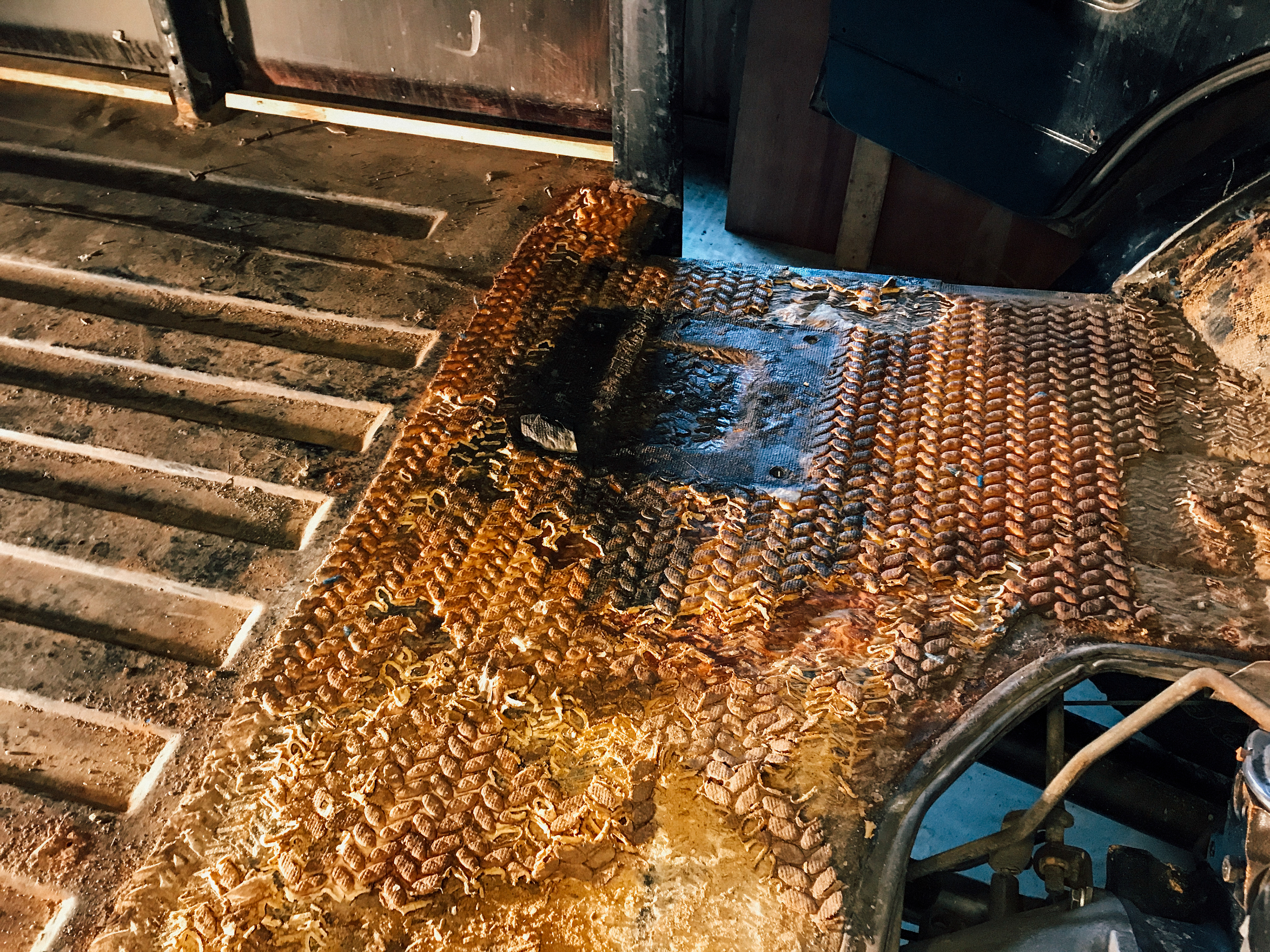
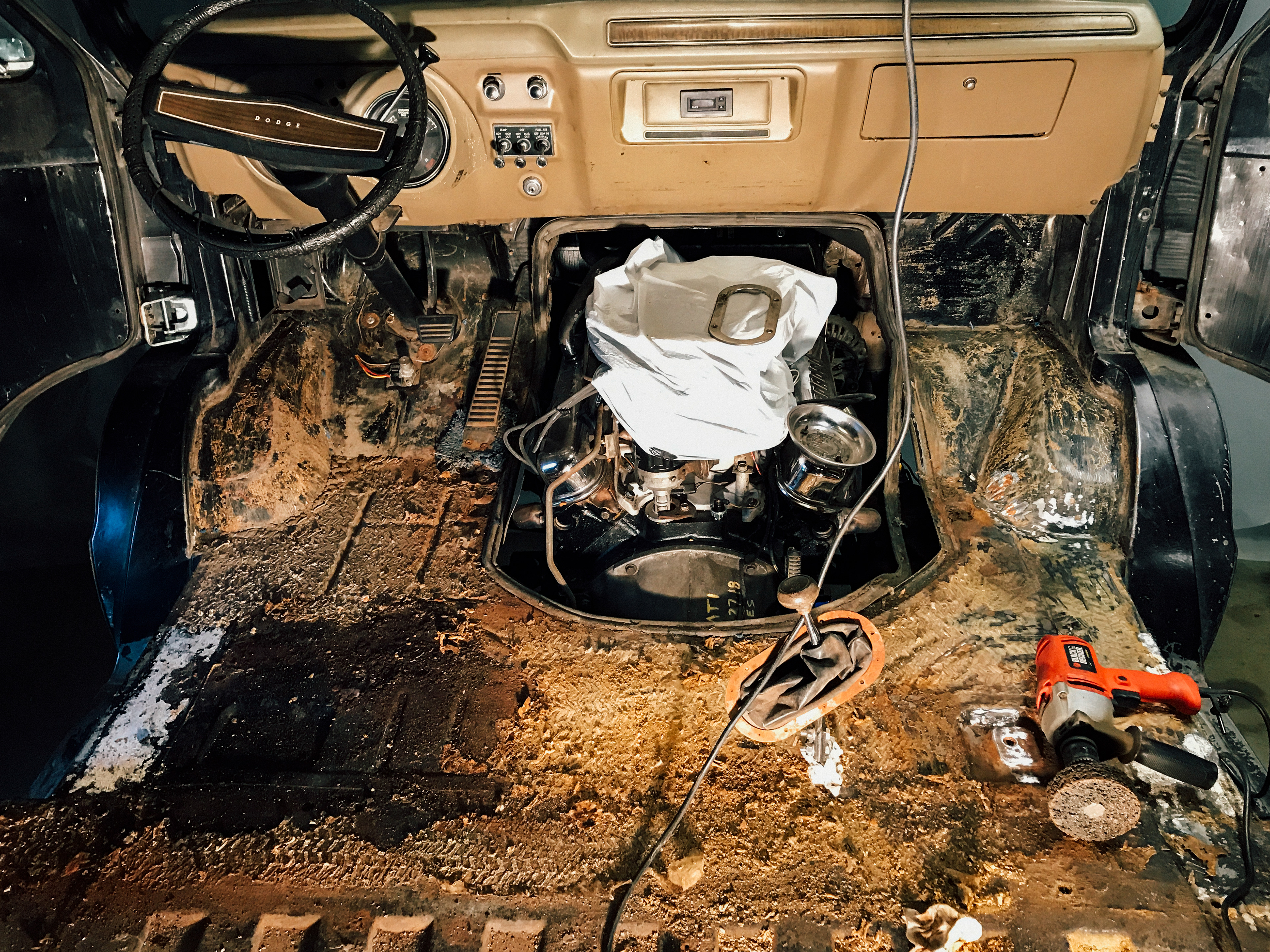
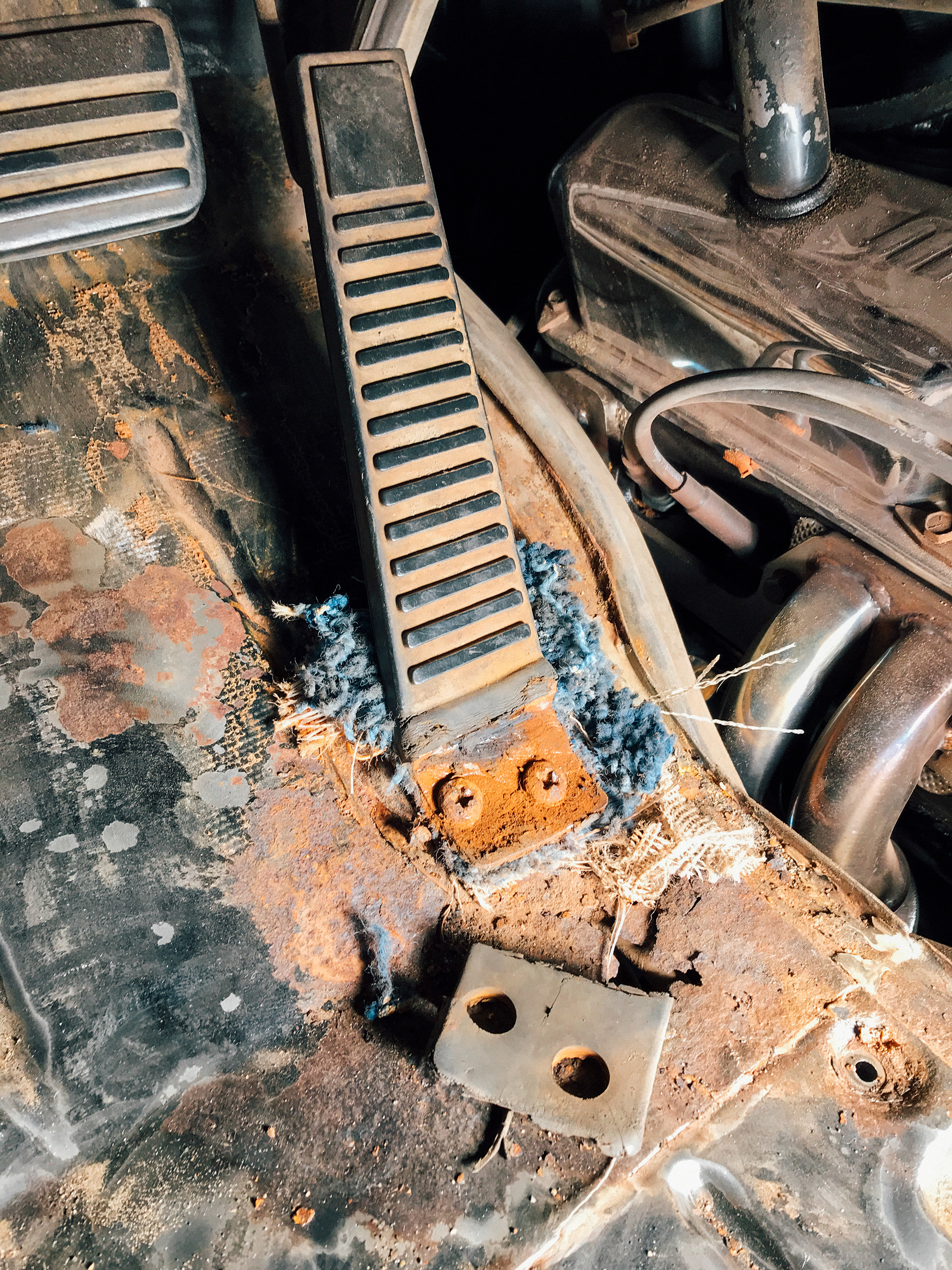
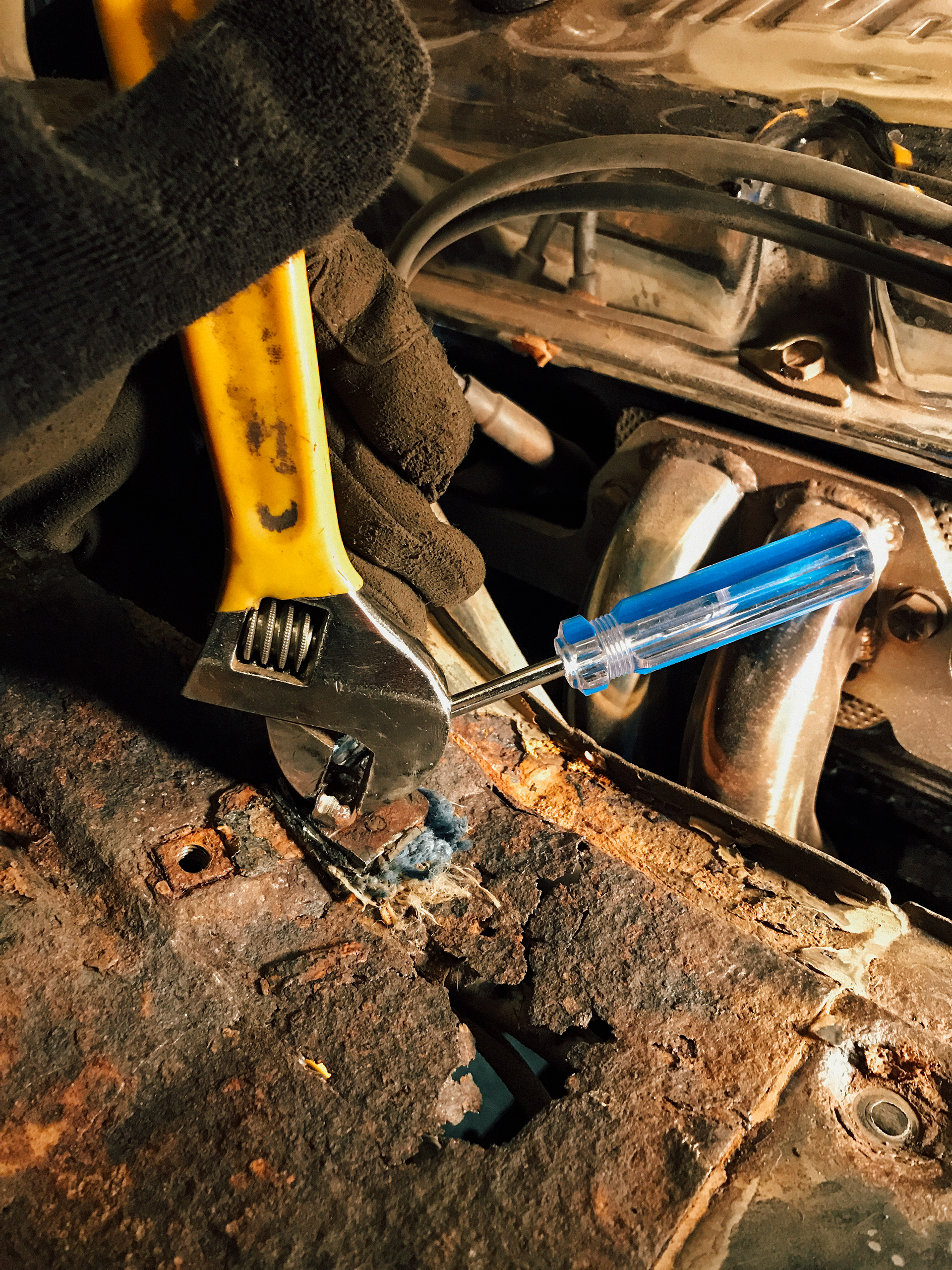

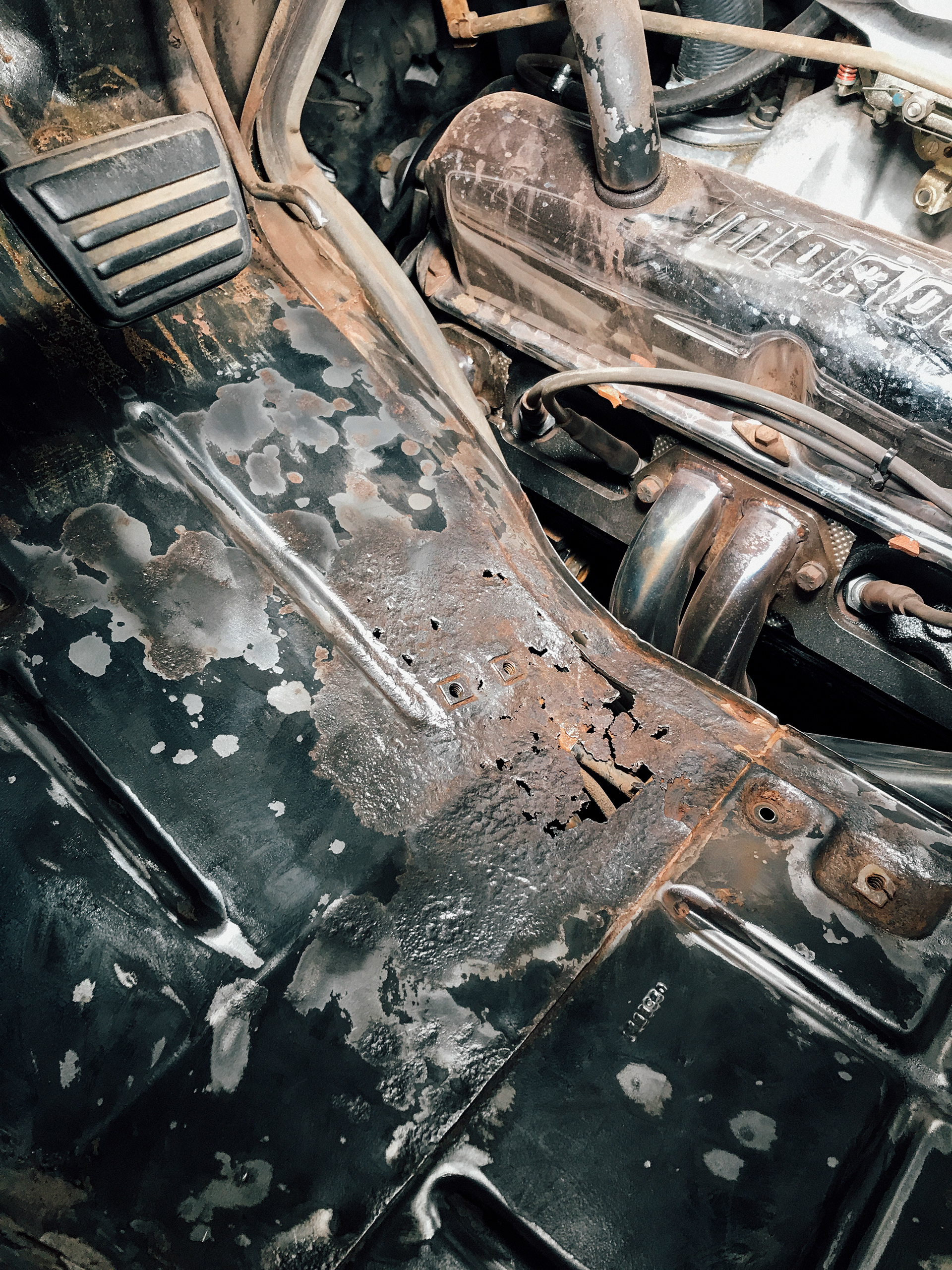
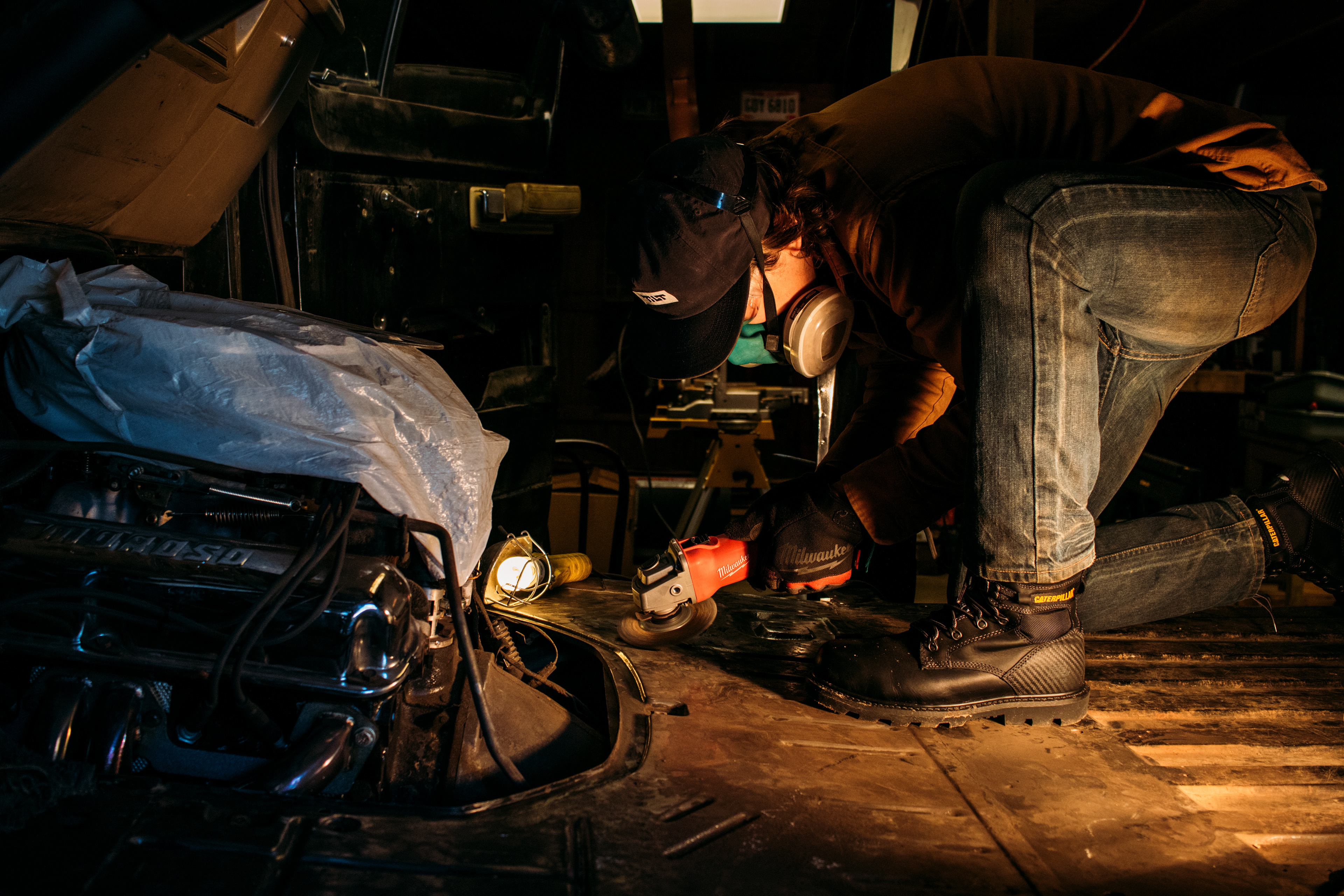
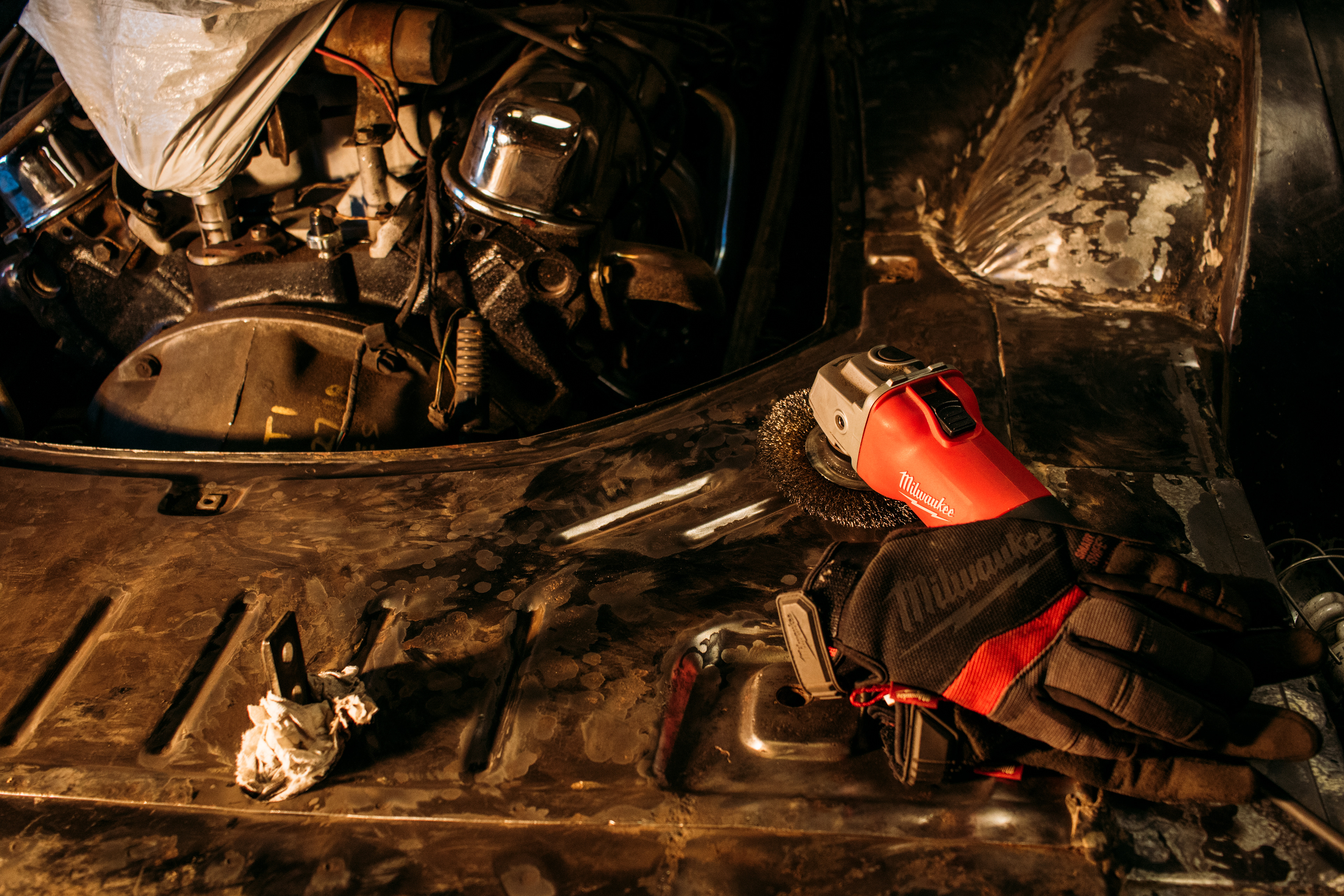
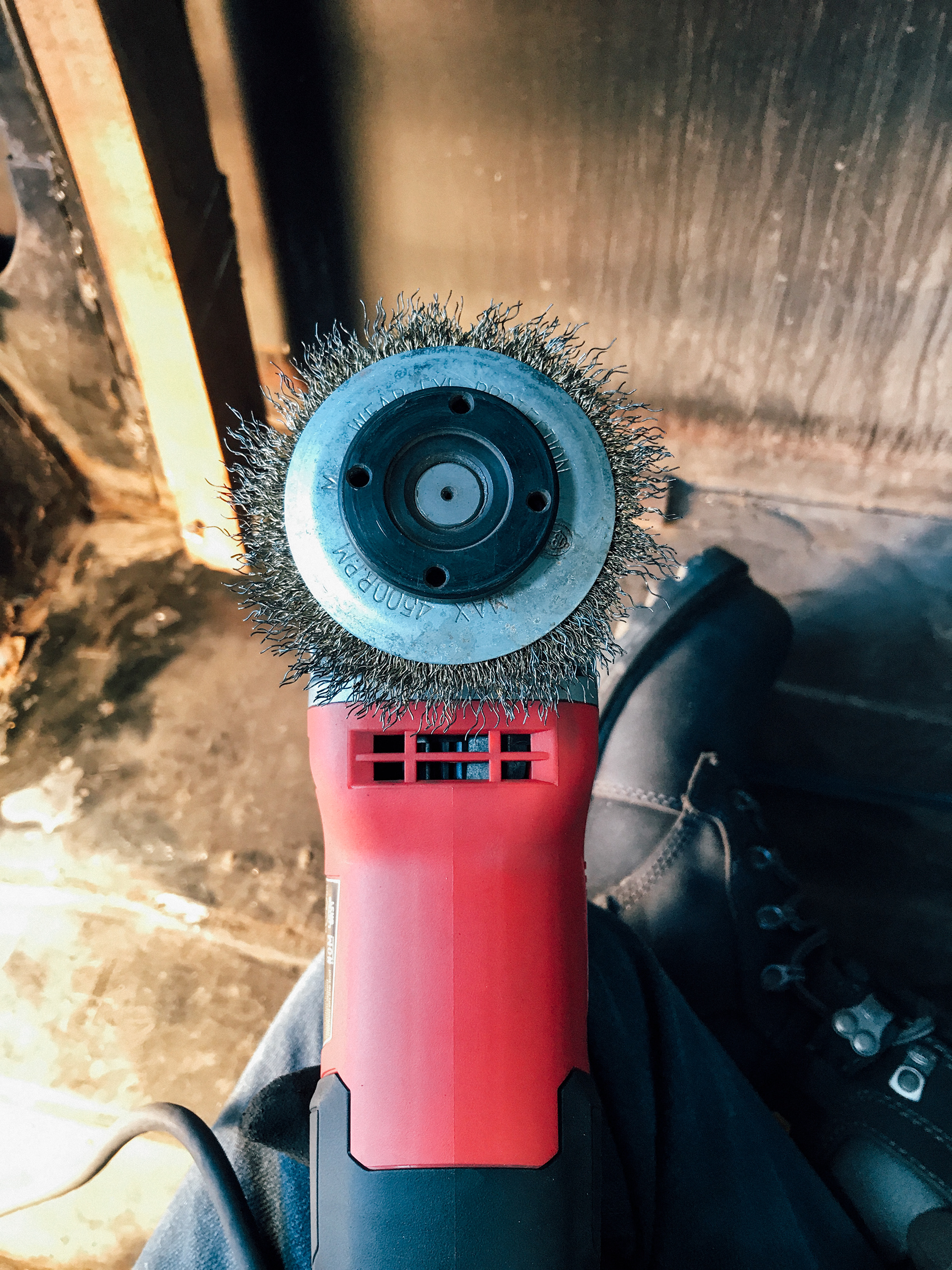
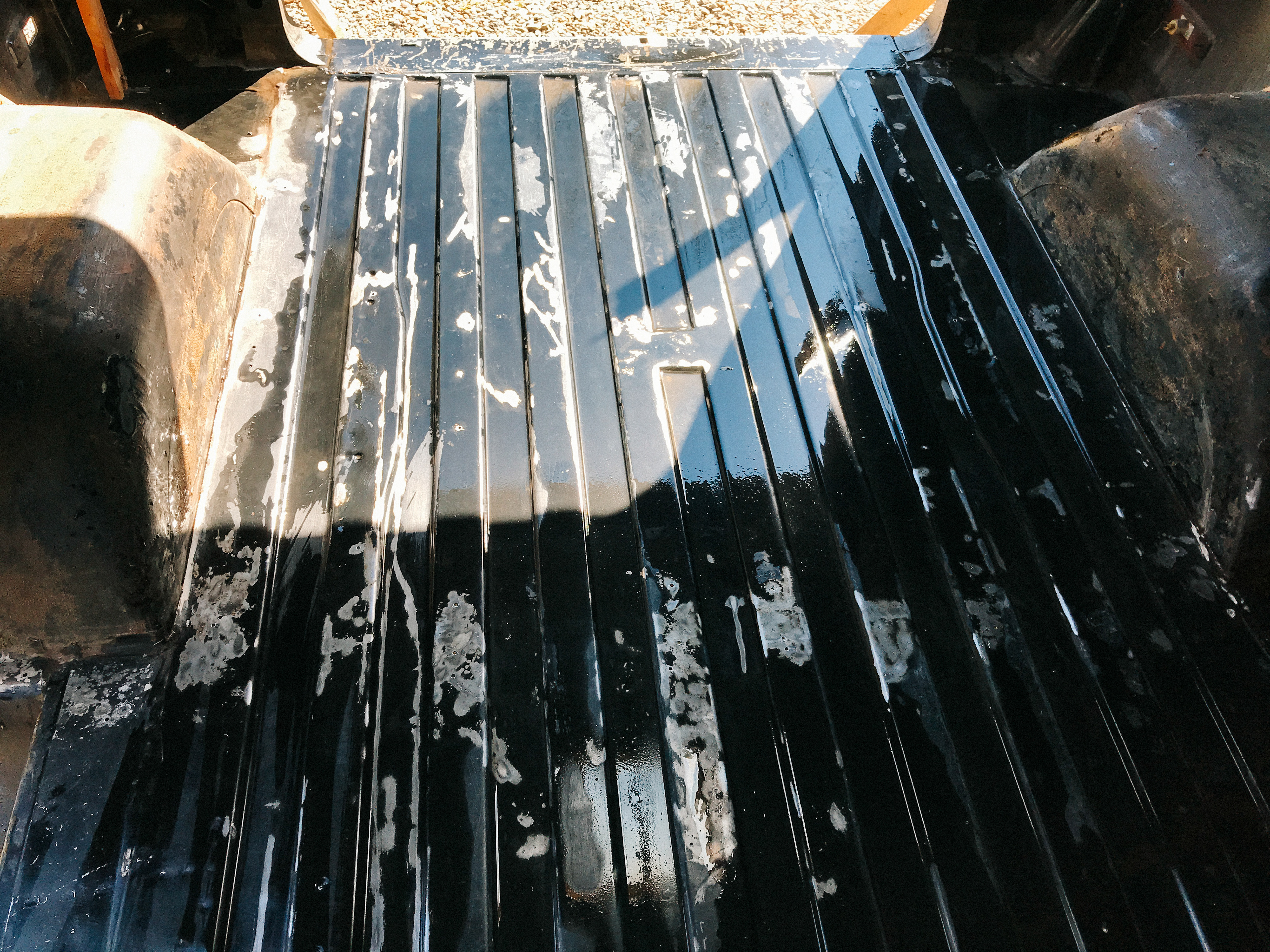
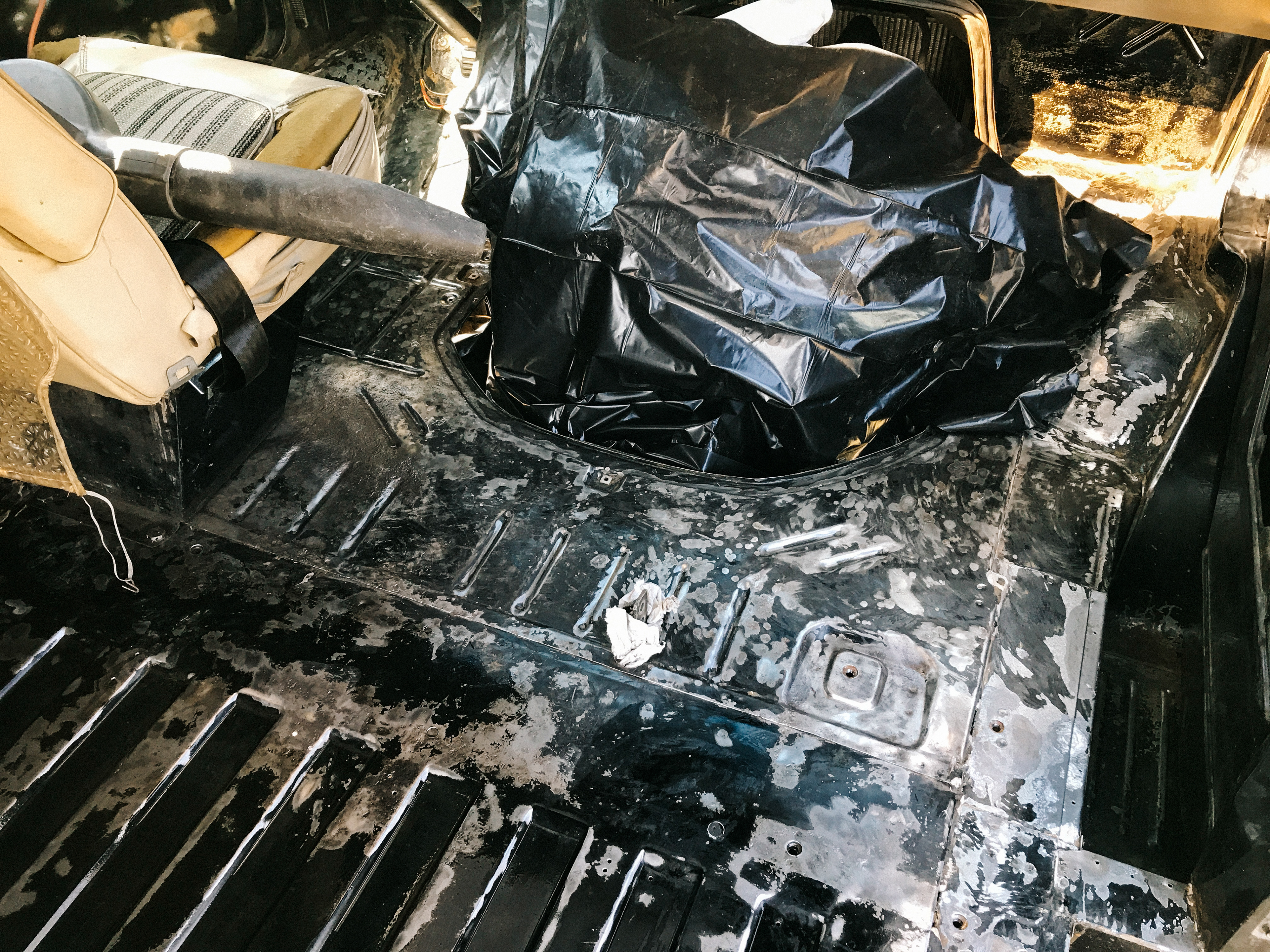
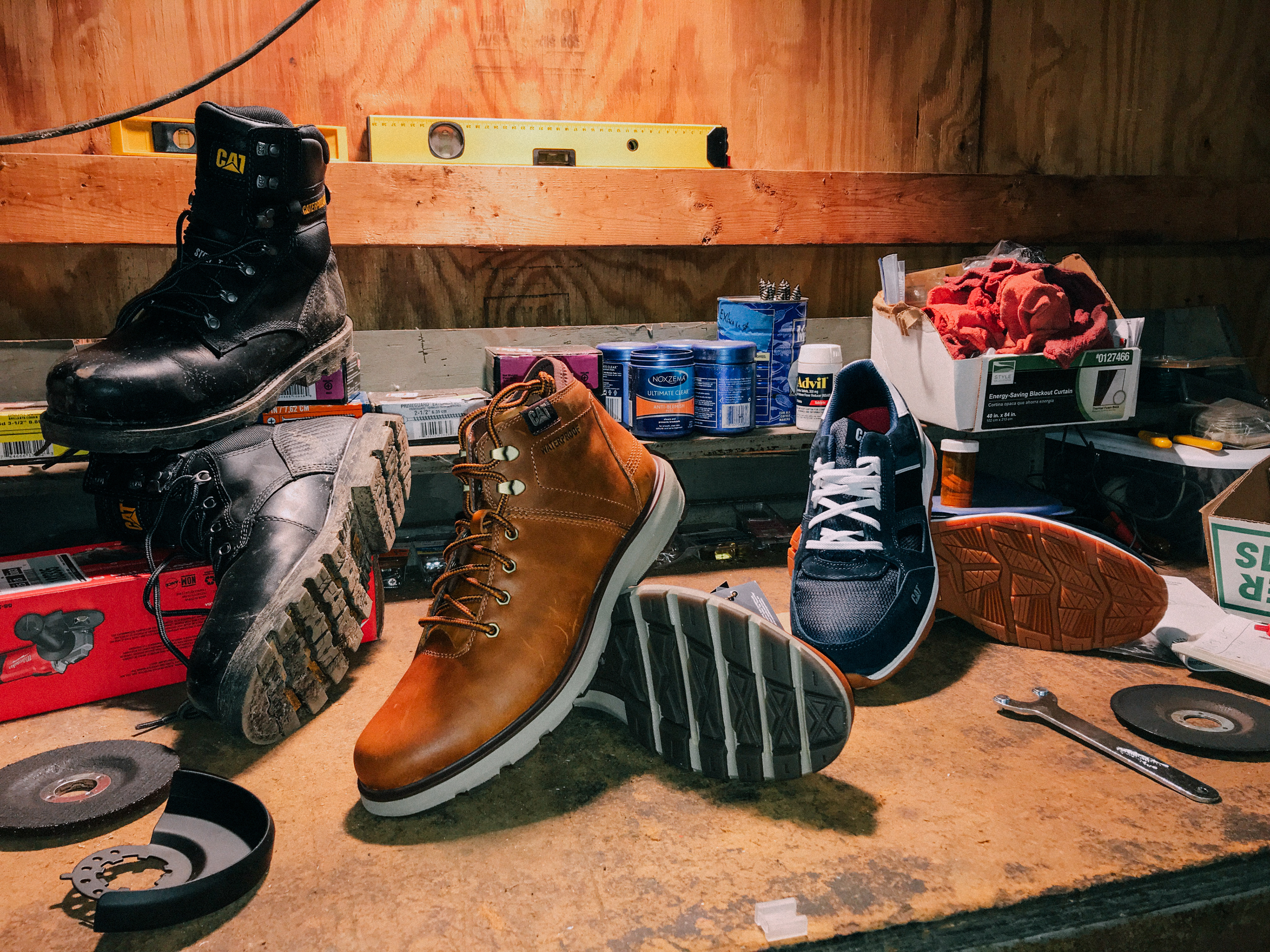
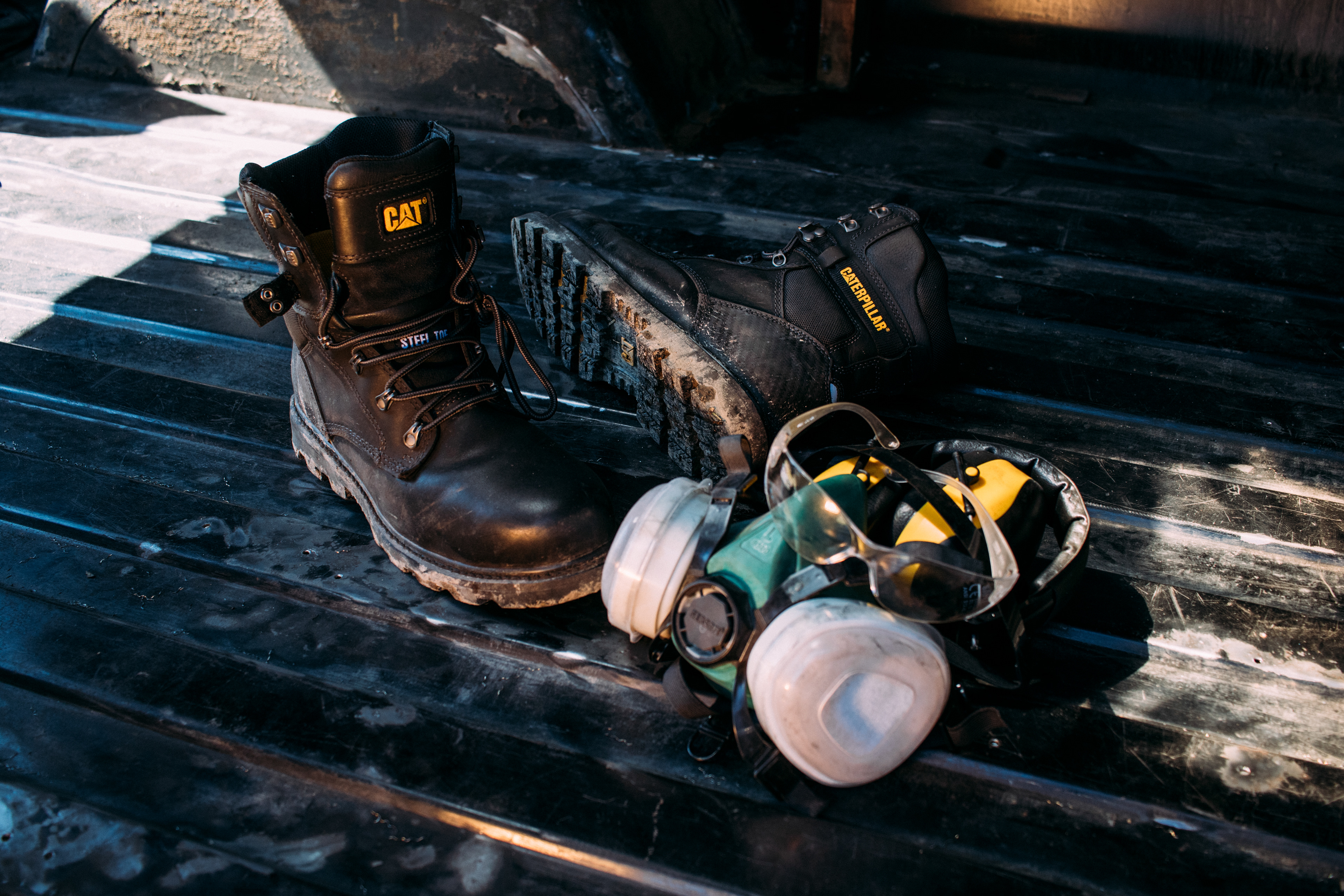
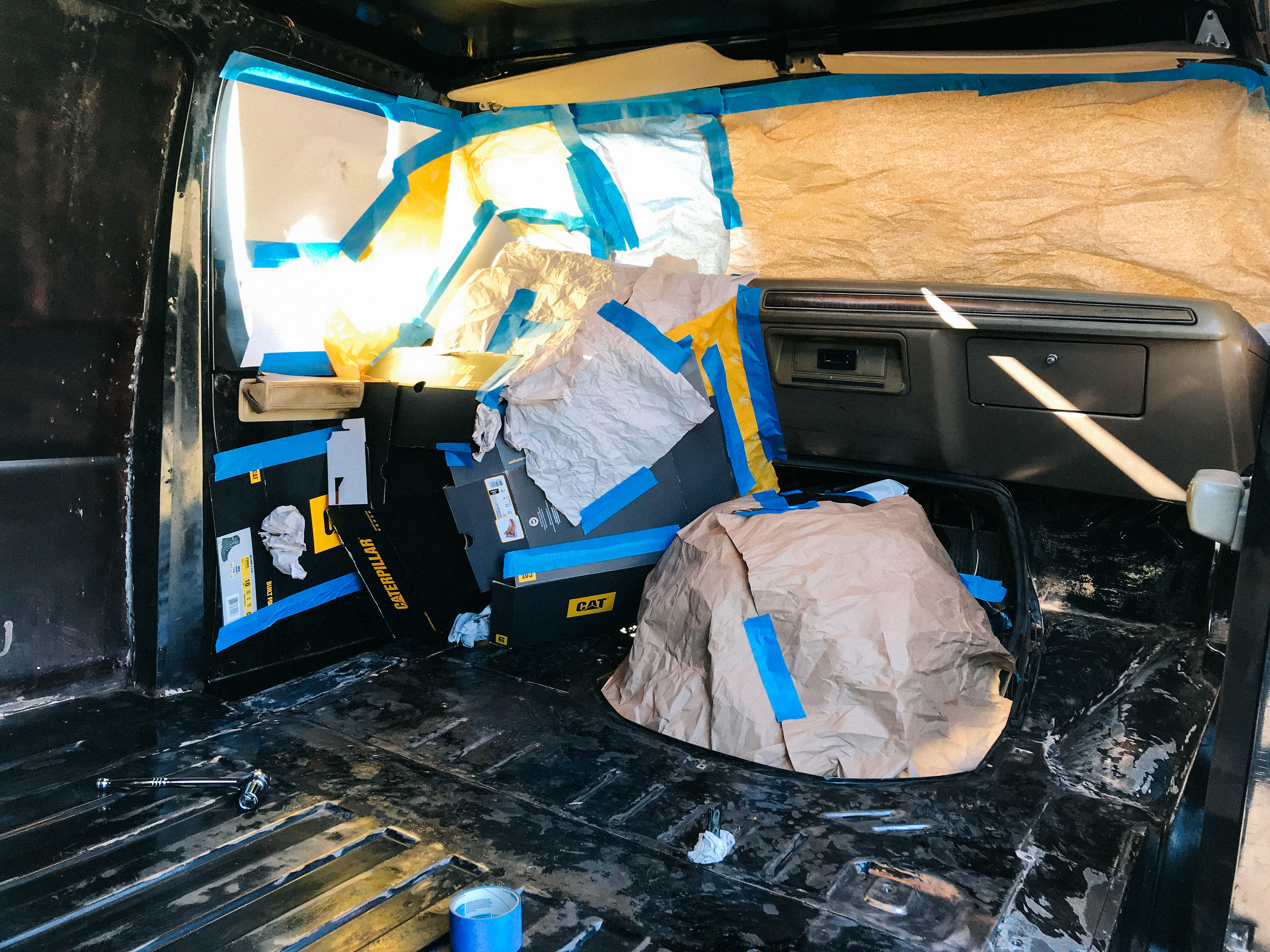
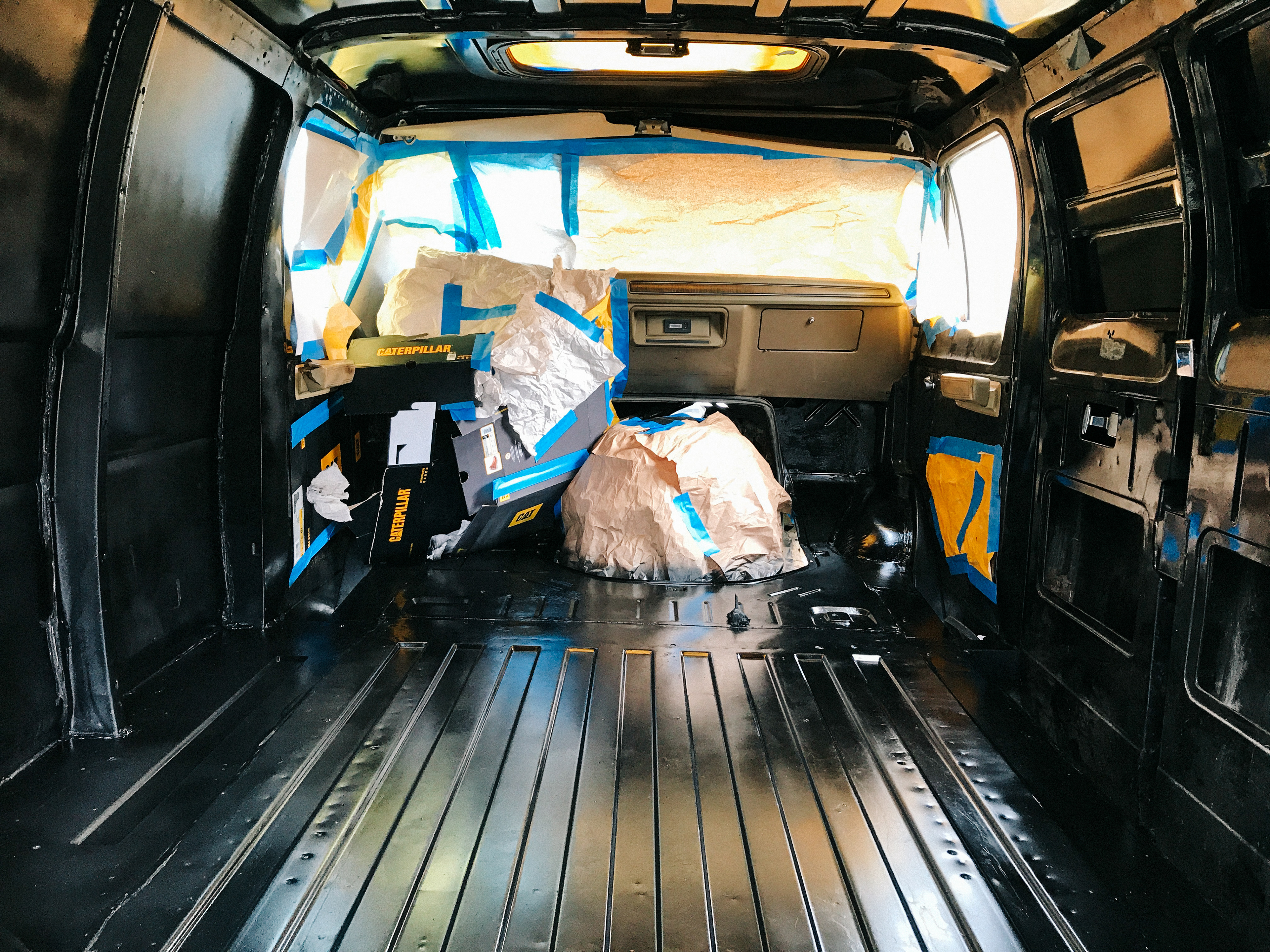

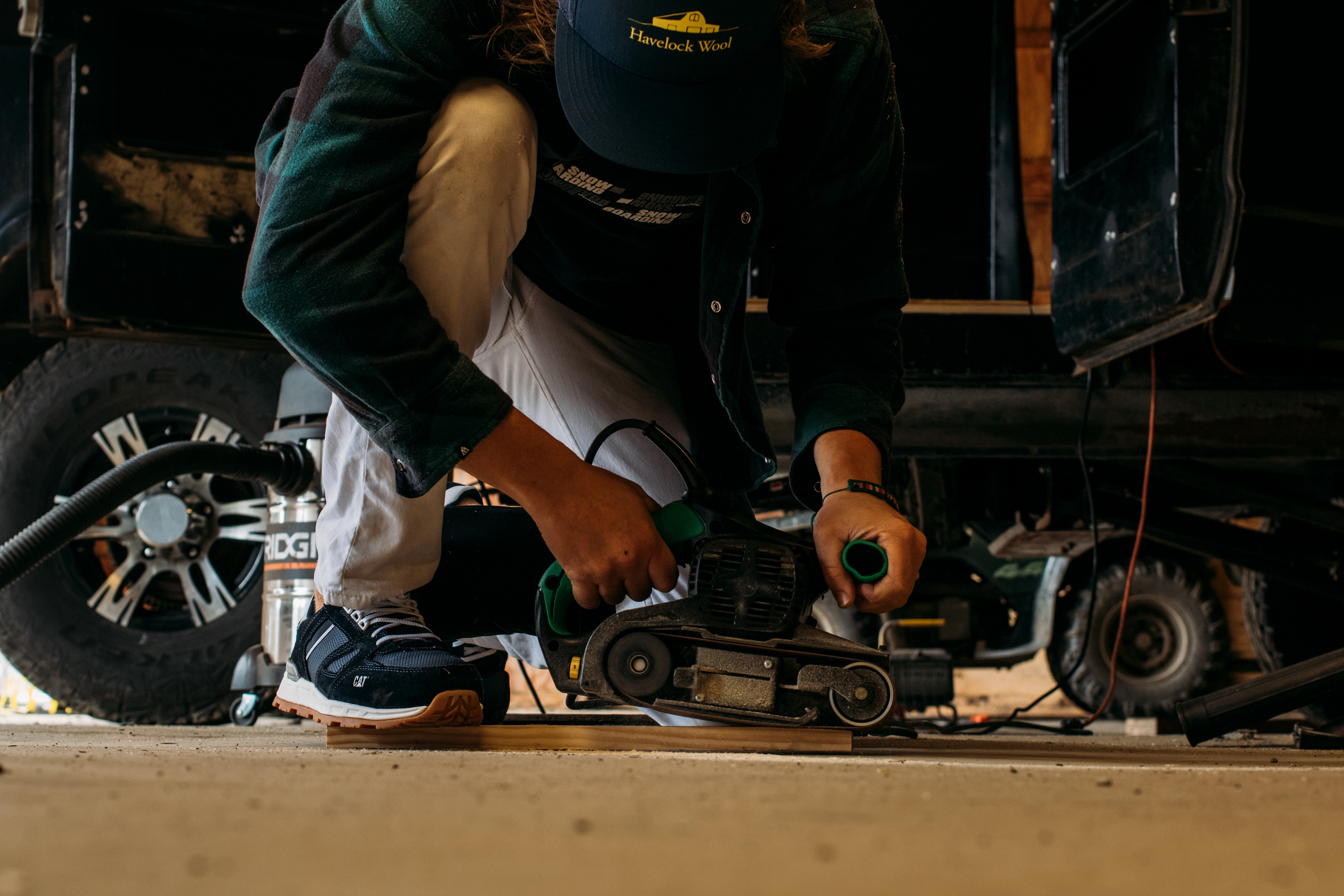
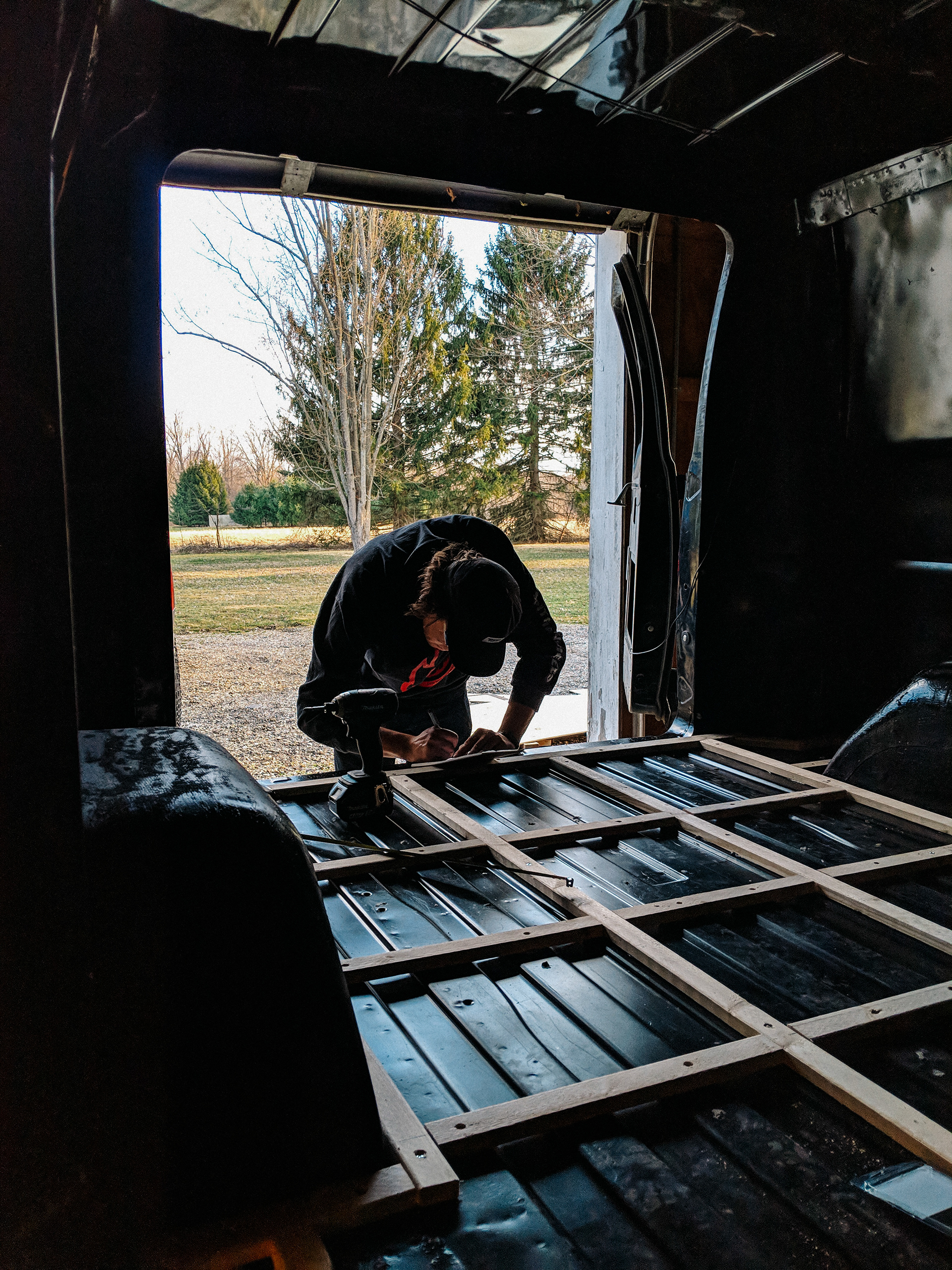
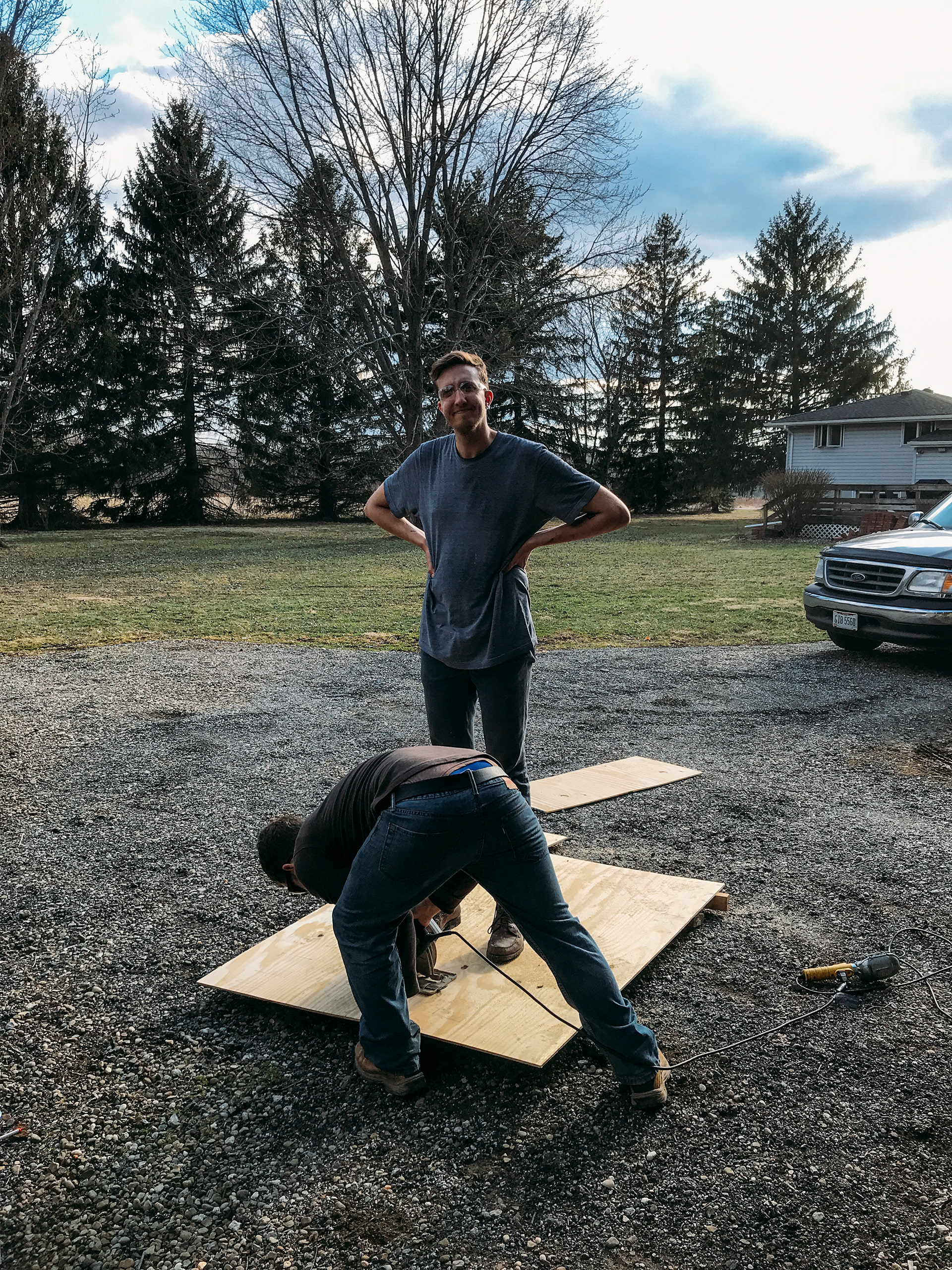
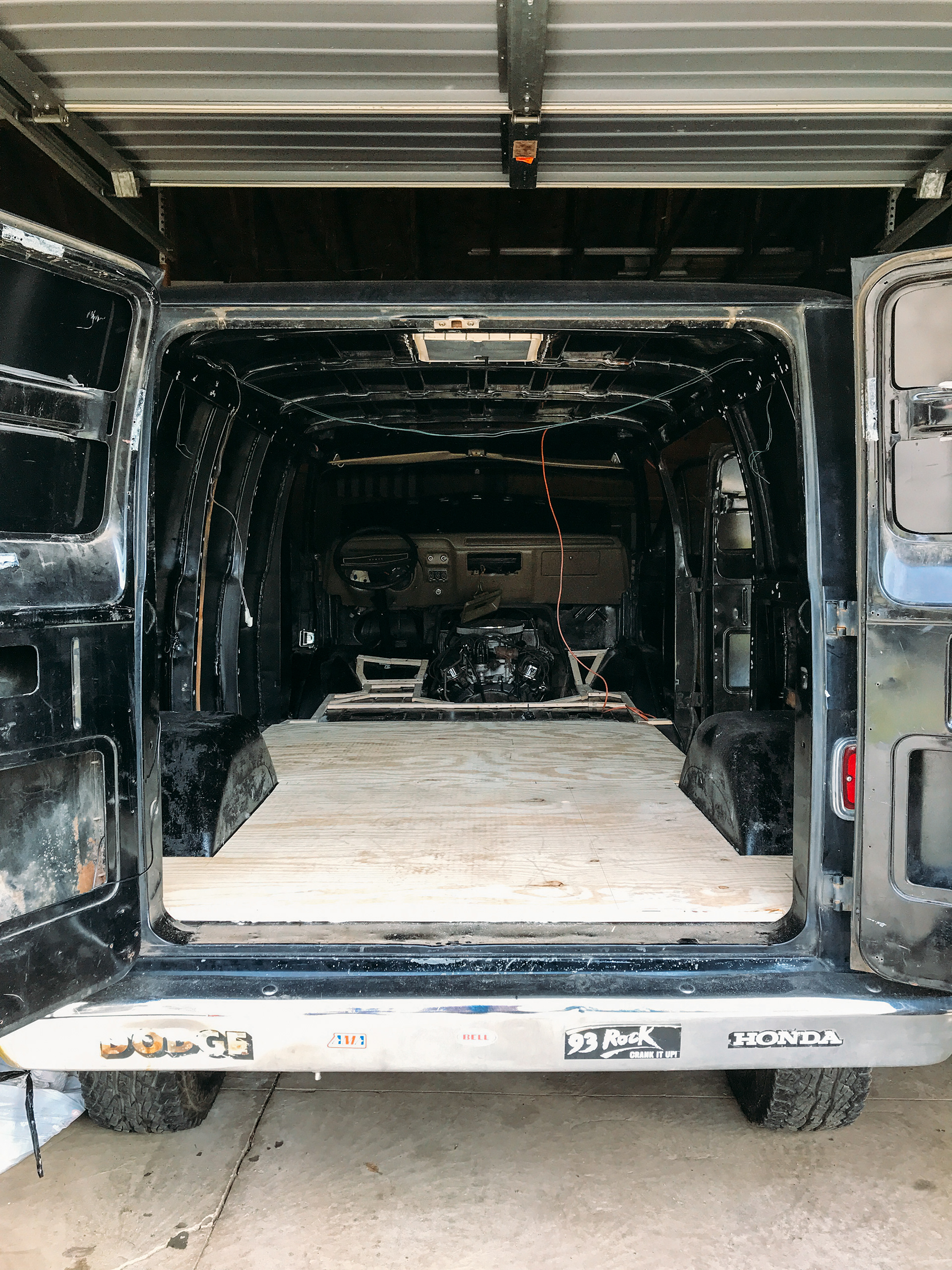
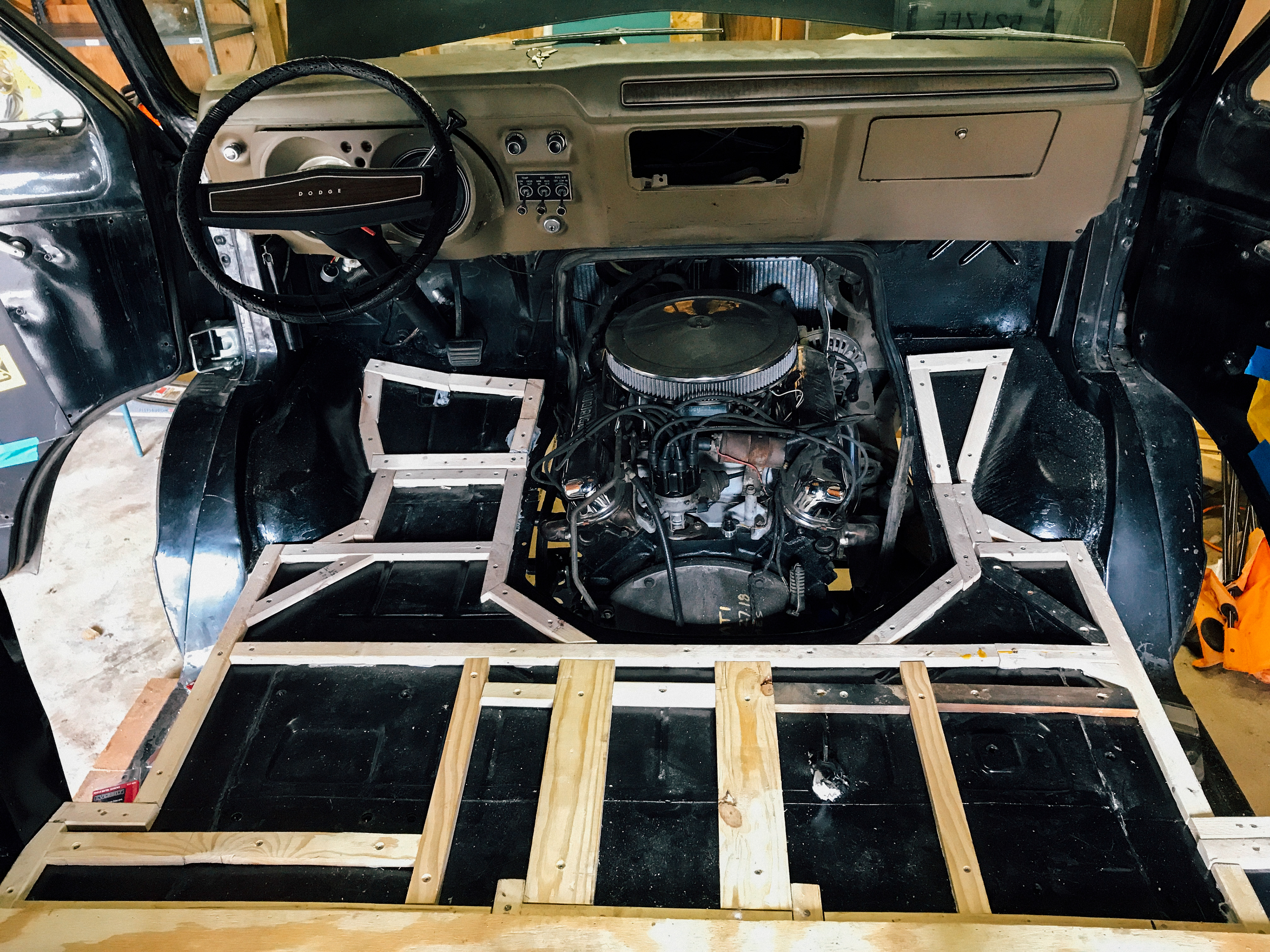
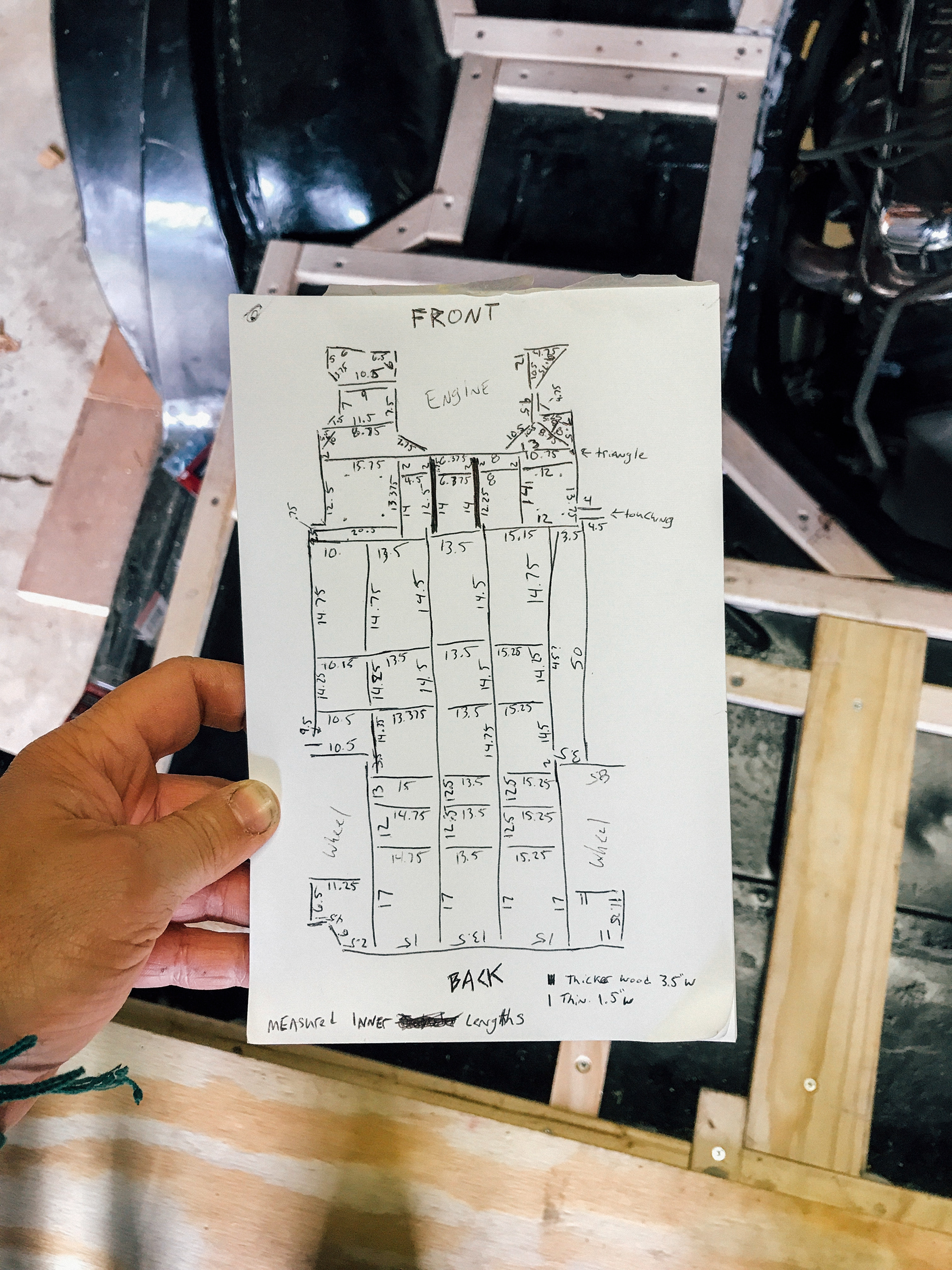
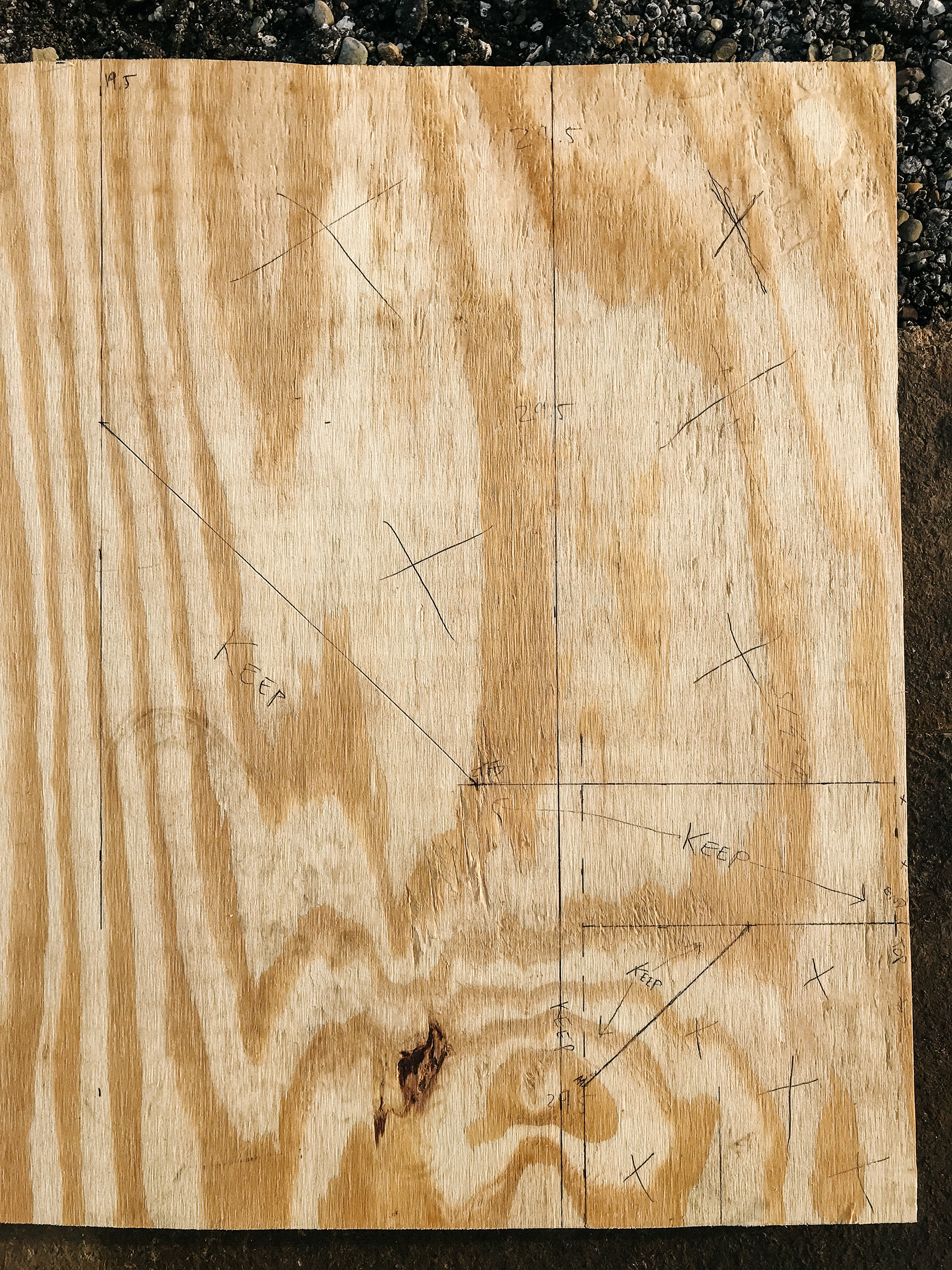
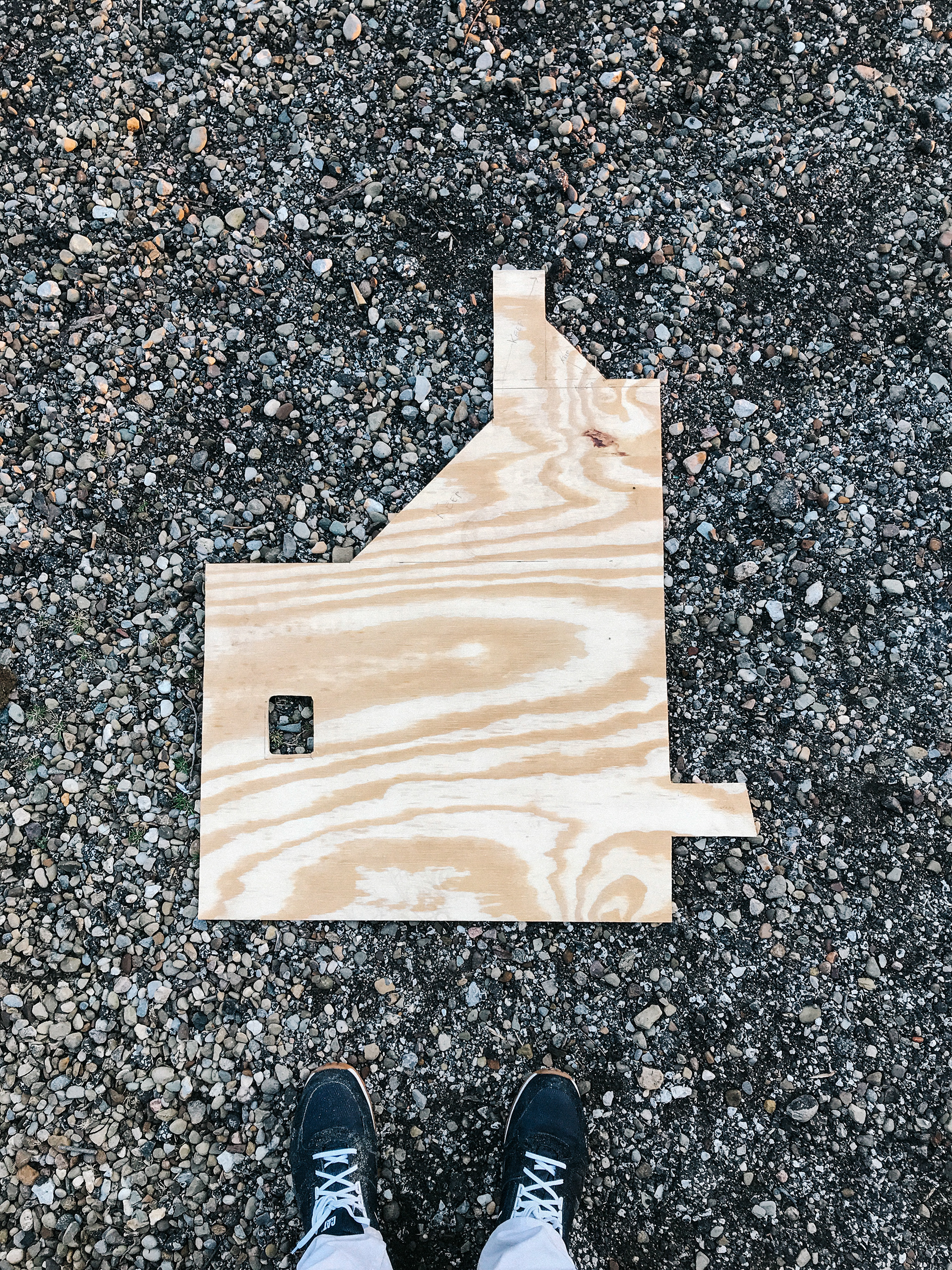
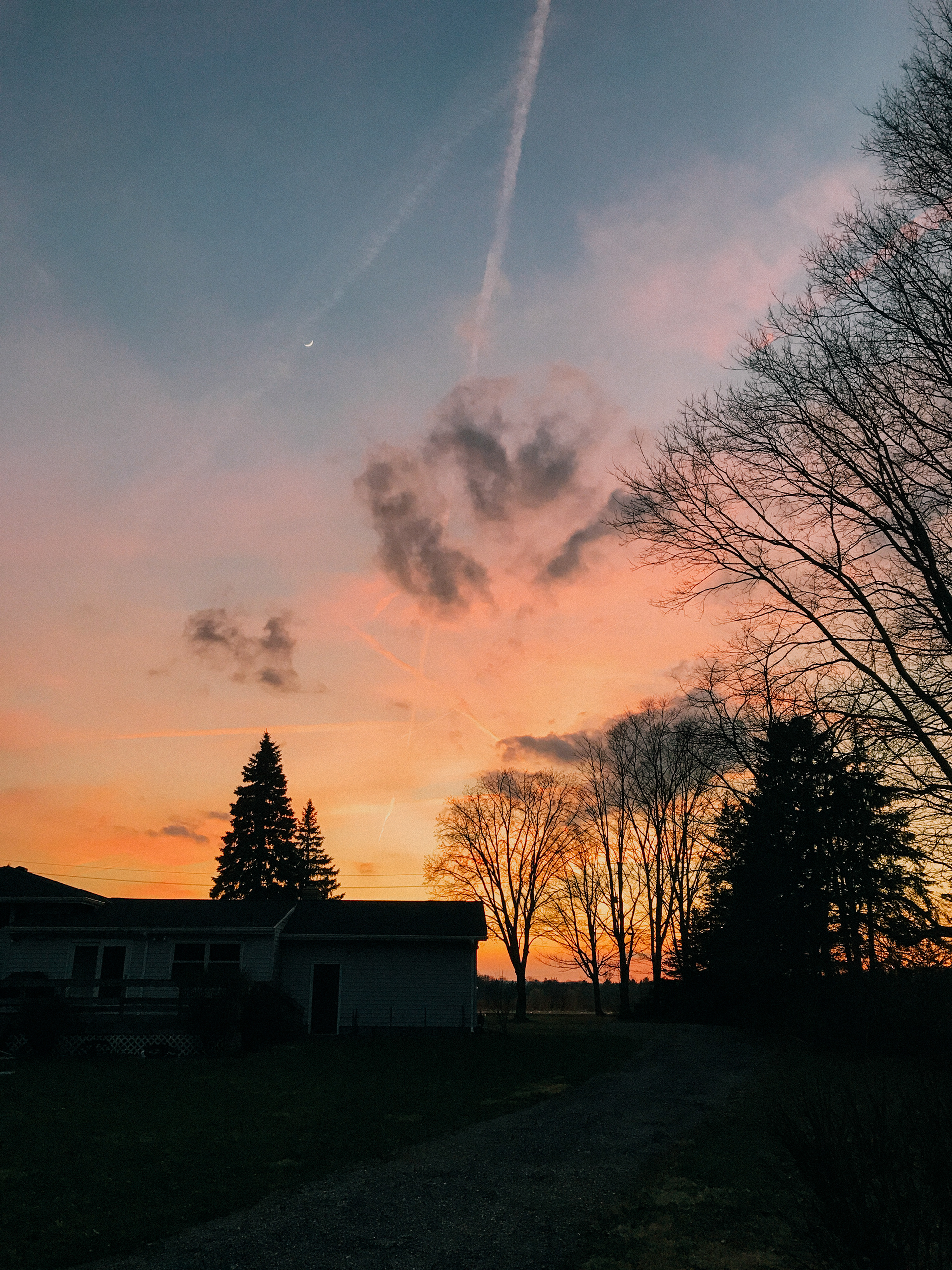

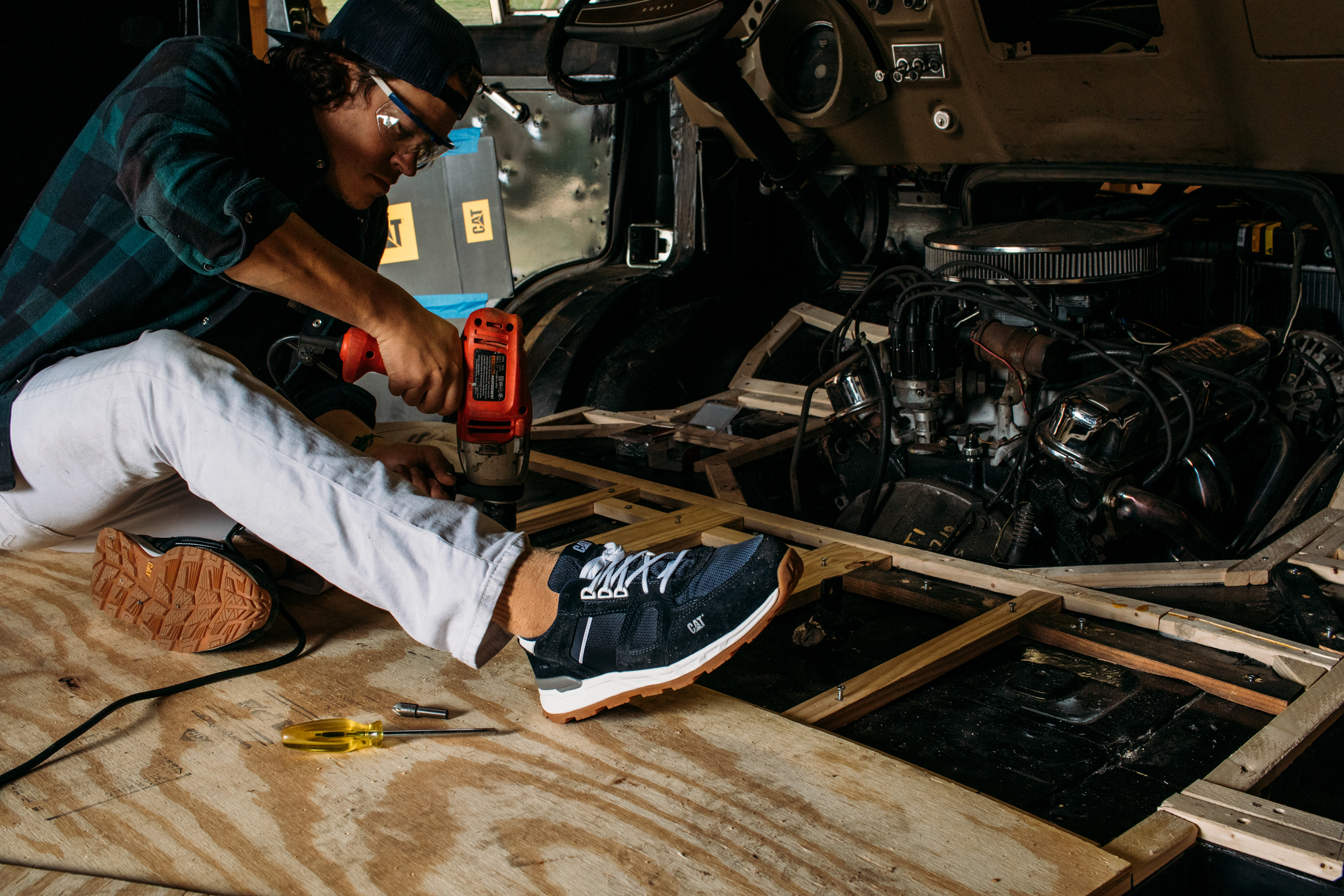
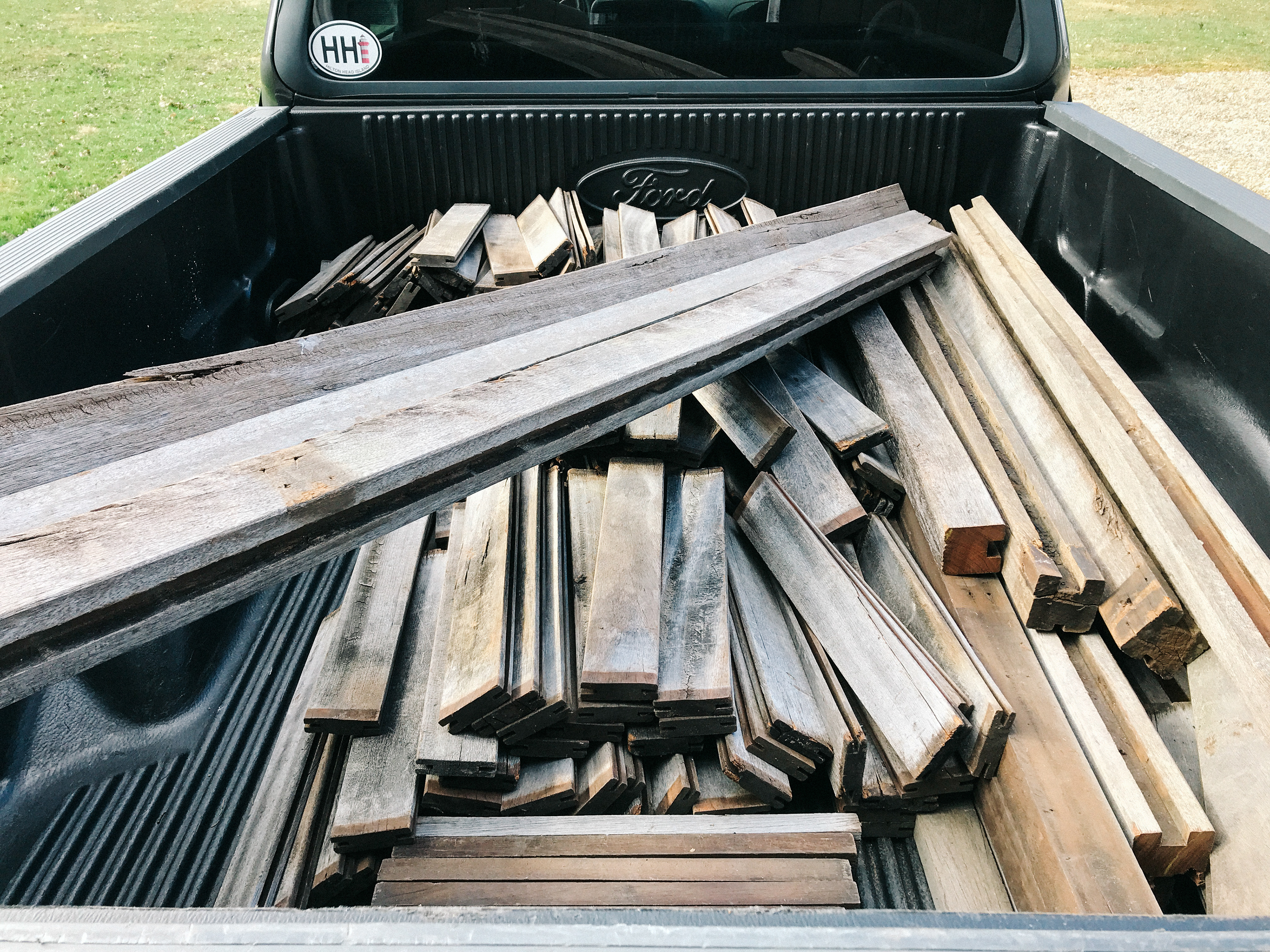
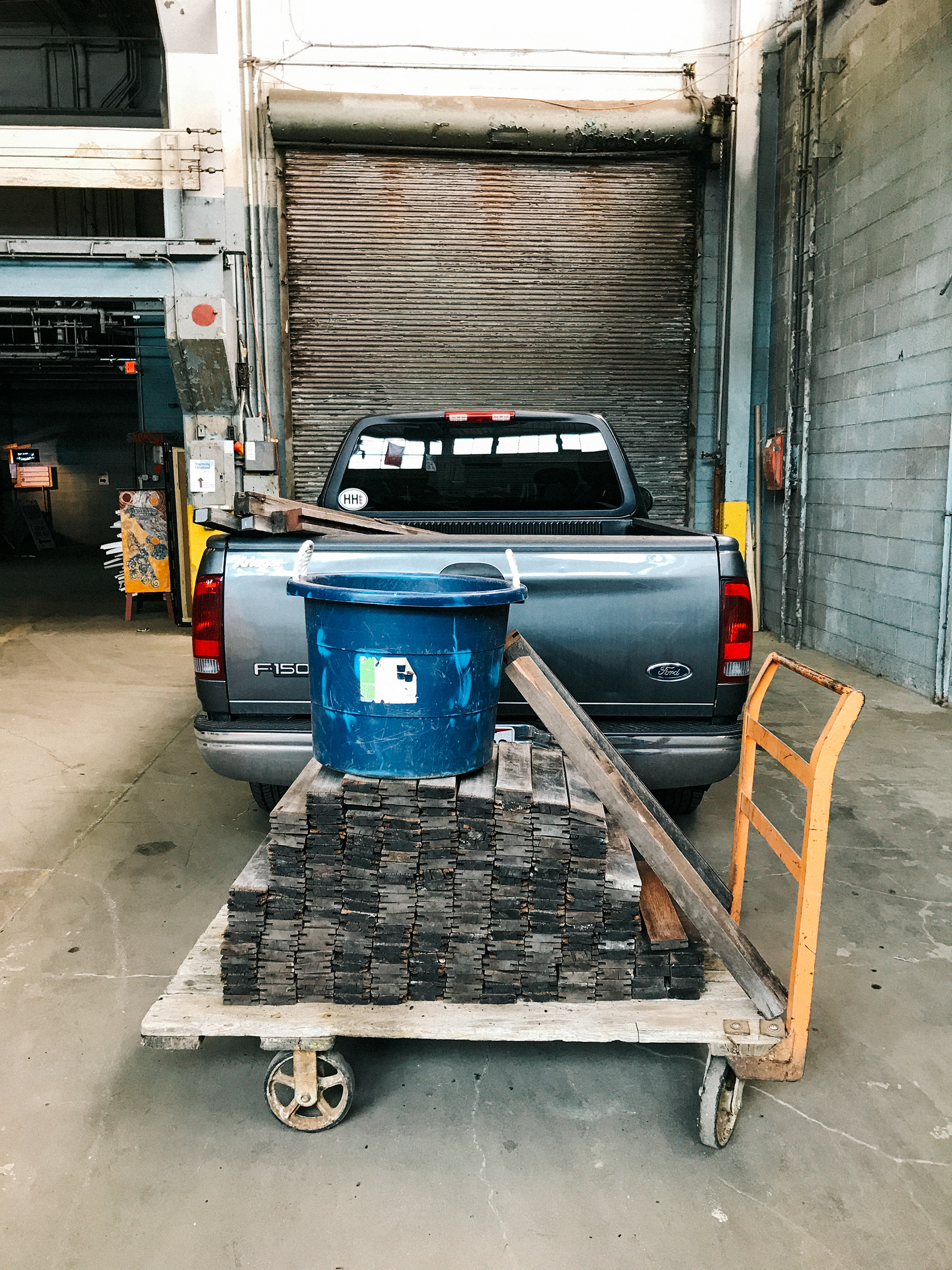
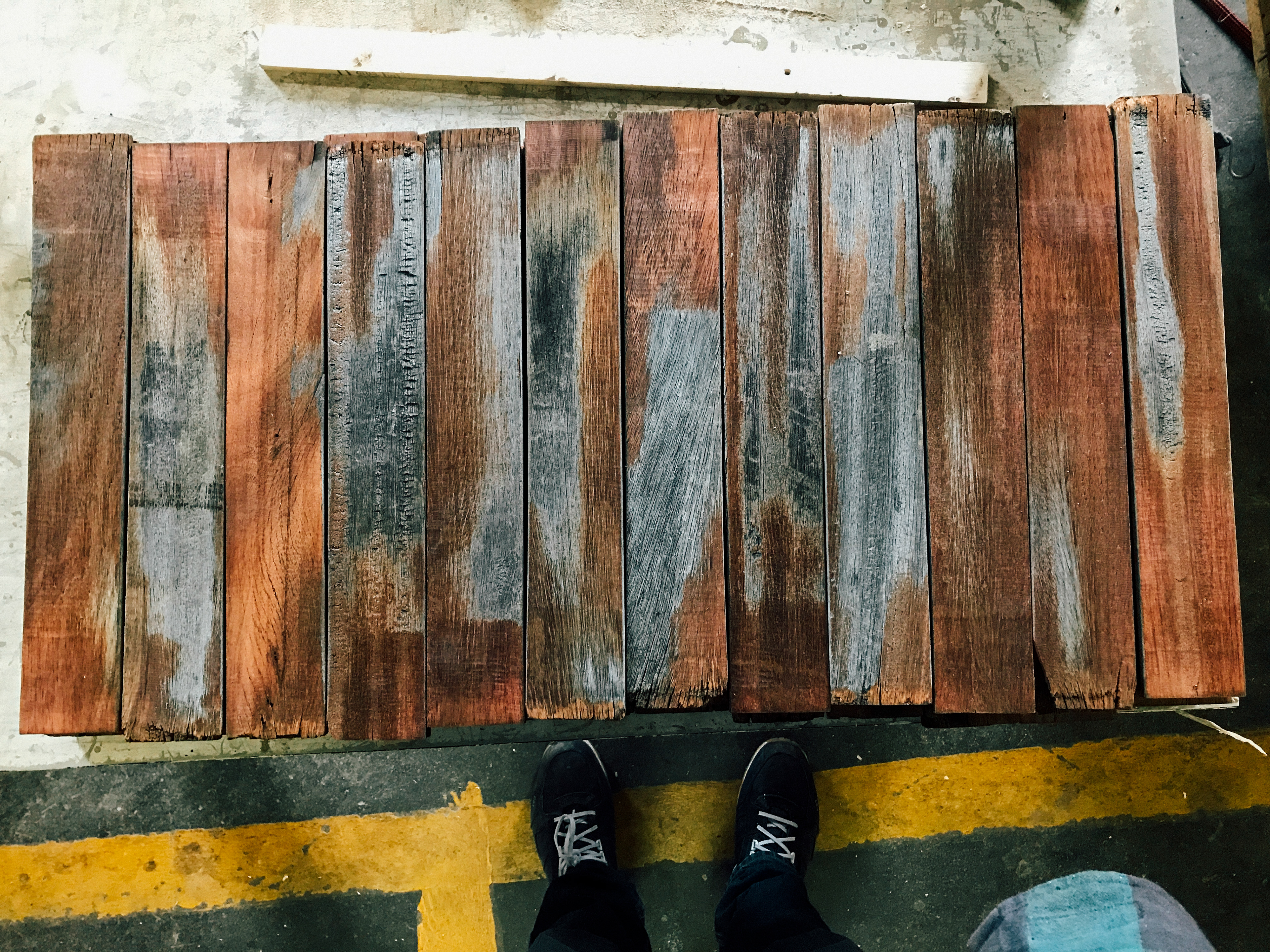
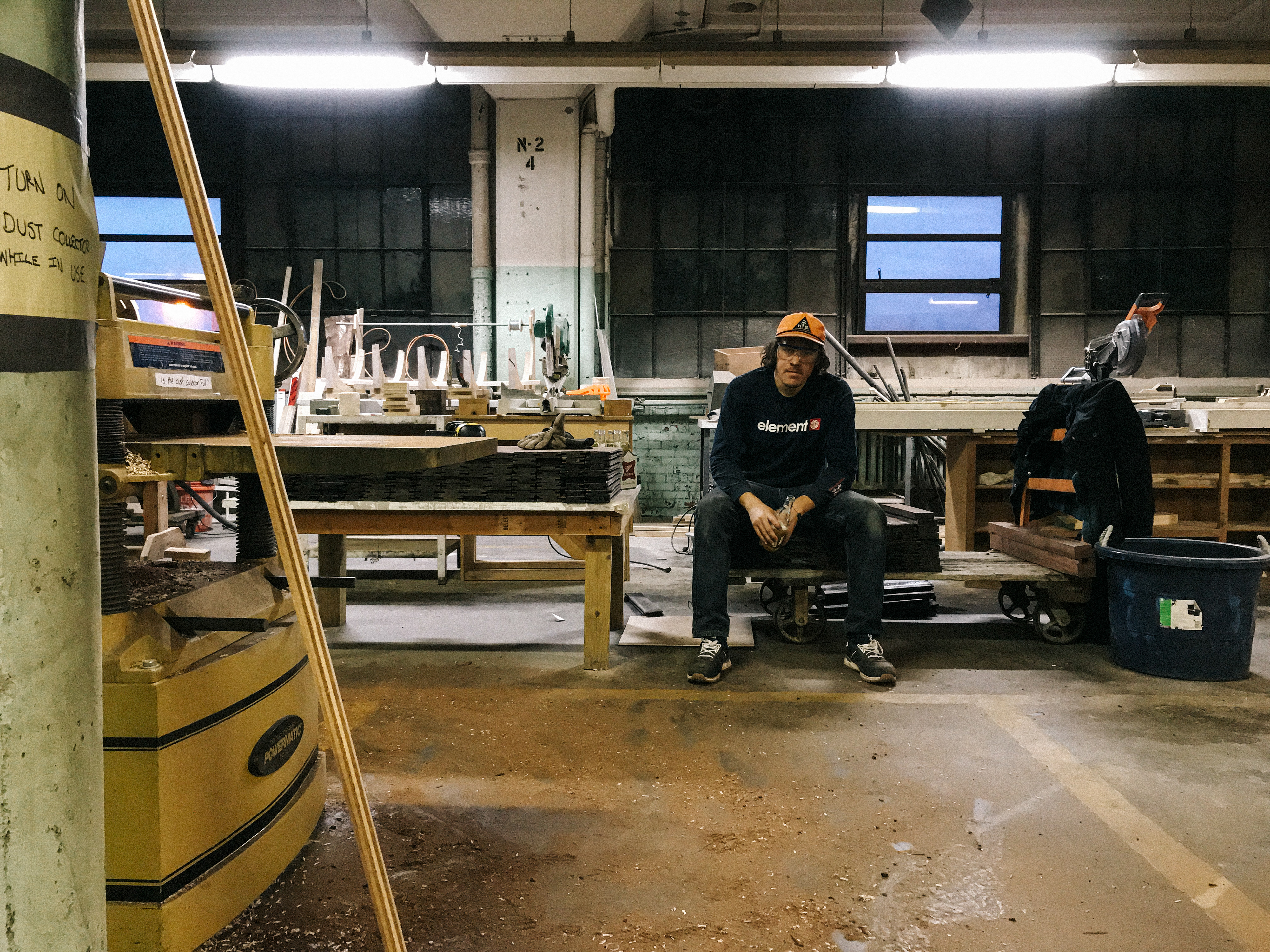
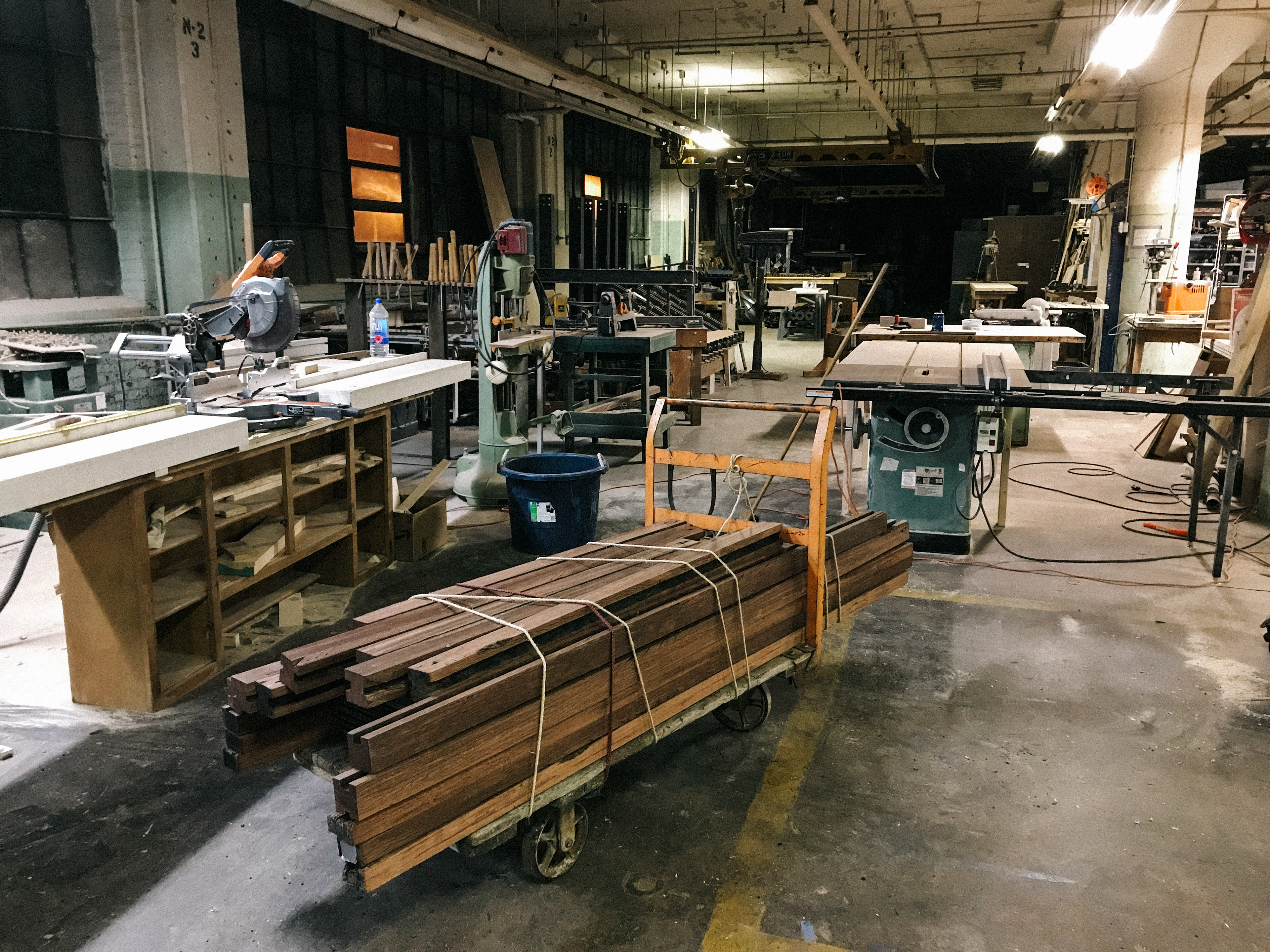
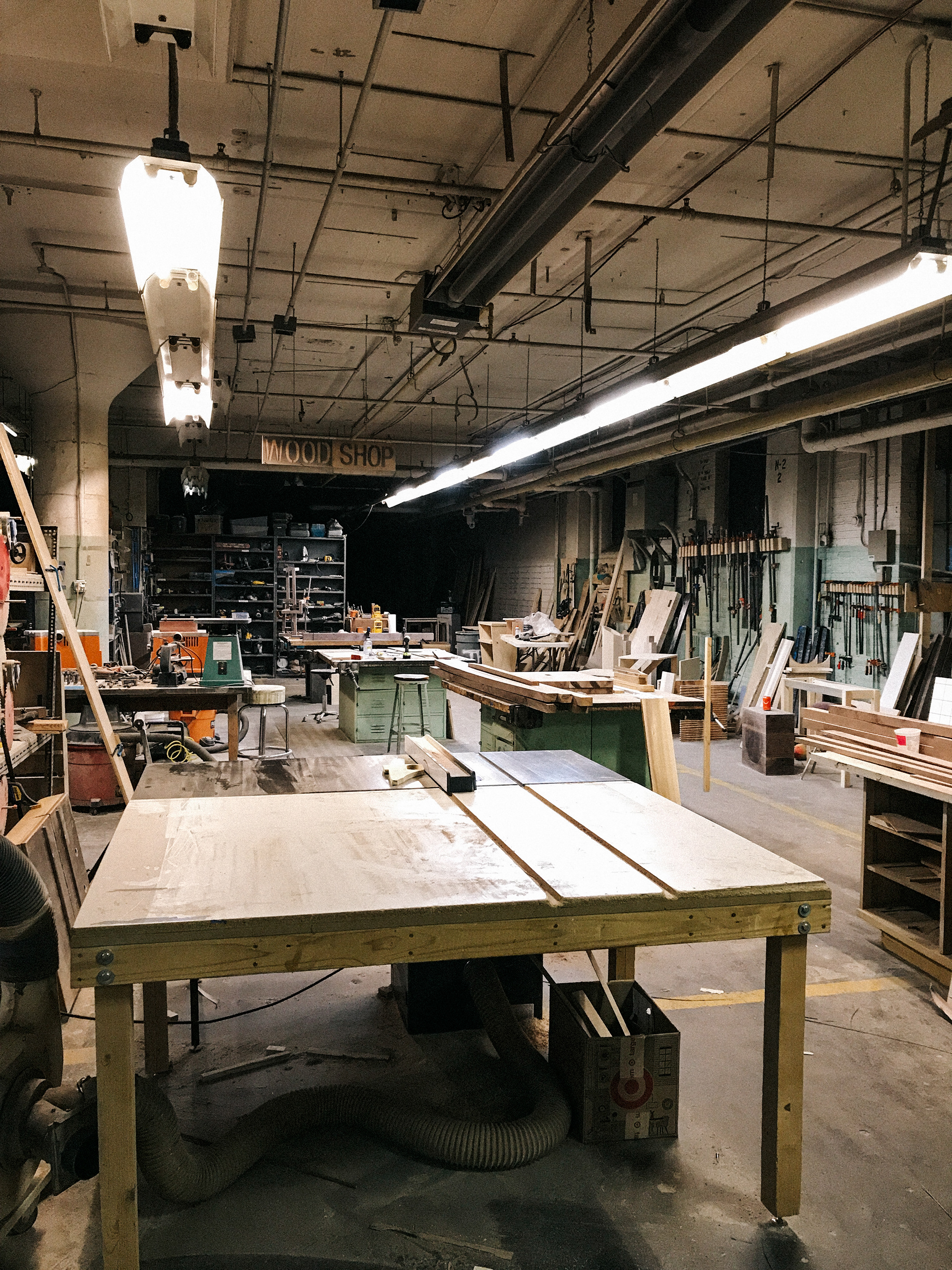
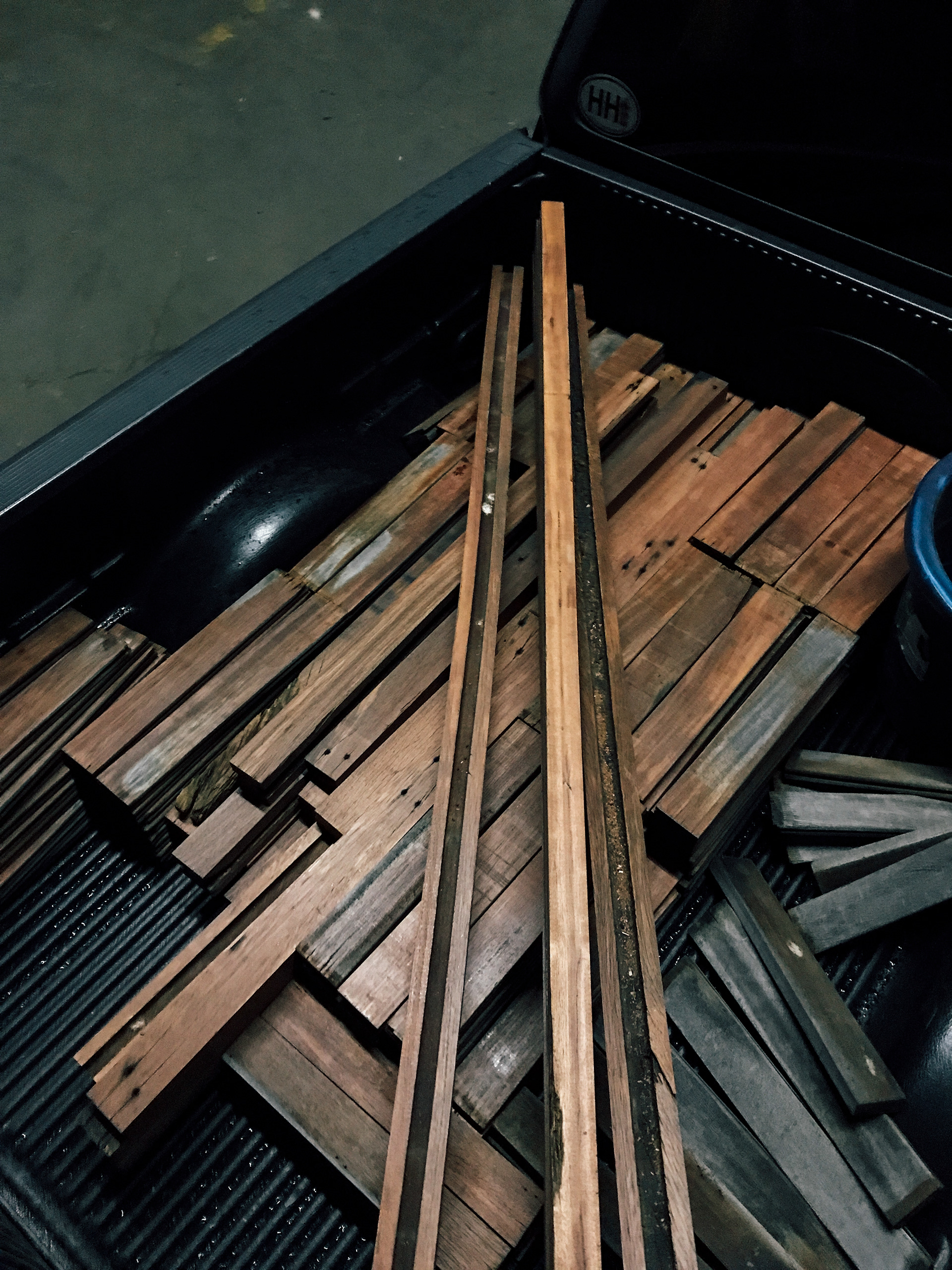
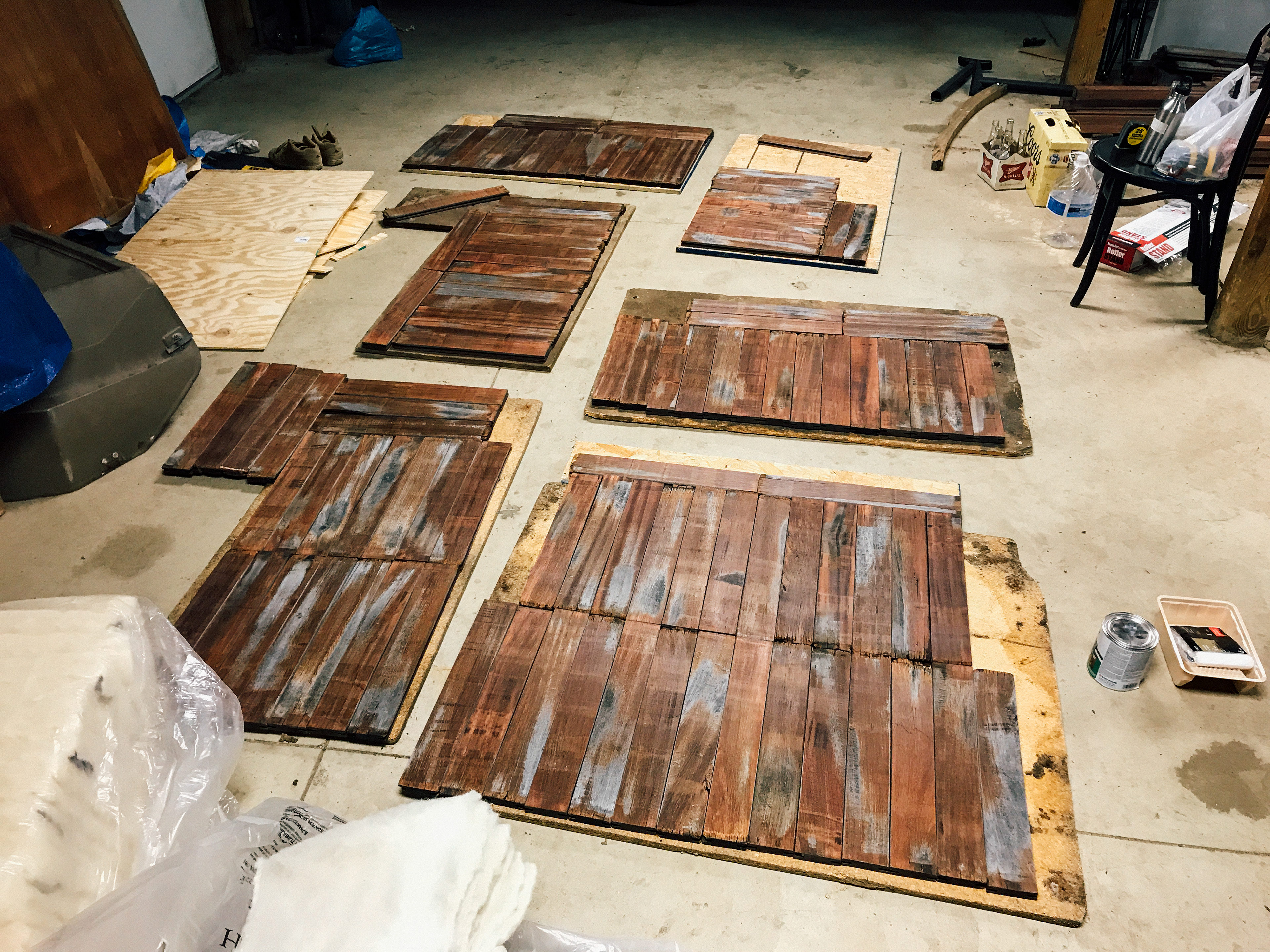
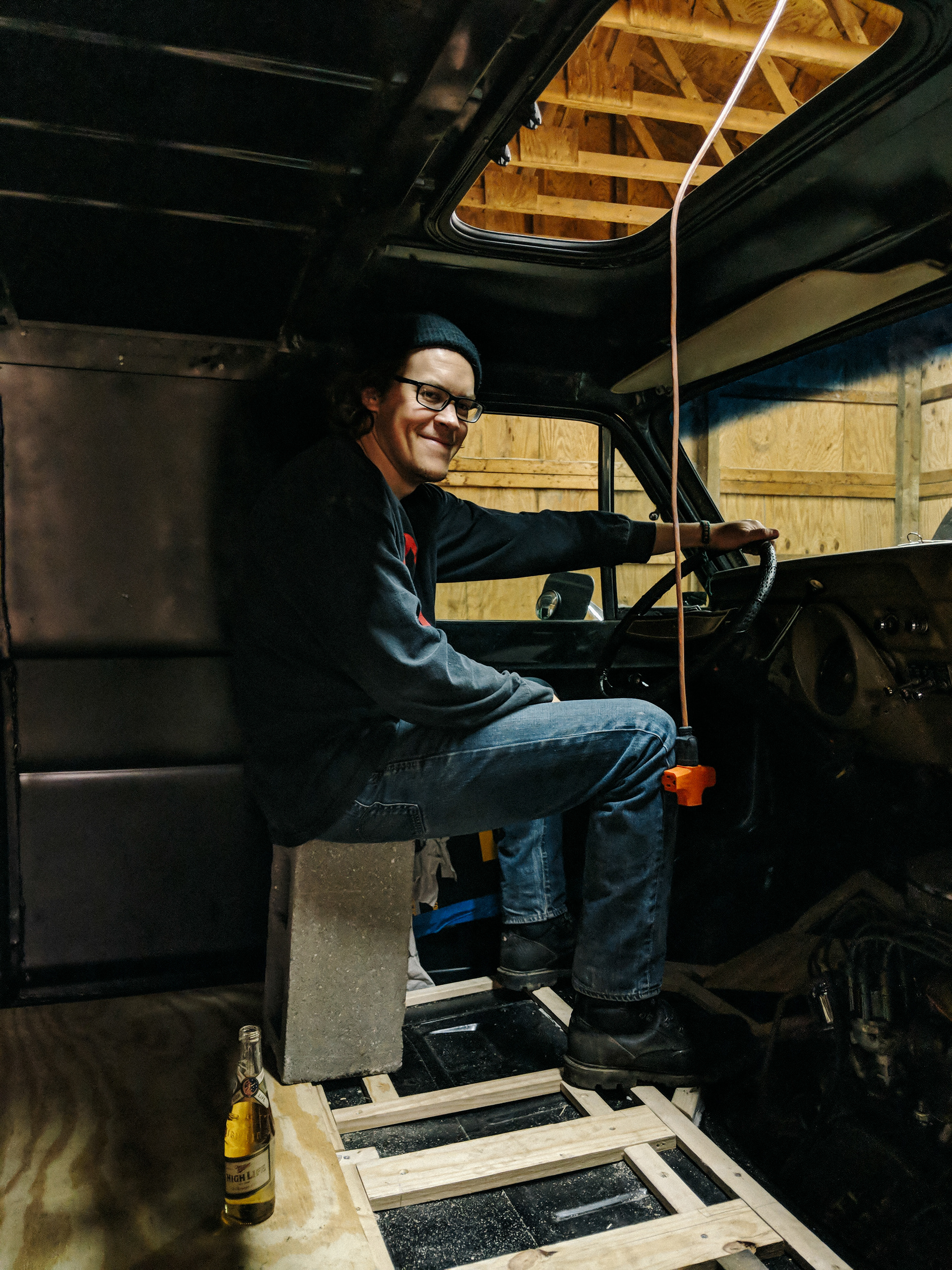
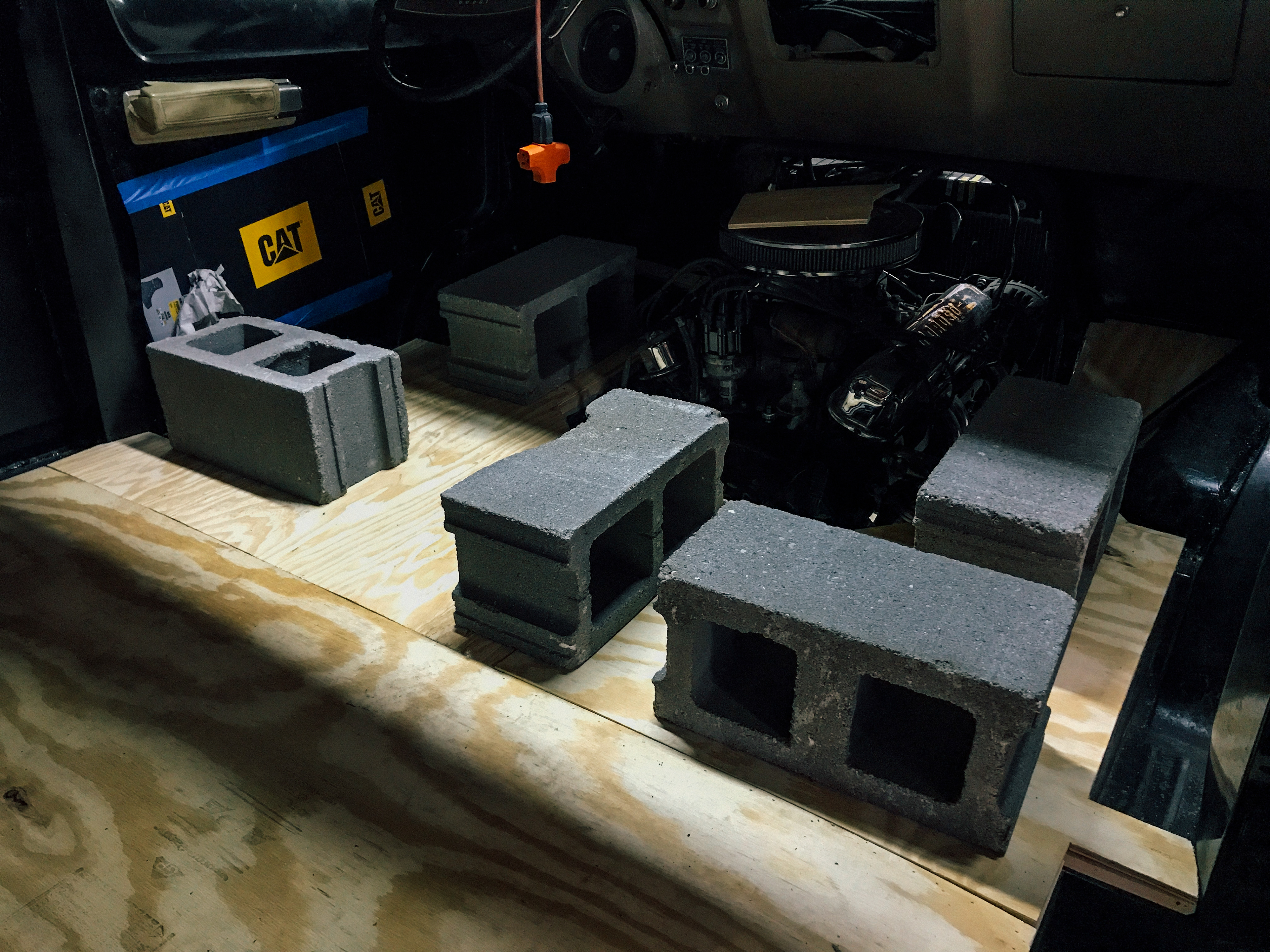
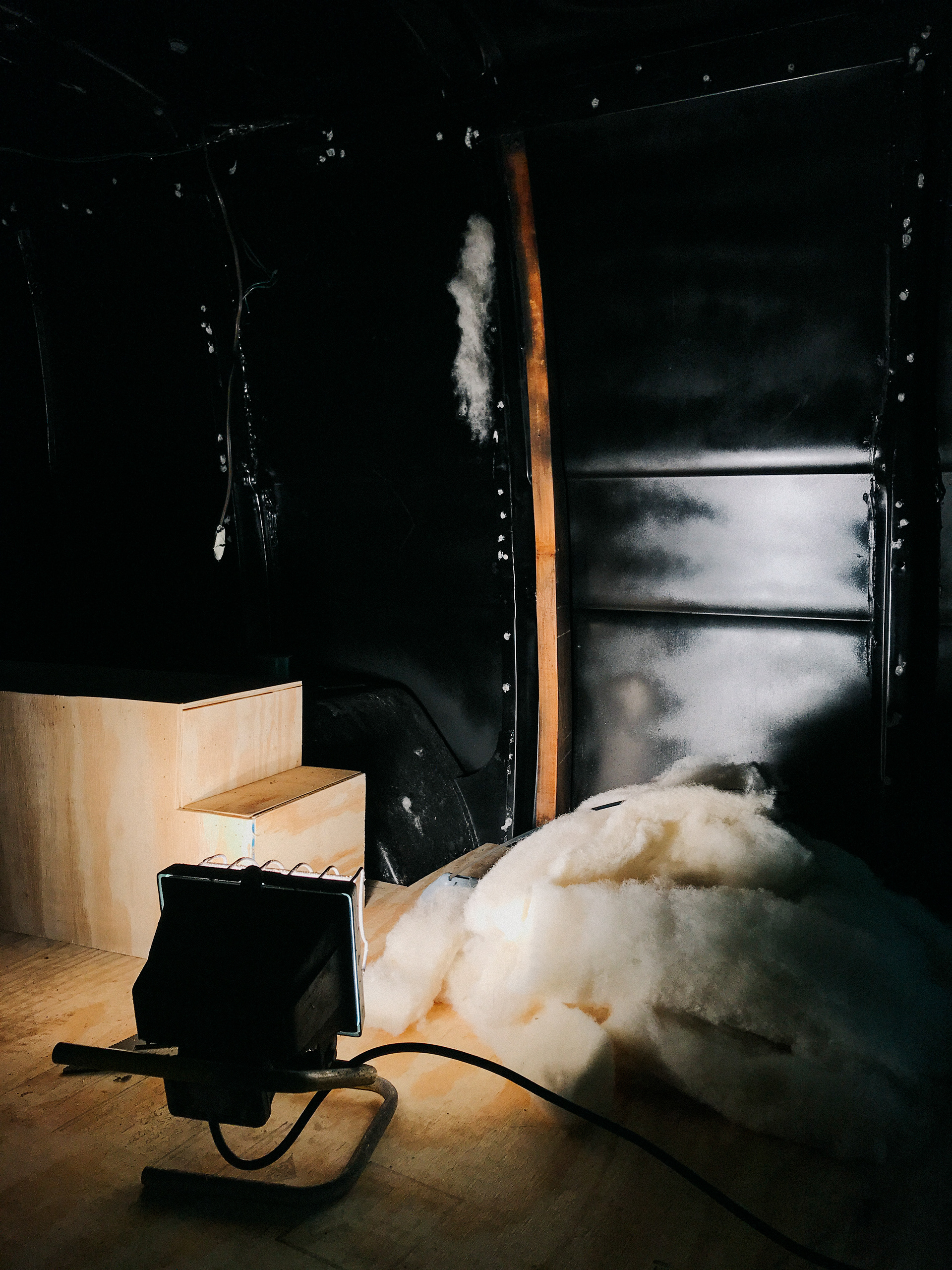
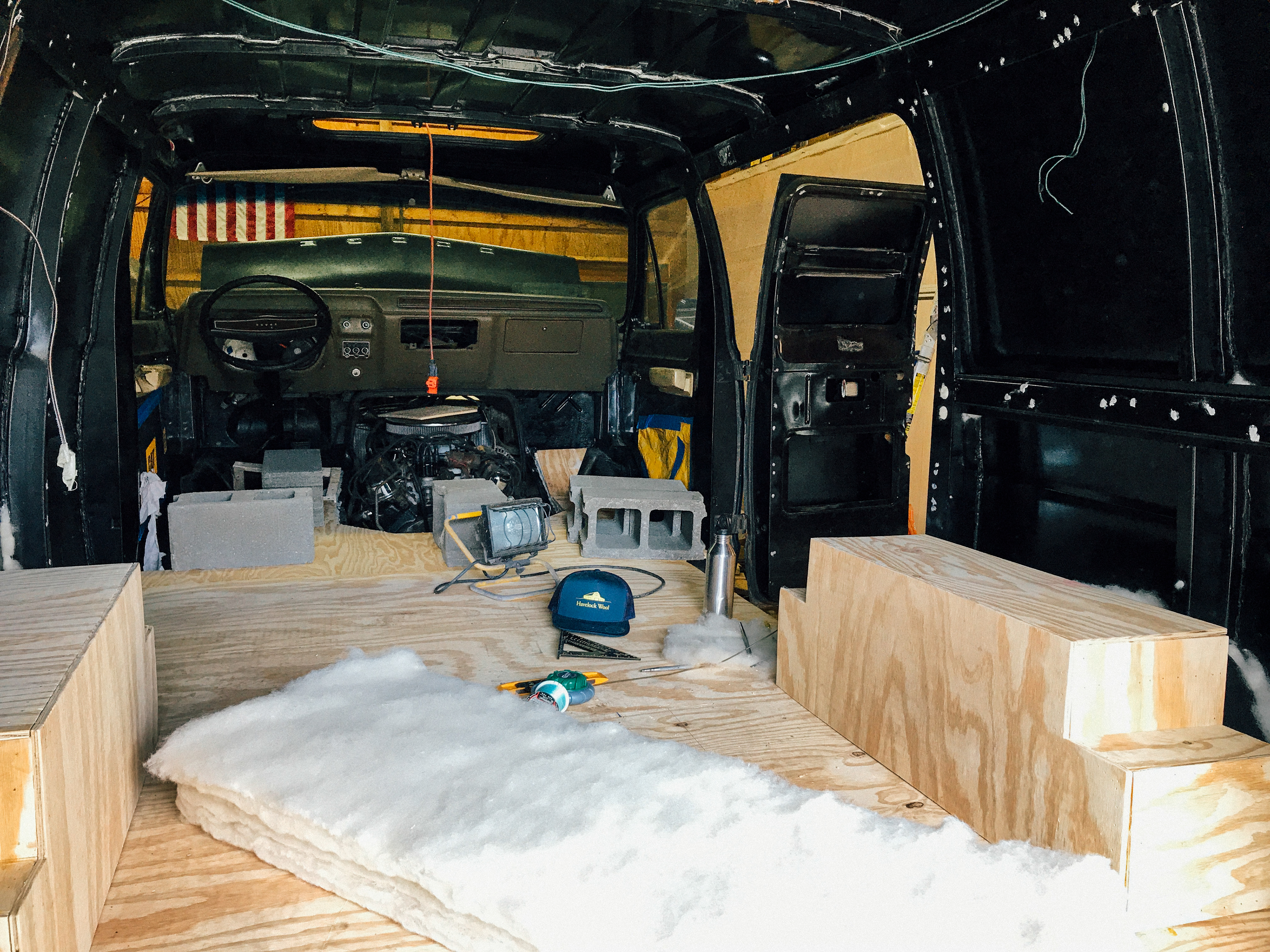
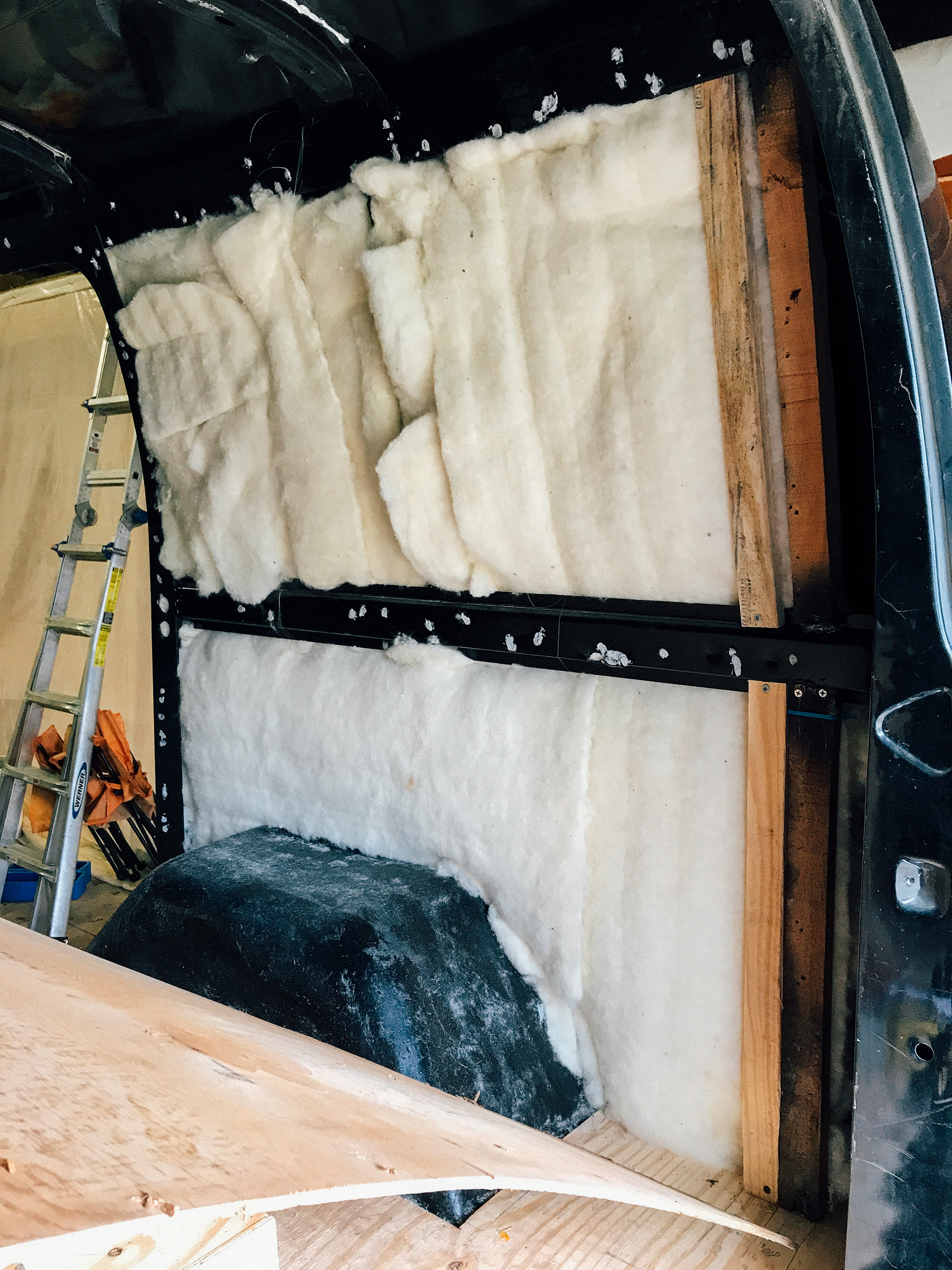
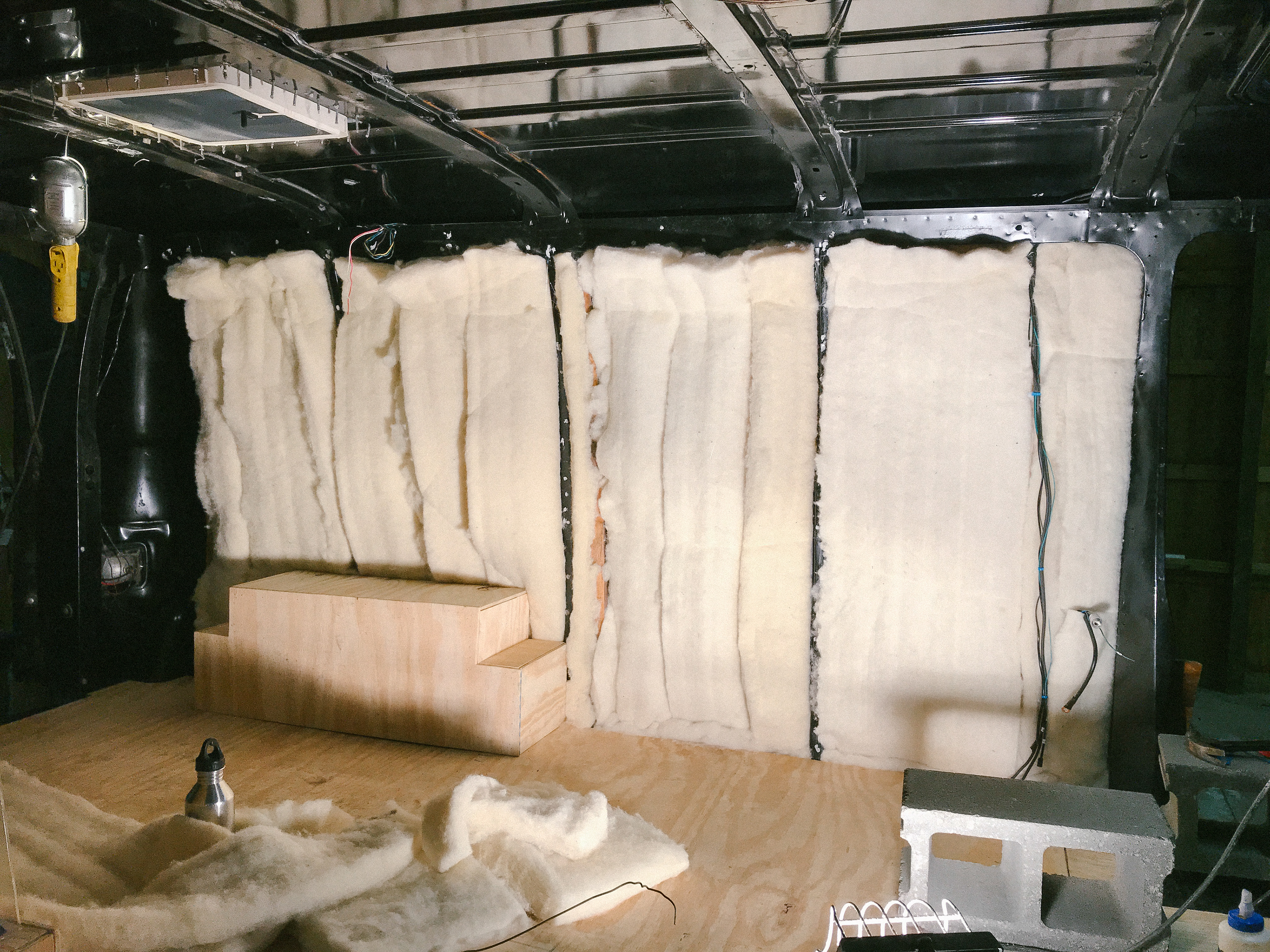
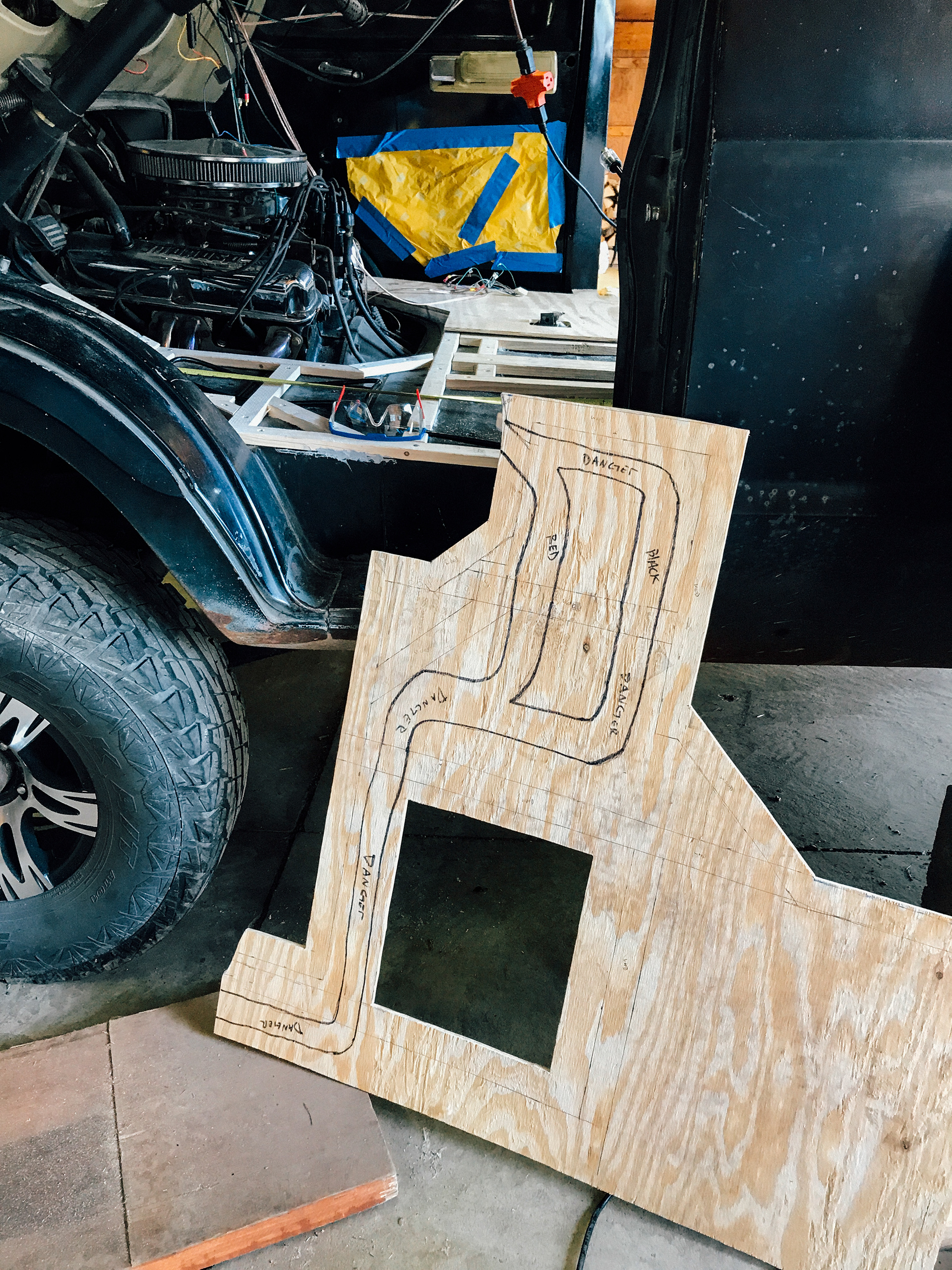
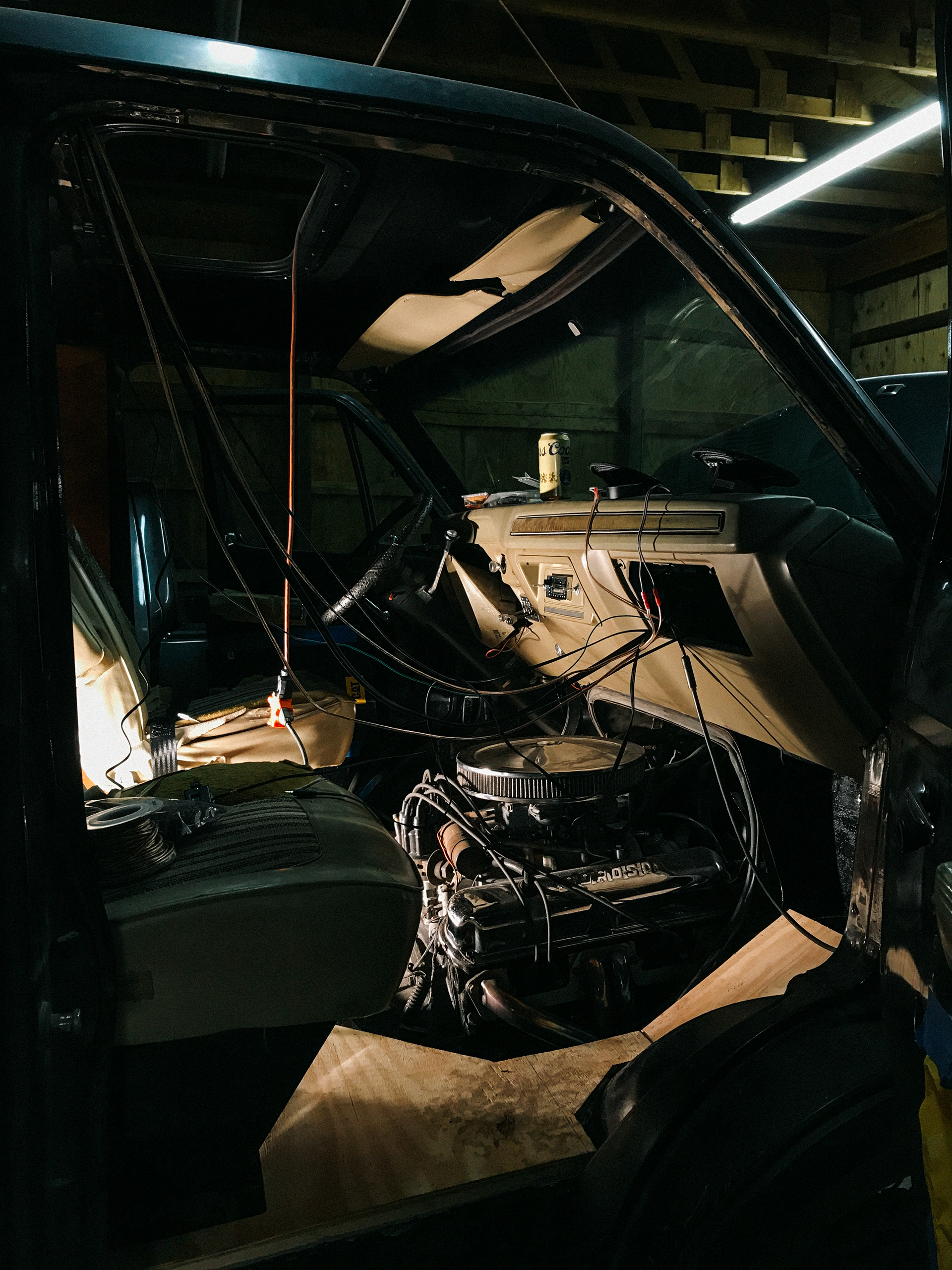
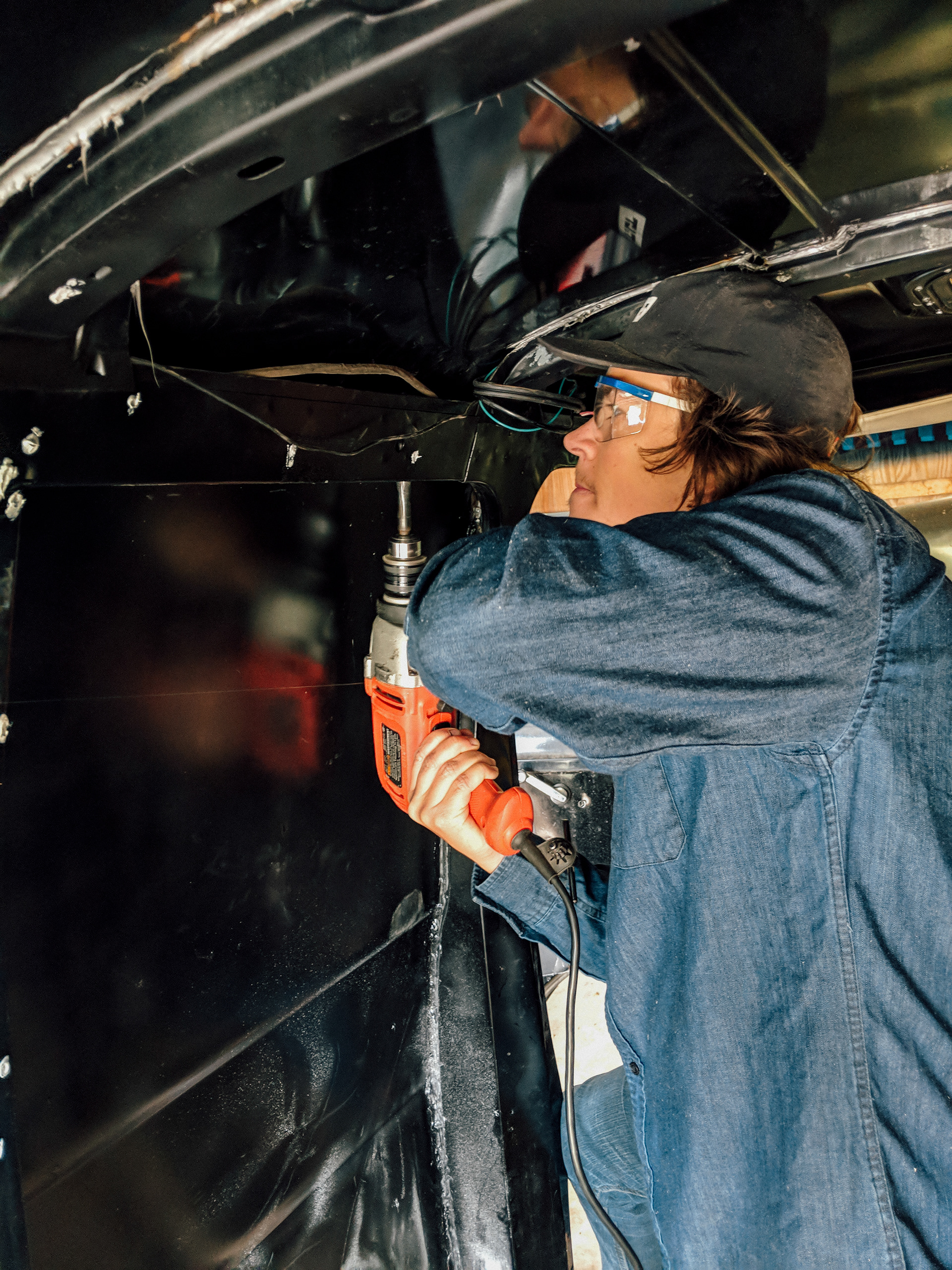
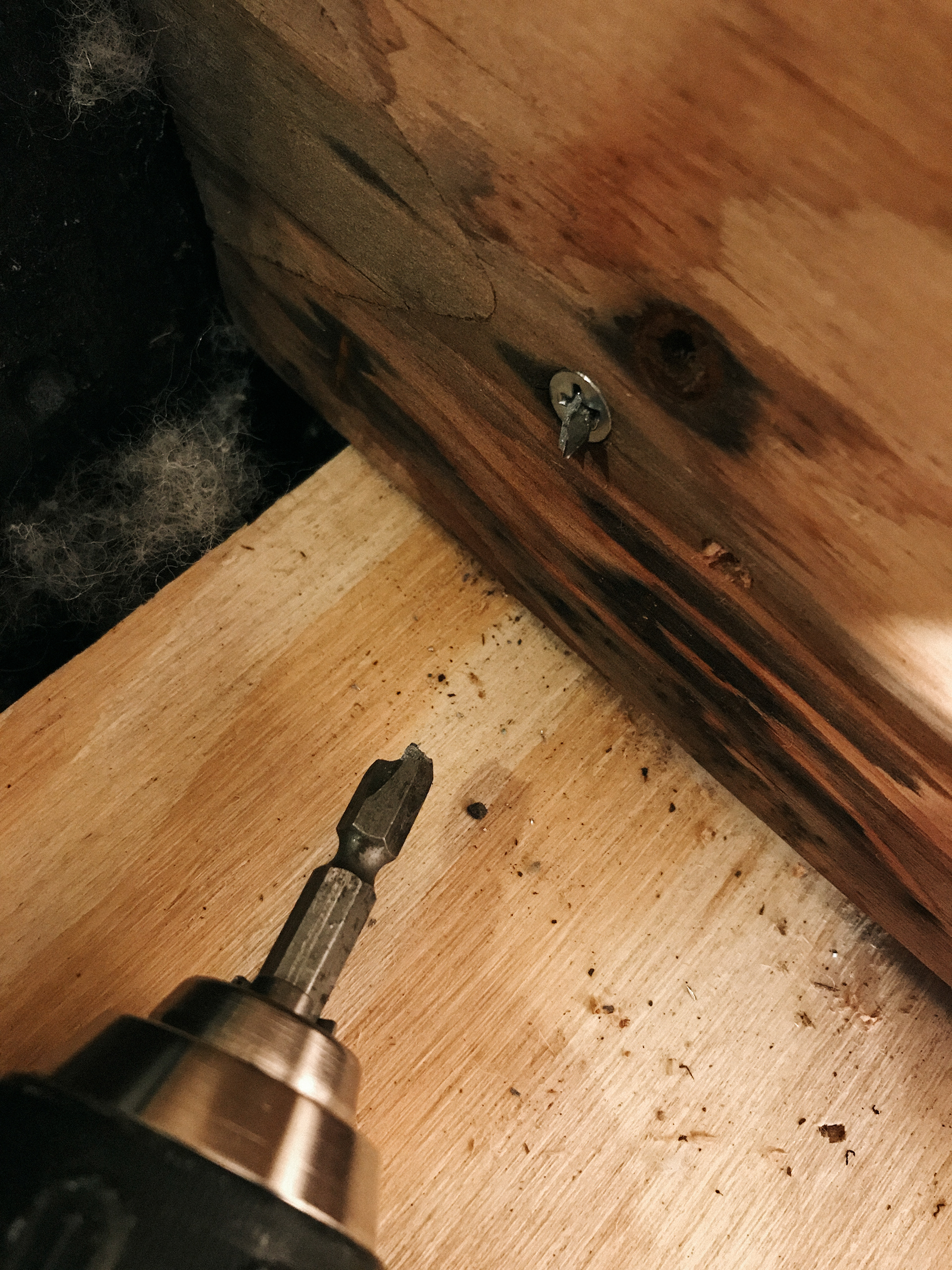
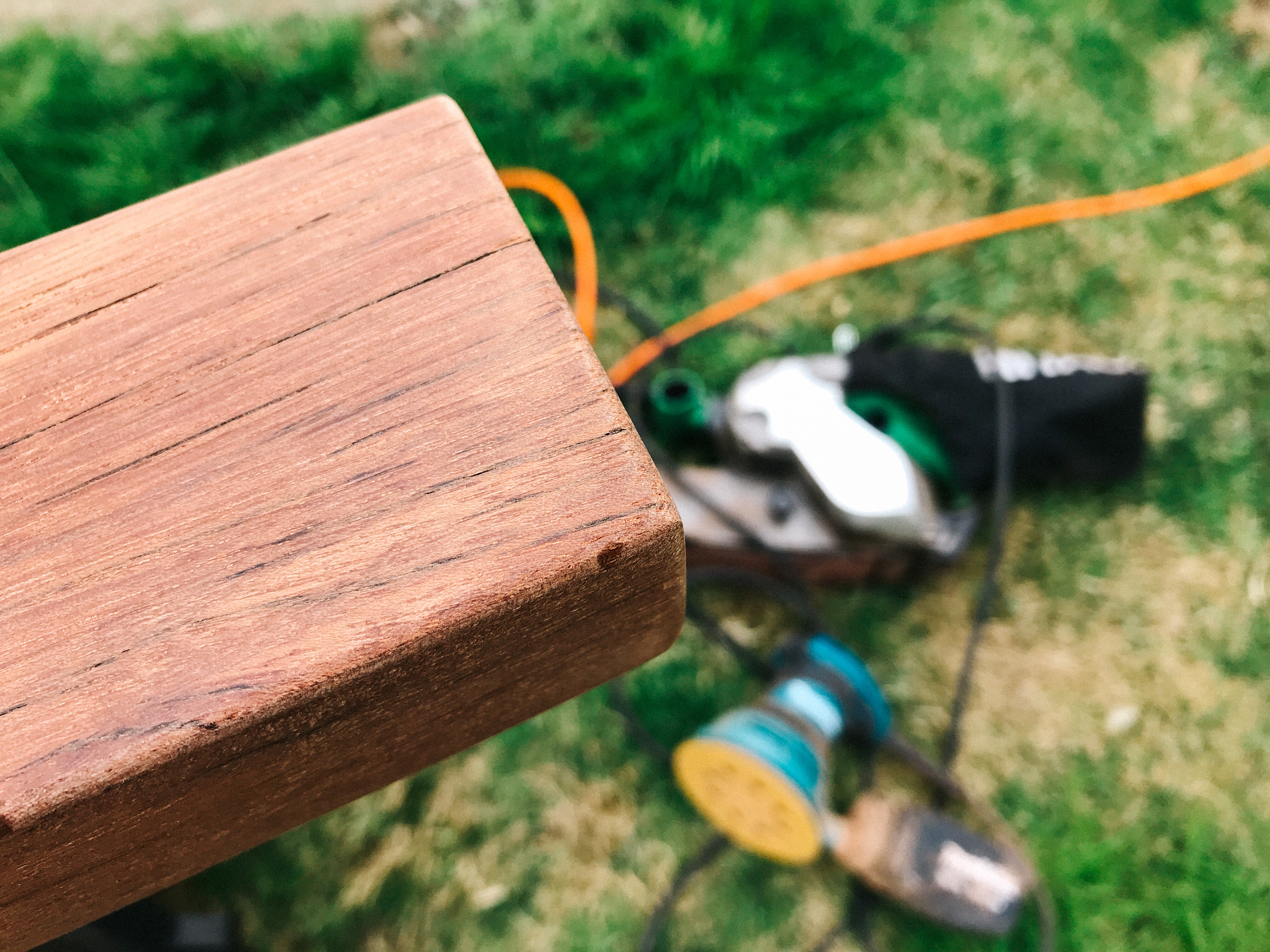
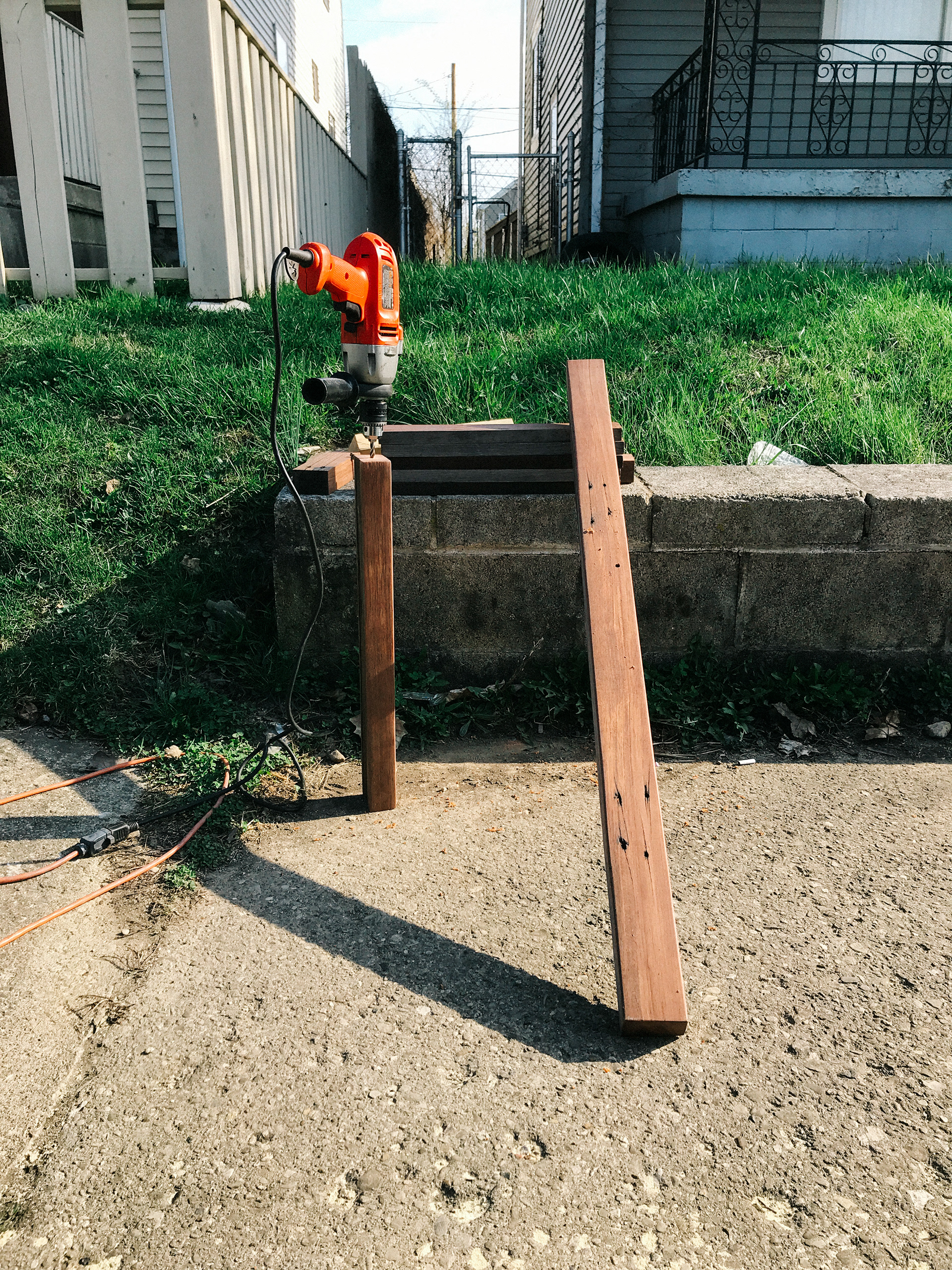
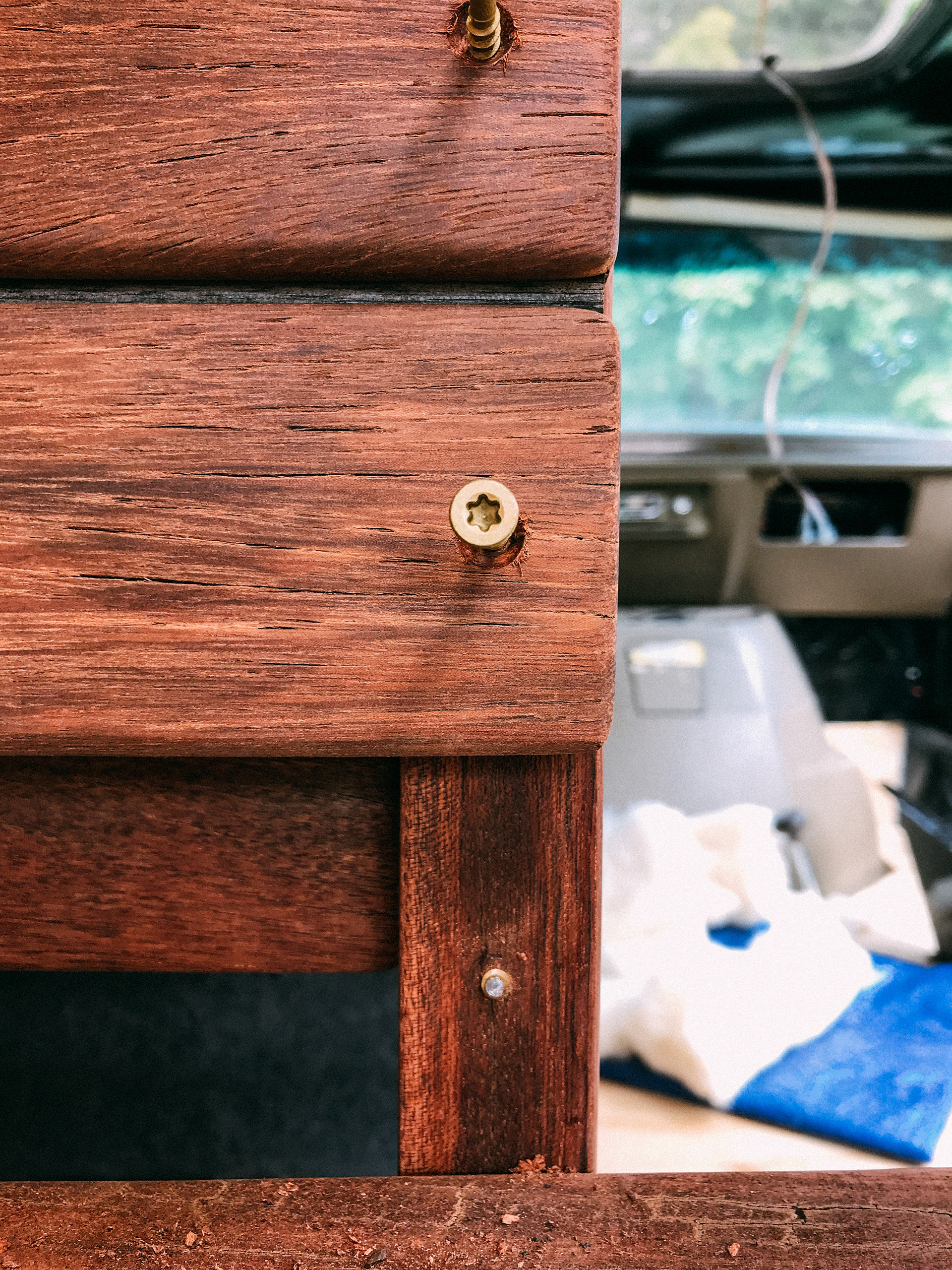
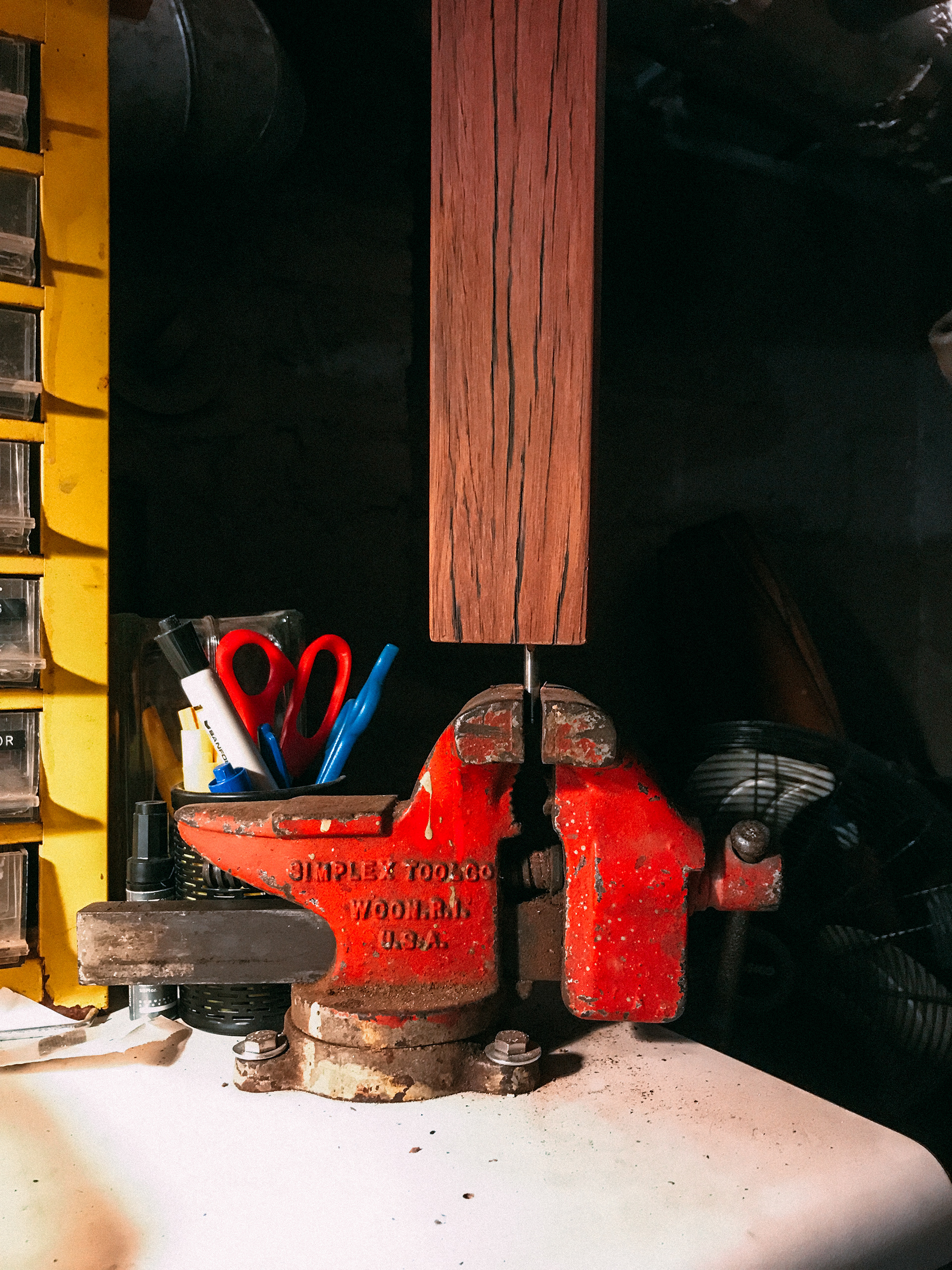
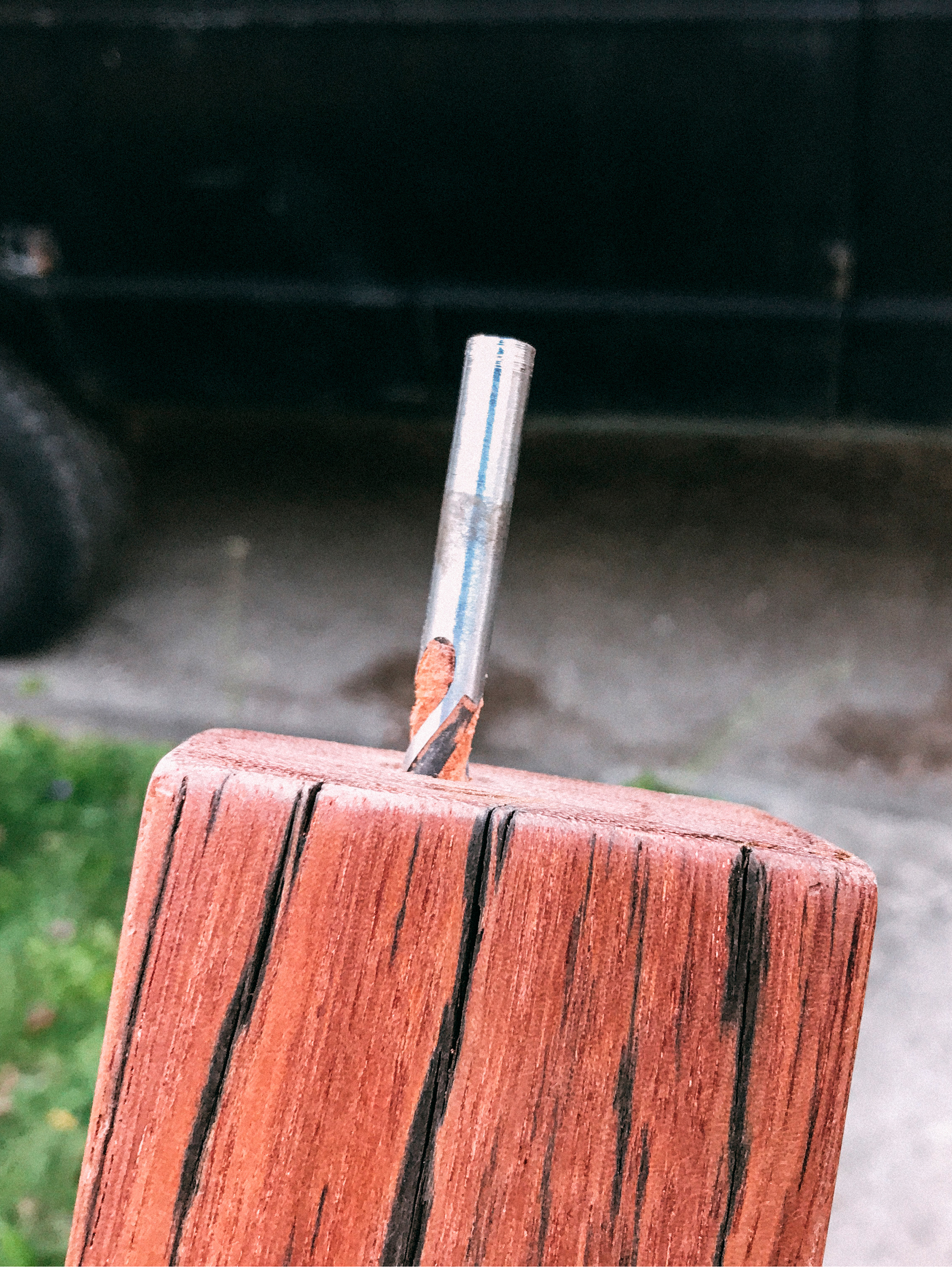
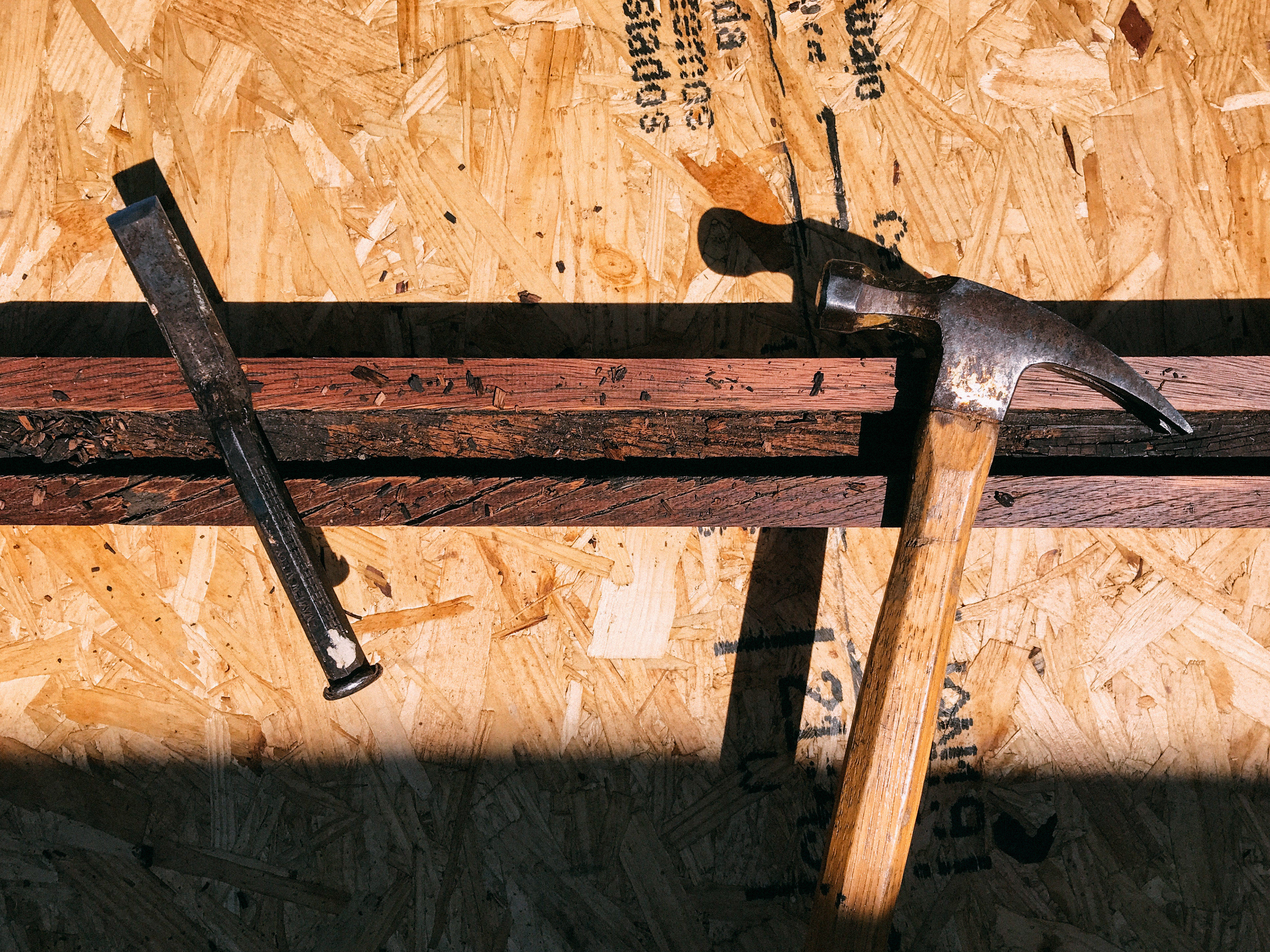
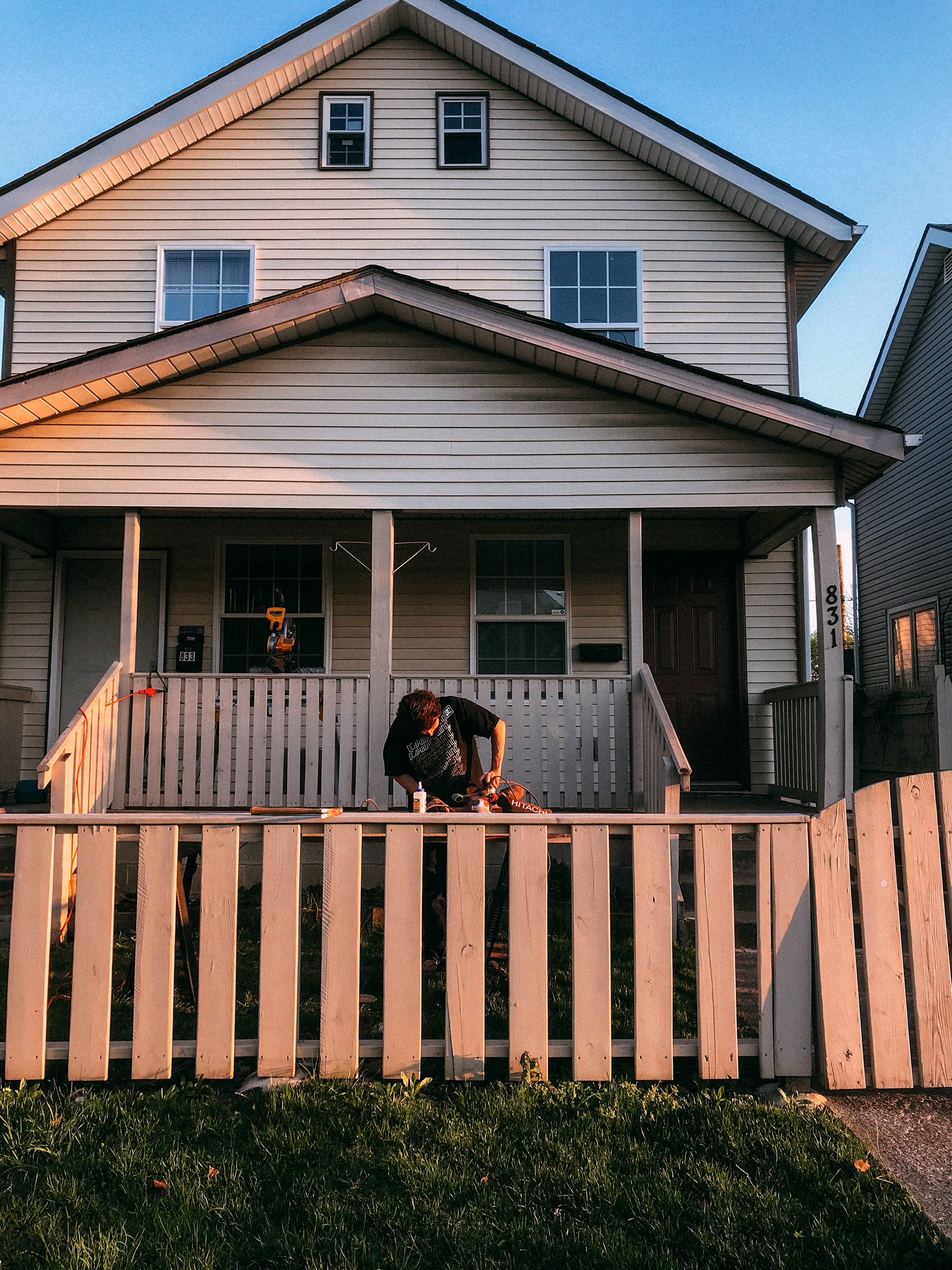
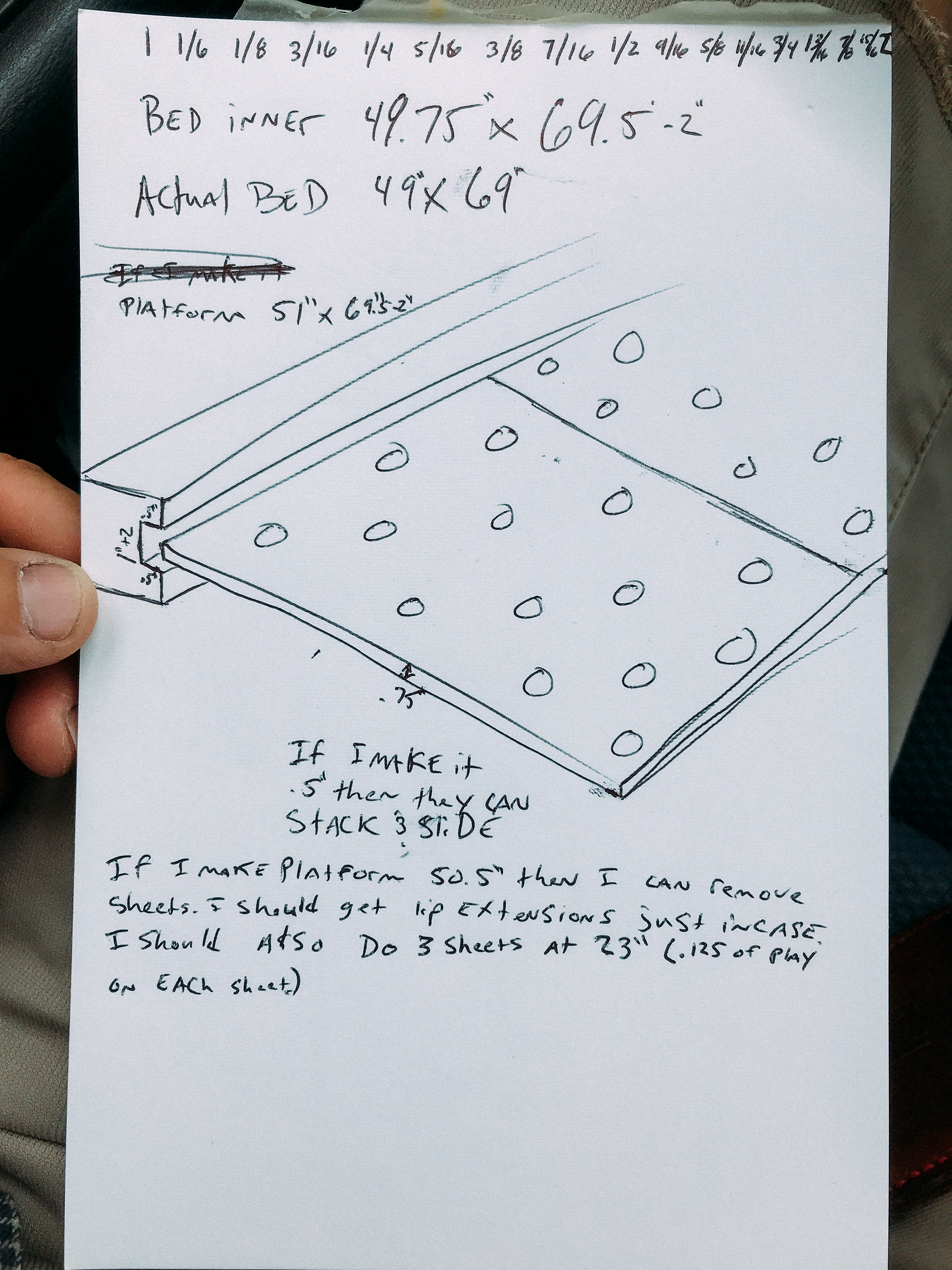

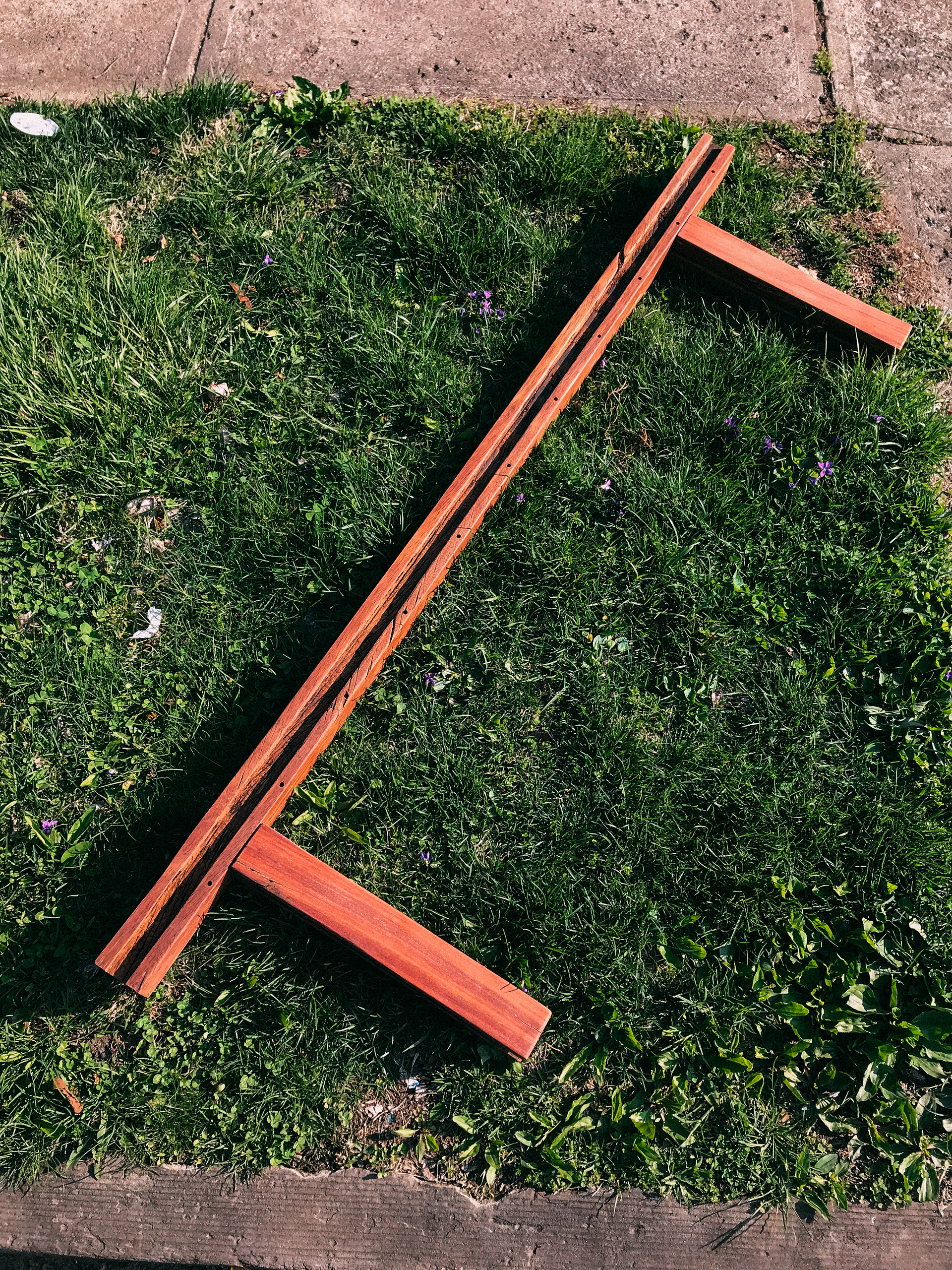
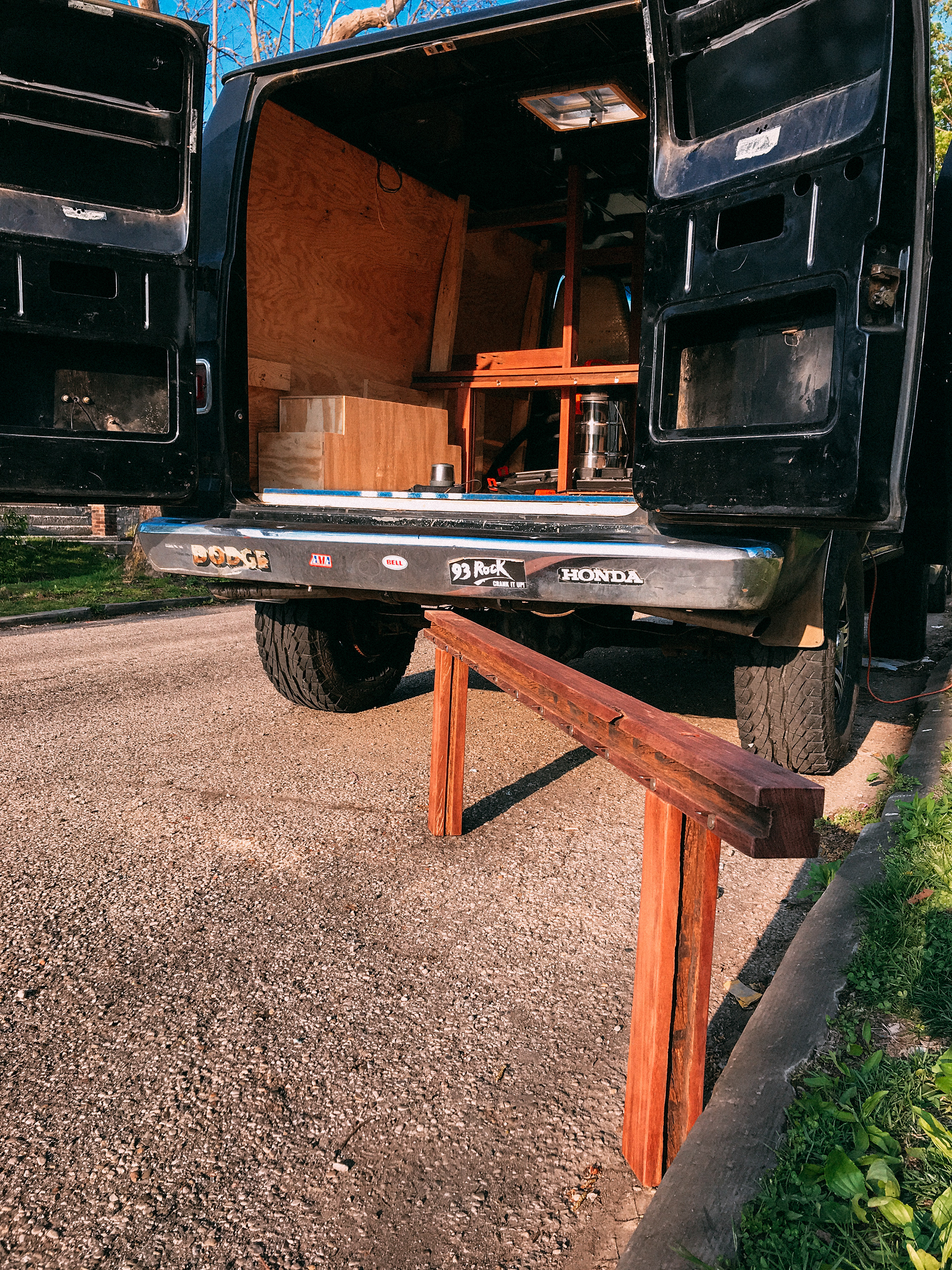
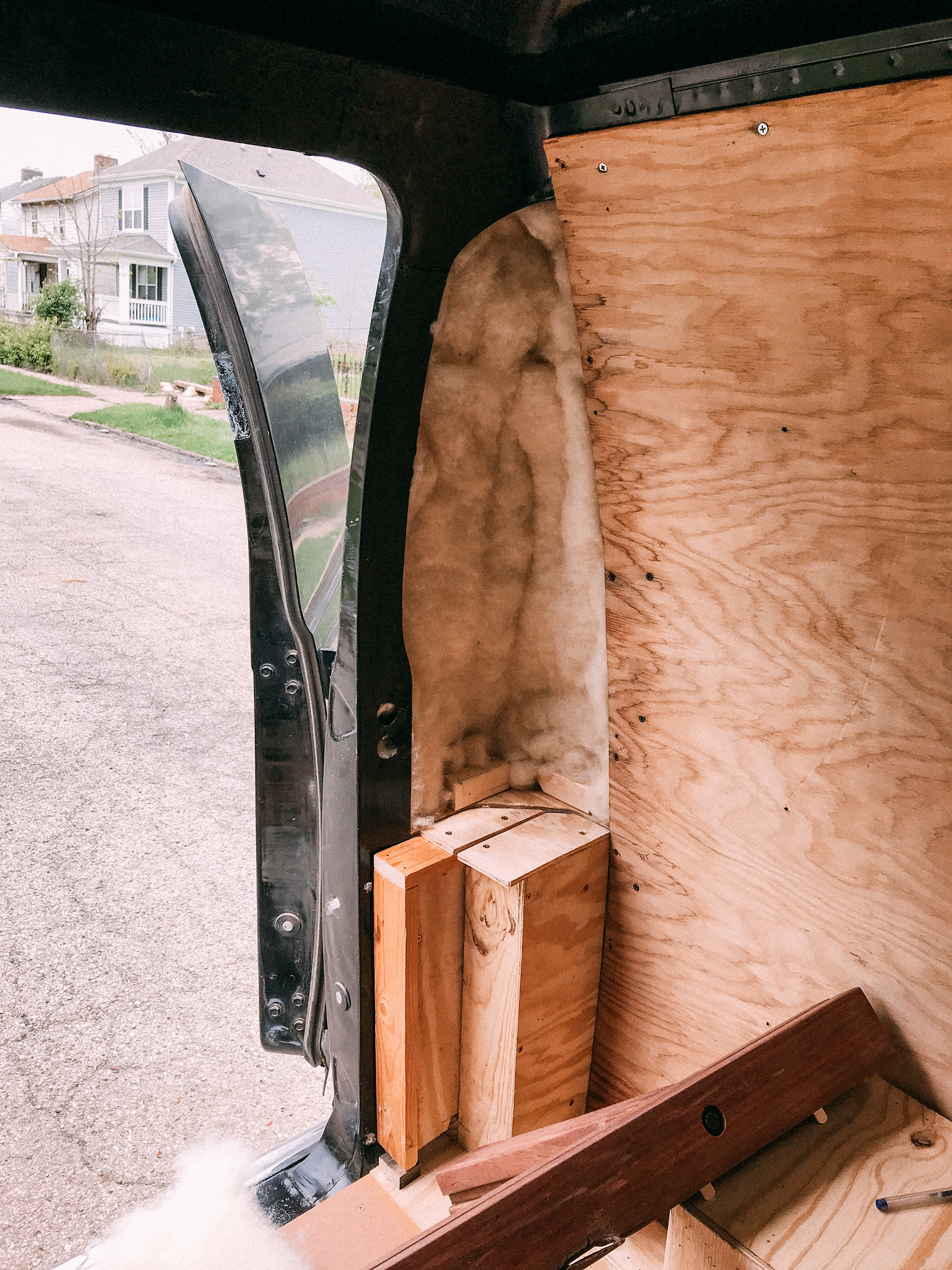
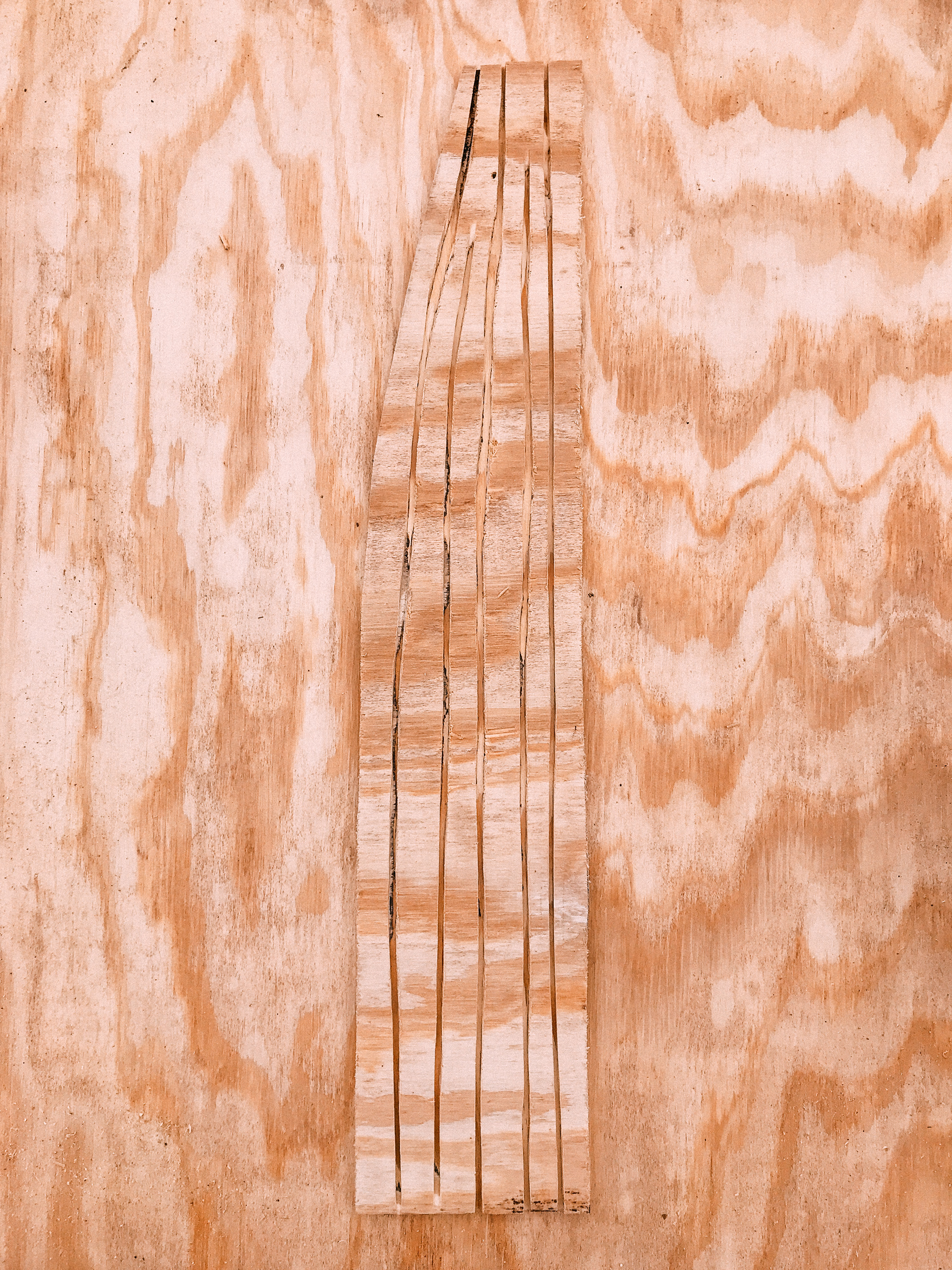
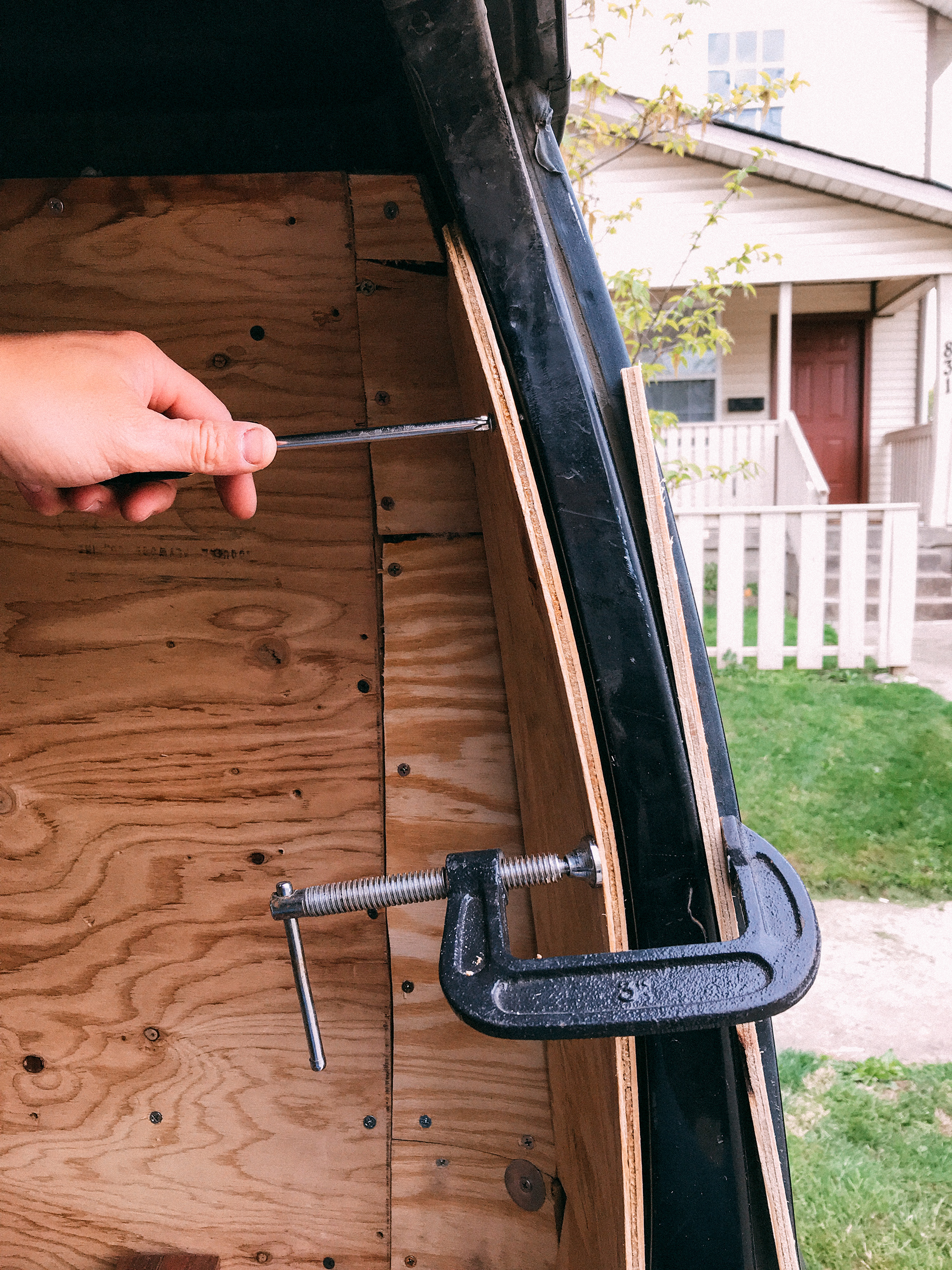
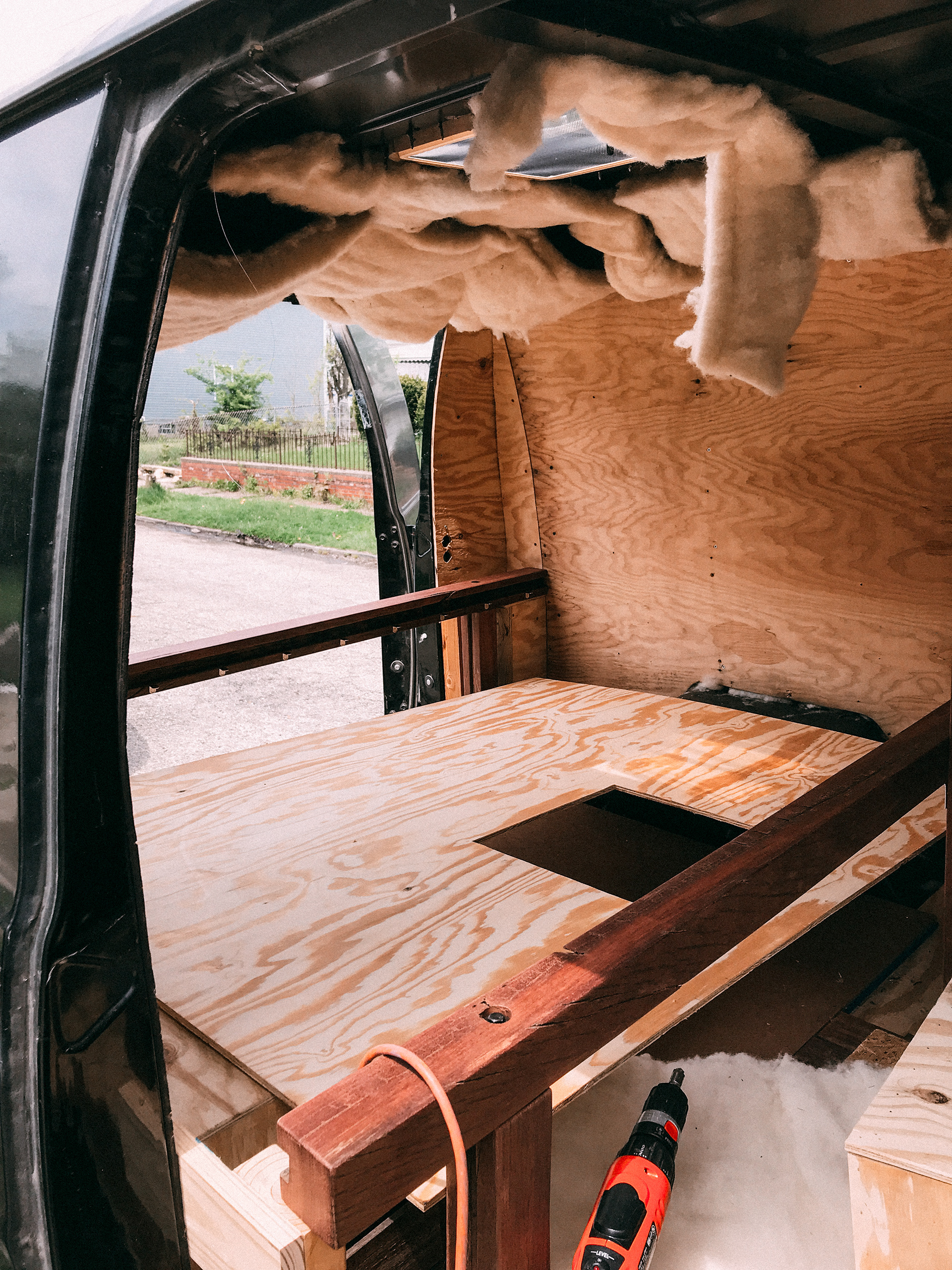
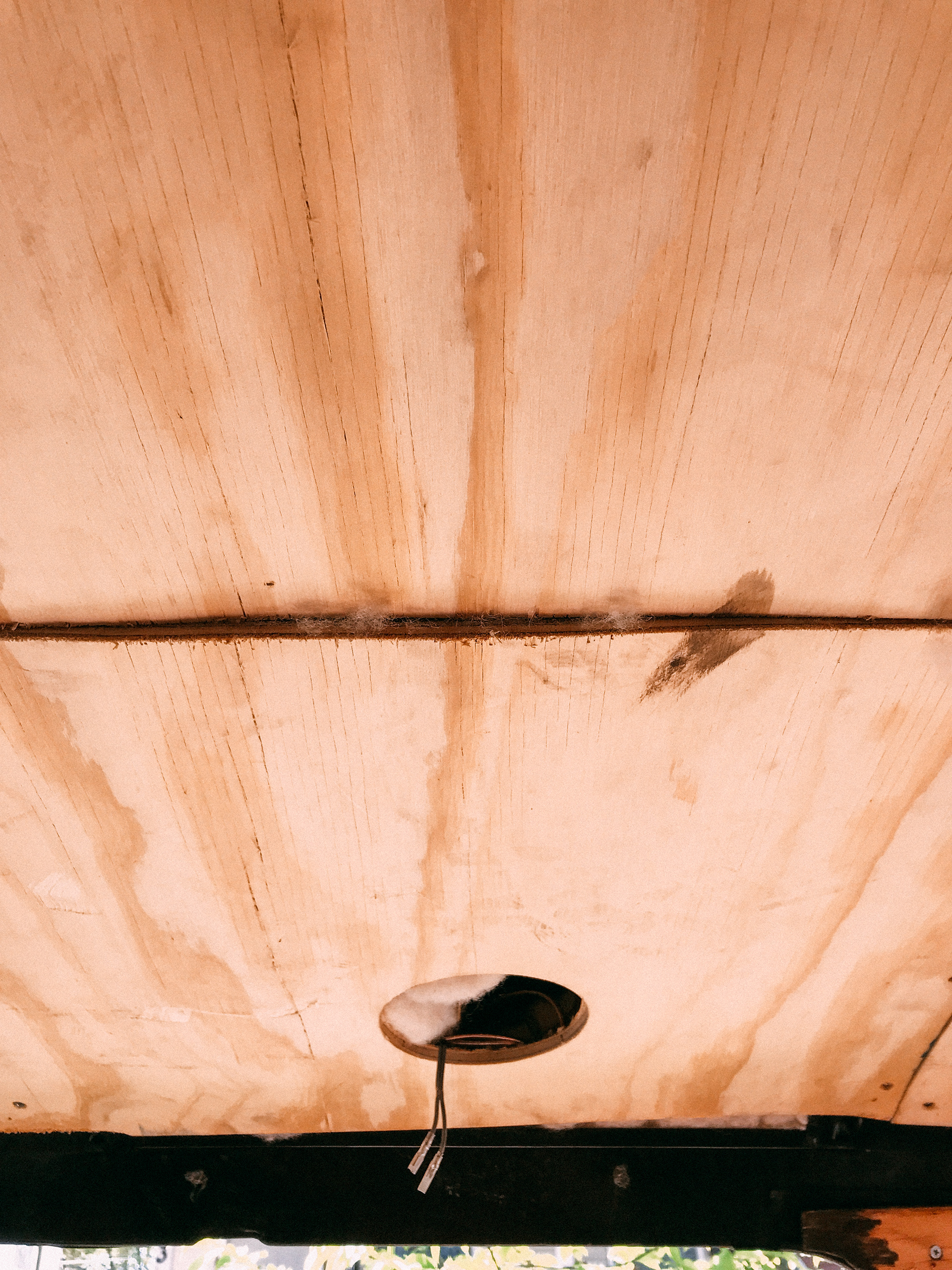
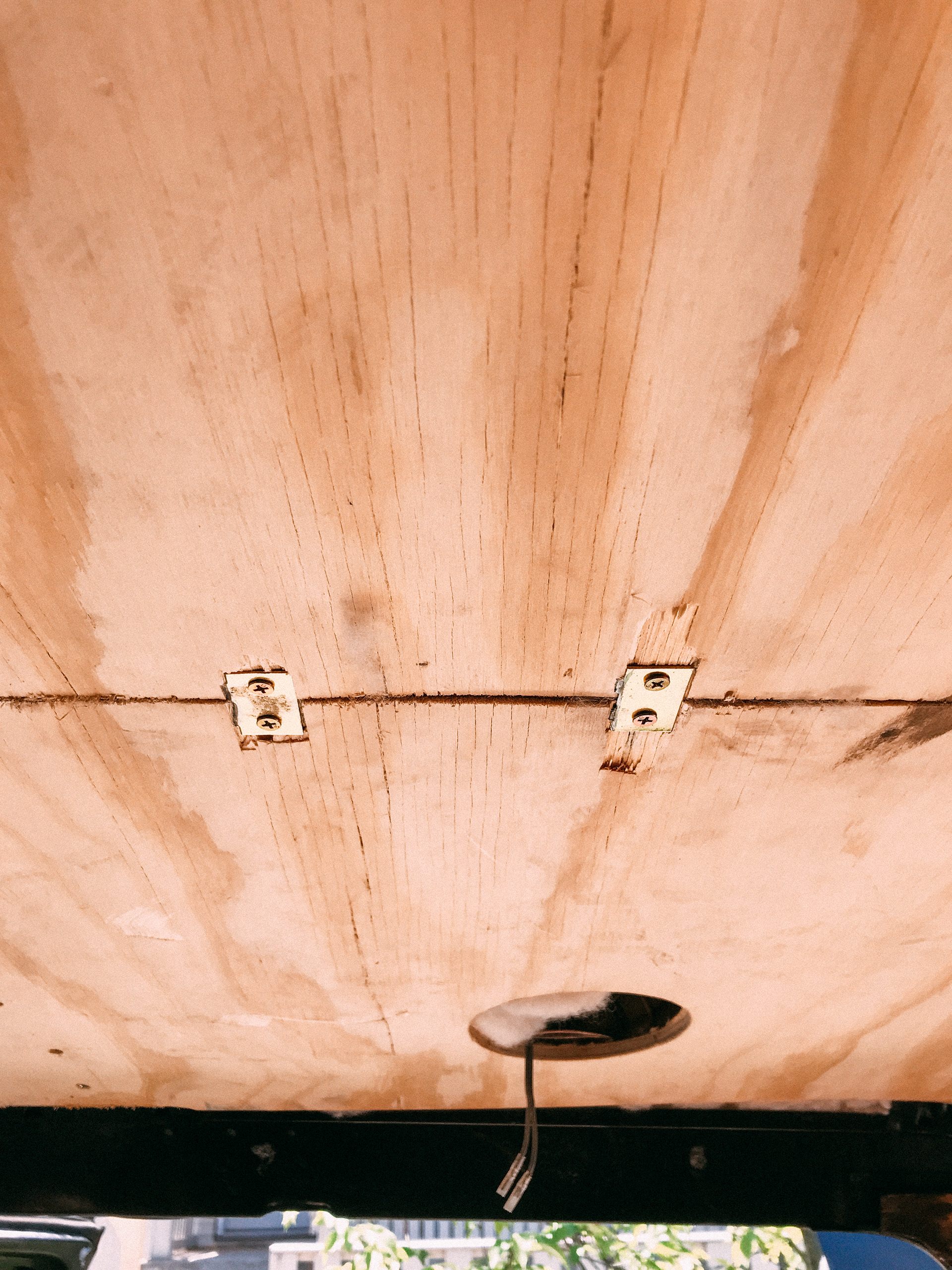
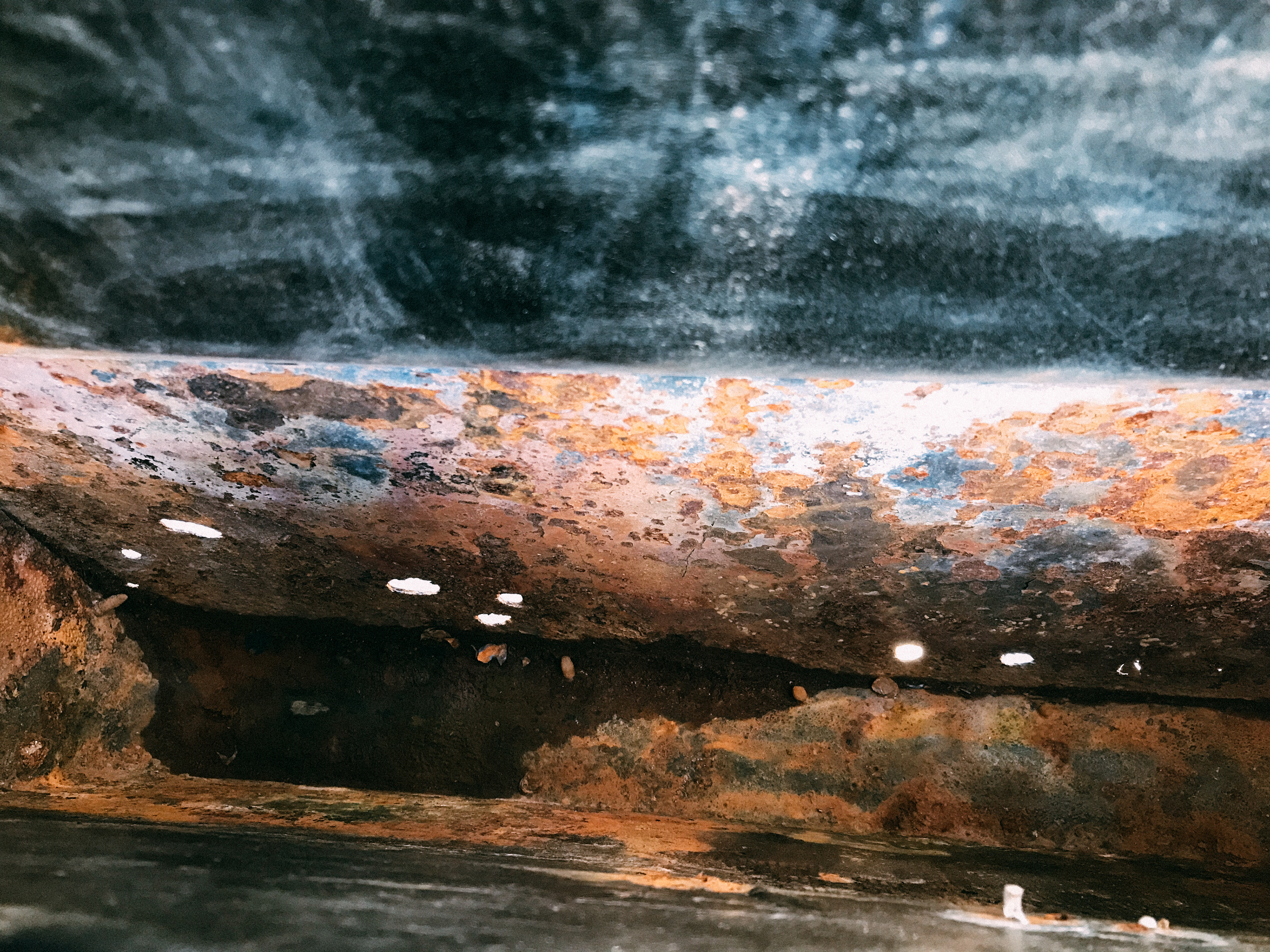
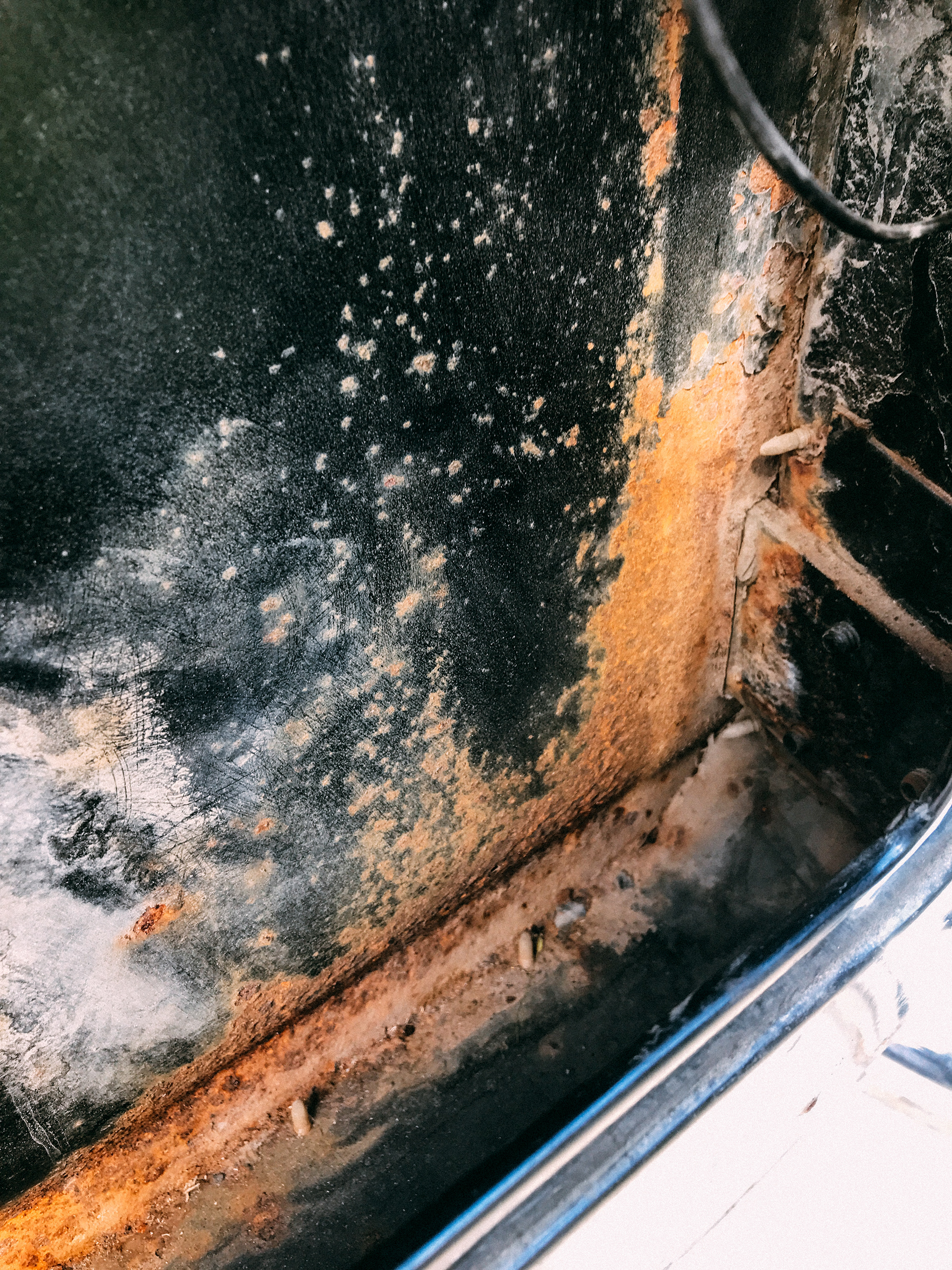
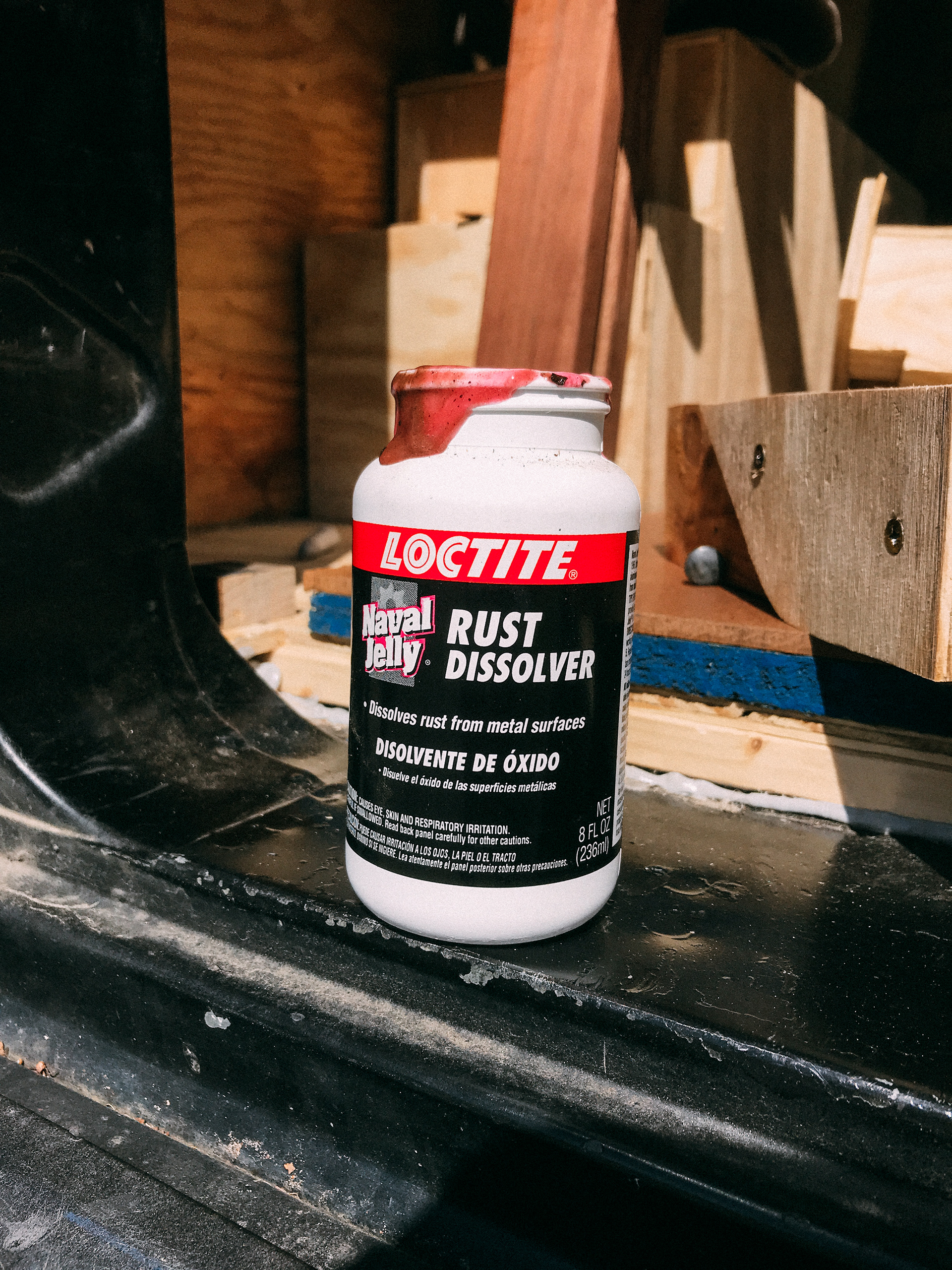
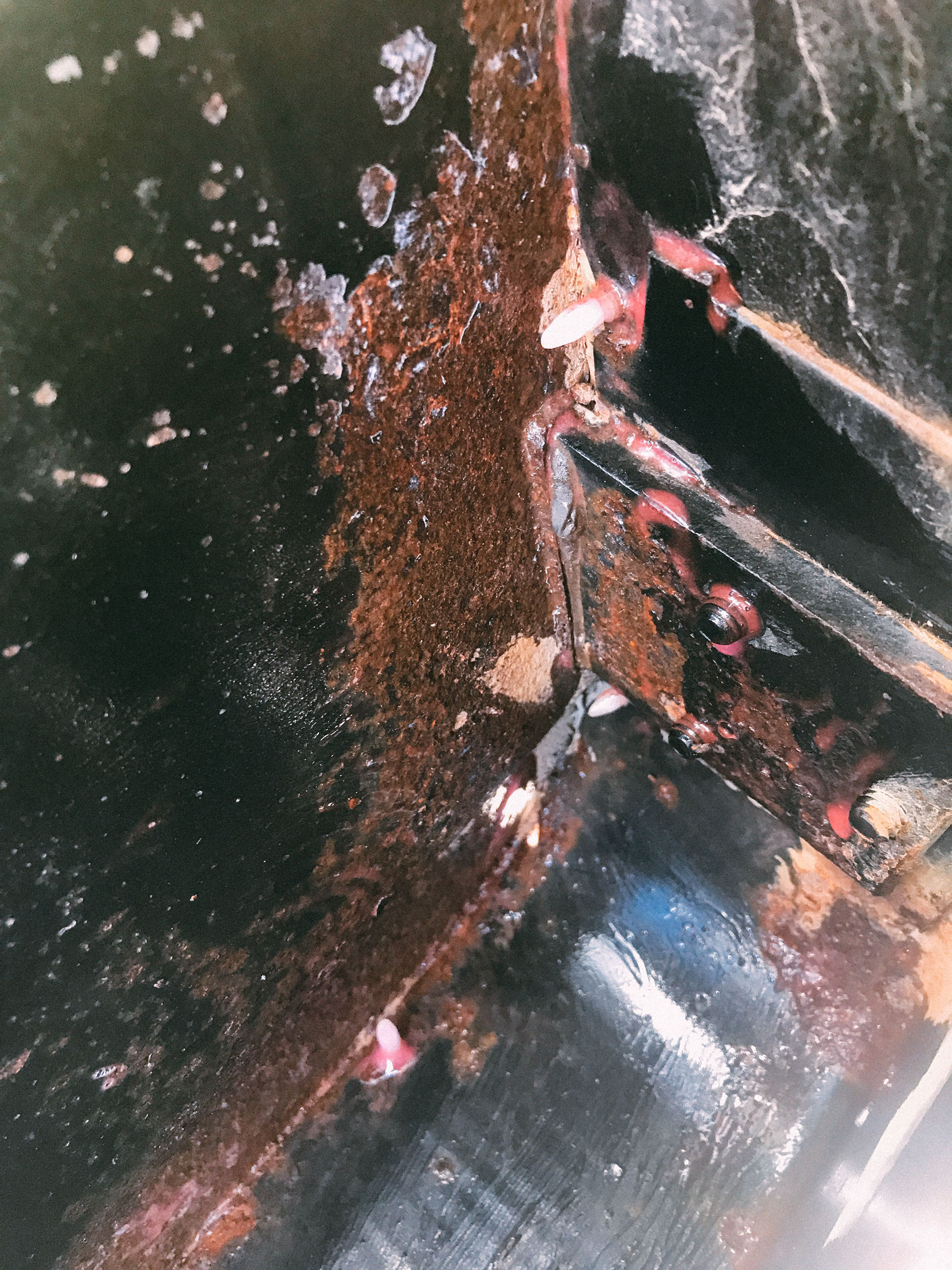
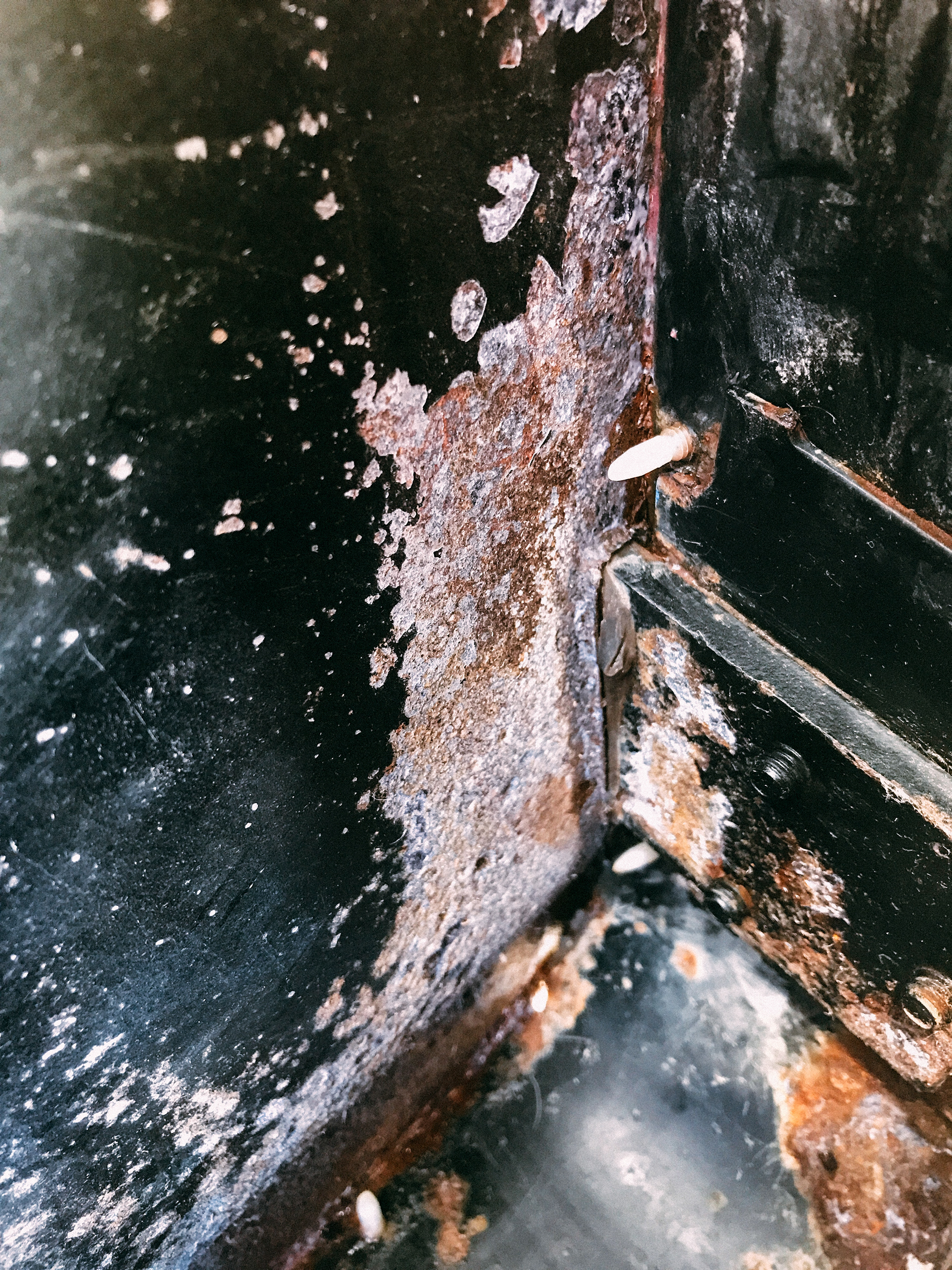
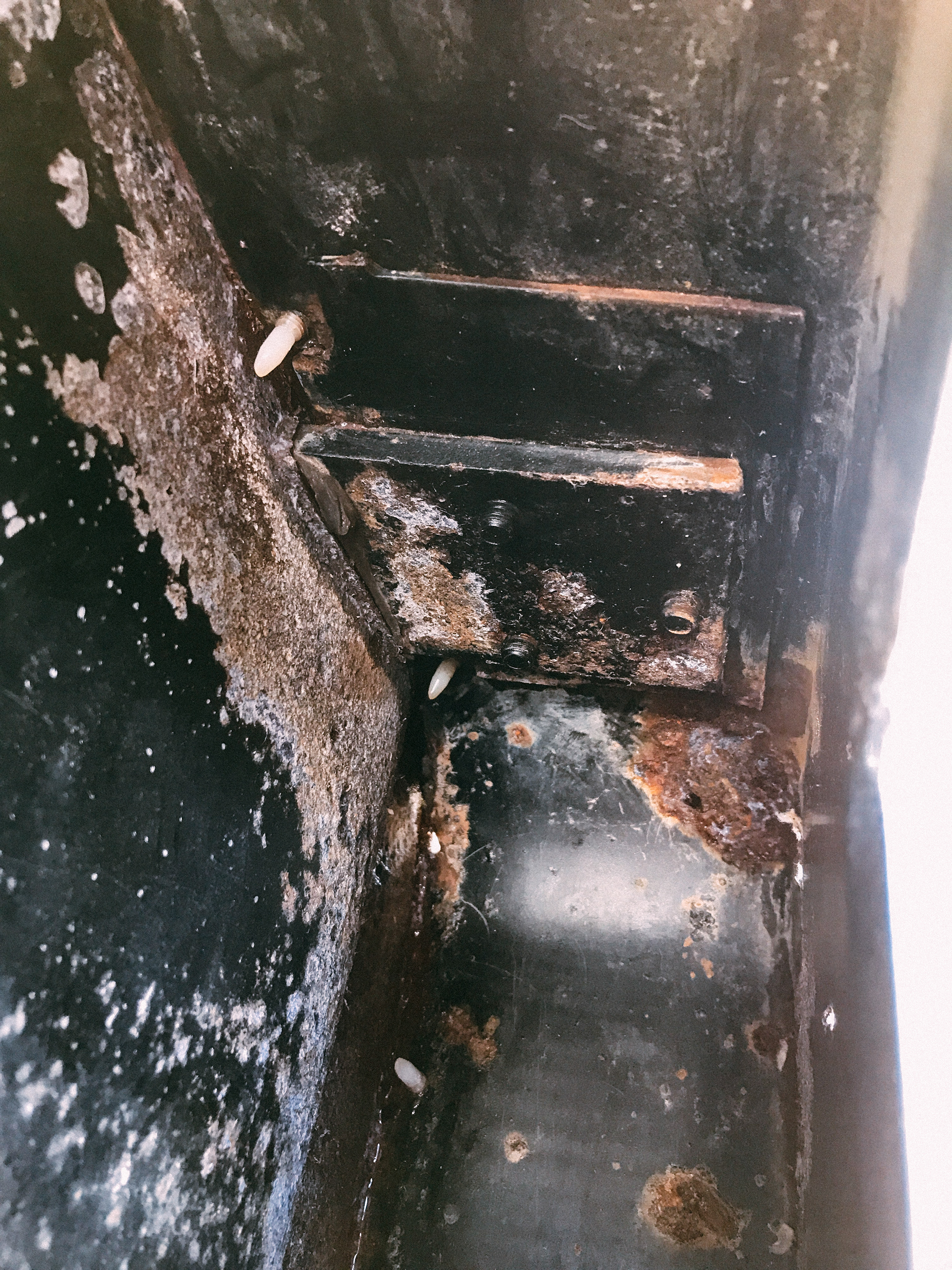
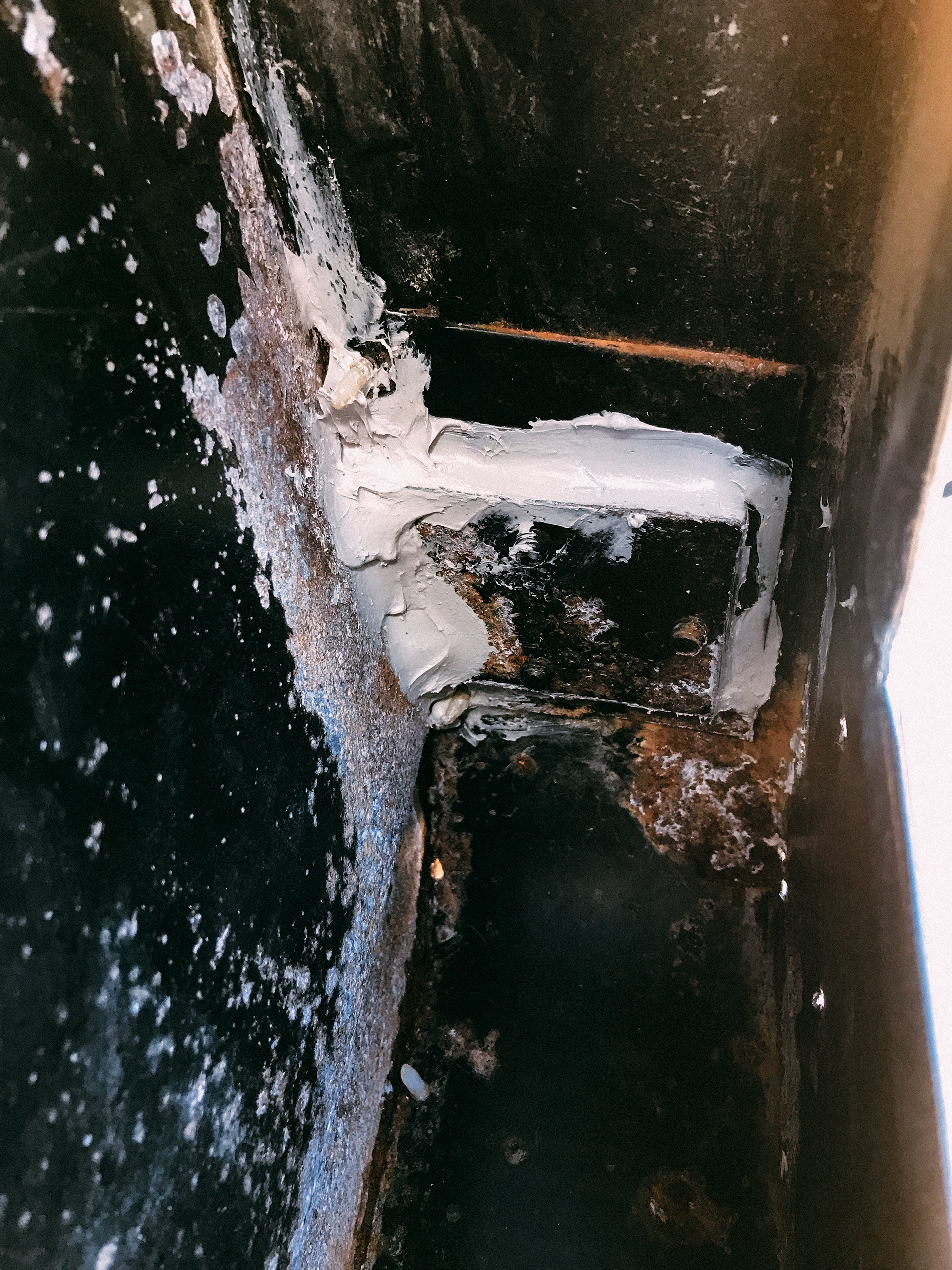
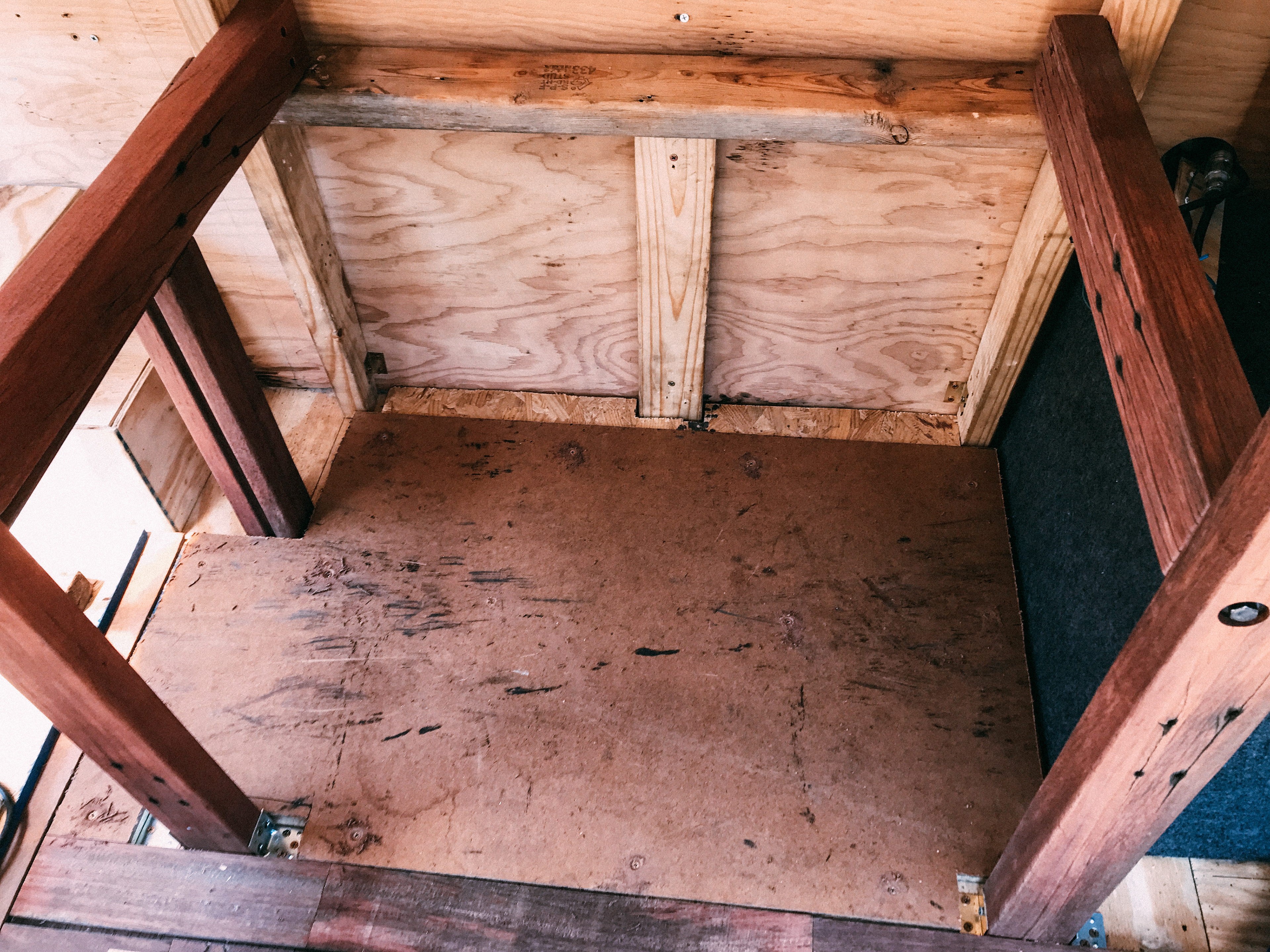
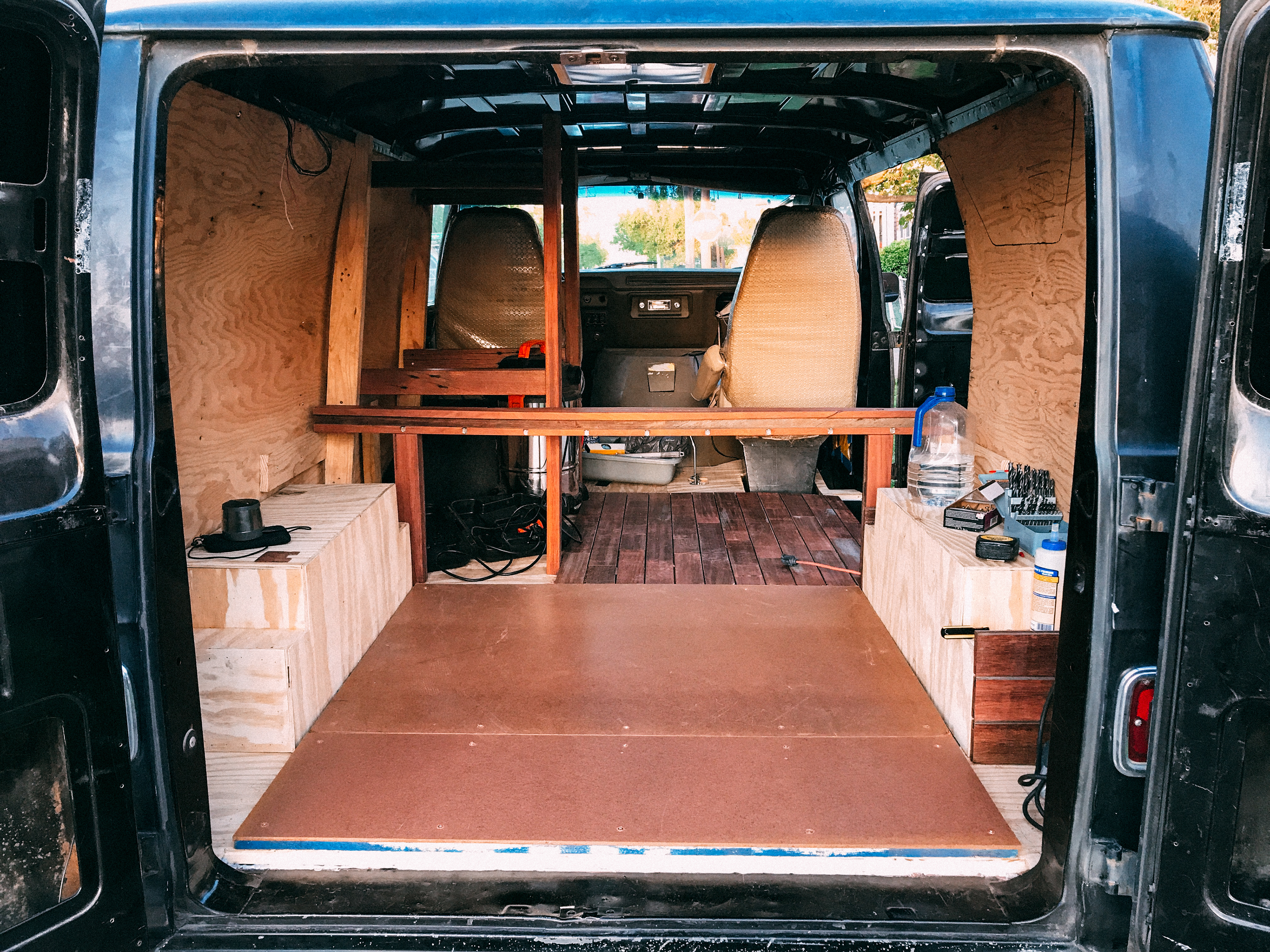
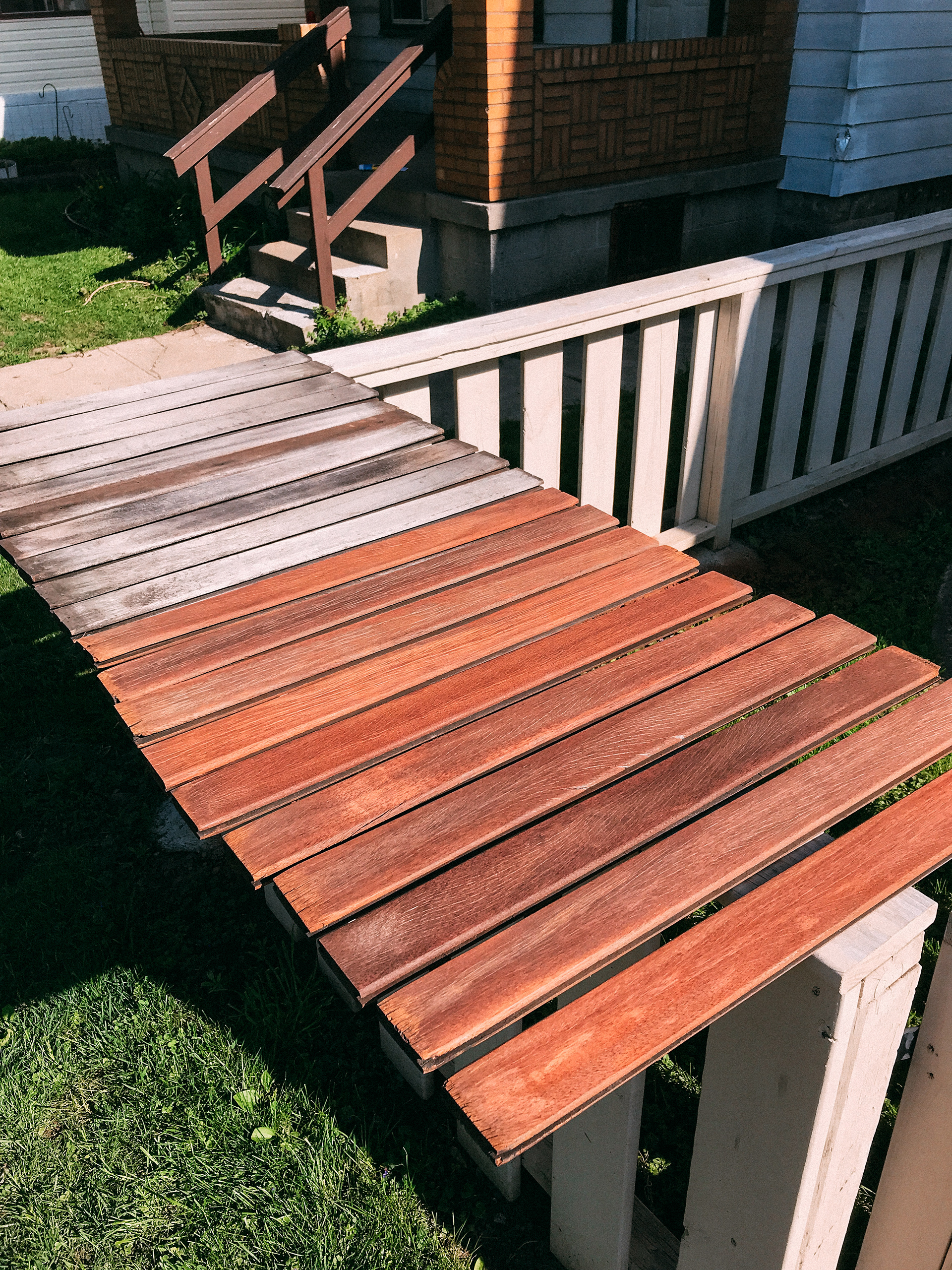
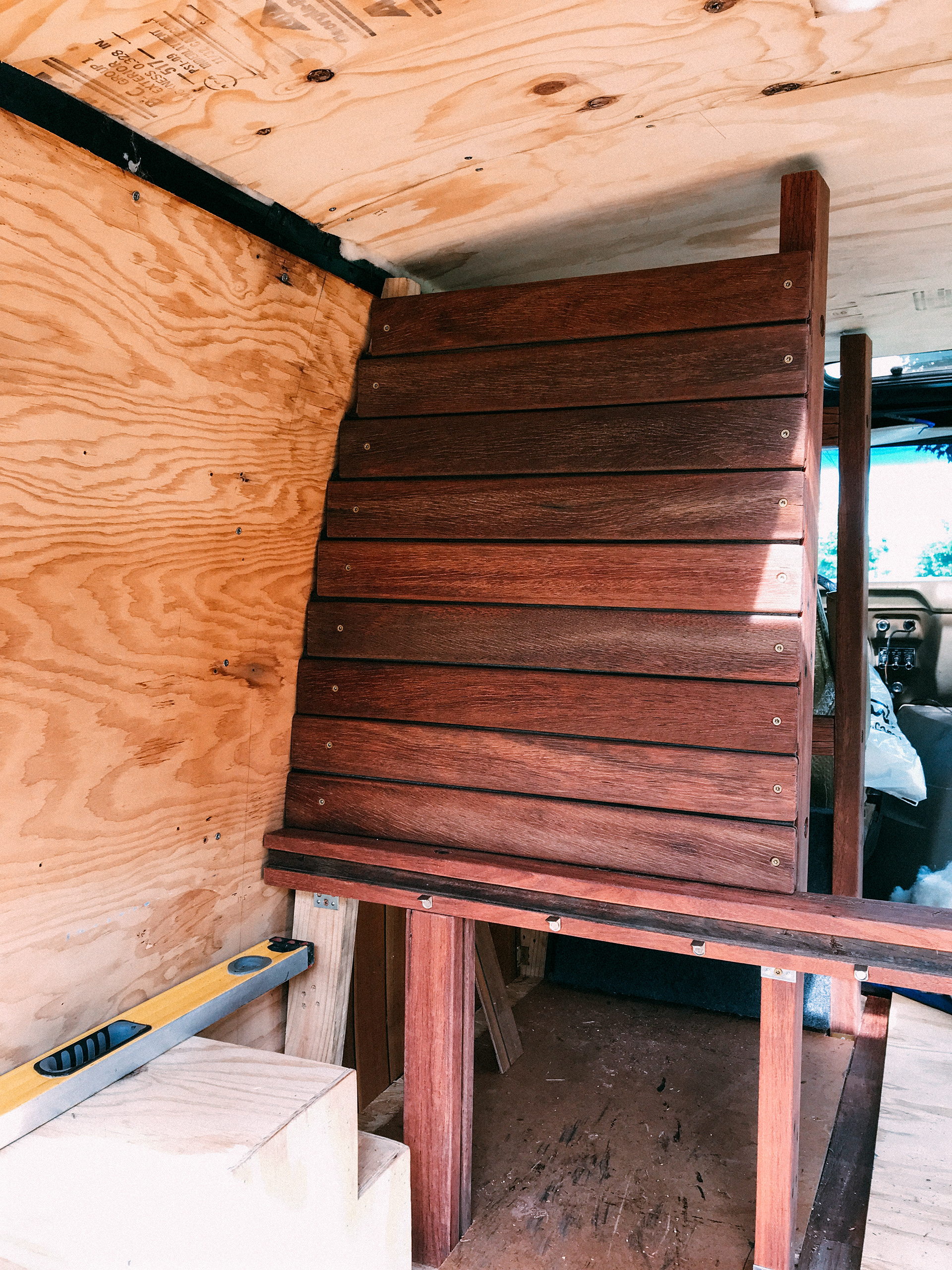
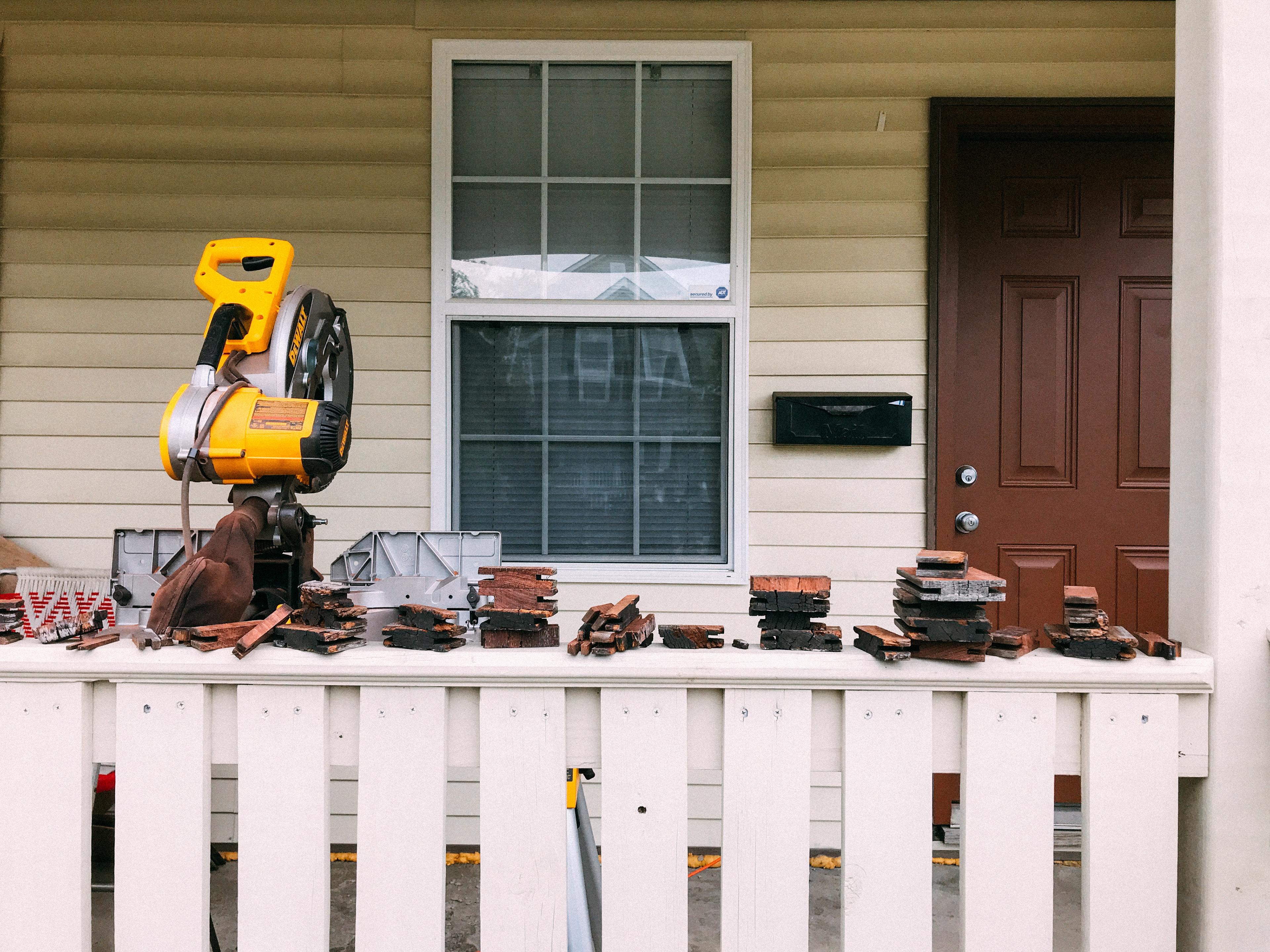
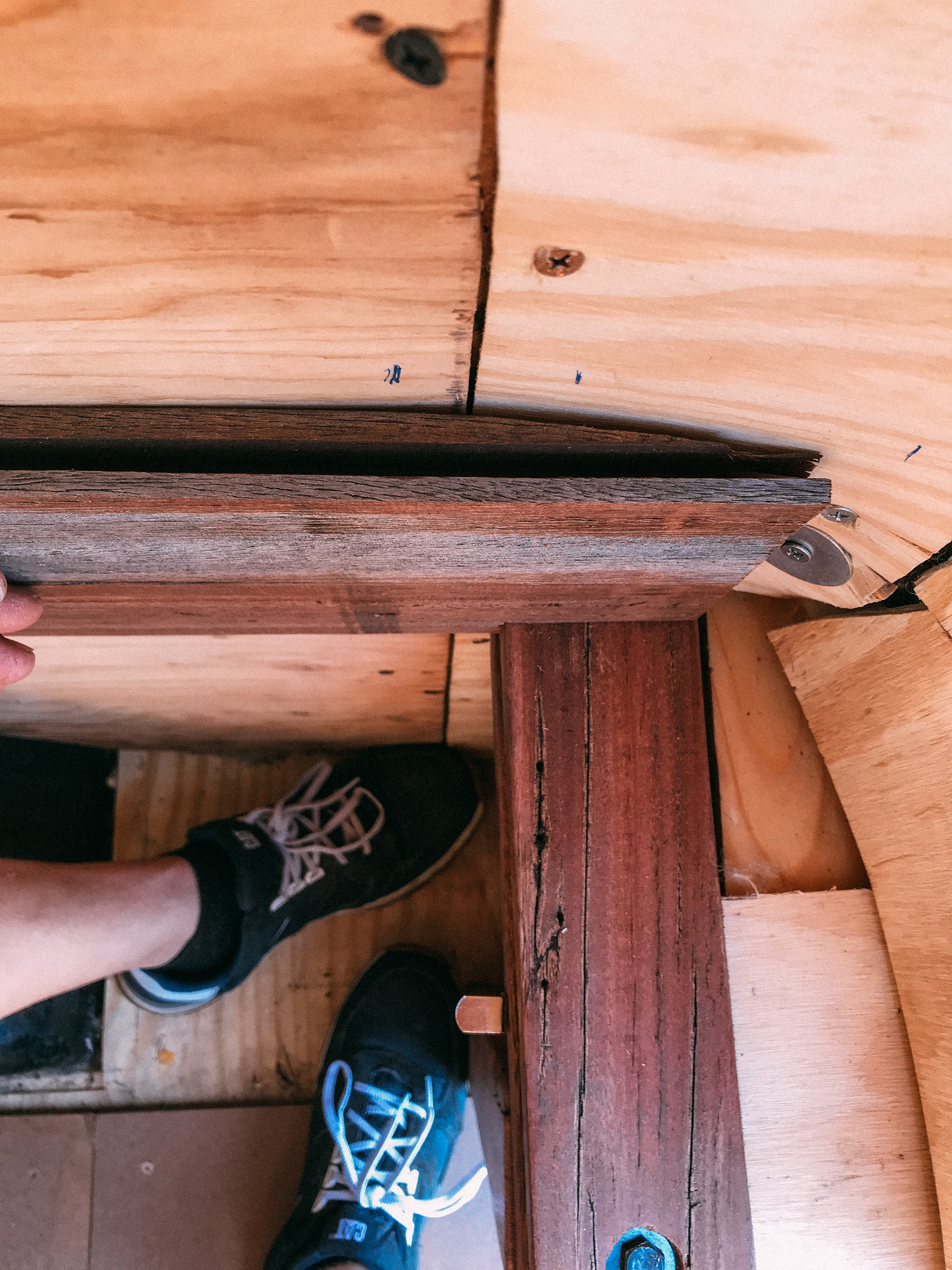
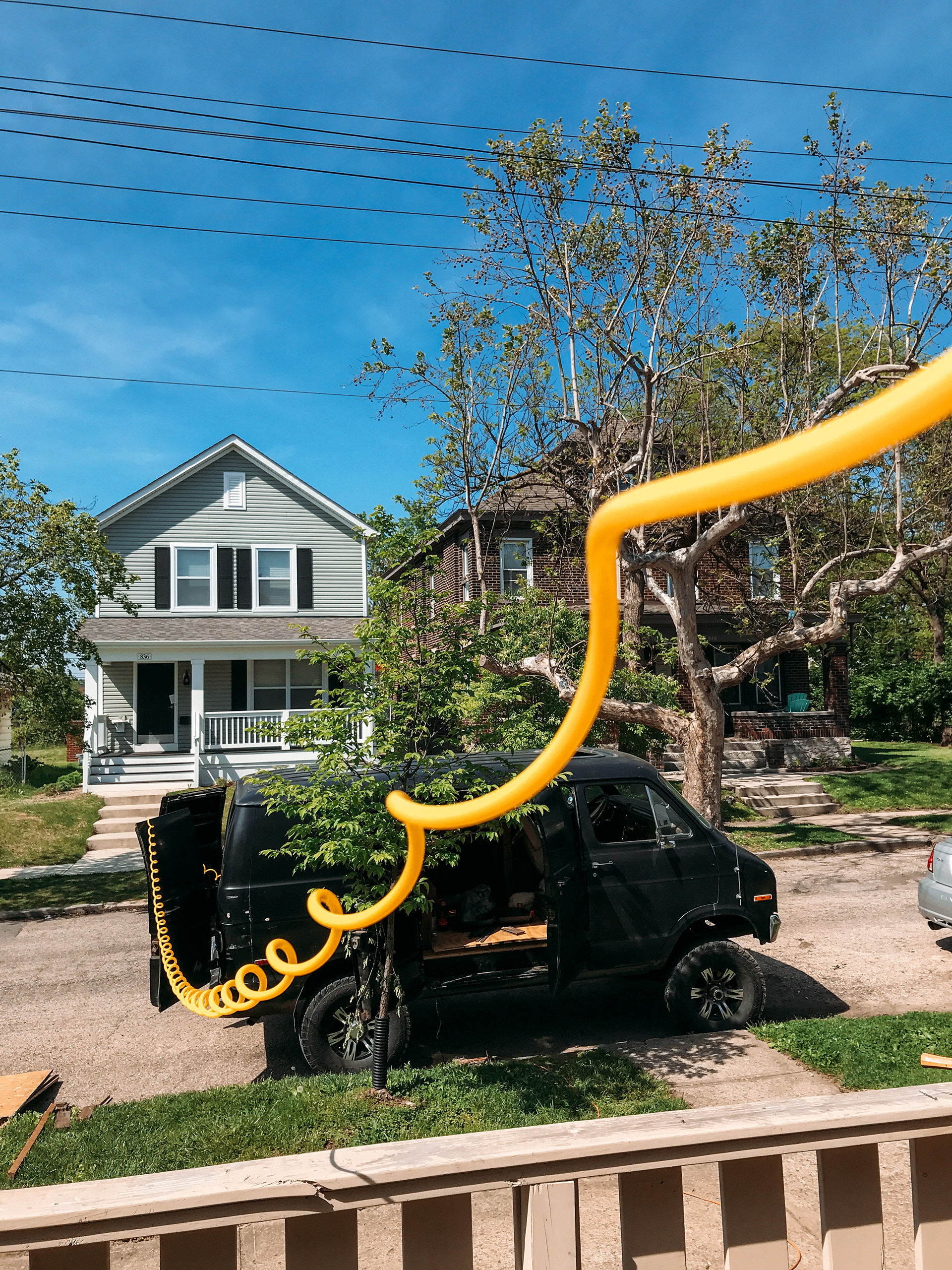
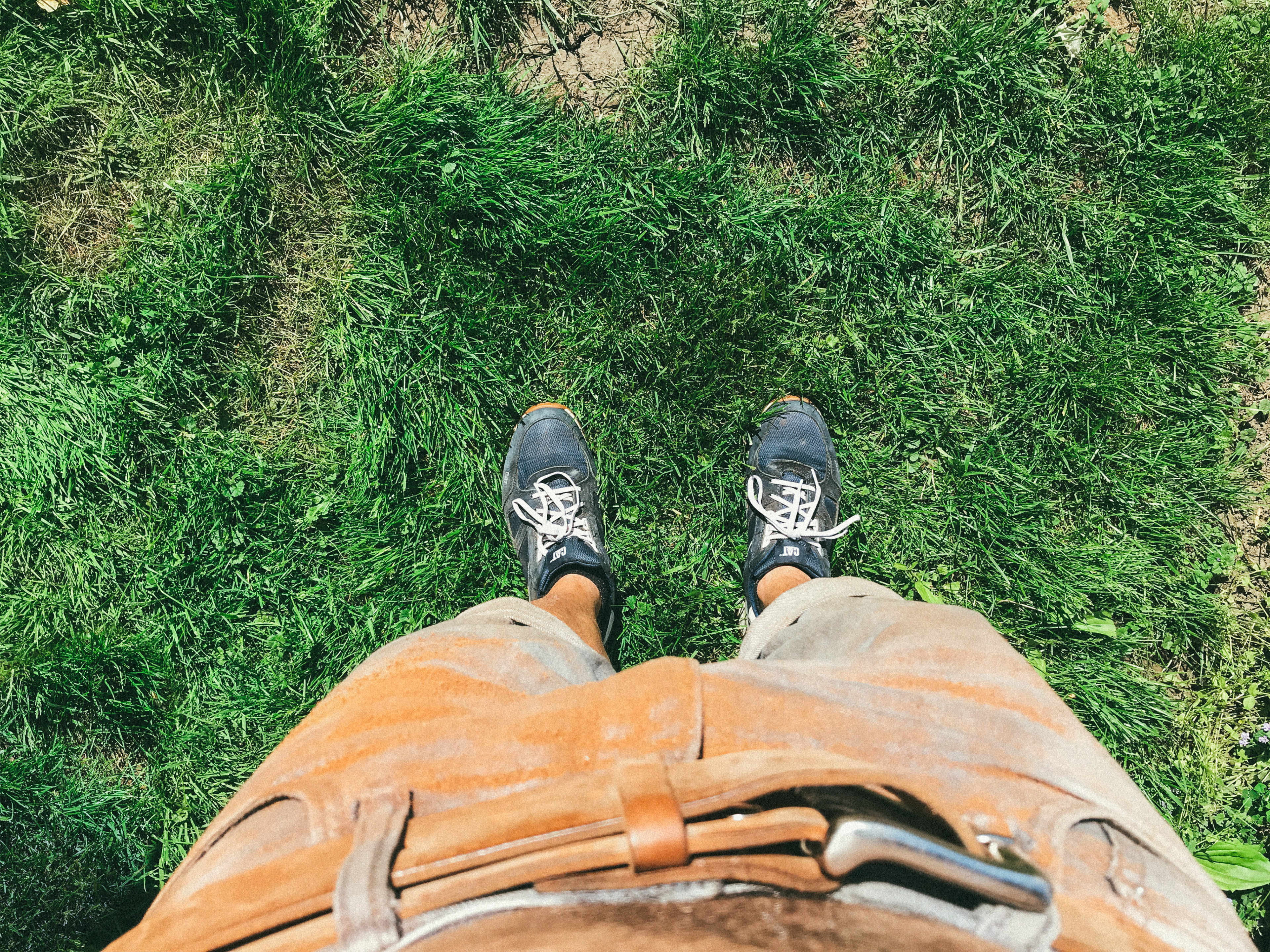
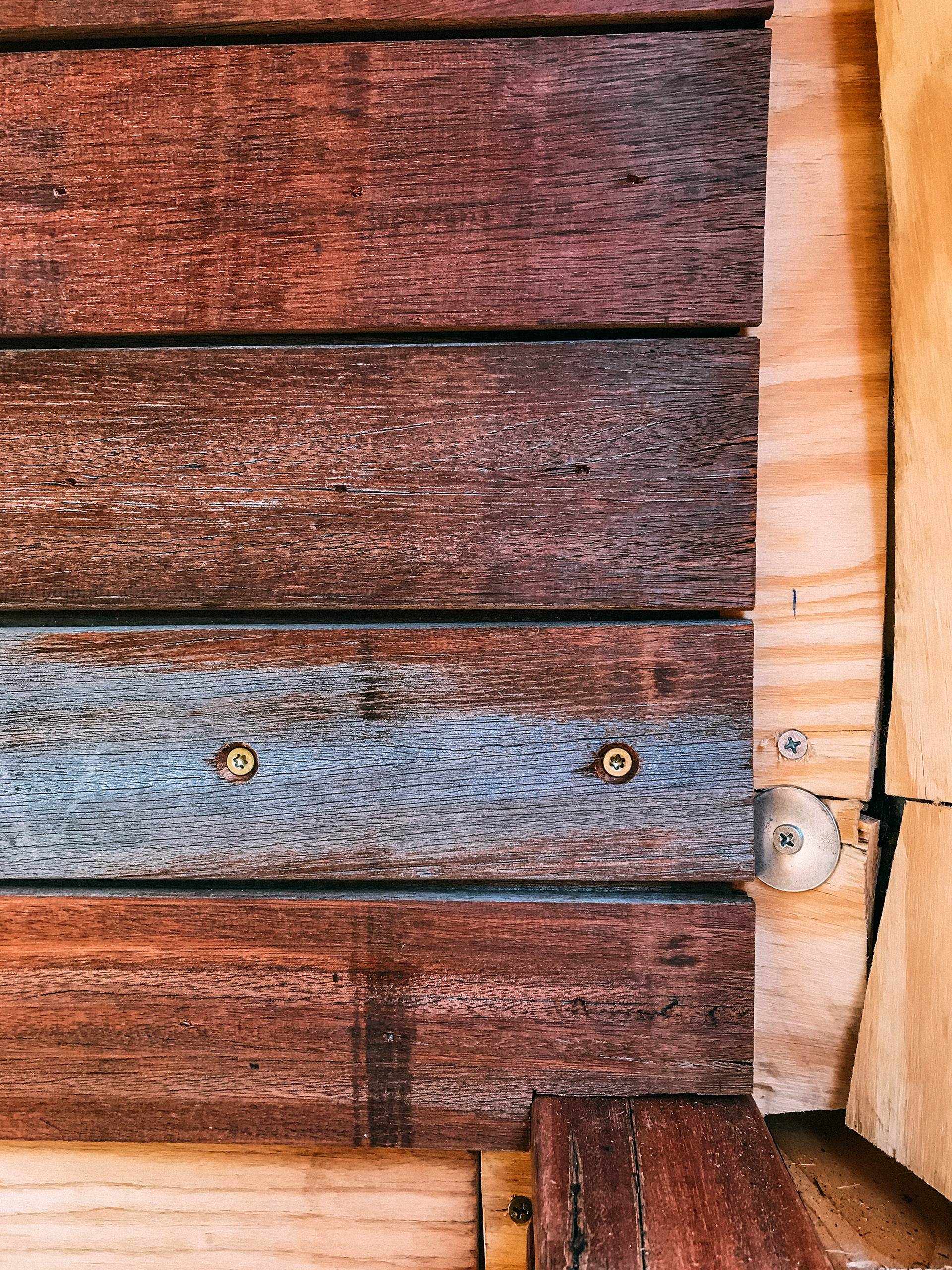
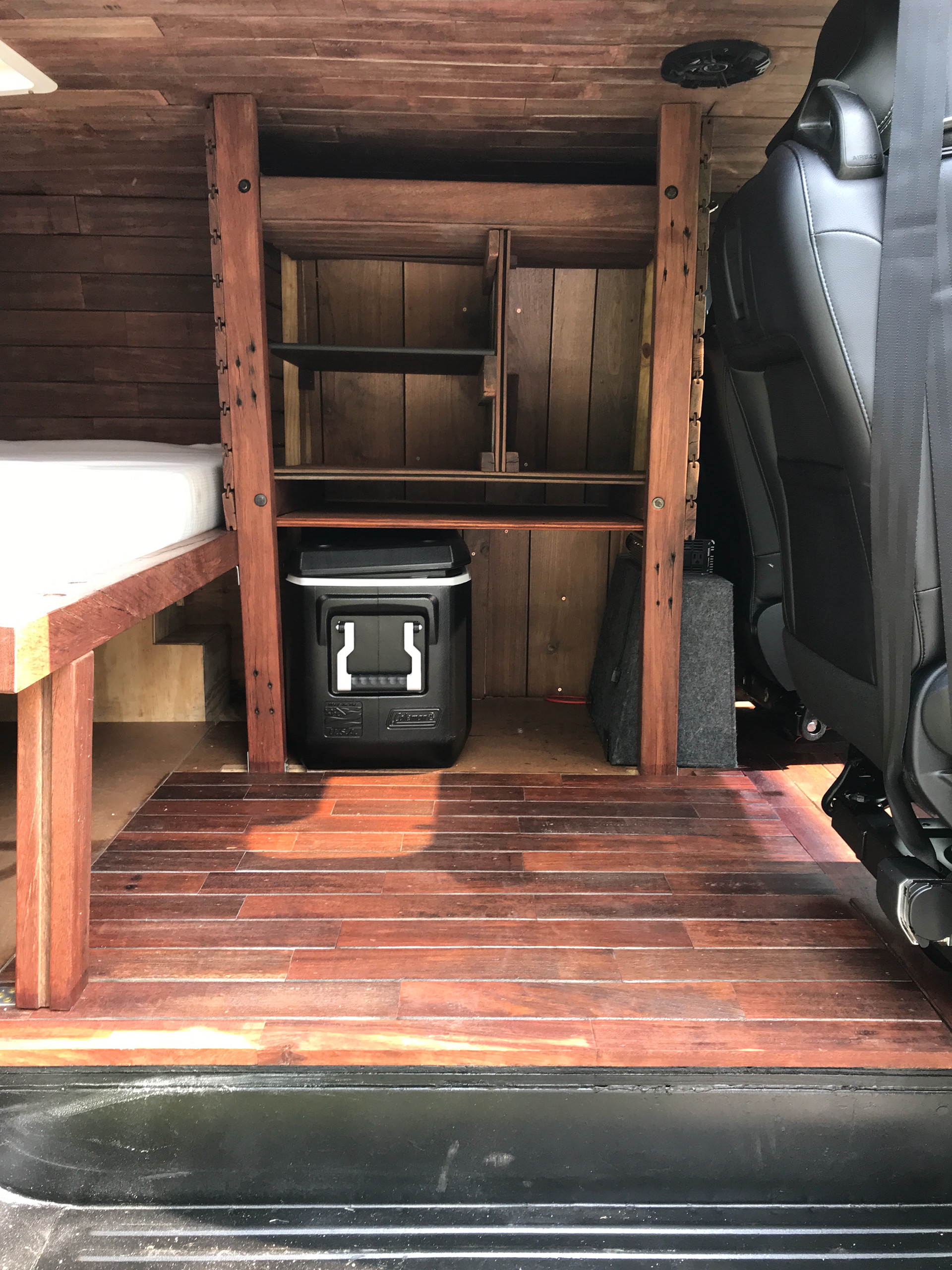
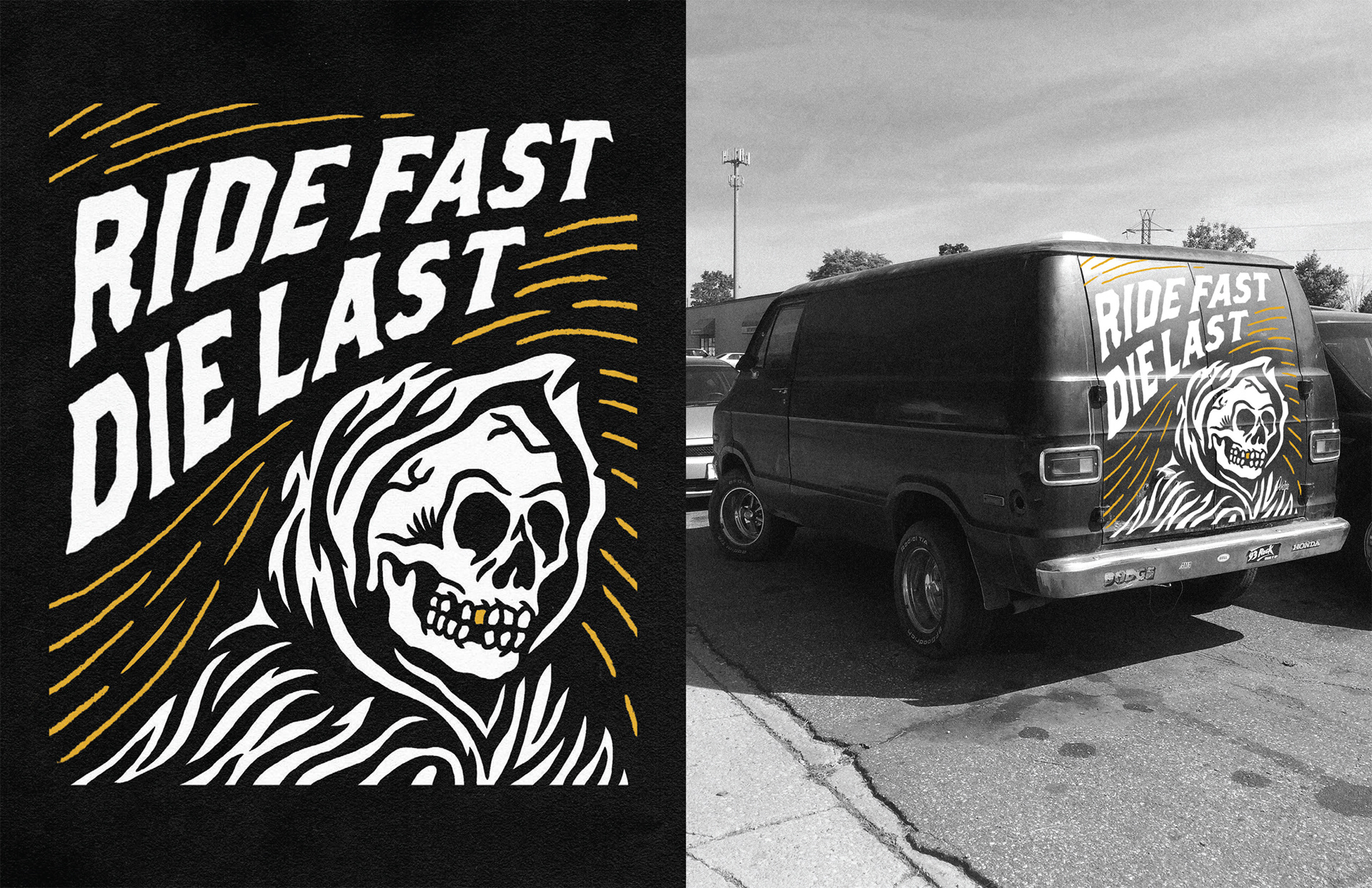
Meet Jerry, a 1976 Dodge Street Van aka B200 Tradesman. I bought this van from a man named Jerry in Idaho. He bought this bad boy off the lot back in '76 and used it to haul his motorcycles he use to race. In '86 he garaged it and it sat until 2016 of November when I purchased it. Knowing how gnarly Canada and Alaska can get, I decided it needed a stronger motor and a better drivetrain. Over the past two and a half years, the van has gone through some frankensteining. I purchased a 1984 Dodge Ramcharger and stole the 4x4 drivetrain and 318 5.2L V8 to put in the Street Van. The motor has been 30 over which puts this carbureted motor to 323 cubic inches. Once the exterior upgrades have been completed, the interior will get an overhaul to store all the gear, insulation and sleeping arrangements.